Establishing Supply Contracts: A Guide to SCM

Type of Supply Contract | Definition | Advantages and Disadvantages |
---|---|---|
Supply Contract | An agreement between a buyer and a supplier which outlines the terms and conditions of the sale. | Protects both parties in the event of a dispute but needs regular review to remain up-to-date and relevant. |
Fixed Price Contract | A contract that sets out the number of goods or services to be purchased and how much they will cost. May include inflation adjustments and incentives for meeting targets. | Offers financial predictability for the buyer but can potentially lead to quality compromise as suppliers aim for maximum profit. |
Cost-plus Contract | A contract where the buyer agrees to cover the actual costs, plus a percentage or fixed fee as profit. | Allows for greater flexibility and adaptation to changes in the cost of materials/labour but risks budget overrun due to absence of an upper limit. |
Time and Materials Contract | A contract that offers payment based on the time and materials used to complete the project. | Provides flexibility where scope of work is undefined but can be riskier due to potential for cost overruns and longer completion time. |
Definite Delivery Contract | A contract where the date of delivery is agreed upon in advance. | Offers certainty about delivery date but lacks flexibility if changes in the project occur. |
Indefinite Delivery Contract | A contract where the delivery does not have a set date and is determined by the buyer's demand. | Offers greater flexibility but there's uncertainly about when goods or services will be delivered. |
Performance-Based Contract | A contract where payment is made based on the supplier's performance. | Incorporates quality checks and performance metrics but can be challenging to measure and enforce. |
Purchase Order Contract | A document between a buyer and seller detailing types and quantities of products. | Provides legal protection but can be time-consuming to make changes if required. |
Master Service Agreement | A contract that spells out most but not all of the terms between signing parties, the balance being agreed upon by separate agreements. | Efficient when parties frequently contract but still need separate agreements. |
Blanket Purchase Agreement | A contract providing for the future purchase of goods or services during a period of time at preset prices. | May allow for volume discounts but could be disadvantageous if unit prices decrease. |
This article discusses the different types of supply contracts, their advantages and disadvantages, and the benefits of an indefinite delivery contract. In addition, it explains that supply contracts are important agreements between buyers and suppliers that outline the terms and conditions of the sale and help protect both parties in the event of a dispute.
The article highlights the importance of ensuring both parties understand their obligations and that the contract is clear and concise. It also emphasizes the need to review the agreement regularly to ensure it remains up-to-date and relevant.
Introduction
Types of Supply Contracts
Fixed-price contract
Cost-plus contract
Time and materials contract
Introduction: Supply contracts are agreements between buyers and suppliers that outline the terms and conditions of the sale. Supply contracts are used to ensure that both parties understand their obligations and to help protect both parties in the event of a dispute. There are several types of supply contracts, each of which has its advantages and disadvantages.
Supply Chain Visibility Solutions For İmproved Business Efficiency
Digital Transformation İmpact On Supply Chain İnterview Question
Types of Supply Contracts
Fixed-price contract: A fixed-price contract sets out the number of goods or services to be purchased and how much they will cost. This type of contract may include inflation adjustments and incentives for meeting targets.
Cost-plus contract: A cost-plus arrangement compensates a supplier for their costs and allows them to charge an additional fee. The fee is usually a fixed percentage of costs.
Time and materials contract: A time and materials contract is often used for repairs. The buyer agrees to pay the supplier set rates for parts and labor they use on a project. You will probably sign a time and materials contract whenever you take your car in for service.
Indefinite delivery contract: An indefinite delivery contract is used when the buyer does not know the exact quantity of goods or services they need. This contract allows the buyer to purchase goods or services as required without renegotiating the contract each time.
Effective Procurement Management Strategies For Supply Chain Success
Balancing Carrying Costs And Service Levels İnterview Question
Benefits of an Indefinite Delivery Contract
An indefinite delivery contract offers several benefits to both buyers and suppliers. For buyers, it provides flexibility and allows them to purchase goods or services as needed without renegotiating the agreement. This type of contract also offers cost savings, as it eliminates the need to renegotiate the contract each time the buyer needs to purchase more goods or services.
For suppliers, an indefinite delivery contract provides the security of a long-term relationship with the buyer and the ability to plan ahead and secure supplies in advance. This contract also allows suppliers to manage their resources better and ensure they have the necessary supplies to meet their customers’ needs.
Conclusion: Supply contracts are essential to any business relationship between buyers and suppliers. There are several types of supply contracts, each of which offers its advantages and disadvantages. An indefinite-delivery agreement is an attractive option for buyers and suppliers, as it provides flexibility, cost savings, and a secure long-term relationship.
Tip
When entering a supply contract, it is essential to ensure that both parties understand their obligations and that the agreement is clear and concise. In addition, reviewing the agreement regularly is necessary to ensure it remains up-to-date and relevant.
Supply contracts are the foundation of successful supply chain management; establish them wisely.
The article provides a detailed overview of supply contracts, their types, and the importance of such contracts in establishing clear terms and conditions of sale for both buyers and suppliers. It specifically underscores the necessity of these contracts in preventing disputes and maintaining clarity between both involved parties. Moreover, the article stresses the importance of regularly reviewing these contracts to ensure their relevance and accuracy over time. Thorough understanding of such contractual agreements could potentially be a significant topic within logistics and supply chain management courses, given their inherent role in procuring goods and services.

Regarding business agreements, supply contracts are essential documents that must be created and maintained. Supply contracts are legal agreements that outline the terms and conditions of the sale of goods or services between two parties. These contracts are essential to ensure that both parties know their respective rights and obligations under the contract. Several types of supply contracts can be used depending on the specific needs of the parties involved.
The first type of supply contract is the fixed-price contract. This type of contract is often used when the parties involved want to agree on a fixed amount for the goods or services provided. The price is set in advance, and both parties are obligated to honor the terms of the contract. This type of contract benefits both parties because it eliminates the risk of any surprises or additional costs.
Another type of supply contract is the cost-plus contract. This contract is similar to a fixed-price contract, but the price is not set in advance. Instead, the cost of the goods or services is determined by the cost-plus method. This means that the price of the goods or services is determined by the cost to the seller, plus a predetermined percentage or fee. This contract benefits the seller, allowing them to recoup their costs and make a profit.
The third type of supply contract is the cost-plus-incentive-fee contract. This type of contract is similar to a cost-plus contract but includes an incentive payment. This payment is based on the performance of the goods or services provided. If the performance meets or exceeds the buyer's expectations, the seller may receive an additional payment. This type of contract benefits the buyer, ensuring that the seller will perform to the best of their ability.
Finally, the fourth type of supply contract is the demand-driven contract. This type of contract is used when the demand for the goods or services being provided fluctuates. The market determines the price of the goods or services, and the seller must deliver the goods or services at the agreed-upon price. This type of contract benefits the seller, allowing them to adjust their pricing based on the demand.
In conclusion, four main types of supply contracts can be used to define the terms and conditions of a sale of goods or services. These contracts are the fixed-price contract, the cost-plus contract, the cost-plus-incentive-fee contract, and the demand-driven contract. Each type of contract has its benefits and drawbacks, and it is essential to understand the differences between them to ensure that the agreement benefits both parties.

An indefinite delivery contract (IDC) is a procurement agreement between a buyer and a supplier that offers the buyer the option to order supplies and services when needed. This contract provides several benefits to both parties, making it a popular choice for many procurement processes.
One of the main benefits of an IDC is its flexibility. Unlike traditional contracts, which often require specific supplies and services to be ordered in a certain way, an IDC allows buyers to specify the goods and services they need when they need them. This will enable buyers to adjust their required orders, making them more responsive to changing market conditions.
Another benefit of an IDC is its cost-effectiveness. The flexibility of an IDC allows buyers to order only the supplies they need when needed. This reduces the costs associated with purchasing materials in bulk or making large orders which may not be used. In addition, the buyer may be able to negotiate better prices with the supplier due to the long-term nature of the agreement.
Finally, an IDC also offers the buyer the opportunity to build a relationship with the supplier. Because the buyer and supplier will be working together for an extended period, they can develop a rapport and understand each other's needs and preferences. This can make the procurement process more efficient, as both parties are familiar with the process and understand how to work together.
In conclusion, an indefinite delivery contract offers several benefits for both the buyer and the supplier. It is a flexible and cost-effective way for buyers to procure goods and services and provides an opportunity for buyers to build a relationship with their suppliers. For these reasons, an IDC is a popular choice for many procurement processes.

A guide to Supply Chain Management (SCM) can be a valuable tool for companies when establishing supply contracts. SCM manages the flow of products and services from the supplier to the customer. It involves various activities, including inventory management, transportation, and customer service. An SCM guide can help companies understand the complexities of supply contracts and ensure that they are properly established.
A guide to SCM should provide an overview of the entire supply chain process. It should explain the different stages of the process, such as sourcing, production, and distribution. It should also provide an in-depth look at the different types of supply contracts, such as exclusive, open market, and limited term. Finally, a guide to SCM should include information on the legal requirements of supply contracts, such as contract duration, specifications, and pricing.
In addition, a guide to SCM should guide how to negotiate with suppliers. It should provide information on evaluating potential suppliers and negotiating terms, such as payment terms and delivery times. It should also provide information on how to monitor supplier performance and how to manage any disputes.
Finally, a guide to SCM should provide information on ensuring that the contract is implemented correctly. This includes ensuring that the agreement is appropriately documented, that the supplier is meeting the terms of the contract, and that the customer is receiving the goods and services as agreed.
In summary, a guide to SCM can be a valuable tool for companies when establishing supply contracts. It can provide an overview of the entire supply chain process, guidance on negotiating with suppliers, and information on ensuring that the agreement is implemented correctly. By following the advice provided in a guide to SCM, companies can ensure that their supply contracts are precisely established.

Role of Supply Contracts
A supply contract is an essential element in supply chain management, serving as a legally binding agreement between a buyer and a supplier. It outlines the terms and conditions of the purchase, delivery, and payment for goods or services. The role of a supply contract in supply chain management entails several key functions, such as risk management, relationship management, and performance evaluation.
Risk Management Function
In the context of supply chain management, supply contracts play a crucial role in mitigating risks. They help protect both parties against uncertainties in price fluctuations, disruptions, and other unforeseen events. By clearly defining the responsibilities, requirements, and expectations of both parties, a supply contract reduces the likelihood of disputes and misunderstandings, ensuring a smooth flow of goods and services throughout the supply chain.
Relationship Management Function
Another important role of the supply contract is to foster strong relationships between the buyer and the supplier. A well-drafted contract can establish a basis for long-term collaboration, trust, and mutual benefit. This enables the parties involved to work together to address challenges, make improvements, and achieve shared goals. A strong supplier-buyer relationship is vital for optimizing the efficiency of the supply chain and achieving a competitive advantage in the market.
Performance Evaluation Function
A supply contract serves as a critical tool for monitoring and evaluating a supplier's performance. The contract clearly defines the desired quality standards, delivery schedules, and other KPIs (key performance indicators) that the supplier is expected to meet. By regularly reviewing contract compliance and performance, buyers can identify opportunities for improvement and take corrective actions if necessary. This ultimately leads to enhanced supply chain performance and better decision making.
In conclusion, the role of a supply contract in supply chain management is indispensable. Through risk management, relationship management, and performance evaluation functions, supply contracts help to ensure efficient and effective supply chain operations. Ultimately, a well-designed supply contract is a vital component of a successful supply chain strategy, contributing to the long-term sustainability and competitive advantage of businesses in today's dynamic and complex marketplace.

Essential Components for Supply Chain Management Planning
Strategic Alignment and Objectives
A critical aspect of developing a supply chain management plan is ensuring that it aligns with the overall organizational strategy and objectives. This involves understanding the company's vision, goals, and competitive landscape, to design supply chain strategies that support the organization's desired positioning in the market.
Operations and Process Management
Effective supply chain management requires analysis and optimization of operations and processes related to procurement, transportation, production, warehousing, and distribution. Identifying potential bottlenecks, inefficiencies, and areas for improvement will help streamline operations, reduce lead times, and ultimately increase customer satisfaction.
Inventory Management and Control
Supply chain management must take into account the demands of managing inventory levels to ensure adequate product availability while minimizing holding costs. This requires accurate demand forecasting, inventory control mechanisms, and timely visibility of stock levels throughout the supply chain.
Supplier Selection and Relationship Management
Choosing the right suppliers is vital to successful supply chain management, as their performance can directly impact the company's ability to meet customer expectations. Developing strong relationships with strategic suppliers and monitoring their performance regarding cost, quality, and delivery standards can contribute to supply chain efficiency and effectiveness.
Technology Integration and Information Sharing
Utilizing current technology and sharing data across supply chain participants can boost collaboration, improve decision-making, and enhance supply chain visibility. Implementing an integrated system, like enterprise resource planning (ERP) software, can connect suppliers, producers, and customers to facilitate timely information exchange and help optimize supply chain processes.
Risk Management and Contingency Planning
Risk management is crucial in ensuring supply chain resilience, as unexpected disruptions can have severe consequences. Identifying potential risks, prioritizing them based on their likelihood and impact, and developing contingency plans to mitigate the impacts of disruptions enable a more agile and resilient supply chain.
Performance Measurement and Continuous Improvement
Monitoring and measuring supply chain performance using key performance indicators (KPIs) is essential for continuous improvement. Regularly reviewing KPIs can provide insights into the effectiveness of supply chain strategies, highlight areas for improvement, and drive ongoing efforts to optimize overall supply chain performance.

**Stages of Supply Chain Evolution**
Supply chain management (SCM) is an essential aspect of businesses, focusing on the strategic coordination of various processes to improve efficiency and sustainability. Over the years, SCM has evolved significantly across four main stages, each marked by critical advancements and enhanced capabilities for organizations.
**Stage 1: Functional Optimizations**
During the initial stage of SCM development, organizations aimed to optimize individual functions such as procurement, manufacturing, and transportation. This siloed approach targeted cost reduction, increased efficiency, and overall improvement within the specific area, with limited integration between the departments. However, the lack of a holistic view and collaboration led to inconsistencies and conflicting objectives throughout the supply chain.
**Stage 2: Enterprise Integration**
Recognizing the need for better alignment, the second stage of SCM evolution emphasized integrating functions and processes within the organization. Firms adopted tools and practices to enhance communication, data sharing, and decision making, thereby fostering collaboration between departments. This shift enabled companies to optimize processes more cohesively, leading to reduced lead times, inventory levels, and costs, while increasing customer satisfaction.
**Stage 3: Supply Chain Extension**
In the third stage of SCM evolution, organizations acknowledged the importance of extending their focus beyond the internal enterprise to include external partners such as suppliers and customers. By building strong relationships and leveraging information technology, businesses aimed to achieve better visibility, coordination, and responsiveness across the entire supply chain. This stage allowed organizations to further enhance efficiency, mitigate risks, and boost competitiveness.
**Stage 4: Network Collaboration**
The most recent stage in SCM evolution involves fostering collaboration among multiple supply chain partners to create a cohesive network. This stage emphasizes the importance of joint decision-making, pooling resources, and sharing risks, to create value for all parties involved. Network collaboration enables organizations to rapidly respond to market changes, drive innovation, and achieve a higher level of agility and resilience.
In conclusion, the four stages of supply chain evolution represent a continuous journey towards embracing a more integrated, strategic, and collaborative approach to managing supply chains. Each stage signifies a notable shift in practices and priorities, aimed at enhancing overall performance and adaptability. Businesses that recognize and adapt to these evolving SCM perspectives stand to gain competitive advantages, improve efficiency, and achieve long-term sustainability.

**Understanding the SCM Plan**
A Supply Chain Management (SCM) plan establishes a strategy for coordinating various business processes to facilitate the efficient movement of goods from suppliers to consumers. The five steps of an SCM plan are as follows:
**1. Defining Objectives**
The first step in establishing an effective SCM plan is defining the overarching goals and objectives that the supply chain should achieve. This involves identifying both short-term and long-term targets and aligning them with the organization's overall business strategy.
**2. Supply Chain Design**
Next, the supply chain design step involves determining the suitable architecture for the supply chain. This includes analyzing factors such as transportation costs, facility locations, and sourcing requirements to enhance operational efficiency and minimize costs while ensuring product accessibility to the target market.
**3. Planning and Forecasting**
Accurate planning and forecasting are essential for effective supply chain management. This step involves utilizing historical data, market trends, and consumer insights to predict future demand and appropriately plan for potential risks and disruptions.
**3. Inventory and Order Management**
Effective inventory management ensures that optimal inventory levels are maintained and that all customer orders are fulfilled as efficiently as possible. In this step, organizations need to develop strategies for tracking inventory levels, replenishment, and order fulfillment to reduce stockouts or excess inventory.
**5. Performance Evaluation and Optimization**
Finally, continuous evaluation and optimization of the SCM plan are imperative for sustained success. Monitoring Key Performance Indicators (KPIs) and comparing them against predetermined benchmarks help organizations identify areas of improvement and excellent performance. This feedback loop enables the continuous refining and enhancement of the supply chain strategy.
In conclusion, a well-crafted SCM plan involves defining clear objectives, designing a suitable supply chain structure, establishing accurate planning and forecasting methods, efficiently managing inventory and orders, and regularly evaluating and optimizing supply chain performance. By diligently adhering to these steps, organizations can improve operational efficiency, minimize costs, and ultimately, deliver greater value to their end customers.

**Concept of Supply Chain Contracts**
Supply chain contracts define the legal and operational relationships between businesses within a supply chain. These agreements stipulate the terms and conditions under which firms engage with each other, outlining the responsibilities, risks, and rewards for each party. They foster coordination and collaboration, enhancing the overall efficiency and effectiveness of the supply chain.
**Fixed-Price Contracts**
A fixed-price contract establishes a preset price for goods or services. The supplier is responsible for delivering the agreed-upon product at the specified cost, regardless of any fluctuations in production expenses. This contract type offers assurance to the buyer, but may result in reduced flexibility for the supplier.
**Cost-Plus Contracts**
In a cost-plus contract, the buyer agrees to reimburse the supplier for the production costs, while also providing an additional fee that represents the supplier's profit margin. This arrangement allows for greater flexibility on both sides, with the potential for more accurate pricing.
**Incentive-Based Contracts**
These contracts link supplier remuneration to the achievement of specific objectives or performance indicators. Incentive-based contracts can motivate suppliers to improve their performance, leading to increased efficiency and value for the buyer. They also help to align the interests of both parties, promoting collaboration and coordination.
**Risk-Sharing Contracts**
Under risk-sharing contracts, both the buyer and supplier jointly assume responsibility for potential risks and uncertainties within the supply chain. This approach can encourage a more collaborative relationship, as parties are incentivized to jointly manage and mitigate risks to ensure supply chain resilience.
**Consignment Contracts**
With consignment contracts, the supplier retains ownership of goods until they are sold to the end customer. The retailer then pays the supplier for the sold items, taking a commission for the sale. This type of contract provides flexibility for both parties, enabling the efficient management of inventory levels and reduced financial risks for the retailer.
Overall, supply chain contracts play a critical role in governing the relationships between businesses and establishing the operational guidelines that underlie supply chain management. By selecting the appropriate contract type or combination, companies can optimize their supply chain performance and ensure a smoother flow of goods and services.

Understanding the Four Types of Supply Chain Strategies
Efficient supply chain management is vital for companies to meet customer demands, reduce costs, and improve overall competitiveness. To achieve efficiency, businesses often adopt various supply chain strategies, which can be primarily categorized into four types: efficient, responsive, agile, and risk-hedging.
Efficient Supply Chain Strategy
An efficient strategy focuses on cost minimization and maximizing supply chain surplus. The main objective is to deliver products at the lowest possible total cost. Companies employing this strategy generally operate in predictable and stable markets, aiming to produce large volumes of standardized or commoditized goods. The major implications include a need for well-coordinated and streamlined processes, long-term partnerships with suppliers, and the use of economies of scale.
Responsive Supply Chain Strategy
In contrast to the efficient strategy, a responsive strategy prioritizes speed, flexibility, and adaptability over cost. This is suitable for businesses operating in dynamic, uncertain, and rapidly changing environments, offering a wide variety of products with short life cycles. Key implications of this strategy involve maintaining low inventory levels, leveraging technology to enhance visibility, and focusing on customer service to provide customized solutions.
Agile Supply Chain Strategy
Combining the best features of efficient and responsive strategies, the agile strategy seeks to create a flexible and cost-effective supply chain. Companies employing this strategy can adapt to market changes while still maintaining cost-efficiency. The main implications include developing cross-functional teams, using modular product designs to enable easy customization, and establishing strong relationships with multiple suppliers to ensure supply continuity.
Risk-Hedging Supply Chain Strategy
Lastly, the risk-hedging strategy aims to minimize potential supply chain disruptions and reduce vulnerabilities. This is particularly relevant for companies operating in high-risk environments, dealing with complex global networks, or relying on a limited number of critical suppliers. Implications for this strategy include diversifying supplier base, utilizing contingency plans, and adopting tools for risk assessment and mitigation.
In conclusion, choosing the right supply chain strategy can significantly impact the efficiency and effectiveness of supply chain management. By understanding and implementing the appropriate approach – whether it is an efficient, responsive, agile, or risk-hedging strategy – companies can optimize their supply chains, enhance their competitiveness, and achieve long-term success.

Stages of Supply Chain
The four stages of supply chains include supplier management, production, distribution, and customer management. Each stage has specific implications for efficient supply chain management.
Supplier Management
In the supplier management stage, companies form partnerships with suppliers and evaluate their performance to ensure consistent and high-quality raw materials. Efficient management in this stage reduces procurement costs, lead times, and the risk of stockouts, contributing to the effectiveness of the entire supply chain.
Production Management
The production stage involves planning, scheduling, and controlling the transformation of raw materials into finished products. Efficient management in this stage ensures timely production, minimizes waste and downtime, and controls production costs. Key performance indicators include output, quality, productivity, and capacity utilization.
Distribution Management
During the distribution stage, companies must ensure the right products are delivered to the right place at the right time. This requires coordination with warehouses, transportation providers, and other stakeholders. Efficient distribution management results in shorter lead times, reduced transportation costs, and increased customer satisfaction. Key metrics include delivery time, order accuracy, and shipping costs.
Customer Management
In the customer management stage, companies focus on delivering value through effective communication, order fulfillment, and relationship-building. Efficient customer management supports demand forecasting, product availability, and enhanced customer experiences, leading to increased sales, loyalty, and profitability.
To achieve efficient supply chain management, companies must focus on optimizing each stage, addressing challenges, and maximizing performance. This involves leveraging advanced technologies, such as data analytics and artificial intelligence, adopting best practices, and fostering a culture of continuous improvement. The result is an agile, cost-effective, and customer-centric supply chain that drives competitive advantage and long-term success.

Role of Contracts in Supply Chain Management
Contracts play a vital role in supply chain management, serving as legally binding agreements defining the rights, responsibilities, and expectations of each party involved. They provide a clear framework for collaboration between supply chain partners, ensuring that the necessary resources and materials are available at the right time and place.
Promoting Successful Collaboration
Effective contracts contribute to successful collaboration by outlining the terms and conditions of the partnership, such as pricing structures, payment terms, and delivery schedules. They provide a common understanding of each party's performance expectations and establish consequences for non-compliance, which ensures that partners are held accountable.
Risk Mitigation
Contracts help mitigate risks associated with supply chain disruptions, such as delays, shortages, and quality issues. They outline contingency plans and strategies for dealing with unexpected events, reducing the likelihood of disputes and ensuring the continuity of resources and services. Furthermore, contracts allocate risk-sharing between supply chain partners, providing incentives for cooperation and resource optimization.
Creating Trust and Transparency
Contracts foster trust and transparency among supply chain partners by delineating the responsibilities of each party involved, such as who is responsible for managing inventory levels or ensuring quality assurance. This clarity ensures that all parties' expectations are aligned, promoting a more effective and efficient supply chain, ultimately leading to stronger relationships and increased cooperation between partners.
Standardizing and Streamlining Operations
The standardization and streamlining of operations are crucial for supply chain efficiency. By including specific terms relating to operational procedures, contracts help create consistency and uniformity across the entire supply chain. This uniformity allows partners to plan and forecast more accurately and improves the overall supply chain's adaptability and responsiveness.
Continuous Improvement and Innovation
Contracts can also drive continuous improvement and innovation within the supply chain by establishing performance targets and incentivizing partners to pursue new technologies or processes to achieve these objectives. By fostering a culture of collaboration, contracts encourage supply chain partners to share knowledge and expertise, leading to more efficient, resilient, and competitive supply chains.
In conclusion, contracts in supply chain management are essential for promoting successful collaboration, mitigating risks, fostering trust and transparency, standardizing operations, and driving continuous improvement and innovation. When used effectively, they lead to stronger relationships, increased cooperation, and better overall performance of supply chain systems.

Supply Planning in SCM
Supply planning refers to the strategic coordination and management of resources, to ensure the efficient and effective allocation of materials and information throughout a specific supply chain. In supply chain management (SCM), this involves anticipating the availability, capacity, and allocation of resources, as well as identifying bottlenecks and inefficiencies that may hinder timely and cost-effective delivery of products and services.
Role in Material Flow
In ensuring a smooth flow of materials, supply planning helps balance current and future supply with demand. By aligning production output and inventory levels, it ensures that materials are available when needed, preventing stock shortages or excess inventory. This process includes monitoring lead times, order quantities, safety stock levels, and supplier performance, so that all components of the supply chain operate in harmony. As a result, supply planning contributes to minimizing costs, reducing stockouts, and improving customer satisfaction.
Role in Information Flow
In addition to managing the flow of materials, supply planning plays a crucial role in improving information flow throughout the supply chain. Effective communication among stakeholders, including suppliers, manufacturers, and distributors, is essential in achieving smooth coordination of supply planning activities. The use of modern information technologies, such as enterprise resource planning (ERP) systems and other advanced communication tools, facilitates real-time data sharing and simplifies decision-making processes. By fostering transparent and seamless information flow, supply planning helps stakeholders to make more informed decisions and to jointly respond to challenges in a timely manner.
Benefits and Outcomes
Overall, the implementation of effective supply planning within SCM can ensure a smooth flow of materials and information through the supply chain. By aligning supply with demand and promoting efficient communication among all supply chain participants, supply planning can enhance operational efficiency, minimize costs, and improve customer satisfaction. As a result, companies that invest in robust supply planning practices can benefit from increased competitiveness and long-term success in the marketplace.

Key Elements of Effective SCM Strategy
An effective supply chain management (SCM) strategy is crucial for organizations to achieve higher levels of efficiency and competitiveness in global markets. The key elements of a successful SCM strategy are integration, visibility, flexibility, and collaboration.
Integration in SCM
Integration refers to the seamless flow of information, materials, and finances throughout the entire supply chain. It ensures that all the components of the management process are interconnected to avoid disruptions and improve efficiency. By integrating various supply chain functions, such as procurement, production, and distribution, businesses can optimize their resources, reduce costs, and improve customer satisfaction levels.
Visibility for Better Decision-Making
Visibility in SCM involves having real-time access to information related to inventory levels, demand forecasts, and production schedules. This allows organizations to make informed decisions, reducing the risk of stockouts and excess inventory. Enhanced visibility also helps in monitoring supplier performance, ensuring adherence to contractual agreements and identifying opportunities for further improvement.
Flexibility as a Competitive Edge
Flexibility refers to the ability of an organization to adapt to changes in the market conditions, such as fluctuations in customer demand or disruptions in the supply chain. A flexible SCM strategy enables businesses to swiftly respond to challenges, maintain continuity in production, and minimize potential losses. It also helps organizations to better cater to diverse customer needs, improving customer satisfaction and loyalty.
Collaboration for Greater Efficiency
Collaboration in SCM is the process of sharing information, resources, and decision-making responsibilities across different stakeholders. This includes suppliers, manufacturers, distributors, and customers. A collaborative approach to SCM fosters strong partnerships, enhances communication, and leads to joint problem-solving. In turn, this collective effort ensures higher efficiency levels and better overall performance in the supply chain.
In conclusion, a successful supply chain management strategy encompasses integration, visibility, flexibility, and collaboration as its fundamental components. By adopting these key elements, organizations can enhance their efficiency, reduce costs, improve customer satisfaction, and maintain a competitive edge in the market. Ultimately, an effective SCM strategy lays the foundation for overall business success.

Supply Chain Design
One crucial aspect of sustainable supply chain management is designing and implementing a well-thought-out supply chain strategy. By aligning procurement, production, and distribution processes with sustainability principles, companies can significantly reduce their environmental footprint. This involves selecting eco-friendly materials, optimizing transportation routes, investing in renewable energy sources, and adopting circular economy practices, such as recycling and remanufacturing.
Supplier Selection and Collaboration
To enhance sustainability in the supply chain management process, it is essential for companies to choose suppliers that prioritize environmentally responsible practices. This entails evaluating potential partners based on their environmental performance, adherence to industry regulations, and commitment to continuous improvement. Furthermore, fostering long-lasting relationships and collaborating with suppliers can help drive innovation in sustainable product and process design, reducing overall environmental impacts.
Green Procurement
Green procurement practices can significantly contribute to the reduction of environmental impacts in the supply chain management process. By integrating environmental criteria into purchasing decisions, organizations can opt for products and services that have lower environmental footprints throughout their life cycle, minimizing waste generation and carbon emissions. In addition, green procurement can encourage suppliers to adopt more sustainable practices, ultimately promoting a greener supply chain.
Efficient Logistics and Transportation
Optimizing logistics and transportation practices can measurably lessen the environmental impacts of supply chain processes. This may include employing route optimization software, consolidating shipments, and selecting fuel-efficient transportation modes. By doing so, companies can reduce their greenhouse gas emissions, minimize energy consumption, and optimize resource utilization. Moreover, utilizing innovative technologies, such as electric vehicles and drones for delivery, can further enhance sustainability in supply chains.
Performance Measurement and Reporting
Continuous improvement and transparency are vital in achieving sustainability in supply chain management. By regularly monitoring key performance indicators (KPIs), companies can identify areas needing improvement and implement corrective measures. These KPIs may encompass energy use, carbon emissions, waste generation, and water consumption. Transparent reporting of environmental performance, ideally following established frameworks like the Global Reporting Initiative, demonstrates commitment to sustainable practices and fosters stakeholder trust.
In conclusion, various supply chain management concepts and practices can significantly contribute to enhancing sustainability and reducing environmental impacts in the SCM process. By adopting sustainable strategies, collaborating with environmentally responsible suppliers, implementing green procurement practices, optimizing logistics and transportation, and continuously monitoring and reporting performance, companies can create greener, more sustainable supply chains.

Risk Identification in Supply Chain Management
Risk management is an integral aspect of supply chain operations, where potential disruptions and vulnerabilities are identified, assessed, and minimized. One way in which risk management is incorporated into supply chain planning is by conducting a comprehensive risk identification process. This entails mapping the entire supply chain, pinpointing areas of vulnerability, and considering factors such as supplier reliability, geopolitical instability, and natural disasters.
Risk Assessment and Prioritization
Following risk identification, supply chain managers evaluate the probability and impact of each identified risk. This process is essential in determining the prioritization of risks, which subsequently aids in allocating resources and establishing mitigation strategies. Factors that should be considered during this phase include the financial cost of potential disruptions, potential damage to brand reputation, and the feasibility of risk mitigation strategies.
Mitigation Strategies in Supply Chain Management
After assessing and prioritizing identified risks, supply chain managers develop and implement mitigation strategies to minimize potential disruptions. This includes contingency planning, in which an alternate course of action is prepared to be executed in the event of a disruption. Furthermore, supply chain managers can establish risk-sharing agreements with suppliers in order to reduce the negative impacts of potential disruptions.
Ongoing Monitoring and Review
The integration of risk management into supply chain operations is not a one-time process. Rather, it requires ongoing monitoring and review of the supply chain to identify new potential risks, assess their impact, and implement corresponding mitigation strategies. This ensures that supply chain managers are constantly aware of the evolving risk landscape and are prepared to act accordingly when disruptions occur.
In conclusion, risk management plays a crucial role in the planning and execution of supply chain operations. By identifying, assessing, and mitigating potential risks, supply chain managers can minimize disruptions and ensure the smooth functioning of their supply chains. This in turn, contributes to the overall success and competitiveness of the organization.

Stages of Supply Chain Management
Stage 1: Planning and Demand Forecasting
Effective supply chain management begins with accurate planning and demand forecasting, which considers factors such as market trends, customer needs, and sales data. This information helps organizations set realistic goals and eliminate unexpected issues, enabling them to allocate resources efficiently and balance inventory levels.
Stage 2: Sourcing and Procurement
Sourcing and procurement involve selecting suppliers, negotiating contracts, and purchasing raw materials or finished goods. Strategic sourcing focuses on finding cost-effective and high-quality suppliers to ensure reliable deliveries, which significantly impacts the overall supply chain performance. Effective procurement practices contribute to reduced costs and risks, fostering strong supplier relationships.
Stage 3: Production and Manufacturing
In the production stage, manufacturers transform raw materials into finished products or assemble components. Efficient manufacturing operations, such as lean and just-in-time (JIT) methodologies, can optimize production lead times, resource utilization, and minimize waste, contributing to better supply chain performance. Ensuring quality control and timely order fulfillment is crucial in satisfying customer requirements and maintaining supply chain efficiency.
Stage 4: Logistics and Transportation
Once products have been manufactured, logistics and transportation come into play. This stage involves coordinating the shipment of goods to customers, distribution centers, or retail outlets. Effective logistics management reduces transportation costs, improves delivery times, and ensures a seamless flow of goods through the supply chain. Employing agile transportation solutions and implementing real-time tracking systems can enhance overall supply chain performance.
Stage 5: Return and Post-Sale Management
The final stage of supply chain management involves handling product returns, repairs, and maintenance or disposal of obsolete items. Efficient return and post-sale management processes can promote customer satisfaction and reduce costs related to reverse logistics. Additionally, integrating sustainability and eco-friendly practices in this stage can further optimize a supply chain's overall performance.
In conclusion, the five stages of supply chain management play a significant role in optimizing its performance. Accurate planning, strategic sourcing, efficient production, effective logistics, and proactive return management contribute to reduced costs, increased customer satisfaction, and improved overall supply chain efficiency. Companies that successfully coordinate and integrate these stages can create a competitive advantage within their respective markets.

Role of Contracts in Establishing Relationships
Contracts play a central role in supply chain management, particularly in fostering and upholding robust relationships between stakeholders in the supply chain. By defining precise terms of engagement, contracts ensure a stable foundation for collaboration among businesses, suppliers, manufacturers, and distributors. This collaborative environment brings about mutual benefits and establishes trust among stakeholders.
Negotiated Agreements and Alignment
Through negotiated agreements, businesses clarify their expectations and requirements, and suppliers commit to fulfilling those needs. This process ensures alignment of goals, thus fostering a harmonious collaboration. Shared objectives further contribute to supply chain efficiency, as all parties strive towards a common goal.
Risk Mitigation and Conflict Resolution
Contracts in supply chain management also serve a vital function in risk mitigation, providing a legal framework to manage and resolve disputes that may arise between parties. By incorporating clauses for handling disputes and possible risks, contracts reduce the likelihood of misunderstandings and legal battles, securing long-term relationships.
Ensuring Continuity and Adaptability
Supply chain contracts ensure continuity and adaptability within the supply chain by laying out guidelines for managing changes in market conditions, technological advancements, and expansions in business operations. Setting out frameworks for addressing unforeseen challenges and disruptions further strengthens the relationships between stakeholders.
Monitoring Performance and Accountability
Performance monitoring and accountability are indispensable components of supply chain contracts. By stipulating measures of success and expectations for each party, contracts enable monitoring, evaluation, and continuous improvement, ultimately contributing to higher levels of satisfaction and cooperation among supply chain stakeholders.
In conclusion, contracts are a crucial instrument in supply chain management, as they serve not only as a legal binding commitment but also a guiding compass for establishing and maintaining strong relationships between supply chain stakeholders. They provide negotiated agreements, risk mitigation, continuity, adaptability, and performance monitoring, ensuring streamlined operations and harmony in the global supply chain network.

Key Components of a Supply Contract
A supply contract in supply chain management encompasses essential elements that are vital in providing transparency, clarity, and enforceability. These components include a detailed description of products and services, delivery terms, payment terms, warranties, quality requirements, and dispute resolution mechanisms.
Product and Service Description
A comprehensive description of the products and services contracted ensures both parties fully understand the expectations and requirements. This detail eliminates ambiguity, strengthens compliance, and safeguards the effective execution of supply chain activities.
Delivery Terms
Defining delivery terms such as dates, locations, modes of transportation, and associated costs contributes to improved transparency and a seamless execution of supply chain operations. Inclusion of penalty clauses for non-adherence further reinforces the enforceability aspect of the contract.
Payment Terms
Establishing explicit payment terms, including the payment amount, currency, invoicing procedures, and timelines, creates clarity and avoids misunderstandings between parties. These provisions also facilitate a smooth financial interaction, promoting trust and integrity within the supply chain.
Warranties
Incorporating well-defined terms for warranties on products or services mitigates risk and potential disputes. These provisions protect both parties' interests, assisting in maintaining a mutually beneficial relationship while ensuring an undisrupted supply chain process.
Quality Requirements
Identifying the quality specifications demanded for products or services significantly contributes to supply chain performance and customer satisfaction. Standard conformity, regular inspections, and quality assurances establish clear expectations and validate a product's compliance with the predetermined requirements.
Dispute Resolution
Integrating clearly defined dispute resolution mechanisms within a supply contract helps avoid disruptions in the supply chain and maintain business continuity. Specifying channels of negotiation, arbitration, or litigation set forth a roadmap for resolving disagreements between parties while maintaining enforceability.
In conclusion, the key components of a supply contract play a crucial role in the ongoing execution of supply chain operations. By detailing these elements within a contract, parties establish a transparent, enforceable, and explicit agreement that governs their specific responsibilities and expectations in the supply chain process. This mutual understanding ultimately leads to improved efficiency and collaboration between parties, ensuring the successful delivery of products and services within the ever-evolving supply chain landscape.

**Step 1: Strategy Development**
The first step in a supply chain management (SCM) plan involves developing a strategy that aligns with the organization's goals, such as reducing costs or increasing inventory turnover. This step helps decision-makers create a road map for executing the plan and overcoming potential challenges.
**Step 2: Supplier Relationship Management**
Once a strategy is established, companies must foster strong relationships with their suppliers, promoting collaboration and information sharing. Building a transparent relationship with suppliers enables organizations to better anticipate challenges and adapt to market fluctuations, ultimately enhancing supply chain efficiency.
**Step 3: Demand and Inventory Management**
Effective SCM requires companies to efficiently manage their demand and inventory levels to prevent stockouts, minimize surplus, and enhance customer satisfaction. By analyzing historical data, forecasting demand, and maintaining optimal inventory levels, organizations can meet consumer needs, increase operational efficiency, and overcome potential challenges.
**Step 4: Manufacturing and Production Planning**
In this step, production schedules are developed to meet customer demand in the most operationally efficient manner. Manufacturing and production planning enable organizations to optimize resource utilization, minimize waste, and balance competing priorities, contributing to the successful achievement of organizational goals.
**Step 5: Transportation and Logistics Management**
The final step in a supply chain management plan is ensuring efficient transportation and logistics. This involves managing inbound and outbound shipments, optimizing routes, and selecting the most cost-effective transportation methods. Implementing effective transportation and logistics management strategies helps to minimize lead times, reduce costs, and ensure timely delivery of products, ultimately contributing to organizational success and overcoming challenges.
In conclusion, the five steps of a supply chain management plan - strategy development, supplier relationship management, demand and inventory management, manufacturing and production planning, and transportation and logistics management - contribute to achieving organizational goals and overcoming challenges by enhancing efficiency, optimizing resource utilization, and maintaining customer satisfaction. Each step plays a critical role in ensuring the supply chain functions effectively and supports the organization's overall objectives.

**Understanding the Supply Chain Stages**
The four stages of supply chains consist of plan, source, make, and deliver. Each stage plays a critical role in determining the efficiency and effectiveness of supply chain management processes.
**Planning and Strategizing**
In the first stage, organizations develop strategies and establish plans for utilizing resources to meet customer demand. Effective planning enables companies to optimize costs, reduce lead times, and ensure availability, allowing for increased competitiveness and customer satisfaction.
**Sourcing and Supplier Management**
The second stage encompasses activities related to procurement, including supplier selection, contract negotiation, and management. Sourcing from reliable suppliers with competitive prices is crucial for organizations to maximize profitability and efficiently utilize resources. Good supplier relationships contribute to reduced disruptions, faster delivery times, and increased quality.
**Manufacturing and Production**
This third stage involves transforming raw materials and components into finished products. Efficient manufacturing processes enable organizations to minimize waste, produce high-quality products, and meet customer demand in a timely manner. Moreover, effective production strategies lead to cost reductions and increased profitability.
**Delivery and Distribution**
In the final stage, organizations ensure products reach their intended destinations through transportation, warehousing, and distribution. Streamlined distribution Networks and transportation strategies help reduce delays, maintain product quality, and enable timely deliveries. Consequently, effective delivery systems contribute towards customer satisfaction, brand reputation, and increased sales.
Overall, the four stages of supply chains significantly impact the efficiency and effectiveness of supply chain management processes. Greater emphasis on planning, sourcing, manufacturing, and delivery lead to optimized processes, reduced costs, and improved customer satisfaction. Therefore, organizations must continually evaluate and enhance these supply chain stages to achieve long-term success and competitiveness in the market.

Importance of Contracts in Supply Chain Management
Promoting Collaboration
Contracts play a central role in supply chain management by fostering collaboration among partners. They establish the groundwork for building trust and forming long-lasting relationships by outlining the responsibilities, expectations, and obligations of each party. Through mutual agreement on roles and the distribution of resources, contracts enable organizations to efficiently coordinate their efforts, promoting synergy and ensuring a seamless flow of goods and services in the supply chain.
Enhancing Transparency
The clarity provided by contracts in terms of outlining terms and conditions, service level agreements, and performance metrics is crucial for transparency in supply chain management. By explicitly stating the rights and duties of all parties, contracts help to prevent potential conflicts or misunderstandings and facilitate smooth information sharing. This transparency enables organizations to monitor and evaluate the performance of their supply chain partners, ensuring that all stakeholders are working together cohesively and in pursuit of common objectives.
Ensuring Accountability
Contracts serve as a powerful tool for establishing accountability in supply chain management. They provide distinct performance benchmarks, timelines, and measurable outcomes for every partner to adhere to and achieve. By setting out these factors, contracts enable organizations to hold their supply chain partners accountable for their actions and deliverables, thus promoting reliability and trust throughout the chain. This accountability mechanism not only guarantees proper execution of tasks but also enables the identification and mitigation of risks in a timely manner, ensuring the overall resilience and effectiveness of the supply chain.
In conclusion, contracts are essential in supply chain management as they promote collaboration, transparency, and accountability among supply chain partners. By effectively utilizing contracts, organizations can foster trust, streamline operations, and ensure efficient coordination, ultimately resulting in a more resilient and successful supply chain.

Introduction to SCM Plan Steps
A Supply Chain Management (SCM) plan entails a system of five critical steps that facilitate the effective implementation of supply chain strategies in a business context. These steps ensure that organizations achieve efficiency in operations, minimize costs, and optimize service levels while managing the entire chain of activities, from procurement to distribution of products to customers.
1. Establish Supply Chain Objectives
The first step involves defining clear objectives based on overall business goals, ensuring alignment between supply chain performance metrics and desired organizational outcomes. Objectives may include improving customer service levels, reducing lead times, or optimizing inventory levels.
2. Conduct a Supply Chain Analysis
The second step is to perform a comprehensive analysis of the supply chain components, which entails evaluating the existing processes, suppliers, logistics infrastructure, and risks. This analysis enables organizations to identify areas of improvement, potential bottlenecks, and risk mitigation strategies, providing a solid foundation for implementing supply chain strategies.
3. Develop Integrated Supply Chain Strategies
The third step revolves around formulating integrated strategies for procurement, production, logistics, and distribution, among others. Employing a cross-functional approach, organizations are equipped to enhance collaboration and streamline operations across different departments and stakeholders, ensuring overall supply chain coherence and effectiveness.
4. Implement the Supply Chain Strategies
In the fourth step, organizations initiate the execution of the devised strategies by incorporating new processes, engaging with suppliers, and investing in logistics infrastructure. Accurate monitoring of performance metrics and the adaptation of strategies as needed contribute to successful implementation and continuous improvement.
5. Evaluate and Continuously Improve Supply Chain Performance
Lastly, regular evaluation and performance measurement of the established supply chain strategies guarantees continuous improvement and the identification of further opportunities for optimization. By establishing a feedback loop, organizations can effectively adapt their supply chain strategies to respond to market dynamics and customer requirements.
In conclusion, the five steps of a SCM plan guide organizations in systematically designing, implementing, and evaluating supply chain strategies, enabling them to achieve operational excellence, cost efficiency, and fast response to changing market conditions. By embracing these steps, businesses can maximize the value and effectiveness of their supply chain management efforts.

Stages of Supply Chains
The four stages of supply chains are plan, source, make, and deliver. These stages play a vital role in determining the overall performance and adaptability of supply chain management processes.
Planning Phase
In the planning phase, companies devise strategies for effectively meeting customer demand while minimizing costs and inventory. This stage influences the efficiency, flexibility, and responsiveness of supply chain management processes by determining optimal production and distribution plans.
Sourcing Phase
During the sourcing phase, organizations procure raw materials, goods, and services from suppliers. The choice of suppliers and negotiation of contracts can have a significant impact on the cost, quality, and availability of inputs for the production process, ultimately affecting a supply chain's performance and adaptability.
Manufacturing Phase
In the manufacturing phase, companies transform raw materials into finished products. The efficiency of production processes, adoption of new technologies, and the ability to maintain high-quality standards play a crucial role in determining a supply chain's competitiveness. Rapid changes in market demands and product preferences necessitate continuous improvements in manufacturing processes to ensure adaptability.
Delivery Phase
Finally, in the delivery phase, organizations distribute finished products to customers through various channels, including direct-to-consumer models, retailers, and wholesalers. Effective logistics management, transportation choices, and technology utilization influence the speed, accuracy, and cost of order fulfillment. Adaptable supply chains are better prepared to respond to disruptions or changes in market conditions, enabling businesses to maintain high levels of customer satisfaction.
In conclusion, all four stages of supply chains significantly influence the overall performance and adaptability of supply chain management processes. Companies must focus on optimizing each phase to ensure a competitive and responsive supply chain that meets customer demands while minimizing costs and risks.

Contracts as Key Tools
The importance of contracts in supply chain management cannot be overstated, particularly when it comes to fostering trust, clarity, and mutual understanding among the involved parties. Contracts serve as key tools to outline the expectations, rights, and obligations of each party, effectively creating a blueprint for collaboration and risk management.
Establishing Trust
A fundamental aspect of successful supply chain management is building trust among the different parties involved, and contracts play a crucial role in this process. By specifying the performance requirements, payment terms, and delivery conditions, contracts create a shared understanding of each party's responsibilities. Additionally, they provide mechanisms for addressing any disputes or performance issues, thus establishing a solid foundation for long-term collaboration.
Enhancing Clarity
Unclear or ambiguous business relationships can lead to miscommunication, misunderstandings, and even costly errors. Contracts provide a sense of clarity and certainty for the parties involved in the supply chain by setting forth clear definitions of roles, responsibilities, and expectations. They also outline processes for communication, feedback, and amendment, ensuring that all parties stay informed and can adapt to changes as needed.
Promoting Mutual Understanding
A well-crafted contract can be instrumental in promoting mutual understanding among the parties in the supply chain. It allows the parties to negotiate terms, exchange ideas, and address concerns before formalizing their commitments. Such open communication fosters collaboration and leads to an agreement that is beneficial for all involved. Ultimately, this enhances the overall efficiency, performance, and stability of the entire supply chain.
Minimizing Risks
Contracts are essential for mitigating risks in supply chain management. By establishing performance standards, liability provisions, and indemnification clauses, they protect both parties from potential losses or damages. Furthermore, they outline dispute resolution processes, ensuring that any issues arising during the course of the business relationship are addressed promptly and fairly.
In conclusion, the use of contracts in supply chain management is integral to building trust, enhancing clarity, and promoting mutual understanding among the involved parties. By laying out the terms and conditions, contracts foster greater collaboration and reduce the potential for disputes, ultimately leading to a more stable and resilient supply chain.

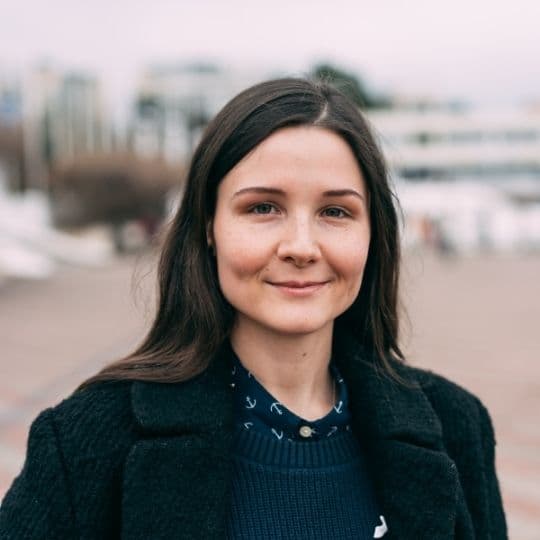
I am Amara Weiss and for many years I have worked in the field of education, specifically in the area of technology. I firmly believe that technology is a powerful tool that can help educators achieve their goals and improve student outcomes. That is why I currently work with IIENSTITU, an organization that supports more than 2 million students worldwide. In my role, I strive to contribute to its global growth and help educators make the most of available technologies.