Maximizing Supply Chain TCO: Managing Life Cycle Costs

It was a crisp autumn morning when I first realized the profound impact that understanding the total cost of ownership (TCO) could have on my business decisions. I remember sitting in the conference room, gazing out at the fiery hues of leaves fluttering in the breeze, as our procurement team debated over two seemingly similar suppliers. On paper, one offered a lower purchase price, but our seasoned financial analyst urged us to look beyond the immediate costs. That day marked a turning point in how I approached purchasing—embracing a holistic view that encompasses every facet of cost associated with owning an asset.
Concept | Explanation | Benefits |
---|---|---|
Total Cost of Ownership (TCO) | A comprehensive view of the total cost of an item over its entire life cycle, not just the purchase price. | Understanding TCO can help businesses ensure they are getting the most value for their money. |
Purchase Price | The initial cost paid to acquire an item. | While a significant part of TCO, focusing solely on purchase price when determining value can lead to overlooking additional costs. |
Transportation | Covers costs involved in transporting the item from the vendor to business and possibly to customers. | Understanding these costs can help identify savings opportunities in shipping and logistics. |
Inventory Holding Costs | Associated with storing inventory such as warehousing, handling, insurance, and losses through theft, damage, and obsolescence. | Understanding these costs can assist in inventory optimization decisions. |
Quality Inspection & Defect Resolution | Costs involved in quality control and fixing or replacing defective items. | Reducing these costs can improve product quality and customer satisfaction. |
Duties, Tariffs and Taxes | Financial payments required by governments for transactions. | Predicting these charges accurately can optimize cross-border transactions. |
Maintenance Costs | These are costs associated with maintaining the performance and value of an item over its life cycle. | Understanding these costs will improve long-term budgeting for business operations. |
Disposal Costs | Costs associated with disposing or recycling an item at the end of its life cycle. | These can influence decisions on environmentally friendly business practices. |
Recoverable Value | The potential value an item might have at the end of its life cycle, such as resale or scrap value. | Knowing this value can influence purchasing decisions and item life cycle management. |
Product Liability | The legal liability a manufacturer or trader incurs for producing a faulty product. | Understanding this factor can help in assessing risks and liabilities related to an item. |
Introduction
The Total Cost of Ownership
Factors Affecting TCO
Benefits of Understanding TCO
Conclusion
Grasping the Concept of Total Cost of Ownership
At its core, the total cost of ownership is not just about the upfront purchase price. It's about the entire spectrum of costs that accrue over the item’s lifetime. Think of it like buying a car. While the sticker price might fit your budget, have you considered the ongoing expenses like fuel, maintenance, insurance, and depreciation? Similarly, in business, understanding TCO means looking beyond the initial expenditure and considering all future costs that an item or service will entail.
Why TCO Matters More Than You Think
When we dwell only on the purchase price, we might miss out on hidden costs that can significantly affect profitability. For instance, a cheaper machine might save money upfront but could lead to higher maintenance costs down the line. On the other hand, investing in a slightly more expensive piece of equipment with better energy efficiency could save substantial amounts in operational costs over time.
Factors Affecting TCO
Unpacking the total cost of ownership reveals a myriad of factors. These can be broadly categorized into:
1- Acquisition Costs: These are the direct costs involved in purchasing an item. They include:
- Purchase Price: The initial amount paid to acquire the item.
- Installation Fees: Costs associated with setting up the item for use.
- Training Costs: Expenses for teaching staff how to use the new asset.
The actual cost of a supply chain is determined by the costs incurred throughout its entire life cycle.

2- Operating Costs: Ongoing expenses necessary to keep the item functional.
- Maintenance and Repairs: Regular upkeep and fixing any issues that arise.
- Energy Consumption: The cost of power or fuel needed for operation.
- Supplies and Consumables: Materials required for the item to function properly.
3- Ownership Costs: Indirect costs that come with owning an asset.
- Insurance: Protecting the asset against potential risks.
- Taxes and Permits: Legal obligations associated with ownership.
- Depreciation: The decrease in value over time.
4- Disposal Costs: Expenses linked to either disposing of or reselling the item at the end of its life.
- Environmental Fees: Costs for proper disposal to meet environmental regulations.
- Salvage Value: Potential income from selling the asset after use.
Consider the following long-term factors that can subtly influence TCO:
Quality Inspection and Defect Resolution Costs: Investing in quality assurance can prevent defective products from reaching customers, saving money on returns and preserving brand reputation.
Inventory Holding Costs: The longer you hold inventory, the higher the costs due to storage, insurance, and potential obsolescence.
Shrinkage, Safety, and Loss Prevention: Implementing measures to prevent theft or damage can reduce losses, impacting the overall cost of ownership.
An Example to Illustrate TCO
Let me share an experience from my friend's small manufacturing business. He faced a choice between two suppliers for a critical component. Supplier A offered a lower price per unit, while Supplier B's price was slightly higher but promised better reliability.
Initially, the lower cost seemed appealing. However, after calculating the TCO, including factors like defect rates, delivery times, and support services, it became evident that Supplier B was the more cost-effective option in the long run. By choosing Supplier B, he reduced downtime due to faulty parts and improved his product's overall quality, leading to higher customer satisfaction.
The Intersection of TCO and Project Management Strategies
Understanding TCO is not just vital for procurement decisions but also plays a significant role in project management. When we consider strategies like the critical path method project management strategy, the focus is on identifying the sequence of crucial steps that determine the project's duration.
By incorporating TCO into this strategy, project managers can:
Optimize Resource Allocation: By understanding the total costs, resources can be allocated more efficiently to critical tasks, ensuring the project stays on schedule and within budget.
Mitigate Risks: Identifying potential high-cost areas allows for proactive measures to minimize financial risks associated with project delays or overruns.
Enhance Decision Making: A clear picture of TCO supports better decisions regarding subcontracting, equipment purchases, and scheduling.
Long-Tail Keywords in TCO and Project Management
In the realm of business and project management, it's imperative to stay informed about concepts like:
Strategic procurement methods for cost savings
Impact of inventory management on TCO
Long-term benefits of efficient energy consumption in operations
Risk assessment techniques in TCO calculation
Cost-benefit analysis in equipment procurement decisions
Incorporating these concepts into your strategic planning can lead to more informed decisions and ultimately, a healthier bottom line.
Benefits of Understanding TCO
Recognizing and applying the concept of TCO brings numerous advantages:
1- Informed Purchasing Decisions: By evaluating all costs, businesses can choose options that offer the best value over time, not just the lowest initial price.
2- Cost Savings: Identifying areas where costs can be reduced—like energy-efficient equipment or bulk purchasing—can lead to significant savings.
3- Improved Negotiations with Suppliers: Understanding the full cost structure allows businesses to negotiate better terms, focusing on long-term value rather than just upfront costs.
4- Risk Management: Anticipating future costs helps in planning for potential financial risks and setting aside reserves for unexpected expenses.
5- Enhanced Budgeting and Forecasting: A comprehensive view of costs enables more accurate budgeting and financial projections.
Personal Insights on TCO Benefits
Reflecting on my own experiences, embracing TCO has transformed how I approach business investments. I recall investing in a new software system for our team. While there was a free version available, we opted for a paid version with better support and additional features. Over time, this choice proved wise as it:
Increased Productivity: The additional features streamlined our workflows.
Reduced Downtime: Prompt support resolved any issues quickly.
Enhanced Collaboration: Improved tools facilitated better teamwork.
The initial higher cost was offset by the long-term gains we realized—an embodiment of TCO's value.
Practical Steps to Calculate TCO
Calculating TCO doesn't have to be overwhelming. Here's a simple approach:
List All Costs: Start by listing every possible cost associated with the item over its expected life span.
Gather Data: Collect information on operating expenses, maintenance schedules, disposal costs, etc.
Use a TCO Calculator: There are tools and formulas available in texts like Investment Decision-Making in Asset Management by John Dyson (2017) that can help simplify calculations.
Review and Adjust: Regularly revisit TCO estimates to account for changes in usage, market conditions, or unforeseen expenses.
Key Considerations in TCO Calculations
When calculating TCO, keep in mind:
Time Value of Money: Consider that money now is worth more than the same amount in the future due to its earning potential.
Life Span of the Asset: The longer the asset lasts, the more spread out the costs become.
Depreciation Methods: Different assets depreciate differently; choose an appropriate method for accurate accounting.
Conclusion
Embracing the concept of total cost of ownership has been a game-changer in my professional journey. It has shifted my focus from short-term gains to long-term value, ensuring that decisions are not just cost-effective but also strategic and sustainable.
By understanding TCO, businesses can:
Make Smarter Investments: Align purchases with long-term goals and financial health.
Enhance Operational Efficiency: Identify and eliminate wasteful expenditures.
Strengthen Competitive Advantage: Optimize costs to offer better pricing or invest in innovation.
As we navigate the complexities of today's business environment, tools like TCO analysis are indispensable. They not only illuminate the true cost landscape but also empower us to make decisions that foster growth and resilience.
References
1- Dyson, J. (2017). Investment Decision-Making in Asset Management: Building Value through Smart Capital Decisions. New York: Wiley.
2- Thompson, A. A. (2016). Supply Chain Management: Concepts, Techniques and Practices Enhancing Value Through Collaboration. New Jersey: Pearson Education.
3- Johnson, G., & Scholes, K. (2018). Exploring Corporate Strategy. London: Prentice Hall.
4- Smith, M. (2015). Project Management: Strategic Financial Planning for Projects. Boston: McGraw-Hill.
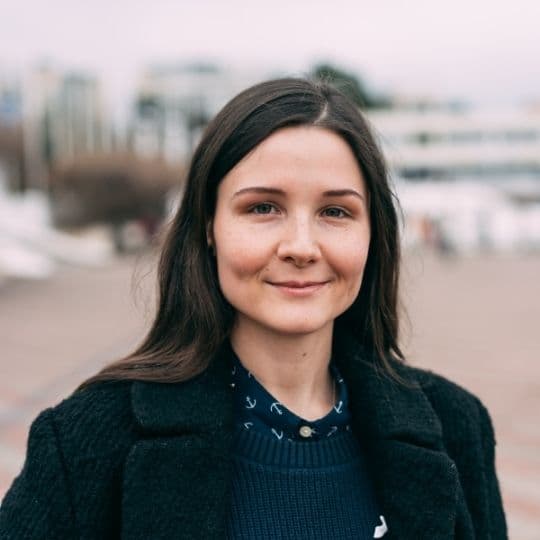
I am Amara Weiss and for many years I have worked in the field of education, specifically in the area of technology. I firmly believe that technology is a powerful tool that can help educators achieve their goals and improve student outcomes. That is why I currently work with IIENSTITU, an organization that supports more than 2 million students worldwide. In my role, I strive to contribute to its global growth and help educators make the most of available technologies.