Order Processing in Logistics Mgmt: An Important Task

Imagine ordering a product online and eagerly waiting for its arrival, only to find out days later that it's been delayed due to some unforeseen processing hiccup. Frustrating, isn't it? I remember the time when I ordered a crucial part for my bike. The weather was perfect for cycling, and I was itching to hit the trails. But due to some complicated order processing, my part arrived weeks later, dampening my enthusiasm and causing a fair bit of inconvenience.
Area of Focus | Importance | Effect of Poor Management |
---|---|---|
Order Processing in Logistics Management | Crucial for smooth functioning of supply chain and order completion. | Delays in delivery and increased costs. |
Steps of Order Processing | Verifying and approving orders; checking availability of materials. | Could lead to errors and slow down the entire operation. |
Slow and Complicated Order Processing | Quick processing ensures timely delivery and customer satisfaction. | Can cause customer dissatisfaction and increased costs due to unnecessary delays. |
Order Processing as legal document | Contains essential details of the transaction. | Misunderstanding between buyer and supplier, legal issues. |
Order Processing in relation to performance cycle | Directly affects the time between order and delivery. | Delivery delays, customer dissatisfaction. |
Checking for deviations in terms | Part of the steps of Order Processing, ensures accuracy of transactions. | Unexpected changes in prices, payment and delivery terms. |
Material availability | Ensures completeness of order delivery. | Shortages and delivery delays. |
Paperwork in Order Processing | Mandatory for documentation and record-keeping. | Might slow down the process and cause delays. |
Acknowledge the order | Confirmation step in order processing. | Communication breakdown, errors in fulfilling orders. |
Streamlining Order Processing | Improves efficiency, reduces time and costs. | Higher operational costs, unnecessary delays, dissatisfaction. |
Introduction
The Importance of Order Processing in Logistics Management
The Steps Involved in Order Processing
The Impact of Slow and Complicated Order Processing
Conclusion
This simple experience made me appreciate the intricate dance that is order processing in logistics management. It's not just about taking an order and shipping a product; it's about ensuring the entire process is streamlined, efficient, and tailored to meet customer expectations. Let's dive deeper into why order processing is so vital, the steps involved, and how slow processing can have a ripple effect on both businesses and customers.
The Heartbeat of Logistics: Understanding Order Processing
At its core, order processing is the backbone of any logistics operation. It's the sequence of actions that a company undertakes from the moment a customer places an order to the point of delivery. This includes verifying, approving, and tracking orders from both customers and suppliers. Think of it as the central nervous system of the supply chain, transmitting information and ensuring every part functions harmoniously.
When I worked with a local logistics company, I saw firsthand how crucial an efficient order processing system was. We handled everything from small, individual orders to large, bulk shipments for corporations. Any delay or mistake in processing could lead to significant setbacks, lost revenue, and unhappy customers.
Why is Order Processing So Important?
Order processing isn't just a routine administrative task. It's an essential legal document between the buyer and the supplier, incorporating all the critical details:
Product descriptions and specifications
Pricing and payment terms
Delivery schedules
Taxes and commercial terms
This document sets the stage for the entire supply chain management process. If any detail is overlooked or mishandled, it could lead to delays, legal complications, or even loss of trust between parties.
Moreover, efficient order processing directly impacts the order cycle time – the duration from when an order is received to when the product is delivered to the customer. A shorter cycle time often translates to higher customer satisfaction, which is paramount in today's competitive market.
The Step-by-Step Journey of an Order
Understanding the steps involved in order processing can shed light on its complexity and importance. Here's a breakdown:
1- Order Verification: Once an order is received, it's crucial to verify all the details. This includes checking for any deviations from agreed terms, confirming prices, payment methods, and delivery dates.
Order processing in logistics management is the backbone of any successful business.

2- Inventory Check: Before confirming the order, the company must ensure that the requested items are in stock. If they're not, this step involves scheduling production and procuring necessary materials.
3- Order Approval and Acknowledgment: After verification and inventory checks, the order is approved. The customer is then sent an acknowledgment, detailing any modifications or confirmations.
4- Order Fulfillment: This involves picking, packing, and preparing the product for shipment. It's the physical aspect of order processing.
5- Shipping and Delivery: Arranging the logistics for transporting the product to the customer's location, ensuring timely and safe delivery.
6- Post-Delivery Service: After the product reaches the customer, post-delivery support and services are provided as needed.
Each step is interlinked, and a delay or error in one can affect the entire process.
The Importance of Streamlining These Steps
In my previous role, we faced a significant challenge: our order processing system was outdated, heavily reliant on paperwork, and prone to human error. Orders would sometimes be misplaced, leading to delays and frustrated customers. Recognizing the need for change, we decided to optimize our supply chain management process.
We invested in a modern order processing system that automated many tasks. The results were almost immediate:
Order cycle times reduced by 30%
Inventory management improved, reducing stockouts
Customer satisfaction scores increased
This transformation taught us that streamlining order processing isn't just beneficial—it's essential for staying competitive.
The Domino Effect of Slow and Complicated Order Processing
When order processing is slow or complicated, the impacts can be far-reaching:
Customer Dissatisfaction: Delayed orders lead to unhappy customers, negative reviews, and potential loss of future business.
Increased Costs: Inefficiencies often mean higher operational costs due to overtime, expedited shipping, or handling returns.
Strained Supplier Relationships: Delays can affect not just customers but also suppliers, leading to strained relationships and possible contractual issues.
Competitive Disadvantage: In a market where speed and reliability are key, companies with sluggish order processing fall behind more agile competitors.
I recall a time when a major client threatened to cancel their contract with us due to repeated delays. Our order processing system was bogged down by manual approvals and redundant checks. It was a wake-up call. We had to rethink our processes and make necessary changes.
The Culprits Behind Slow Order Processing
Several factors contribute to inefficient order processing:
Excessive Paperwork: Reliance on physical documents slows down communication and increases the chance of errors.
Lack of Automation: Manual data entry and processes are time-consuming and error-prone.
Poor Communication: Disconnected departments or lack of clear communication channels can lead to misunderstandings.
Inefficient Inventory Management: Not knowing what's in stock can delay order approvals and fulfillment.
Strategies to Streamline and Optimize Order Processing
So, how can companies optimize their supply chain management process tips to ensure efficient order processing? Here are some strategies:
1- Embrace Automation: Implementing software solutions that automate order entry, verification, and tracking can significantly reduce processing times.
2- Integrated Systems: Ensure that all departments—from sales to warehouse to shipping—are connected through an integrated system for seamless communication.
3- Employee Training: Regular training ensures that staff are proficient with the systems in place and understand the importance of their role in the process.
4- Inventory Management Solutions: Utilizing inventory management software helps in real-time tracking of stock levels, reducing delays due to stockouts.
5- Customer Communication: Keeping customers informed at every stage enhances transparency and builds trust.
6- Continuous Improvement: Regularly reviewing and refining processes helps in identifying bottlenecks and implementing solutions promptly.
In our company, after facing the challenges, we adopted an Enterprise Resource Planning (ERP) system. This move integrated all our processes, from order entry to inventory to shipping. The benefits were evident—we reduced errors, improved efficiency, and could scale operations smoothly.
Real-Life Examples of Efficient Order Processing
Let's look at some companies that have mastered the art of order processing:
Amazon: Known for its lightning-fast fulfillment, Amazon's sophisticated order processing system allows for same-day deliveries in many areas. They've optimized every step, from the moment you click "buy" to when the package arrives at your door.
Zara: This fast-fashion retailer has a supply chain that can move from design to store shelves in mere weeks. Their efficient order and production processes allow them to respond quickly to fashion trends.
The Human Element in Order Processing
While technology plays a significant role, the human element cannot be overlooked. Employees who are engaged, trained, and motivated contribute immensely to the efficiency of order processing.
I remember one of our team members, Lisa, who always went the extra mile. She noticed patterns in order delays related to a specific supplier. By bringing this to management's attention, we could address the issue directly, leading to faster processing times.
Empowering Employees
Empowering staff to make decisions, suggesting improvements, and taking ownership of their roles fosters a proactive culture. It's not just about systems and processes; it's about people working together towards a common goal.
The Future of Order Processing in Logistics Management
With advancements in technology, such as Artificial Intelligence (AI) and Blockchain, the future of order processing looks promising:
AI and Machine Learning: Predictive analytics can forecast demand, optimize inventory levels, and identify potential delays before they occur.
Blockchain Technology: Enhances transparency and security in transactions, ensuring all parties have access to real-time, immutable data.
Robotics and Automation: From automated warehouses to drone deliveries, the physical aspects of order processing are becoming faster and more efficient.
Companies that embrace these technologies are likely to stay ahead of the curve, offering superior service and agility.
Conclusion: Putting It All Together
Order processing is more than just a cog in the logistics machine—it's the heartbeat that keeps the entire operation alive and thriving. By ensuring this process is streamlined, efficient, and customer-focused, businesses can not only meet but exceed customer expectations.
Reflecting on my own experiences, both as a consumer and a professional, the importance of order processing in logistics management is crystal clear. Whether it's waiting for that bike part or managing a team handling thousands of orders daily, the goal remains the same: deliver the right product, to the right place, at the right time.
By optimizing supply chain management processes and embracing both technological and human solutions, companies can pave the way for sustained success and customer loyalty.
References
1- Chopra, S. (2019). Supply Chain Management: Strategy, Planning, and Operation. Pearson Education.
2- Rushton, A., Croucher, P., & Baker, P. (2017). The Handbook of Logistics and Distribution Management. Kogan Page Publishers.
3- Grant, D. B., Trautrims, A., & Wong, C. Y. (2017). Sustainable Logistics and Supply Chain Management. Kogan Page Publishers.
4- Mentzer, J. T. (2004). Fundamentals of Supply Chain Management: Twelve Drivers of Competitive Advantage. Sage Publications.
5- Christopher, M. (2016). Logistics & Supply Chain Management. Pearson UK.
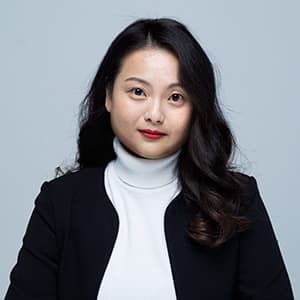
Yu Payne is an American professional who believes in personal growth. After studying The Art & Science of Transformational from Erickson College, she continuously seeks out new trainings to improve herself. She has been producing content for the IIENSTITU Blog since 2021. Her work has been featured on various platforms, including but not limited to: ThriveGlobal, TinyBuddha, and Addicted2Success. Yu aspires to help others reach their full potential and live their best lives.