Reverse Logistics: Benefits, Challenges & Strategies

I still remember my early days working in the logistics department of a mid-sized manufacturing company. Back then, we were so focused on getting our products out the door that we hardly paid attention to what happened after they reached the customer. That was until we faced a significant product recall that turned our operations upside down. It was a wake-up call that highlighted the importance of reverse logistics—a crucial but often overlooked aspect of supply chain management.
Aspect | Details | Additional Information |
---|---|---|
Definition & Scope of Reverse Logistics | Involves returning products from consumers back to origins for value recapture or proper disposal. | An essential tool for maximizing business ROI and maintaining product competitiveness. |
Benefits for Logistics Management | Reduced costs for transport and disposal, improved customer service, increased inventory accuracy, and efficient warehousing. | Efficient return processes can enhance overall logistics operations and customer satisfaction. |
Challenges in Implementation | High setup and maintenance costs, integration complexities, managing returns, and fraud risk. | Effective strategies can mitigate these challenges in the implementation of reverse logistics. |
Strategies for Optimization | Efficient returns processing, quality control measures, advanced technologies, and improved customer service. | Implementing these strategies can help streamline reverse logistics and enhance performance. |
Impact of Technology | Streamline returns, reduce costs, improve returns prediction and supply chain optimization. | Technologies like artificial intelligence enhance the overall effectiveness of reverse logistics. |
Essentiality of Reverse Logistics | Provides benefits like cost reduction, improved service levels, and maximized ROI. | Despite challenges, reverse logistics is vital for competitive positioning in the market. |
Fraud & Theft Risks | Returned goods are exposed to fraud and theft risks. | Quality control measures and tracking technologies can help mitigate these risks. |
Customer Service Focus | Important for providing timely information and support to customers making returns. | An enhanced customer service experience helps maintain client relationships and reputation. |
Supply Chain Processes | Optimization and prediction of returns affect overall supply chain processes. | Integrating reverse logistics well within the supply chain can yield greater efficiencies. |
Role of Artificial Intelligence | Aids in predicting returns and supply chain optimization. | AI and other advanced technologies can further enhance and streamline reverse logistics processes. |
Definition and Scope of Reverse Logistics
Benefits of Reverse Logistics for Logistics Management
Challenges in Implementing Reverse Logistics Strategies
Strategies for Optimizing Reverse Logistics Processes
Impact of Technology on Enhancing Reverse Logistics
Understanding Reverse Logistics
Reverse logistics isn't just a fancy buzzword in the logistics world. It's the process of moving goods from their final destination back to the manufacturer or distribution center for the purpose of capturing value or proper disposal. This can include returns, recycling, refurbishment, or resale. Essentially, it's all about managing the flow of products in reverse through the supply chain.
The Scope of Reverse Logistics
The scope of reverse logistics is quite broad and includes:
Returns Management: Handling customer returns efficiently.
Refurbishment and Remanufacturing: Restoring products to like-new condition for resale.
Recycling and Waste Disposal: Properly disposing of products that cannot be reused.
Recall Management: Managing product recalls promptly and effectively.
Sustainable Practices: Implementing eco-friendly processes to minimize environmental impact.
By effectively managing these areas, companies can recover value, reduce costs, and enhance customer satisfaction.
The Benefits of Reverse Logistics
Implementing a robust reverse logistics system brings a host of benefits. For starters, it can significantly reduce costs associated with returns and waste. When we began focusing on reverse logistics in my company, we saw a noticeable decrease in expenses related to product disposal and a boost in revenue from refurbished goods.
Cost Reduction
By reclaiming value from returned products, companies can:
1- Minimize Waste Disposal Costs: Properly sorting and processing returns reduces the volume of waste sent to landfills.
Analyzing the Implications and Benefits of Asset Tracking in Business Operations
Unlocking Benefits from CPFR: A Collaborative Planning Journey
2- Recover Assets: Refurbished products can be resold, adding an extra revenue stream.
3- Optimize Inventory Levels: Understanding return patterns helps in adjusting inventory accordingly.
Enhanced Customer Satisfaction
Customers appreciate hassle-free return policies and swift resolutions. An efficient reverse logistics process ensures that customers remain loyal and satisfied.
Environmental Responsibility
Companies that focus on recycling and responsible disposal demonstrate corporate social responsibility. This not only helps the planet but also boosts the company's image among eco-conscious consumers.
Challenges in Implementing Reverse Logistics Strategies
Of course, it's not all sunshine and rainbows. Implementing reverse logistics comes with its own set of challenges.
High Initial Costs
Setting up a reverse logistics system can be expensive. It requires investment in infrastructure, technology, and training. Small businesses might find it particularly daunting to allocate resources for this purpose.
Complexity of Operations
Managing returns is inherently more complicated than forward logistics. Products can come back in various conditions, and handling them requires flexible processes. Sorting, inspecting, and deciding the fate of each item can be labor-intensive.
Reverse logistics can be challenging, but the rewards are worth the effort.

Risk of Fraud and Theft
There's always the risk that return policies can be abused. Detecting fraudulent returns is a significant concern that requires robust monitoring systems.
Integration with Existing Systems
Integrating reverse logistics processes with existing supply chain systems can be tricky. It demands seamless coordination between different departments and technology platforms.
Strategies for Optimizing Reverse Logistics Processes
Despite the challenges, there are effective strategies to optimize reverse logistics.
Develop Clear Return Policies
Having a clear and transparent return policy helps manage customer expectations and streamlines the return process. Customers should know:
Timeframes for returns
Condition requirements
Refund or exchange options
Invest in Technology
Technological solutions like automated tracking systems and data analytics can significantly enhance reverse logistics. For example:
Implementing Return Merchandise Authorization (RMA) Systems: Helps in tracking returns and processing them efficiently.
Using Data Analytics: Predicts return trends and helps in inventory management.
Train Staff Adequately
Employees should be well-trained in handling returns, refurbishments, and customer interactions. After all, they are the frontline in managing reverse logistics operations.
Collaborate with Partners
Working closely with suppliers, distributors, and even competitors can lead to shared solutions that benefit everyone. For instance, joint recycling programs can reduce costs and environmental impact.
The Impact of Technology on Reverse Logistics
Technology has been a game-changer in reverse logistics. I recall when we introduced an advanced tracking system in our company—it was like night and day compared to our old methods.
Automation and Robotics
Automation can handle repetitive tasks like sorting and processing returns, reducing errors and increasing efficiency.
Artificial Intelligence (AI)
AI can predict return patterns, detect fraudulent activities, and optimize routes for transportation.
Internet of Things (IoT)
IoT devices can monitor products throughout their lifecycle, providing valuable data on performance and potential failures.
Blockchain Technology
Blockchain offers a secure and transparent way to track products, ensuring authenticity and preventing fraud.
Personal Experiences in Reverse Logistics
On a more personal note, I once had to oversee the return process for a batch of defective products. It was a hectic time, but it taught me the importance of having a solid reverse logistics strategy. We had to coordinate with multiple departments, manage customer communications, and ensure that the defective products were properly recycled. It wasn't easy, but it reinforced the value of being prepared for such situations.
Tips for Navigating Reverse Logistics Challenges
Having been through the ups and downs, here are some tips I'd offer:
Stay Flexible: Be ready to adapt processes as needed.
Communicate Clearly: Keep all stakeholders informed.
Prioritize Customer Service: A satisfied customer is more likely to remain loyal, even after a return.
Relating Reverse Logistics to Career Development
Interestingly, the complexities of reverse logistics can also impact career paths within a company. Employees might find themselves seeking new roles or responsibilities due to shifting operational needs. In such cases, understanding how to navigate internal processes becomes crucial.
Reassignment Request Letter Tips and Information
For those looking to move into roles related to reverse logistics, it's important to craft a compelling reassignment request letter. Here are some tips:
1- Highlight Relevant Experience: Emphasize any background in supply chain management or customer service.
2- Express Enthusiasm: Show genuine interest in reverse logistics and its importance.
3- Provide Solutions: Mention how you can contribute to optimizing reverse logistics processes.
By following these reassignment request letter tips and information, employees can better position themselves for opportunities in this growing field.
The Future of Reverse Logistics
Looking ahead, reverse logistics will only become more critical. With the rise of e-commerce, returns are increasing, and companies must be prepared to handle them efficiently.
Sustainability and Reverse Logistics
Sustainability will continue to drive reverse logistics strategies. Consumers are more environmentally conscious, and companies that prioritize green initiatives will stand out.
Global Supply Chain Integration
As supply chains become more global, reverse logistics will need to adapt to international regulations and logistics challenges.
Continuous Improvement
Companies must adopt a mindset of continuous improvement, regularly assessing and refining their reverse logistics processes.
Conclusion
Reverse logistics may not always be in the spotlight, but it's an essential component of effective logistics management. By embracing the challenges and leveraging technology, companies can turn reverse logistics into a competitive advantage.
It's been quite a journey from my early days in logistics to now. I've seen firsthand how powerful reverse logistics can be when given the attention it deserves. So, whether you're a seasoned professional or just starting out, don't underestimate the impact of a well-managed reverse logistics system.
After all, in the complex dance of supply chain management, sometimes you have to take a few steps back to move forward.
References
Rogers, D. S., & Tibben-Lembke, R. S. (1999). Going Backwards: Reverse Logistics Trends and Practices. Reverse Logistics Executive Council.
Blumberg, D. F. (2004). Introduction to Management of Reverse Logistics and Closed Loop Supply Chain Processes. CRC Press.
Stock, J. R., & Mulki, J. P. (2009). Product returns processing: an examination of practices of manufacturers, wholesalers/distributors, and retailers. Journal of Business Logistics, 30(1), 33-62.
Blackburn, J. D., Guide Jr, V. D. R., Souza, G. C., & Van Wassenhove, L. N. (2004). Reverse supply chains for commercial returns. California Management Review, 46(2), 6-22.
Carter, C. R., & Ellram, L. M. (1998). Reverse logistics: A review of the literature and framework for future investigation. Journal of Business Logistics, 19(1), 85-102.
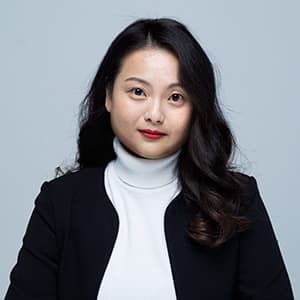
Yu Payne is an American professional who believes in personal growth. After studying The Art & Science of Transformational from Erickson College, she continuously seeks out new trainings to improve herself. She has been producing content for the IIENSTITU Blog since 2021. Her work has been featured on various platforms, including but not limited to: ThriveGlobal, TinyBuddha, and Addicted2Success. Yu aspires to help others reach their full potential and live their best lives.