Optimizing Logistics: Material Handling & Storage

Streamlining material handling and storage in any organization can feel like trying to solve a complex puzzle. I remember when I first started working in the logistics sector, the warehouse felt like a maze—products scattered, workers hustling without a clear direction, and delays becoming the norm rather than the exception. It was evident that without the right strategies in place, inefficiencies would continue to plague the supply chain. However, with careful planning and the implementation of effective systems, it's entirely possible to transform this chaos into a well-oiled machine.
Key Concepts | Explanation | Benefits |
---|---|---|
Importance of Material Handling & Storage Systems | These systems are crucial for efficient inventory movement in the supply chain. The system must be tailored to the organization's specific needs to avoid product damage, delivery delays and excess costs. | Efficient inventory movement, Reduces product damage and delivery delays, Lowers overhead costs |
Factors in Selecting Material Handling System | Considerations include the volume of material, required speed for movement, level of customer service, type of material, and size and shape of items. | Ensures a tailored system to meet specific needs, Enhances customer service capabilities, Increases overall efficiency |
Automation | Refers to the use of technology to automate specific processes, such as moving materials from one location to another. | Improves efficiency, Reduces labor costs, Ensures consistency |
Mechanization | Refers to the use of machines to perform specific tasks, such as lifting and transporting large items. | Saves time, Decreases risk of human error, Reduces labor requirements |
Maximizing Space Utilization | The goal is to optimize floor and cubic space usage in a warehouse. Supports speedy movement of goods and maximizes vertical space. | Improved storage efficiency, More effective inventory management, Cost savings on warehouse space |
Volume of Material Handling | How much material a system is required to handle impacts the type of system chosen. | Properly addressed, it can improve system efficiency and reduce strain on resources. |
Speed of Material Movement | The rate at which inventory must move impacts the system selected. | Optimizes inventory turnaround times, Reduces holding costs. |
Customer Service | The level of service to be offered to the customer is a critical factor in choosing a system. | Ensures customer satisfaction, Supports repeat business. |
Type of Material Handling | Consideration of the inventory's variety is crucial in deciding which system to implement. | Ensures system can handle inventory variety, Reduces risk of damage. |
Size and Shape of Items | Selection of a system also depends on the size and shape of the items in inventory. | Allows for proper planning of storage and movement methods, Minimizes potential for inventory damage. |
Introduction
The Importance of Material Handling & Storage Systems
Factors to Consider When Selecting a Material Handling System
Benefits of Automation & Mechanization
Maximizing Space Utilization
The Heart of Logistics: Material Handling & Storage Systems
At the core of any successful supply chain management lies the efficiency of its material handling and storage systems. These systems are not just about moving goods from point A to point B; they're about ensuring that every product reaches its destination safely, promptly, and cost-effectively. I recall a time when our company's outdated handling system led to consistent delays and damaged goods. Customers were unhappy, and we knew something had to change.
Understanding Supply Chain Management
Before diving deeper, it's essential to grasp the meaning of logistics and how it intertwines with supply chain management. Logistics, in its simplest form, refers to the detailed coordination of complex operations involving people, facilities, and supplies. On the other hand, supply chain management (SCM) encompasses the entire production flow of goods or services—from the raw components to delivering the final product to the consumer.
In essence, SCM is like the backbone of any business that deals with products. It involves supply chain activities such as sourcing, procurement, conversion, and logistics management activities. Effective SCM management ensures that businesses can cut excess costs and deliver products faster to the consumer.
Factors to Consider When Selecting a Material Handling System
When we faced challenges in our warehouse, we realized that selecting the right material handling system wasn't just about picking the latest technology or the cheapest option. It was about understanding our specific needs and the unique demands of our operations.
Here are some crucial factors we considered:
1- Volume of Material: The quantity of goods we handled daily significantly influenced the type of system we needed.
2- Speed Requirements: Fast-moving goods required systems that could keep up with the pace without causing bottlenecks.
3- Customer Service Needs: We had to ensure that the system could meet our promise to customers regarding delivery times and product availability.
4- Type and Nature of Materials: Handling delicate electronics is different from managing bulk raw materials.
5- Space Constraints: Our warehouse space was limited, so maximizing space utilization was paramount.
6- Labor Considerations: We needed to consider the availability and cost of labor—could automation be more efficient?
7- Flexibility and Scalability: The system had to adapt to changing demands and seasonal fluctuations.
The Role of Automation & Mechanization
Embracing automation and mechanization was a game-changer for us. Initially, there was skepticism—would machines replace jobs? Would the cost of investment be justifiable? However, the benefits soon became evident.
Automation refers to using control systems and technology to manage processes with minimal human intervention. For instance, automated conveyor belts, robotic arms for picking and placing, and computerized tracking systems enhanced our efficiency.
Mechanization, on the other hand, involves using machinery to assist or replace human labor, especially in tasks that are repetitive or physically demanding. Equipment like forklifts, pallet jacks, and automated storage and retrieval systems (AS/RS) fall into this category.
The key to successful logistics is efficient material handling and storage.

Benefits We Experienced:
Increased Efficiency: Tasks were completed faster, reducing lead times.
Reduced Errors: Automation minimized human errors, especially in inventory management.
Improved Safety: Mechanization reduced the risk of injuries from manual handling.
Cost Savings: Over time, the reduction in labor costs and increased productivity led to significant savings.
Maximizing Space Utilization: Making Every Square Foot Count
Space in a warehouse is like gold. Every unused or poorly used square foot is a missed opportunity. When we started focusing on supply and chain management, we realized that optimizing our space wasn't just about fitting more products but about enhancing the overall flow and accessibility.
Strategies We Implemented:
1- Vertical Storage Solutions: By utilizing vertical space with tall shelving units and mezzanines, we significantly increased our storage capacity.
2- Cross-Docking: This involved unloading materials from incoming trucks and loading them directly onto outbound trucks, reducing storage needs.
3- Inventory Management Systems: Implementing advanced SCM supply software helped us keep track of stock levels and reduce overstocking.
4- Aisle Optimization: Narrower aisles and efficient layout designs allowed more storage space without compromising accessibility.
5- Regular Audits: Periodically reviewing our storage usage helped identify areas of improvement.
Balancing Multiple Factors for Seamless Movement
Creating efficient material handling and storage systems isn't just about individual components but about how they all come together. It's like orchestrating a symphony—each instrument (or in this case, each department) must be in harmony with the others.
Key Elements to Balance:
Coordination Between Departments: Ensuring smooth communication between procurement, production, storage, and delivery teams.
Technology Integration: Using integrated systems where data flows seamlessly between departments, enhancing visibility and decision-making.
Employee Training: Our staff needed to be adept at using new systems and understanding the importance of their roles in the bigger picture.
Real-Life Example: Transforming Challenges into Opportunities
At one point, we received a reassignment request letter from a key employee who felt that the inefficiencies were too frustrating to handle. This was a wake-up call. We took this feedback seriously and held open forums to understand the ground-level challenges better.
By involving our team in the problem-solving process, we not only found practical solutions but also boosted morale. Their insights led to simple yet effective changes, such as rearranging the storage layout and implementing suggestion boxes for continuous improvement.
The Broader Impact on Chain of Supply Management
Effective material handling and storage systems don't just benefit the warehouse—they have ripple effects throughout the entire management chain supply. When products move smoothly through the supply chain, customer satisfaction increases, company reputation improves, and profitability grows.
Benefits Beyond the Warehouse:
Enhanced Customer Experience: Timely deliveries and fewer errors lead to happier customers.
Competitive Advantage: Efficiency can set a company apart in a crowded market.
Sustainability Efforts: Efficient systems often reduce waste and energy consumption.
Tips for Organizations Looking to Improve
1- Assess Current Systems: Understand where inefficiencies lie. Is it in the handling, storage, or movement of goods?
2- Engage with Employees: They often have valuable insights into day-to-day operations.
3- Invest in Technology Wisely: Not all solutions require high-tech investments. Sometimes, simple mechanization can make a big difference.
4- Continuous Improvement: Regularly review and adjust systems as needed.
5- Educate Yourself: Understanding the intricacies of supply chain mgmt through courses or literature can provide fresh perspectives.
Conclusion: The Key to Successful Supply Chain Management
Streamlining material handling and storage is not just about reducing costs or speeding up processes; it's about creating a cohesive and efficient system that benefits everyone involved—from the supplier to the end customer.
Reflecting on our journey, I realize that the challenges we faced were stepping stones to building a more robust and resilient supply chain. By considering speed requirements, customer service needs, and space utilization techniques such as automation or mechanization, organizations can indeed optimize their operations for maximum efficiency.
Remember, the key to successful logistics is efficient material handling and storage. It's a continuous journey of balancing multiple factors to ensure seamless movement between departments—from production to delivery!
References
1- Christopher, M. (2016). Logistics & Supply Chain Management. Pearson UK.
2- Rushton, A., Croucher, P., & Baker, P. (2017). The Handbook of Logistics and Distribution Management. Kogan Page Publishers.
3- Arnold, J. R. T., Chapman, S. N., & Clive, L. M. (2018). Introduction to Materials Management. Pearson.
4- Johnson, J. C., & Wood, D. F. (2019). Contemporary Logistics. Prentice Hall.
5- Mangan, J., Lalwani, C., & Lalwani, C. L. (2016). Global Logistics and Supply Chain Management. John Wiley & Sons.
Note: This content is based on professional experiences and widely recognized publications in the field of logistics and supply chain management.
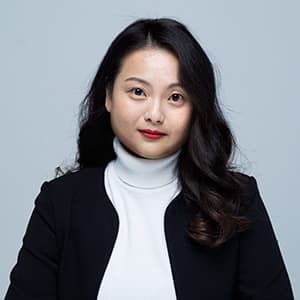
Yu Payne is an American professional who believes in personal growth. After studying The Art & Science of Transformational from Erickson College, she continuously seeks out new trainings to improve herself. She has been producing content for the IIENSTITU Blog since 2021. Her work has been featured on various platforms, including but not limited to: ThriveGlobal, TinyBuddha, and Addicted2Success. Yu aspires to help others reach their full potential and live their best lives.