Optimizing Logistics Mgmt: Material Handling

Activity | Description | Importance |
---|---|---|
Loading and Unloading | First and last step in the material process respectively. Involves offloading materials from the vehicle upon arrival and finally, packing them into boxes for dispatch. | Ensures that goods are adequately received and dispatched from the warehouse, minimizing potential damage. |
Material Movement | Involves the transportation of goods within the warehouse with the help of machinery | Ensures efficient storing and retrieval of goods within the warehouse. |
Order Filling | Final activity where goods are picked, packed, and shipped to the customer | Vital in ensuring correct items are shipped to customers |
Attention to Detail | Extremely essential across all activities to ensure that tasks are carried out correctly | Avoids errors and enhances the efficiency of the warehouse operations |
Usage of Equipment | Employment of machinery like trolleys, conveyors, or forklifts to aid in material handling | Increases productivity and decreases manual labor |
Material Storage | Post-unloading, materials are stored in an assigned place | Facilitates easy location and accessibility. Helps in managing inventory effectively |
Material Brace | Additional efforts put in to secure the material after loading | Prevents damage during transportation |
Order Pickup | Involves moving the material from the storage to packing and then the loading area | Ensures effective retrieval and dispatch of goods |
Hand-picking | Technique mainly used during order filling, where items are picked manually | Helps in further ensuring the correct items are picked and shipped |
Optimizing Logistics Management | Efficiency is sought through all aspects, particularly material handling | Improving efficiency leads to cost-saving and improves overall warehouse operations |
This article has discussed the three main activities of material handling - loading and unloading, material movement, and order filling - and how they work together to ensure the smooth operation of a warehouse. It has also highlighted the importance of paying attention to detail to ensure that goods are handled correctly and efficiently.
Introduction
Loading and Unloading
Material Movement
Order Filling
Conclusion
Introduction: Material handling is a fundamental function of warehouse operations and is essential for the efficient and effective management of goods and services. It is the process of transporting and storing materials within a facility and is divided into three main activities: loading and unloading, material movement, and order filling. This article will discuss each activity in detail and explain how they work together to ensure the smooth operation of a warehouse.
Loading and Unloading
The loading and unloading activities are the first and last steps in the material handling process. Unloading is performed when goods arrive in a warehouse and involve offloading them from the vehicle. Loading is the last function performed in a warehouse and involves packing the material into boxes and loading them onto the vehicle at the loading area. Additional efforts may be required to brace the load to prevent damage.
Material Movement
Material movement is transporting goods from one place to another within the warehouse. This can be done manually or with the help of material-handling equipment such as trolleys, cranes, conveyors, or forklifts.
Incoming material that is unloaded must be moved to an assigned place in the warehouse for temporary storage. In contrast, during order pickup, the material must be moved from the storage area to the packing area and then to the loading area.
Order Filling
Order filling is the last activity in the material handling process. It involves picking, packing, and shipping the goods to the customer. This activity is usually done by hand and requires careful attention to detail to ensure that the correct items are picked, packed, and shipped.
Conclusion: Material handling is an essential part of warehouse operations and involves three main activities: loading and unloading, material movement, and order filling. These activities must be carried out with care and attention to detail to ensure the efficient and effective management of goods and services.
By understanding the functions of each activity, warehouses can ensure that their material handling process is running smoothly and efficiently.
Efficiency in material handling is essential for optimizing logistics management.
Related Course: Logistics Certification

Efficient material handling is essential for maximizing the efficiency and productivity of any logistics operation. To optimize logistics management for material handling, several strategies can be employed.
First and foremost, creating a clear action plan is essential. This should include an assessment of the current material handling system, identifying the operation's objectives, and developing an action plan to achieve them. This plan should also include evaluating the materials and processes involved in the material handling operation and implementing appropriate measures to ensure their effectiveness.
Once a plan has been established, it is essential to establish an effective system for tracking and monitoring the progress of the material handling operations. This should include using appropriate technology, such as barcode scanners and RFID tags, to accurately track product movement and the implementation of automated systems to identify any discrepancies or problems.
In addition, it is essential to optimize the physical design of the material handling system. This involves selecting appropriate equipment, organizing storage and handling areas, and layout production lines. It is also essential to ensure that the material handling system is adequately maintained and serviced, as this can help to reduce downtime and improve efficiency.
Finally, it is essential to establish an effective communication system to ensure that all stakeholders within the logistics operation are kept informed of the progress of the material handling system. This should involve the use of appropriate software, such as an ERP system, to facilitate the sharing of information between different departments.
Employing these strategies makes it possible to optimize logistics management for material handling and ensure maximum efficiency and productivity.

The loading and unloading process of goods is a critical component of the supply chain, and its efficiency and cost-effectiveness are essential for the success of an organization. This article discusses ways to improve the loading and unloading process to reduce costs and increase efficiency.
First, it is essential to optimize the layout of the loading and unloading areas. For example, placing the unloading area next to the loading area can reduce the time and distance it takes to move the goods from one area to the other. Additionally, ample space for the workers should be provided to allow for the efficient movement of goods.
Second, automation can be used to improve the loading and unloading process. Automated systems can reduce the time it takes to load and unload goods and reduce the number of personnel required to complete the task. In addition, automation helps to reduce the risk of damage to the goods due to incorrect handling or mishandling.
Third, technology can also improve the loading and unloading process. For example, by using barcodes and radio frequency identification (RFID) tags, the goods can be quickly identified and tracked, allowing for more efficient loading and unloading. Additionally, mobile technology can provide real-time information about the loading and unloading process, enabling managers to make decisions quickly and accurately.
Finally, loading and unloading operations can be improved by optimizing the loading and unloading strategy. By understanding the characteristics of the goods, such as size, weight, and fragility, the best loading and unloading methods can be employed. Additionally, careful planning and scheduling of the loading and unloading process can help to reduce wait times and improve the efficiency of the process.
In conclusion, the loading and unloading process can be improved by optimizing the layout of the loading and unloading areas, using automation and technology, and optimizing the loading and unloading strategy. These improvements can help to reduce costs and increase efficiency.

Material movement and order filling are essential processes in the supply chain to ensure that goods are delivered accurately and on time to customers. Organizations should follow best practices when handling and filling orders to maximize efficiency, accuracy, and timeliness.
The first step in maintaining accurate and timely delivery is to ensure that material movement and order filling are appropriately planned. This includes having an effective inventory control system and tracking the status of orders as they move through the supply chain. Furthermore, organizations should have a system to monitor the accuracy of orders and to ensure that all orders are filled promptly and accurately.
Another best practice for material movement and order filling is ensuring proper packaging, labeling, and transportation methods. This will ensure that orders are shipped in the most efficient manner possible, reducing the risk of damage or loss in transit. Additionally, organizations should ensure that their order fulfillment system is optimized for fast and accurate order processing.
Finally, organizations should establish clear communication protocols between their suppliers and customers. This will ensure that orders are received accurately and that any changes to orders are communicated promptly. Additionally, organizations should establish clear delivery timelines and monitor the progress of orders to ensure they are delivered on time.
Organizations should follow best practices for material movement and order filling to ensure accuracy and timely delivery. This includes having effective inventory control systems, using the correct packaging and labeling, optimizing order fulfillment systems, and establishing clear communication protocols. Following these best practices will help organizations maximize efficiency, accuracy, and timeliness in their delivery of orders.

Understanding Material Handling Optimization
Optimizing material handling in integrated logistics management systems entails streamlining the movement, storage, and control of goods in an efficient and cost-effective manner. This process involves a holistic approach to managing resources, equipment, and information throughout the entire supply chain.
Incorporation of Advanced Technologies
Integrating advanced technologies, such as automation and robotics, into material handling systems significantly enhances the efficiency and accuracy of activities. Automated storage and retrieval systems (AS/RS), conveyor systems, and robotic palletizers are examples of equipment that improve warehouse performance, reduce labor costs, and minimize the potential for human errors.
Adoption of Lean Principles
Implementing lean principles in material handling processes helps eliminate waste, optimize space utilization, and streamline workflows. This approach involves continuous improvement, visual management, and standardized work practices to create a seamless and orderly flow of goods through the supply chain.
Utilization of Standardized Equipment and Processes
By utilizing standardized equipment and processes, organizations can facilitate interoperability and coordination among various departments and components of the logistics management system. This approach enables easier communication, faster decision-making, and improved traceability of goods, contributing to a more efficient and synchronized supply chain.
Application of Data Analytics
Data analytics plays a critical role in optimizing material handling activities. Analyzing historical and real-time data helps identify patterns and trends, enabling organizations to make informed decisions about inventory management, resource allocation, and process improvements. Data-driven insights also allow for the implementation of predictive maintenance, minimizing downtime and ensuring optimal equipment performance.
Effective Employee Training
Lastly, investing in comprehensive employee training programs ensures that staff members are well-equipped to operate advanced technology and adhere to standardized processes. Demonstrating a commitment to employees' professional development fosters an environment of teamwork, collaboration, and continuous improvement, ultimately contributing to the overall success of the integrated logistics management system.
In conclusion, optimizing material handling in an integrated logistics management system requires a comprehensive approach that incorporates advanced technologies, lean principles, standardized equipment, data analytics, and employee training. By addressing these key aspects, organizations can achieve greater efficiency, cost savings, and competitive advantage within the global supply chain landscape.

Material Selection and Ergonomics
A crucial factor in designing a material handling system is the proper selection of materials, ensuring they are durable, lightweight, and easy to maneuver. The chosen materials should be readily available and economically viable for large-scale deployment. Ergonomically designed equipment should be incorporated within the system for reduced worker fatigue and enhanced productivity.
Load Capacity and Adaptability
Factoring in the load capacity of the material handling equipment is essential, as underestimating or overestimating the capacity requirements can lead to inefficiencies and higher costs. The system must be flexible and adaptable to accommodate varying load types and sizes, enabling the smooth integration of new equipment or processes.
Technology Integration
Integrating advanced technologies such as automation, robotics, sensors, and data analytics into the material handling system can improve operational efficiency and reduce the logistical burden on employees. Additionally, incorporating real-time tracking and inventory management systems allows for better visibility and control across the supply chain, aiding in decision-making and resource allocation.
Safety and Risk Mitigation
Ensuring the safety of employees operating within the material handling system is paramount. Consequently, designers must consider safety features, such as fall protection equipment, anti-collision systems, and worker training, to minimize potential hazards. Furthermore, the handling system should have contingency plans in place to mitigate the risk of unforeseen disruptions, like equipment breakdowns or other system malfunctions.
Environmental Impact
The material handling system's design should consider the environmental impact of both the equipment and transportation processes, seeking ways to minimize the carbon footprint of the entire operation. Implementing eco-friendly solutions such as energy-efficient equipment, reducing idling times, and optimizing material loads can greatly enhance the system's sustainability.
Proper Maintenance and Training
Lastly, the material handling system must include plans for regular maintenance and preventative measures to prolong equipment lifespan and minimize downtime due to malfunctions. A well-trained workforce capable of operating and maintaining the equipment ensures overall efficiency and cost-effectiveness in the logistical processes.
In conclusion, when designing a material handling system, considering factors such as material selection, load capacity, technology integration, safety, environmental impact, and maintenance ensures the enhancement of logistics management efficiency. A well-designed system can greatly improve productivity and minimize the risk of disruptions throughout the supply chain.

Role of 7 R's in Improving Material Handling Practices
Right Product
The first R highlights the importance of ensuring that the correct product is being transported to the customers. By focusing on delivering the right product, logistics management minimizes errors and returns, which leads to improved material handling practices as products are handled fewer times.
Right Quantity
Adequate quantity management is essential for reducing waste and minimizing the chances of stock-outs or overstocking. Accurate forecasting and inventory management help in determining the right quantity of materials to handle, store and transport – ultimately improving material handling practices.
Right Condition
Ensuring that products are in the right condition when they reach customers is critical for customer satisfaction and reducing returns. Proper packaging, careful handling during transportation, and suitable storage conditions contribute to maintaining product quality and enhancing material handling practices in logistics management.
Right Place
Efficient logistics management involves transporting materials to the right destinations with minimal handling. By implementing effective routing and distribution strategies, managers can improve material handling practices by reducing unnecessary movements, minimizing damages, and streamlining the supply chain process.
Right Time
Timely delivery is crucial in maintaining customer loyalty and preventing inventory stockpiles. Logistics managers streamline the transportation process and reduce lead times, resulting in efficient material handling practices as materials are quickly moved through the supply chain without being held up in warehouses or distribution centers.
Right Cost
Cost optimization is a primary goal of logistics management, and improving material handling practices can aid in achieving this. Reducing damages, minimizing transportation and handling times, and optimizing storage methods all contribute to reducing overall costs and maximizing the efficiency of logistic operations.
Right Customer
Lastly, delivering the right product to the right customer is essential in ensuring customer satisfaction and repeat business. By combining accurate order processing with effective transportation and handling processes, logistics managers can improve material handling practices to better meet customer demands and increase overall supply chain efficiency.

Material Optimization Techniques
To optimize material handling for minimal environmental impact and enhanced sustainability, various strategies can be implemented. Among them are material efficiency, waste reduction, and energy optimization.
Material Efficiency
In material efficiency, the primary goal is to use the minimum amount of materials in production without compromising quality. This approach reduces the demand for raw materials and decreases waste generation. One technique for achieving this is lean manufacturing, which aims to maximize value and minimize waste in production processes. Employing lightweight and durable materials or designing products for easy disassembly and reassembly also contributes to material efficiency.
Waste Reduction
Effective waste reduction entails diverting materials from landfills and incinerators, thus reducing greenhouse gas emissions and conserving resources. A crucial aspect of waste reduction is adopting a circular economy model that emphasizes recycling, reuse, and remanufacturing. For instance, businesses can implement remanufacturing processes to refurbish used products or components for reuse. Another method is reverse logistics, which involves identifying materials that can be returned, recycled or repurposed from the end of the supply chain back to their origin.
Energy Optimization
Energy optimization in material handling minimizes the environmental impact by reducing energy consumption and utilizing renewable energy sources. One approach is to use energy-efficient equipment and methods of transportation, such as electric and hybrid vehicles. Additionally, optimizing routes and consolidating shipments can reduce transportation distances and fuel consumption. Automated systems, such as conveyors and sortation equipment, can also decrease energy use by streamlining material movement.
In conclusion, strategic approaches including material efficiency, waste reduction, and energy optimization can significantly minimize the environmental impact of material handling processes and promote sustainability. Adopting these strategies entails a holistic approach to manufacturing, transportation, and waste management, ultimately contributing to a more sustainable and eco-friendly industry.

Role of Technology in Material Handling Processes
Efficiency Improvement
Technology plays a crucial role in enhancing material handling processes within logistics management by improving efficiency. Advanced machinery and automation, such as conveyor belts, forklifts, and robotic arms, enable the swift movement of goods, leading to reduced processing times and increased productivity.
Inventory Management Enhancement
Effective inventory management is essential in logistics, and technology offers various tools to achieve this objective. Barcode scanners, Radio Frequency Identification (RFID) tags, and warehouse management systems significantly reduce human error in tracking inventory items, ensuring accurate stock counts and minimizing losses caused by misplaced goods.
Reduced Labor Costs
Automated systems require minimal human intervention in material handling processes, which helps businesses save on labor costs. Robotics and autonomous guided vehicles (AGVs) can efficiently perform tasks related to picking and packing, handling heavy loads, and sorting, thus decreasing the need for manual labor and reducing the potential for workplace injuries.
Integration and Coordination
Technology facilitates seamless integration and coordination among different components of the logistics management process. Electronic Data Interchange (EDI) and Application Programming Interface (API) systems enable swift and accurate data transfer between organizations, leading to improved communication and collaboration among supply chain partners.
Data Analysis and Optimization
Logistics management operations produce vast amounts of data that can be harnessed through technology for optimization. Sophisticated analytics software and algorithms can analyze this data to identify patterns, trends, and inefficiencies. This information allows managers to make better-informed decisions and implement improvements, leading to enhanced material handling processes and optimized overall supply chain performance.
Environmentally Sustainable Practices
Lastly, technology also contributes to promoting environmentally sustainable logistics management practices by enabling eco-friendly material handling processes. Energy-efficient equipment, such as electric forklifts, reduces greenhouse gas emissions, and waste-minimization technologies, like recycling systems and biodegradable packaging, contribute to a more sustainable and ethical material handling process.
In conclusion, technology plays a fundamental and increasingly critical role in enhancing material handling processes within logistics management. Through operational improvements in efficiency, inventory management, labor costs reduction, integration, optimization, coordination, and environmentally sustainable practices, technology offers businesses the opportunity to streamline their logistics operations, ensuring a competitive edge in the global market.

Interdepartmental Collaboration
Effective communication between different departments and stakeholders plays a crucial role in improving material handling and overall logistics optimization. By facilitating a collaborative environment, various departments can work together to streamline the flow of information, leading to faster and more efficient decision-making processes.
Data Sharing and Analysis
When departments and stakeholders openly share data related to material handling, they can provide valuable insights, identify inefficiencies, and develop optimization strategies. Through transparent communication, organizations can utilize their collective knowledge and resources to improve both the speed and accuracy of material flow.
Resource Allocation and Prioritization
Effective communication enables departments to better understand the requirements and priorities of different stakeholders. This insight helps organizations allocate resources effectively and prioritize tasks to maximize productivity. By sharing information and aligning goals, departments can create a more cohesive and efficient approach to logistics optimization.
Problem Solving and Continuous Improvement
Interdepartmental communication fosters a culture of problem-solving and continuous improvement. By addressing and resolving material handling challenges collectively, organizations can drive innovation, improve processes, adopt new technologies, and improve overall logistic efficiency. Moreover, effective communication can lead to better employee engagement and collaboration, creating a more positive work environment.
Risk Management and Compliance
When different departments communicate openly and consistently, they are better equipped to manage risks and ensure compliance with industry regulations. By sharing information on potential hazards, organizations can develop strategies to mitigate risks, minimize disruptions, and maintain high levels of safety and quality.
In conclusion, effective communication between departments and stakeholders is a key factor in improving material handling and overall logistics optimization. Through interdepartmental collaboration, data sharing and analysis, resource allocation, problem solving, and risk management, organizations can achieve better efficiency, productivity, and competitiveness in today's fast-paced global market.

Key Performance Indicators for Material Handling Systems
Efficiency and Productivity
A primary indicator of a material handling system's effectiveness is its efficiency and productivity. This can be measured by examining the amount of material moved per unit of time or by comparing the actual output with the desired output. Additionally, assessing the overall throughput rate allows logistics managers to ensure the system maximizes its capacity and delivers optimal performance.
Cost Reduction
Another vital performance indicator is the extent to which a material handling system reduces overall costs. This includes evaluating the operational and maintenance costs associated with the equipment, such as energy consumption, labor expenses, and repair costs. Furthermore, assessing the return on investment (ROI) of the equipment is crucial to determine the long-term financial benefits of implementing a particular material handling approach.
Inventory Accuracy
Inventory accuracy is a critical element in determining the effectiveness of material handling systems. By monitoring and maintaining accurate records of the inbound and outbound material flow, management can assess the system's ability to prevent errors such as overstocking or stockout situations. Consequently, this supports an organization's capability to meet customer demands, minimize waste, and improve overall operational efficiency.
Space Utilization
Effectively utilizing available space is crucial in optimizing material handling performance. Indicators such as the volume or density of material that can be stored and transported in a given area provide insight into how well the system maximizes resources and reduces costs. Additionally, an effective material handling system should be flexible and adaptable to accommodate variations in inventory or facility layout.
Safety and Ergonomics
The safety and ergonomic aspects of the material handling systems are critical indicators of their effectiveness. Systems that ensure the safety of workers and reduce the likelihood of accidents or injuries contribute to greater efficiency and productivity. Moreover, ergonomic equipment and procedures can minimize the physical strain on workers, resulting in lower absenteeism and higher morale.
In conclusion, the key performance indicators that measure the effectiveness of material handling systems in logistics management include efficiency and productivity, cost reduction, inventory accuracy, space utilization, and safety and ergonomics. By focusing on these aspects, organizations can optimize their material handling processes and maximize the overall performance of their supply chain operations.

Defining Lean Principles in Material Handling
The implementation of lean principles in material handling processes can optimize overall logistics performance by reducing waste, enhancing efficiency, and maximizing resources. Lean principles focus on providing value to customers while minimizing waste, thereby improving operational processes with a constant emphasis on meeting customer requirements.
Identifying Waste in Material Handling Processes
The first step in incorporating lean principles to material handling processes is to identify and eliminate waste, which could manifest in various forms such as material waste (excess inventory), time waste (waiting times), and labor waste (inefficient work practices). To uncover waste, management should analyze material flow, equipment usage, and worker activities to pinpoint any inefficiency and redundancy in existing processes.
Applying Lean Tools and Techniques
After identifying waste in material handling processes, organizations can utilize various lean tools and techniques to optimize their operations. Some common approaches include value stream mapping, 5S, kanban, and cellular manufacturing.
1. Value stream mapping: A visual tool that allows firms to map the process from raw materials to finished products, identifying non-value-adding activities and opportunities for improvement.
2. 5S: A workspace organization system, consisting of sorting, setting, shining, standardizing, and sustaining aimed at reducing clutter, streamlining work processes, and sustaining improvements.
3. Kanban: A visual inventory control technique, used to signal production when more materials or parts are required, eliminating excess inventory and minimizing shortages.
4. Cellular manufacturing: The organization of equipment and workspaces in close proximity to facilitate the smooth flow of materials without delays or interruptions.
Continuous Improvement in Material Handling
When lean principles have been applied to material handling processes, companies should continue pursuing opportunities for improvement through continuous evaluation and refinement. Tracking key performance indicators (KPIs) and regularly benchmarking against industry standards can help identify areas for future optimization.
To ensure that the benefits of lean principles are sustained, organizations must also develop a robust training program for employees, fostering a culture of continuous improvement and lean thinking. By investing in employee development, companies can empower their workforce to identify new waste-reduction opportunities, driving efficiency and improved performance in material handling processes.
Overall, the implementation of lean principles in material handling processes can lead to significant improvements in logistics performance. By adopting these principles, organizations can optimize their operations to provide increased value to customers, better use of resources, and reduced waste—factors that are critical to the long-term success and competitiveness of a business in today's dynamic market environment.

Assessing Risks and Disruptions
Organizations can build agility and resilience in their material handling systems by regularly assessing risks and potential disruptions. This involves identifying vulnerabilities in the supply chain, such as single-sourcing, transportation bottlenecks, and limited inventory. By evaluating these risks, organizations can make informed decisions and implement appropriate contingency plans.
Diversifying Supply Sources
To overcome logistics challenges, organizations should diversify their supply sources. By engaging with multiple suppliers, they can minimize the impact of supplier-related disruptions. This strategy reduces dependency on a single supplier and strengthens the organization's ability to absorb shocks in the supply chain.
Embracing Automation and Technology
Leveraging automation and advanced technology in material handling systems enhances agility and resilience. Organizations should invest in state-of-the-art equipment, like automated guided vehicles and robotics, to optimize warehouse operations. Additionally, implementing digital tools, such as warehouse management systems and artificial intelligence, allows for real-time data collection and analysis, resulting in better decision-making and improved efficiency.
Developing a Robust Inventory Management System
A robust inventory management system is essential for achieving agility and resilience. Organizations should employ practices such as cross-docking, just-in-time inventory, and demand forecasting to optimize storage and minimize disruptions. These strategies help ensure materials are readily available, reducing the likelihood of delays and keeping operations running smoothly.
Fostering Collaboration and Communication
Promoting collaboration and communication among stakeholders is crucial to overcoming logistics challenges. Open communication lines enable organizations to quickly identify and address issues arising in the supply chain. Regularly engaging with suppliers, consignees, and transport providers develops solid business relationships, ensuring a shared commitment to addressing disruptions and maintaining operations.
Continuous Training of Employees
Investing in employee training is essential for building agility and resilience in material handling systems. Providing ongoing training programs keeps staff updated on the necessary skills and knowledge to handle disruptions effectively. A well-trained workforce can adapt and respond to challenges quickly, ensuring continued operational success.
In conclusion, organizations can build agility and resilience in their material handling systems by diversifying supply sources, investing in automation and technology, developing robust inventory management systems, fostering collaboration and communication, and continuously training employees. These strategies enable organizations to overcome logistics challenges and disruptions, ensuring their supply chains remain efficient and effective.

Significance of Material Handling
Material handling plays a critical role within logistics management. It ensures the accurate movement and tracking of goods through the entire supply chain, from production to customer.
Effective Use of Resources
Material handling improves efficiency. It allows for the best use of warehouse space and equipment. Better organized facilities result in decreased operational costs and downtime.
Accurate Tracking and Control
The correct handling of materials enables precise record-keeping. This leads to effective control over inventory, reducing loss and wastage. It ensures the right product reaches the customer on time.
Enhancement of Safety Measures
Handling equipment properly increases safety. It decreases accidents and enhances worker satisfaction. This not only complies with regulations but also protects company reputation.
Cost Optimization
Proper handling techniques lower operational costs. Reduced errors and damage translate into savings. An efficient process paves the way towards competitive pricing.
Boosting Productivity
Efficient material handling increases productivity. It lessens handling time and speeds up delivery. Quicker processes enable companies to meet market demands swiftly.
In summary, the importance of material handling in logistics management cannot be overstated. It optimizes resources, provides control, enhances safety, reduces costs, and improves productivity. Proper material handling is a cornerstone of successful logistics management, contributing to overall business growth.

Optimization of Inventory
The first step towards improving the material handling process involves optimizing inventory. An excessive or poorly organized inventory results in inefficiencies. By implementing inventory management systems like Just-In-Time inventory or FIFO (First-In, First-Out), we can improve traceability and reduce surplus.
Automation Adoption
The adoption of automation in the material handling process can also significantly enhance operations. Automated machines, advanced robotics, and conveyor systems can manage repetitive tasks, reduce human error and streamline processes. In this way, companies can enhance productivity, increase speed, and save time.
Training and Staff Development
A significant way to improve the material handling process is by focusing on training and staff development. Knowledge in material handling techniques, equipment operation, and relevant safety protocols is crucial. Empowering the staff with the necessary skills can result in fewer accidents, less equipment damage and improved workflow efficiency.
Enhanced Storage Solutions
Storage improvements can also make a huge impact. Optimal use of space, suitable storage systems, and clear marking and labeling can result in easy retrieval, lesser time waste, and improved efficiency.
Implementation of Technology
Implementation of advanced technology such as Workplace Management Systems (WMS) or Radio Frequency Identification (RFID) can smooth the material handling process. Technology can provide real-time data, resulting in improved decision-making, reduced costs, and better customer service.
Regular maintenance and inspection
Regular maintenance and inspection is integral for improving material handling processes. Predictive maintenance can identify potential issues before they lead to equipment breakdown, maintain high productivity levels, and prolong equipment life.
Overall, improvements in material handling processes require strategic planning and utilization of technology. By doing so, companies can optimize their operations and enhance efficiency, leading to substantial cost and time savings.

Operational Efficiency in Logistics
Optimizing logistics operations begins with understanding the existing processes. Analyze current activities, identify pressure points, and study trends. This helps in gaining insight into operational inefficiencies and devising strategies for improvement.
Lean Principles Application
Applying lean principles, which emphasize waste reduction and value enhancement, is vital. Target redundant procedures that are complex, outdated, or time-consuming. By limiting waste, resources are used efficiently, which inevitably boosts productivity.
Implementing Technology
Modernize operations by implementing technology. Use logistics management software for tracking and optimization. Data analytics assists in making informed decisions about the supply chain. Real-time updates prevent delays and improve client satisfaction.
Training and Retention
Optimization also relies on staff training and retention. Teams should be proficient, adaptable, and knowledgeable about logistics operations. Training initiatives enhance staff skills, leading to improved efficiency and reduced errors.
Supply Chain Visibility
Another strategy is increasing supply chain visibility. A transparent operation aids all stakeholders. Everyone involved understands their roles, reducing miscommunications and clarifying expectations. This also aids in tracking deliveries and detecting anomalies swiftly.
Inventory Management
Lastly, effective inventory management is important. Overstocking or understocking both lead to inefficiencies. Advanced systems like Just-In-Time (JIT) inventory can help in managing goods efficiently.
Optimizing logistics operations needs a comprehensive strategy comprising of lean principles, technology implementation, employee training, supply-chain visibility, and efficient inventory management. By adopting these methods, logistics operations can be streamlined for maximum efficiency and customer satisfaction.

The Role of Ergonomics
Ergonomics plays a critical role in material handling. It primarily focuses on designing machinery that suits human capabilities. Therefore, it fosters an effective logistics management system.
Promotion of Worker Health
Primarily, ergonomics promotes the health and safety of workers. It helps to minimize injuries and discomfort. Lesser injuries lead to reduced absenteeism or turnover. As a result, there is an increase in worker productivity.
Facilitating Streamlined Operations
Ergonomics helps streamline operations. Effective ergonomic designs reduce the human effort needed for material handling. They reduce labor, time, and effort needed. Hence, companies can deliver products more swiftly and efficiently.
Benefit to the Company's Financial Performance
Beyond productivity, effective ergonomics plays a part in a company's financial performance. Improved worker health means less compensation or healthcare costs. Streamlined operations translates into increased output, potentially boosting profits.
Conclusion
In conclusion, effective ergonomics is integral for enhanced efficiency in logistics management. It can improve worker health, streamline operations, and even boost profits. Businesses should embrace ergonomic practices in their material handling for overall efficiency.

Optimization of Inventory Management
Proper inventory management is vital to the enhancement of material handling in logistic operations. It plays a pivotal role in streamlining workflow, reducing costs, and ensuring efficiency.
Realization of Efficient Workflow
An optimized inventory management system leads to an efficient workflow. Companies can monitor product availability and prevent stockouts or surplus inventories. This knowledge enables them to plan better and allocate resources effectively, leading to smooth operational processes.
Component of Cost Reduction
Cost reduction is another contribution to improve logistics operations. By optimizing inventory levels, companies can avoid unnecessary expenses associated to overstocking or understocking. These avoided costs can then be directed to improve other elements of logistics operations, therefore enhancing the overall efficiency.
Elimination of Wastage
Effective inventory management helps eliminate wastage. Knowing the exact quantity of goods in stock prevents the risk of products being lost, expired, or damaged. The absence of such wastage makes processes within the warehouse smoother and more efficient.
Enhancement of Customer Satisfaction
Finally, enhanced customer satisfaction is a critical advantage of proper inventory management. Ensuring that product availability aligns with customer demand is the essence of customer satisfaction. When customers receive their orders on time, it boosts their confidence in the company's logistics operations.
In conclusion, proper inventory management improves the material handling process within logistics operations by ensuring efficient workflow, cost reduction, elimination of wastage, and enhanced customer satisfaction. The essence of all these benefits underscores the need for companies to invest in optimized inventory management systems.

Efficient Layout and Design
An efficient facility layout and design can significantly enhance the material handling process in various ways. Logically arranged warehouses promote coherent flow of resources, minimizing wastage and unnecessary handling. By grouping similar items together, businesses streamline product retrieval and improve the overall logistics management.
Improved Equipment Utilization
Good layout and design also maximize equipment utilization. For instance, a well-planned traffic pattern ensures forklifts and other machinery perform tasks effectively without colliding. Likewise, suitable aisle widths allow efficient, safe machinery operation and swift material movement.
Time-Saving Aspects
Time-saving attributes also arise from well-thought-out facility layouts. Efficient inventory location can substantially minimize the total time spent in retrieving items. This leads to quick order fulfillment and assists in managing high volumes during peak times.
Enhancing Safety Measures
Safety enhancement is another crucial benefit. An adequate layout minimizes chances of stock damage and employee accidents. This preventive approach improves worker morale and decreases potential loss from damaged goods, thus contributing to better logistics management.
Increased Storage Capacity
Lastly, facility layout and design optimizations can increase storage capacity. By arranging items optimally, utilizing vertical space, and avoiding wasted floor space, businesses can store more products in the same square footage, enhancing both material handling and logistics management.
Overall, facility layout and design indisputably play a decisive role in improving the material handling process, making them essential elements for successful logistics management.

Material Handling in Logistic Management
Material handling is a critical facet of logistics management. It involves the movement, control, storage, and protection of products throughout the manufacturing, distribution, consumption and disposal process.
Functions and Importance
Its main function is to ensure that the right materials are in the right place at the right time. This optimizes efficiency and productivity. It also ensures safety of the products and those handling them. Alongside, it enhances customer satisfaction by delivering undamaged goods on time.
Types of Material Handling
There are four types of material handling equipment: storage, engineered systems, industrial trucks, and bulk material handling equipment. Each type serves different purposes but collectively they contribute to a smooth logistical operation.
Techniques Used
Specific techniques in material handling include barcoding, Radio-frequency identification (RFID), automated guided vehicles (AGVs), robotic delivery systems and contemporary software systems. They enable precise tracking and efficient management of goods in transit.
Role in Logistic Management
Logistics management integrates all aspects of the supply chain, beginning from procurement to customer delivery. Material handling plays a pivotal role here by ensuring a smooth, uninterrupted flow of materials, making it indispensable to logistics.
In conclusion, material handling in logistics management plays a significant role in maximizing efficiency, productivity, and customer satisfaction while minimizing costs and potential damages.

Integrating Automation and Robotics in Material Handling
The incorporation of automation and robotics in material handling processes can enhance efficiency and minimize human errors in logistics management. Automated material handling systems provide superior precision, greater speed, and higher productivity. By replacing traditional manual operations with advanced technology, companies can significantly reduce human errors associated with tasks such as loading, sorting, and packaging.
Automation for Increased Efficiency
Efficiency in logistic processes increases substantially with automation integration. For example, Automated Storage and Retrieval Systems (AS/RS) can expedite warehouse operations by ensuring fast and precise storage and retrieval of goods. Autonomous mobile robots can efficiently handle large volumes of material, thereby increasing throughput and eliminating bottlenecks.
Reducing Human Errors with Robotics
The application of robotics, on the other hand, can significantly lower human errors that could lead to process disruptions or product damage. Robots offer precise, consistent execution of tasks, minimizing errors due to human fatigue or distraction. These robotic systems can also perform complex tasks with a high degree of accuracy, contributing to high-quality outcomes.
In conclusion, integrating automation and robotics in material handling processes can provide substantial benefits for logistics management. By augmenting human labor with robots and automating operations, companies can achieve better operational efficiency, reduced human errors, and optimal resource utilization, paving the way for an enhanced and more efficient logistics landscape.

Material Handling Safety
Material handling systems necessitate several safety considerations to ensure efficiency within logistics operations. Operators must receive adequate training in handling equipment. This helps to reduce the incidences of accidents.
Proper Equipment Utilization
Workers should not only understand how to use equipment, but they should also be aware of the load limits. The work environment must ensure that equipment like forklifts and pallet jacks are well-maintained. Regular inspections help to identify potential problems before they escalate.
Implemented Safety Protocols
Establishing clear safety protocols is necessary. Adequate signage to denote load capacities, no-entry zones, and safety wear zones should be strategically visible. Procedures for incident reporting are crucial to tackle issues efficiently and quickly.
Personal Protective Equipment
Utilization of personal protective equipment (PPE) can prevent injury. Typically, this includes protective footwear, eyewear, and gloves. Companies should ensure workers have access to the necessary PPE and are trained in its correct use.
Consider Ergonomic Factors
Inclusion of ergonomic factors in system design can assist in minimizing risk. This can include height-adjustable workstations or reducing the demand for heavy manual lifting. Ergonomic designs contribute to employee comfort, productivity, and safety.
Risk Assessment
Regular comprehensive risk assessments should be conducted to identify hazards. This aids in the prevention of accidents and injuries by correcting potential safety risks. Having an emergency response plan in place is equally important.
Consideration for Health and Hygiene
Good health and hygiene practices help maintain the wellbeing of employees. This includes managing noise levels, ventilation, and temperature. Hygiene protocols, particularly in the current COVID-19 pandemic, provide an additional safety layer in logistics operations.
In summary, the safety considerations for material handling systems extend to adequate training, using equipment properly, enforcing safety protocols, use of PPE, ergonomic considerations, regular risk assessment, and health and hygiene practices. These offer a robust safety framework for logistics operations.

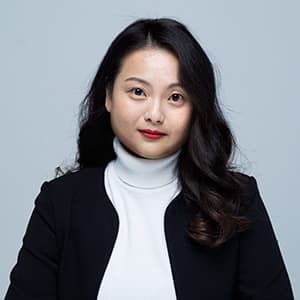
Yu Payne is an American professional who believes in personal growth. After studying The Art & Science of Transformational from Erickson College, she continuously seeks out new trainings to improve herself. She has been producing content for the IIENSTITU Blog since 2021. Her work has been featured on various platforms, including but not limited to: ThriveGlobal, TinyBuddha, and Addicted2Success. Yu aspires to help others reach their full potential and live their best lives.