Logistics Management Job Interview: Key Questions to Prepare For

Question Category | Sample Question | Intent of Question |
---|---|---|
Basic & Experience-Based | How do you define logistics management? | To assess the candidate's understanding of the role and its responsibilities. |
Basic & Experience-Based | Can you describe a challenging logistics project you managed in the past and how you handled it? | To gauge real-world experience and problem-solving capabilities. |
Operational & Scenario-Based | How do you handle a situation where a shipment is delayed, and a client is getting impatient? | To evaluate ability to manage crises, communicate effectively and handle customer relationship. |
Operational & Scenario-Based | Describe a time when you had to optimize a supply chain to reduce costs without compromising on delivery time or quality. | To test strategic problem-solving and cost efficiency skills. |
Technical & Analytical | Describe a time when you used analytics or data to improve logistics operations. | To evaluate proficiency in data-driven decision making and optimization. |
Interpersonal & Soft Skills | How do you handle disagreements or conflicts with team members or other departments? | To test candidate's teamwork and conflict resolution skills. |
Interpersonal & Soft Skills | How do you communicate bad news, like a delay or an error, to stakeholders or clients? | To assess the candidate's transparency, tact, and problem-solving skills in difficult situations. |
Forward-Thinking & Strategy | How do you see the future of logistics and supply chain management evolving in the next 5-10 years? | To understand the candidate's foresight and awareness of industry trends. |
Technical & Analytical | What KPIs (Key Performance Indicators) do you consider most important in logistics management? | To understand the candidate's knowledge of key metrics in logistics management. |
Operational & Scenario-Based | If there's a strike at a major port, how would you adjust logistics plans to mitigate impacts? | To gauge candidate's adaptability and crisis management skills. |
Logistics management is essential to global trade, ensuring products get from point A to point B efficiently, on time, and in the best condition. Whether you're interviewing for a role in logistics or hiring for one, it's crucial to understand what skills, experience, and insights are necessary for success. This article dives deep into the key questions that can be asked during a logistics management job interview, ensuring both interviewees and interviewers are well-prepared.
Related Course: Logistics Certificate Programs
Basic & Experience-Based Questions
1 - How do you define logistics management?
Logistics management involves planning, implementing, and controlling the efficient flow and storage of goods, services, and information from their origin to their final consumption. It encompasses all supply chain processes, ensuring timely delivery, optimal storage, and cost-efficiency.
Interview Question: Define Logistics Management?
2 - Can you describe a challenging logistics project you managed in the past and how you handled it?
This question gauges real-world experience. Interviewees might detail a project where they navigated customs regulations, coordinated with multiple suppliers, or addressed sudden disruptions.
Interview Question: Tell a Challenging Logistics Project?
3 - What logistics software or management systems have you worked with? Which do you prefer and why?
Different software caters to various logistical needs. An ideal answer might demonstrate proficiency with several systems and provide valid reasons for preferences, emphasizing efficiency, user-friendliness, or accurate reporting.
Interview Question: Used Which Logistics Software?
4 - How do you stay updated with the latest trends in logistics and supply chain management?
Continuous learning is vital. Candidates might mention following industry news, attending seminars, or participating in relevant courses and workshops.
Interview Question: How You Track Logistics Trends?
Operational & Scenario-Based Questions
5 - How do you handle a situation where a shipment is delayed, and a client is getting impatient
Handling delays requires tact and communication. The ideal response would stress proactive communication with the client, transparency, and finding swift solutions.
Interview Question: Handle Delayed Shipment
6 - Describe a time when you had to optimize a supply chain to reduce costs without compromising on delivery time or quality.
This explores strategic problem-solving. Candidates might discuss renegotiating supplier contracts, optimizing route planning, or implementing just-in-time delivery systems.
Interview Question: Optimized a Supply Chain Story
7 - How do you prioritize tasks when you have multiple shipments that need attention?
Logistics often requires juggling many responsibilities. Responses should highlight organizational skills, perhaps mentioning tools or frameworks used for prioritization.
Interview Question: Prioritize Multiple Shipments
8 - If there's a strike at a major port, how would you adjust logistics plans to mitigate impacts?
Such curveballs test adaptability. Candidates could discuss diversifying shipment routes, pre-emptively moving goods, or working with alternative transport modes.
Interview Question: Strike at a Port. Your Plan?
Technical & Analytical Questions
9 - Describe a time when you used analytics or data to improve logistics operations.
Data-driven decision-making is pivotal. Look for answers that delve into using metrics to streamline operations, predict disruptions, or improve supplier relations.
Interview Question: Used Analytics in Logistics
10 - How do you measure the success or effectiveness of a logistics process?
Success in logistics can be multifaceted. Answers might revolve around metrics like on-time delivery rates, cost-efficiency, or customer satisfaction scores.
Interview Question: Metrics for Logistics Success
11 - What KPIs (Key Performance Indicators) do you consider most important in logistics management?
Different roles might prioritize different KPIs. Common ones include transportation costs, warehouse efficiency, or inventory turnover.
Interview Question: Top KPIs in Logistics?
12 - Explain the importance of route optimization in logistics.
Route optimization can lead to fuel savings, quicker deliveries, and reduced environmental impact. Candidates should discuss its benefits and perhaps the tools they've utilized for it.
Interview Question: Importance of Route Optimization
Interpersonal & Soft Skills Questions
13 - How do you handle disagreements or conflicts with team members or other departments?
Logistics involves many stakeholders. Answers should stress collaboration, active listening, and compromise.
Interview Question: Handle Team Conflicts
14 - Describe a time when you had to convince upper management to adopt a new logistics strategy.
This gauges persuasion skills. Candidates might discuss presenting data-driven cases, benefits, and potential ROI.
Interview Question: Can You Adapt to Logistics Changes?
15 - How do you communicate bad news, like a delay or an error, to stakeholders or clients
Transparency and tact are essential. Ideal responses prioritize timely communication, taking responsibility, and offering solutions.
16 - How do you ensure that all team members are aligned and working cohesively in the logistics process?
Team alignment ensures smoother operations. Answers might involve regular check-ins, clear goal-setting, or team-building exercises.
Interview Question: Align Team in Logistics
Forward-Thinking & Strategy Questions
17 - How do you see the future of logistics and supply chain management evolving in the next 5-10 years?
This question assesses industry foresight. Candidates might discuss automation, AI integration, sustainability trends, or geopolitical shifts.
Interview Question: Logistics Future in 5-10 Years
18 - What are the biggest challenges facing logistics today, and how do you anticipate overcoming them?
From global disruptions to sustainability demands, logistics faces many challenges. Good responses will offer a blend of proactive and reactive strategies.
Interview Question: Biggest Logistics Challenges
19 - How do concepts like sustainability or environmental considerations factor into your logistics planning and decisions?
With increasing emphasis on sustainability, logistics professionals should prioritize eco-friendly practices, from green transportation to reduced packaging.
20 - What role do you see emerging technologies, like AI, drones, or blockchain, playing in the future of logistics?
Technological advancements are reshaping logistics. Candidates might discuss real-time data analysis, drone deliveries in remote areas, or blockchain's role in transparent supply chains.
Interview Question: AI, Drones in Logistics Future
Culture & Company Fit Questions
21 - How do you adapt to rapidly changing circumstances or uncertainties in a logistics operation?
Adaptability is key. Look for answers that emphasize flexibility, continuous learning, and quick decision-making.
22 - What do you value most in a company's logistics culture?
Company culture fit can drive employee success. Responses could focus on collaboration, innovation, sustainability, or transparency.
Interview Question: Value in Logistics Culture?
23 - Can you describe an instance where you had to adapt to a significant change or new technology in your previous logistics role?
Change is inevitable. Ideal answers would discuss the challenges faced, the learning curve, and the eventual benefits of adaptation.
24 - How do you manage stress or pressure, especially during peak logistics operations?
Stress management is vital in high-pressure logistics roles. Candidates might discuss time management, seeking support, or employing relaxation techniques.
Related Course: Time Management Course Online
Related Course: Online Course Stress Management
Interview Question: How do you manage logistics stress?
Logistics management is a multifaceted discipline requiring a blend of hard and soft skills. These interview questions offer a comprehensive view into a candidate's experience, adaptability, and forward-thinking approach.
Whether you're gearing up for an interview or seeking the right candidate, understanding these questions can set you on the path to success in the dynamic world of logistics.

Optimizing supply chain processes and reducing costs require a multifaceted approach that involves various strategies and techniques. Firstly, it is essential to conduct a thorough analysis of the existing supply chain processes to identify areas of inefficiency and potential cost savings. This analysis should include an examination of the entire supply chain, from sourcing raw materials to delivering finished products to customers.
Streamlining Processes
One effective strategy for optimizing supply chain processes is to streamline operations by eliminating redundant or non-value-added activities. This can be achieved through process mapping, which involves creating a visual representation of the supply chain to identify bottlenecks and areas for improvement. By simplifying processes and reducing waste, companies can improve efficiency and reduce costs.
Leveraging Technology
Another important strategy is to leverage technology to automate and optimize supply chain processes. This can include implementing enterprise resource planning (ERP) systems, transportation management systems (TMS), and warehouse management systems (WMS). These technologies can help companies to improve visibility, reduce errors, and optimize inventory levels, leading to significant cost savings.
Collaborative Partnerships
Building collaborative partnerships with suppliers and logistics providers is also crucial for optimizing supply chain processes and reducing costs. By working closely with partners, companies can improve communication, reduce lead times, and negotiate better prices. This can be achieved through initiatives such as vendor-managed inventory (VMI) programs, where suppliers take responsibility for managing inventory levels at the customer's site.
Continuous Improvement
Finally, it is essential to adopt a continuous improvement mindset when optimizing supply chain processes and reducing costs. This involves regularly monitoring and measuring supply chain performance, setting targets for improvement, and implementing ongoing initiatives to drive efficiency and cost savings. By continuously seeking out opportunities for improvement, companies can stay ahead of the competition and maintain a competitive edge in the marketplace.

Effective communication and conflict resolution are essential for maintaining positive relationships with suppliers. When conflicts or communication breakdowns occur, it is crucial to address the issues promptly and professionally. The first step is to identify the root cause of the problem and gather all relevant information. This may involve reviewing contracts, order details, or previous correspondence to gain a clear understanding of the situation.
Open and Honest Communication
Once the issue is identified, initiate an open and honest dialogue with the supplier. Arrange a meeting or a call to discuss the problem and express your concerns clearly and calmly. Listen actively to their perspective and try to understand their position. Avoid making accusations or placing blame; instead, focus on finding a mutually beneficial solution.
Collaborative Problem Solving
Approach the conflict with a collaborative mindset, aiming to find a win-win solution. Brainstorm potential options together and be open to compromises. Consider the long-term relationship with the supplier and prioritize finding a resolution that works for both parties. If necessary, involve a mediator or a neutral third party to facilitate the discussion and help reach an agreement.
Implementing Solutions and Follow-up
Once a solution is agreed upon, clearly outline the action steps and responsibilities for each party. Set realistic timelines and milestones to ensure progress is made. Regularly follow up with the supplier to monitor the implementation of the solution and address any new concerns that may arise. Maintain open lines of communication and provide updates on the progress.
Strengthening the Relationship
After resolving the conflict, take proactive steps to strengthen the relationship with the supplier. Show appreciation for their efforts in finding a resolution and acknowledge their value as a partner. Regularly engage in open and transparent communication, sharing information, and seeking feedback. Invest time in building trust and fostering a long-term, mutually beneficial partnership.
Continuous Improvement
Use conflicts or communication breakdowns as opportunities for learning and improvement. Analyze the situation to identify any systemic issues or areas where processes can be enhanced. Implement necessary changes to prevent similar problems from recurring in the future. Continuously monitor and evaluate the effectiveness of communication channels and conflict resolution strategies to ensure they remain effective.
By addressing conflicts promptly, communicating openly, and working collaboratively with suppliers, organizations can maintain positive relationships and minimize disruptions to their supply chain. A proactive approach to conflict resolution and relationship management leads to stronger partnerships, improved efficiency, and long-term success.

Implementing a new logistics system or technology can be a complex and challenging process, but it can also lead to significant improvements in efficiency and productivity. One example of a successful implementation occurred when I worked as a logistics manager for a medium-sized manufacturing company. The company had been using an outdated inventory management system that was prone to errors and inefficiencies, leading to delays in production and shipping.
Identifying the Problem
The first step in the implementation process was to identify the specific problems with the current system. This involved conducting a thorough analysis of the existing processes and gathering feedback from employees at all levels of the organization. We found that the main issues were related to inaccurate inventory tracking, poor communication between departments, and a lack of automation.
Researching Solutions
Once we had a clear understanding of the problems, we began researching potential solutions. We looked at various inventory management systems and technologies, evaluating them based on their features, costs, and compatibility with our existing infrastructure. After careful consideration, we decided to implement a cloud-based inventory management system that offered real-time tracking, automated ordering, and seamless integration with our other systems.
Implementing the New System
The implementation process involved several challenges, including data migration, employee training, and system configuration. We had to ensure that all of our existing inventory data was accurately transferred to the new system, which required close collaboration with our IT department. We also had to provide comprehensive training to our employees to ensure that they were comfortable using the new system and understood its features and benefits.
Configuring the System
Another challenge was configuring the system to meet our specific needs and requirements. This involved working closely with the software vendor to customize the system's settings and workflows to align with our business processes. We also had to integrate the system with our other software applications, such as our ERP and shipping management systems, to ensure seamless data flow and communication.
Measuring Success
Despite these challenges, the implementation was ultimately successful. We were able to reduce inventory discrepancies by 90%, improve order accuracy by 95%, and reduce shipping delays by 75%. We also saw significant improvements in employee productivity and satisfaction, as the new system eliminated many of the manual and time-consuming tasks that had previously been required.
Continuous Improvement
One of the keys to our success was our commitment to continuous improvement. We regularly solicited feedback from employees and monitored system performance to identify areas for optimization. We also invested in ongoing training and support to ensure that our employees were able to use the system effectively and efficiently.
Conclusion
Implementing a new logistics system or technology can be a daunting task, but with careful planning, communication, and execution, it can lead to significant benefits for the organization. By identifying the specific problems with the current system, researching potential solutions, and providing comprehensive training and support, we were able to successfully implement a new inventory management system that improved our efficiency, accuracy, and productivity.

Logistics interviews often focus on assessing a candidate's knowledge, problem-solving skills, and ability to handle various situations. Common questions revolve around the individual's experience, understanding of logistics processes, and approach to challenges. Interviewers may ask about the candidate's familiarity with supply chain management, inventory control, and transportation methods. They might also inquire about the applicant's ability to optimize routes, reduce costs, and improve efficiency. Appropriate answers should demonstrate a solid understanding of logistics principles, showcase relevant experience, and highlight the candidate's problem-solving capabilities. Responses should be concise, well-structured, and supported by specific examples from previous roles or education. Candidates should also emphasize their ability to work collaboratively, adapt to changing circumstances, and continuously improve processes.
Experience and Background
Interviewers often begin by asking about the candidate's experience and background in logistics. They may inquire about previous roles, responsibilities, and accomplishments. Candidates should provide a brief overview of their work history, highlighting relevant positions and key achievements. It's essential to demonstrate a progression of responsibilities and a track record of success in logistics-related roles.
Example questions:
Can you tell me about your experience in logistics and supply chain management?
What specific roles have you held, and what were your primary responsibilities?
Can you describe a successful project you led or contributed to in a previous logistics position?
Knowledge of Logistics Processes
Interviewers will assess the candidate's understanding of various logistics processes, such as inventory management, warehousing, and transportation. They may ask about specific techniques, technologies, or methodologies used in the field. Candidates should demonstrate a solid grasp of logistics concepts and be able to explain how they have applied this knowledge in practice.
Example questions:
Can you explain the key components of an effective inventory management system?
How do you ensure efficient warehousing operations and optimize space utilization?
What strategies have you used to streamline transportation processes and reduce costs?
Problem-Solving and Decision-Making
Logistics professionals often face complex challenges and must make informed decisions to optimize operations. Interviewers may present hypothetical scenarios or ask about real-life situations the candidate has encountered. Candidates should showcase their ability to analyze problems, evaluate options, and implement effective solutions. They should also demonstrate adaptability and resilience when facing unexpected challenges.
Example questions:
How would you handle a situation where a critical shipment is delayed due to unforeseen circumstances?
Can you describe a time when you had to make a difficult decision in a logistics context?
How do you approach problem-solving when faced with limited resources or tight deadlines?
Continuous Improvement and Innovation
Logistics is a dynamic field that requires professionals to continuously improve processes and embrace innovation. Interviewers may ask about the candidate's approach to process optimization, technology adoption, and staying updated with industry trends. Candidates should demonstrate a proactive mindset, a willingness to learn, and a commitment to driving positive change within the organization.
Example questions:
How do you identify opportunities for process improvement in logistics operations?
Can you describe a time when you successfully implemented a new technology or innovative solution?
How do you stay informed about the latest trends and best practices in the logistics industry?
Collaboration and Communication
Logistics professionals often work closely with cross-functional teams and external partners. Interviewers may inquire about the candidate's ability to collaborate effectively, communicate clearly, and build strong relationships. Candidates should highlight their interpersonal skills, experience working in team environments, and ability to communicate complex information to various stakeholders.
Example questions:

Preparing for a logistics interview requires a comprehensive approach that covers various aspects of your professional profile and knowledge. First, research the company thoroughly to understand its mission, values, and recent developments in the industry. This information helps you align your answers with the company's goals and demonstrate your genuine interest in the position. Next, review the job description carefully and identify the key skills and qualifications required for the role. Assess your own experiences and accomplishments that match these requirements and prepare specific examples to illustrate your competencies during the interview.
Brush Up on Logistics Knowledge
To increase your chances of success, brush up on your knowledge of logistics concepts, terminology, and best practices. Review topics such as supply chain management, inventory control, transportation modes, and warehouse operations. Stay updated on the latest trends and technologies in the logistics industry, such as automation, data analytics, and sustainable practices. Demonstrating a solid understanding of these subjects showcases your expertise and commitment to professional growth.
Prepare for Common Interview Questions
Anticipate common interview questions and practice your responses beforehand. Some typical questions in a logistics interview may include:
How do you handle multiple priorities and tight deadlines?
Describe a time when you successfully optimized a logistics process.
How do you ensure effective communication with cross-functional teams?
Share an example of how you resolved a challenging logistics problem.
Craft concise and structured answers that highlight your problem-solving skills, attention to detail, and ability to work collaboratively. Use the STAR method (Situation, Task, Action, Result) to provide concrete examples that demonstrate your competencies.
Showcase Your Soft Skills
In addition to technical expertise, logistics roles often require strong soft skills. Emphasize your ability to communicate effectively, both verbally and in writing. Highlight your leadership potential, teamwork skills, and adaptability to change. Share examples of how you have successfully collaborated with colleagues, suppliers, or customers to achieve common goals. Demonstrating your interpersonal skills and emotional intelligence can set you apart from other candidates.
Prepare Questions for the Interviewer
Engage actively in the interview by preparing thoughtful questions for the interviewer. Inquire about the company's logistics strategies, challenges, and opportunities for growth. Show curiosity about the team dynamics and the expectations for the role. Asking relevant questions not only demonstrates your interest but also allows you to assess if the position aligns with your career goals.
Practice and Seek Feedback
Finally, practice your interview skills through mock interviews with friends, family, or mentors. Request feedback on your responses, body language, and overall presentation. Refine your answers based on their suggestions and continue practicing until you feel confident and well-prepared. Remember to dress professionally, arrive punctually, and bring copies of your resume and relevant documents.
By following these steps and showcasing your logistics expertise, soft skills, and enthusiasm, you can significantly increase your chances of success in a logistics interview. Remember to stay positive, articulate your value proposition clearly, and express your genuine interest in contributing to the company's success.

When preparing for a logistics interview, it's essential to understand the common expectations and how to differentiate yourself. Logistics interviews typically assess your knowledge of supply chain management, problem-solving skills, and ability to work under pressure. Interviewers may ask about your experience with inventory control, transportation management, and cost optimization. They may also present hypothetical scenarios to gauge your decision-making abilities and adaptability.
Research the Company
To stand out from other candidates, start by thoroughly researching the company you're interviewing with. Understand their business model, values, and recent developments in their logistics operations. Demonstrating a deep understanding of the company shows genuine interest and sets you apart.
Highlight Relevant Experience
During the interview, emphasize your relevant experience and skills. Share specific examples of how you've optimized logistics processes, reduced costs, or improved efficiency in previous roles. Use data and metrics to substantiate your achievements and showcase your impact.
Showcase Problem-Solving Skills
Logistics often involves complex challenges that require creative problem-solving. Prepare examples of how you've tackled logistics-related issues in the past. Explain your thought process and the steps you took to find effective solutions. Demonstrating strong problem-solving abilities is highly valued in logistics roles.
Emphasize Adaptability and Resilience
The logistics industry is dynamic and fast-paced, requiring professionals who can adapt to changing circumstances. Highlight instances where you've successfully navigated unexpected challenges or implemented contingency plans. Showcase your resilience and ability to remain calm under pressure.
Discuss Technology Proficiency
Technology plays a crucial role in modern logistics operations. Discuss your proficiency with relevant logistics software, such as transportation management systems (TMS), warehouse management systems (WMS), and inventory management tools. Highlight any experience you have with automation, data analytics, or emerging technologies in logistics.
Ask Thoughtful Questions
Prepare thoughtful questions to ask the interviewer about the company's logistics strategies, challenges, and growth plans. Show genuine curiosity and enthusiasm for the opportunity. Asking insightful questions demonstrates your engagement and critical thinking skills.
Conclusion
By understanding the expectations of a logistics interview and implementing these tips, you can increase your chances of standing out from other candidates. Remember to showcase your relevant experience, problem-solving abilities, adaptability, and technology proficiency. Thoroughly research the company, ask thoughtful questions, and demonstrate your passion for the logistics industry. With proper preparation and a confident approach, you can make a strong impression and increase your likelihood of success in your logistics interview.

A successful logistics strategy is crucial for businesses to optimize their supply chain and deliver products efficiently. The key components of a logistics strategy include transportation management, inventory management, warehousing, and information technology. By focusing on these areas, companies can streamline their operations, reduce costs, and improve customer satisfaction.
Transportation Management
Effective transportation management is essential for timely delivery of goods to customers. Companies should select the most appropriate transportation modes based on cost, speed, and reliability. They should also optimize routes, consolidate shipments, and collaborate with carriers to reduce transportation costs. Using technology like GPS tracking and real-time monitoring can help improve visibility and efficiency in transportation.
Inventory Management
Proper inventory management ensures that the right products are available when needed while minimizing holding costs. Companies should implement inventory control systems to track stock levels, monitor demand patterns, and automate replenishment processes. They should also use forecasting techniques to anticipate future demand and adjust inventory levels accordingly. Regular inventory audits and analysis can help identify slow-moving or obsolete items and optimize stock holdings.
Warehousing
Efficient warehousing is crucial for storing and handling inventory effectively. Companies should design their warehouses to maximize space utilization, minimize travel distances, and facilitate smooth product flow. They should also implement warehouse management systems to automate processes like receiving, putaway, picking, and shipping. Using technologies like barcode scanning and RFID can help improve accuracy and productivity in warehousing operations.
Information Technology
Information technology plays a vital role in integrating and optimizing various aspects of the logistics strategy. Companies should leverage technologies like enterprise resource planning (ERP) systems, transportation management systems (TMS), and warehouse management systems (WMS) to streamline processes and enhance visibility. They should also invest in data analytics and business intelligence tools to gain insights into supply chain performance and identify improvement opportunities.
Continuous Improvement
A successful logistics strategy requires continuous improvement and adaptation to changing market conditions. Companies should regularly review their logistics processes, identify bottlenecks, and implement improvements. They should also benchmark their performance against industry best practices and seek feedback from customers and partners. By fostering a culture of continuous improvement, companies can stay ahead of the competition and deliver superior logistics performance.
Collaboration and Partnerships
Collaboration and partnerships are essential for a successful logistics strategy. Companies should work closely with suppliers, carriers, and customers to align goals, share information, and optimize processes. They should also explore strategic partnerships and alliances to access specialized expertise, expand geographic reach, and improve service levels. By leveraging the strengths of partners, companies can create a more resilient and efficient logistics network.
In conclusion, a successful logistics strategy requires a holistic approach that encompasses transportation management, inventory management, warehousing, and information technology. By continuously improving processes, collaborating with partners, and leveraging technology, companies can optimize their logistics operations and gain a competitive edge in the market.

Technology can be leveraged to optimize supply chain management in several ways. Firstly, the use of artificial intelligence (AI) and machine learning (ML) can help predict demand accurately. AI and ML algorithms can analyze historical data, identify patterns, and forecast future demand. This enables companies to plan their production and inventory levels effectively, reducing waste and minimizing stockouts.
Real-time Visibility and Tracking
Another way technology can optimize supply chain management is through real-time visibility and tracking. Internet of Things (IoT) devices, such as sensors and GPS trackers, can monitor the movement of goods in real-time. This provides companies with valuable insights into the location and condition of their products. Real-time tracking helps identify potential delays, reroute shipments if necessary, and ensure timely delivery to customers.
Automation of Processes
Technology can also automate various processes in the supply chain, improving efficiency and reducing errors. Robotic process automation (RPA) can handle repetitive tasks, such as data entry and order processing. Automated warehouse management systems can optimize inventory storage and retrieval, reducing labor costs and increasing accuracy. Blockchain technology can automate and secure transactions, enhancing transparency and trust among supply chain partners.
Collaboration and Information Sharing
Technology facilitates collaboration and information sharing among supply chain stakeholders. Cloud-based platforms allow real-time data exchange and communication. Suppliers, manufacturers, distributors, and retailers can access shared information, enabling better coordination and decision-making. Collaborative planning, forecasting, and replenishment (CPFR) systems help align supply and demand, reducing inventory levels and improving customer service.
Predictive Maintenance and Asset Management
Technology enables predictive maintenance and asset management in the supply chain. IoT sensors can monitor the health and performance of equipment, such as trucks and machines. Predictive analytics can identify potential failures before they occur, allowing proactive maintenance and reducing downtime. This improves asset utilization, extends equipment lifespan, and minimizes disruptions in the supply chain.
Optimization through Data Analytics
Data analytics plays a crucial role in optimizing supply chain management. Big data analytics can process vast amounts of structured and unstructured data from various sources. This includes data from IoT devices, social media, and customer feedback. Analytics tools can identify trends, patterns, and anomalies, providing actionable insights for decision-making. Data-driven optimization helps improve demand forecasting, inventory management, and transportation planning.
In conclusion, technology offers numerous opportunities to optimize supply chain management. From AI and ML for demand forecasting to real-time visibility and tracking, automation, collaboration, predictive maintenance, and data analytics, technology enables companies to streamline operations, reduce costs, and enhance customer satisfaction. By leveraging these technologies, businesses can build resilient, agile, and efficient supply chains that adapt to the ever-changing market dynamics.

Reducing transportation costs in logistics is crucial for maintaining a competitive edge and increasing profitability. Implementing best practices can help optimize transportation processes and minimize expenses. One effective strategy is to consolidate shipments whenever possible, which reduces the number of trips and lowers fuel consumption. Utilizing technology, such as transportation management systems (TMS), can also streamline operations and provide valuable insights for cost-saving opportunities.
Optimize Route Planning
Efficient route planning is essential for minimizing transportation costs. By using advanced software and algorithms, companies can determine the most cost-effective routes, considering factors like distance, traffic, and delivery time windows. This optimization reduces fuel consumption, driver hours, and vehicle wear and tear. Additionally, regularly reviewing and adjusting routes based on changing conditions can further improve efficiency and reduce costs.
Collaborate with Suppliers and Customers
Collaborating with suppliers and customers can lead to significant cost savings in transportation. By working closely with suppliers, companies can coordinate shipments, consolidate orders, and optimize delivery schedules. This collaboration reduces the number of trips required and allows for better utilization of vehicle capacity. Similarly, engaging with customers to establish flexible delivery options and time windows can help reduce transportation costs by enabling more efficient route planning and reducing the need for expedited or special deliveries.
Embrace Intermodal Transportation
Intermodal transportation, which involves using multiple modes of transport (e.g., truck, rail, ship) for a single shipment, can be a cost-effective solution for long-distance deliveries. By leveraging the strengths of each mode, companies can optimize transportation costs while maintaining delivery speed and reliability. For example, using rail for long-haul distances and trucks for local deliveries can reduce overall transportation expenses.
Implement Fuel-Saving Strategies
Fuel is a significant expense in transportation, so implementing fuel-saving strategies is crucial for reducing costs. This can include regular vehicle maintenance to ensure optimal performance, training drivers in fuel-efficient driving techniques, and investing in fuel-efficient or alternative fuel vehicles. Additionally, using telematics systems to monitor vehicle performance and driver behavior can help identify areas for improvement and further reduce fuel consumption.
Outsource Transportation Services
Outsourcing transportation services to third-party logistics (3PL) providers can be a cost-effective solution for some companies. 3PLs often have extensive networks, advanced technology, and economies of scale that allow them to provide transportation services at lower costs than in-house operations. By partnering with a reliable 3PL, companies can focus on their core competencies while benefiting from the expertise and cost-saving strategies of the transportation provider.
Continuously Monitor and Analyze Performance
To effectively reduce transportation costs, it is essential to continuously monitor and analyze performance. By tracking key metrics such as on-time delivery, cost per shipment, and vehicle utilization, companies can identify areas for improvement and make data-driven decisions. Regular performance reviews and benchmarking against industry standards can also help identify best practices and opportunities for cost savings.
In conclusion, reducing transportation costs in logistics requires a multi-faceted approach that involves optimizing routes, collaborating with partners, embracing intermodal transportation, implementing fuel-saving strategies, considering outsourcing, and continuously monitoring performance. By adopting these best practices, companies can significantly reduce their transportation expenses and improve their overall competitiveness in the market.

Logistics is a crucial aspect of modern business, and a successful career in this field requires a diverse set of skills. Some of the most important skills for a successful career in logistics include strong analytical and problem-solving abilities, excellent communication and interpersonal skills, proficiency in technology and software systems, and a deep understanding of supply chain management principles.
Analytical and Problem-Solving Skills
Logistics professionals must possess strong analytical and problem-solving skills to effectively manage complex supply chain operations. They need to analyze data, identify potential issues, and develop innovative solutions to optimize processes and minimize disruptions. The ability to think critically and make quick, informed decisions is essential in this fast-paced industry.
Communication and Interpersonal Skills
Effective communication and interpersonal skills are crucial for logistics professionals. They must collaborate with various stakeholders, including suppliers, customers, and internal teams. Clear, concise communication helps ensure smooth operations and resolve conflicts. Building strong relationships and fostering trust among stakeholders is key to success in logistics.
Technology and Software Proficiency
Logistics heavily relies on technology and software systems to streamline processes and improve efficiency. Proficiency in logistics management software, enterprise resource planning (ERP) systems, and transportation management systems (TMS) is essential. Staying updated with the latest technological advancements and being able to adapt to new tools is crucial for career growth.
Supply Chain Management Knowledge
A deep understanding of supply chain management principles is fundamental for a successful career in logistics. This includes knowledge of inventory management, transportation, warehousing, and distribution. Familiarity with lean management techniques, such as Just-in-Time (JIT) and Six Sigma, can help optimize supply chain processes and reduce waste.
Continuous Learning and Adaptability
The logistics industry is constantly evolving, and professionals must be willing to learn and adapt to new challenges. Staying informed about industry trends, regulations, and best practices is essential. Participating in training programs, workshops, and conferences can help expand knowledge and stay competitive in the field.
Leadership and Project Management
As logistics professionals advance in their careers, leadership and project management skills become increasingly important. The ability to lead teams, delegate tasks, and manage complex projects is crucial for success in senior roles. Developing strong organizational and time management skills is essential to effectively oversee logistics operations.
Attention to Detail and Accuracy
Logistics involves managing large volumes of data and ensuring the accuracy of information. Attention to detail is critical to prevent errors that can lead to costly mistakes. Double-checking data, maintaining accurate records, and following standard operating procedures (SOPs) are essential habits for logistics professionals.
Customer Service Orientation
Logistics plays a vital role in customer satisfaction, and having a customer-centric approach is essential. Understanding customer needs, managing expectations, and providing timely and accurate information are crucial. Developing strong customer service skills can help build long-term relationships and enhance the company's reputation.
In conclusion, a successful career in logistics requires a combination of technical skills, soft skills, and industry knowledge. By continuously developing these skills and staying adaptable to change, logistics professionals can thrive in this dynamic and rewarding field.

Handling pressure and tight deadlines in a logistics role requires a combination of effective strategies and personal qualities. Time management is crucial in this fast-paced environment, where prioritizing tasks and managing resources efficiently can make a significant difference. Developing strong organizational skills, such as creating detailed schedules and utilizing project management tools, helps in staying on top of deadlines.
Effective communication is another key aspect of managing pressure in logistics. Maintaining clear and open lines of communication with team members, suppliers, and customers ensures that everyone is on the same page. This helps in identifying potential issues early on and finding solutions collaboratively. Active listening and being proactive in addressing concerns can prevent misunderstandings and delays.
Adaptability and Problem-Solving
In a logistics role, unexpected challenges and changes are common. Being adaptable and quick to respond to these situations is essential. Cultivating a problem-solving mindset, where you approach obstacles as opportunities for improvement, can help in managing pressure effectively. Continuously learning and staying updated with industry trends and best practices equips you with the knowledge to make informed decisions under tight deadlines.
Stress Management Techniques
Managing stress is vital in a high-pressure logistics environment. Incorporating stress management techniques into your daily routine can help in maintaining focus and productivity. Some effective methods include deep breathing exercises, mindfulness practices, and regular breaks to recharge. Engaging in physical activity and maintaining a healthy work-life balance also contribute to overall well-being and resilience.
Collaboration and Support
Handling pressure in logistics is not a solo endeavor. Fostering a collaborative and supportive team environment is crucial. Encouraging open communication, sharing knowledge, and offering assistance to colleagues when needed creates a sense of camaraderie. Recognizing and celebrating individual and team successes boosts morale and motivation, making it easier to tackle challenges together.
Continuous Improvement
Embracing a mindset of continuous improvement is essential in managing pressure and tight deadlines. Regularly reviewing processes, identifying bottlenecks, and implementing streamlined solutions can enhance efficiency and reduce stress. Seeking feedback from team members and stakeholders helps in identifying areas for improvement and fosters a culture of learning and growth.
In conclusion, handling pressure and tight deadlines in a logistics role requires a proactive approach, effective communication, adaptability, and stress management techniques. By cultivating these skills and fostering a supportive team environment, individuals can navigate the challenges of this fast-paced industry successfully. Embracing continuous improvement and staying focused on the end goal helps in maintaining perspective and delivering results under pressure.

In a logistics setting, complex problems often arise that require creative thinking and quick decision-making to resolve. One such instance occurred during my time as a warehouse manager for a large e-commerce company. We received a significant order from a high-priority client with a tight deadline. However, upon reviewing our inventory, I discovered that we were short on a critical component needed to complete the order.
Identifying the Problem
The first step in solving the problem was to assess the situation and gather all relevant information. I quickly realized that our usual supplier for the missing component was unable to deliver the required quantity within the given timeframe. This meant that we needed to find an alternative solution to fulfill the client's order on time.
Brainstorming Solutions
I assembled a team of experienced staff members to brainstorm potential solutions. We considered various options, such as sourcing the component from alternative suppliers, modifying the product design, or negotiating an extension with the client. Each option had its pros and cons, and we needed to weigh them carefully to determine the best course of action.
Collaborating with Stakeholders
To make an informed decision, I reached out to key stakeholders, including the sales team and the client. Through open communication and collaboration, we were able to gain a better understanding of the client's priorities and expectations. This helped us narrow down our options and focus on solutions that would meet the client's needs while minimizing the impact on our operations.
Implementing the Solution
After careful consideration, we decided to source the missing component from a local supplier who could provide a smaller quantity at a higher cost. While this option was not ideal from a financial perspective, it allowed us to complete the order on time and maintain our commitment to the client. I worked closely with the procurement team to expedite the purchase and ensure that the components were delivered to our warehouse as quickly as possible.
Reflecting on the Outcome
Thanks to the collaborative efforts of our team and the swift implementation of our solution, we were able to successfully fulfill the client's order within the given timeframe. This experience taught me the importance of thinking creatively, communicating effectively, and being adaptable in the face of complex challenges. It also highlighted the value of having a strong team that can work together to overcome obstacles and achieve common goals.
Lessons Learned
Looking back on this experience, I learned several valuable lessons that I have carried with me in my professional life. First, it is essential to remain calm and focused when faced with complex problems, as panic and stress can cloud judgment and hinder decision-making. Second, involving key stakeholders and fostering open communication can lead to more effective solutions and better outcomes. Finally, being willing to think outside the box and consider unconventional approaches can often be the key to overcoming seemingly impossible challenges in a logistics setting.

The logistics department faces numerous challenges in today's fast-paced and globalized business environment. One of the most significant challenges is the increasing complexity of supply chain networks. As companies expand their operations globally, they must manage multiple suppliers, distributors, and customers across different regions and time zones. This complexity makes it difficult to maintain visibility and control over the entire supply chain, leading to potential disruptions and inefficiencies.
Technological Advancements and Integration
Another major challenge is keeping up with rapid technological advancements and integrating new technologies into existing logistics processes. The rise of e-commerce, mobile computing, and cloud-based solutions has transformed the way logistics operations are conducted. Logistics departments must continually adapt to these changes and invest in new technologies to remain competitive. However, integrating these technologies with legacy systems can be a complex and costly process, requiring significant resources and expertise.
Increasing Customer Expectations
In addition, logistics departments must meet ever-increasing customer expectations for faster, more flexible, and more personalized delivery options. Customers now expect same-day or next-day delivery, real-time tracking, and easy returns. Meeting these expectations requires logistics departments to optimize their transportation networks, improve inventory management, and enhance customer service capabilities. This can be challenging, especially for smaller companies with limited resources and infrastructure.
Talent Acquisition and Retention
Attracting and retaining skilled logistics professionals is another significant challenge. The logistics industry is facing a shortage of qualified workers, particularly in areas such as supply chain management, transportation, and warehousing. This shortage is due to a combination of factors, including an aging workforce, a lack of interest among younger generations, and the increasing complexity of logistics roles. Logistics departments must develop effective recruitment and retention strategies to build and maintain a strong talent pipeline.
Regulatory Compliance and Sustainability
Regulatory compliance and sustainability are also critical challenges for logistics departments. The logistics industry is subject to numerous regulations related to transportation, customs, and environmental protection. Keeping up with these regulations and ensuring compliance can be a complex and time-consuming process. Additionally, there is growing pressure on logistics departments to adopt sustainable practices and reduce their environmental impact. This requires investing in new technologies, optimizing transportation networks, and collaborating with suppliers and customers to develop eco-friendly solutions.
Cost Management and Optimization
Finally, logistics departments must continually focus on cost management and optimization to remain competitive. This involves identifying opportunities to reduce transportation costs, optimize inventory levels, and improve operational efficiency. However, balancing cost reduction with service quality and customer satisfaction can be a delicate balance. Logistics departments must use data analytics and other tools to make informed decisions and drive continuous improvement.
Conclusion
In conclusion, logistics departments face numerous challenges in today's complex and dynamic business environment. These challenges include managing global supply chain networks, keeping up with technological advancements, meeting customer expectations, attracting and retaining talent, ensuring regulatory compliance and sustainability, and optimizing costs. To overcome these challenges, logistics departments must invest in new technologies, develop effective strategies, and foster a culture of continuous improvement. By doing so, they can position themselves for success in the face of ever-changing market conditions and customer demands.

Measuring and tracking key performance indicators (KPIs) in logistics is crucial for ensuring operational efficiency and customer satisfaction. Our company employs a comprehensive approach to monitor and analyze various metrics that reflect the performance of our logistics processes. We utilize advanced software systems that integrate data from multiple sources, including warehouse management, transportation management, and order fulfillment systems. This allows us to have a holistic view of our logistics operations and identify areas for improvement.
Inventory Accuracy and Turnover
One of the primary KPIs we track is inventory accuracy, which measures the discrepancy between recorded and actual inventory levels. We conduct regular cycle counts and use barcode scanning technology to ensure accurate inventory tracking. Additionally, we monitor inventory turnover rates to optimize stock levels and minimize holding costs. By maintaining high inventory accuracy and turnover, we can respond quickly to customer demands and avoid stockouts or overstocking.
On-Time Delivery and Order Fulfillment
Timely delivery is a critical aspect of logistics performance, directly impacting customer satisfaction. We measure on-time delivery rates by comparing the actual delivery date against the promised delivery date. Our order fulfillment process is closely monitored, tracking metrics such as order processing time, picking accuracy, and packing efficiency. By optimizing these processes and ensuring on-time delivery, we can meet customer expectations and build long-term relationships.
Transportation Efficiency and Cost
Efficient transportation is vital for minimizing costs and reducing lead times. We track various transportation KPIs, including route optimization, fuel consumption, and vehicle utilization. By analyzing these metrics, we can identify opportunities to streamline our transportation network, reduce empty miles, and optimize load consolidation. Additionally, we monitor transportation costs closely to ensure we are getting the best rates from our carriers and maintaining cost-effectiveness.
Warehouse Productivity and Space Utilization
Warehouse operations play a significant role in logistics performance. We measure warehouse productivity by tracking metrics such as order picking speed, accuracy, and labor efficiency. We also monitor space utilization to ensure optimal storage and minimize wasted space. By implementing lean warehousing practices and using data-driven insights, we can improve warehouse productivity and reduce operating costs.
Customer Satisfaction and Feedback
Ultimately, the success of our logistics operations is determined by customer satisfaction. We regularly survey our customers to gather feedback on their experience with our services. We track metrics such as order accuracy, damage rates, and customer complaint resolution time. By actively listening to our customers and addressing their concerns, we can continuously improve our logistics processes and build strong relationships.
Continuous Improvement and Benchmarking
Measuring and tracking KPIs is not a one-time exercise but an ongoing process of continuous improvement. We regularly review our performance metrics, identify trends, and set targets for improvement. We also benchmark our performance against industry standards and best practices to ensure we remain competitive. By fostering a culture of continuous improvement and data-driven decision-making, we can adapt to changing market conditions and exceed customer expectations.

A recent successful logistics project involved the implementation of a new warehouse management system (WMS) for a large e-commerce company. The project aimed to streamline the company's order fulfillment process, reduce errors, and improve overall efficiency. The project team consisted of logistics experts, IT professionals, and key stakeholders from various departments within the organization.
Thorough Planning and Preparation
One of the primary factors contributing to the project's success was thorough planning and preparation. The team conducted extensive research on available WMS solutions and carefully evaluated each option based on the company's specific needs and requirements. They also developed a detailed project plan, including timelines, milestones, and resource allocation, to ensure a smooth implementation process.
Effective Communication and Collaboration
Effective communication and collaboration among team members and stakeholders were crucial to the project's success. Regular meetings and updates kept everyone informed about progress, challenges, and any necessary adjustments to the plan. The team also actively sought input and feedback from end-users, such as warehouse staff, to ensure the new system met their needs and expectations.
Comprehensive Training and Support
To ensure a successful transition to the new WMS, the project team provided comprehensive training and support to all users. They developed detailed training materials, conducted hands-on workshops, and offered ongoing support during and after the implementation. This approach helped employees quickly adapt to the new system and minimize disruptions to day-to-day operations.
Robust Testing and Quality Assurance
Before going live with the new WMS, the project team conducted extensive testing and quality assurance measures. They performed thorough system testing, including integration testing with other existing systems, to identify and resolve any issues or bugs. This proactive approach helped ensure a smooth and successful launch of the new system.
Continuous Improvement and Optimization
The project team recognized that the success of the new WMS relied on continuous improvement and optimization. They established a feedback loop to gather insights from users and regularly monitored system performance. This allowed them to identify areas for improvement and implement necessary changes to further enhance efficiency and productivity.
Measurable Results and Benefits
The successful implementation of the new WMS yielded measurable results and benefits for the e-commerce company. Key performance indicators, such as order accuracy, fulfillment speed, and inventory visibility, significantly improved. The company also experienced cost savings through reduced errors and increased operational efficiency.
Conclusion
The success of this recent logistics project can be attributed to several key factors, including thorough planning, effective communication, comprehensive training, robust testing, and a commitment to continuous improvement. By leveraging these elements, the project team was able to deliver a solution that enhanced the company's logistics capabilities and provided tangible business benefits.

Success in the transport and logistics industry requires a diverse set of skills. First and foremost, individuals must possess strong organizational abilities. They need to manage complex schedules, coordinate routes, and ensure timely deliveries. Attention to detail is crucial to avoid costly mistakes and maintain customer satisfaction.
Communication and Problem-Solving
Effective communication is another essential skill in this industry. Logistics professionals must collaborate with various stakeholders, including drivers, warehouse staff, and clients. They should be able to convey information clearly and concisely, both verbally and in writing. Problem-solving skills are equally important, as unexpected challenges can arise at any time. The ability to think on one's feet and find creative solutions is invaluable.
Technological Proficiency
In today's digital age, technological proficiency is a must. Logistics companies rely heavily on software systems for tracking shipments, managing inventory, and optimizing routes. Familiarity with these tools is essential for streamlining operations and improving efficiency. Additionally, staying updated with the latest technological advancements can give professionals a competitive edge in the industry.
Leadership and Adaptability
Leadership skills are vital for those aspiring to advance in their careers. Logistics managers must be able to motivate and guide their teams effectively. They should foster a positive work environment and encourage collaboration among employees. Furthermore, adaptability is crucial in an industry that is constantly evolving. Being open to change and willing to learn new skills can help professionals thrive in the face of challenges.
Customer Service and Strategic Thinking
Excellent customer service skills are paramount in the transport and logistics industry. Professionals must be responsive to client needs and strive to exceed expectations. Building strong relationships with customers can lead to long-term partnerships and business growth. Moreover, strategic thinking is essential for making informed decisions. Logistics professionals should be able to analyze data, identify trends, and develop innovative strategies to optimize operations and reduce costs.
Time Management and Stress Resilience
Effective time management is crucial in an industry where every minute counts. Logistics professionals must prioritize tasks, meet deadlines, and manage their workload efficiently. They should also be able to work well under pressure and maintain composure in stressful situations. Resilience and the ability to bounce back from setbacks are key to long-term success in this fast-paced industry.
Continuous Learning and Networking
To stay competitive in the transport and logistics industry, professionals must commit to continuous learning. Keeping up with industry trends, regulations, and best practices is essential for staying ahead of the curve. Attending conferences, workshops, and training sessions can help individuals expand their knowledge and skills. Additionally, networking with industry peers can provide valuable insights and opportunities for career growth.

Handling unexpected delays or disruptions in the supply chain requires a proactive and adaptable approach. Companies must develop contingency plans to mitigate potential risks and minimize the impact of disruptions. This involves identifying alternative suppliers, diversifying supply sources, and maintaining adequate inventory levels to buffer against shortages.
Effective Communication and Collaboration
Effective communication and collaboration with suppliers, logistics providers, and internal stakeholders are crucial. Regular updates on the status of shipments, potential delays, and corrective actions help maintain transparency and alignment. Establishing clear lines of communication and decision-making protocols streamlines problem-solving efforts.
Leveraging Technology for Visibility
Leveraging technology solutions such as real-time tracking, supply chain visibility platforms, and predictive analytics can provide valuable insights. These tools help identify potential disruptions early, enabling quick response and mitigation strategies. Data-driven decision-making allows for more informed and timely actions.
Flexibility and Agility in Operations
Building flexibility and agility into supply chain operations is essential for managing disruptions. This includes having multiple sourcing options, flexible manufacturing capabilities, and the ability to quickly adapt production schedules. Cross-functional teams can be formed to rapidly assess the impact of disruptions and implement solutions.
Continuous Risk Assessment and Monitoring
Conducting regular risk assessments and monitoring supply chain vulnerabilities helps anticipate potential disruptions. This involves analyzing supplier performance, geopolitical risks, natural disasters, and other factors that may impact the supply chain. Proactive risk management allows for the development of contingency plans and mitigation strategies.
Building Resilience through Partnerships
Collaborating with strategic partners, such as suppliers, logistics providers, and industry peers, can enhance supply chain resilience. Sharing best practices, pooling resources, and establishing mutual support mechanisms can help mitigate the impact of disruptions. Strong partnerships foster trust and enable joint problem-solving efforts.
Continuous Improvement and Learning
Handling supply chain disruptions is an ongoing process that requires continuous improvement and learning. Conducting post-disruption reviews, analyzing root causes, and implementing corrective actions help prevent future occurrences. Sharing lessons learned across the organization and with partners promotes a culture of resilience and adaptability.
In conclusion, effectively handling unexpected delays or disruptions in the supply chain requires a combination of proactive planning, effective communication, technology adoption, flexibility, risk management, strong partnerships, and continuous improvement. By implementing these strategies, companies can minimize the impact of disruptions and maintain the smooth flow of goods and services to their customers.

Optimizing transportation routes and logistics processes is crucial for efficient and cost-effective operations in various industries. One notable example of such optimization occurred during my internship at a manufacturing company, where I was tasked with improving the efficiency of their product distribution network. The company faced challenges in terms of high transportation costs and longer delivery times, which prompted the need for a comprehensive analysis and redesign of their existing logistics process.
Data Collection and Analysis
To begin the optimization process, I collected extensive data on the company's current transportation routes, delivery schedules, and vehicle capacities. This data served as the foundation for identifying inefficiencies and areas for improvement. I utilized various tools, such as geographic information systems (GIS) and route optimization software, to analyze the data and gain insights into the existing transportation network.
Identifying Inefficiencies
Through meticulous analysis, I identified several inefficiencies in the company's transportation routes. These included overlapping routes, underutilized vehicle capacities, and suboptimal delivery schedules. By pinpointing these issues, I was able to develop targeted strategies to streamline the logistics process and reduce overall transportation costs.
Developing Optimization Strategies
Based on the identified inefficiencies, I developed a multi-faceted optimization strategy. This involved redesigning transportation routes to minimize overlap and reduce total distance traveled. I also proposed a new delivery schedule that prioritized high-volume customers and optimized vehicle utilization. Additionally, I explored the possibility of consolidating shipments to reduce the number of trips required.
Collaboration and Stakeholder Engagement
Throughout the optimization process, I actively collaborated with various stakeholders, including transportation managers, warehouse personnel, and customer service representatives. Their insights and feedback were invaluable in refining the proposed strategies and ensuring their practicality and effectiveness. By engaging stakeholders, I fostered a sense of ownership and commitment to the optimization efforts.
Implementation and Results
Upon receiving approval from senior management, I led the implementation of the optimized transportation routes and logistics processes. This involved coordinating with the transportation team, updating route maps, and communicating the changes to all relevant parties. The implementation phase required close monitoring and continuous refinement to address any unforeseen challenges or adjustments needed.
Measurable Improvements
The optimization efforts yielded significant improvements in the company's transportation and logistics operations. By streamlining routes and improving vehicle utilization, we achieved a 15% reduction in transportation costs. Additionally, the optimized delivery schedules resulted in faster and more reliable deliveries, enhancing customer satisfaction. The increased efficiency also allowed the company to handle higher volumes of shipments without requiring additional resources.
Lessons Learned and Continuous Improvement
The experience of optimizing transportation routes and logistics processes taught me valuable lessons in data-driven decision making, stakeholder collaboration, and the importance of continuous improvement. I realized that optimization is an ongoing process that requires regular monitoring, analysis, and adaptation to changing circumstances. By embracing a culture of continuous improvement, companies can stay ahead of the curve and maintain a competitive edge in their respective industries.
In conclusion, optimizing transportation routes and logistics processes is a complex yet rewarding endeavor. By leveraging data analysis, developing targeted strategies, and engaging stakeholders, companies can achieve significant improvements in efficiency, cost savings, and customer satisfaction. The lessons learned from such optimization efforts can be applied across various industries, driving operational excellence and sustainable growth.

Logistics and supply chain management aim to efficiently manage the flow of goods, services, and information from suppliers to customers. The primary objectives include optimizing resource allocation, minimizing costs, and ensuring timely delivery of products to meet customer demands. Effective logistics and supply chain management also focus on improving customer satisfaction by providing high-quality products and services.
Streamlining Operations
One of the key objectives of logistics and supply chain management is to streamline operations and reduce waste. This involves identifying and eliminating inefficiencies in the supply chain, such as unnecessary transportation, inventory, or handling. By optimizing processes, companies can reduce costs, improve productivity, and enhance overall performance.
Enhancing Collaboration
Logistics and supply chain management also aim to foster collaboration among all stakeholders in the supply chain. This includes suppliers, manufacturers, distributors, and customers. By working together and sharing information, companies can improve communication, reduce lead times, and respond quickly to changes in market conditions.
Implementing Technology
Technology plays a crucial role in achieving the objectives of logistics and supply chain management. Companies use various tools and systems, such as enterprise resource planning (ERP), transportation management systems (TMS), and warehouse management systems (WMS). These technologies help automate processes, improve visibility, and enable data-driven decision-making.
Managing Risk
Another important objective of logistics and supply chain management is to identify and mitigate risks. Supply chains are vulnerable to various disruptions, such as natural disasters, political instability, or supplier failures. Effective risk management strategies, such as diversifying suppliers, maintaining adequate inventory levels, and developing contingency plans, can help minimize the impact of disruptions.
Ensuring Sustainability
In recent years, sustainability has become a key objective of logistics and supply chain management. Companies are increasingly focusing on reducing their environmental impact, such as minimizing carbon emissions, waste, and resource consumption. This involves implementing eco-friendly practices, such as using renewable energy, optimizing transportation routes, and recycling materials.
Measuring Performance
To achieve the objectives of logistics and supply chain management, companies must regularly measure and monitor performance. This involves setting key performance indicators (KPIs), such as on-time delivery, inventory turnover, and customer satisfaction. By tracking these metrics, companies can identify areas for improvement and make data-driven decisions to optimize their supply chain.
Continuous Improvement
Logistics and supply chain management is an ongoing process that requires continuous improvement. Companies must constantly adapt to changing market conditions, customer needs, and technological advancements. By embracing a culture of continuous improvement, companies can stay competitive and achieve long-term success.

Technology can significantly enhance logistics and supply chain processes, leading to increased efficiency, reduced costs, and improved customer satisfaction. By leveraging advanced technologies such as artificial intelligence (AI), Internet of Things (IoT), blockchain, and automation, companies can streamline their operations and gain a competitive edge in the market.
Artificial Intelligence and Machine Learning
AI and machine learning algorithms can analyze vast amounts of data to optimize route planning and resource allocation. These technologies can predict demand, identify potential bottlenecks, and suggest solutions to mitigate risks. AI-powered chatbots and virtual assistants can also improve customer service by providing real-time support and tracking shipment status.
Internet of Things
IoT devices can monitor inventory levels, track shipments, and provide real-time visibility into the supply chain. By using sensors and RFID tags, companies can collect data on the location, condition, and status of their goods. This information can help optimize inventory management, reduce waste, and improve delivery times.
Blockchain Technology
Blockchain can increase transparency, security, and trust in the supply chain. By creating an immutable record of transactions, blockchain can reduce fraud, errors, and disputes. It can also facilitate faster and more efficient payments, reducing the need for intermediaries and paperwork.
Automation and Robotics
Automation and robotics can streamline warehouse operations, reducing labor costs and increasing accuracy. Automated storage and retrieval systems (ASRS) can optimize space utilization and reduce picking times. Collaborative robots can work alongside human workers, performing repetitive tasks and increasing productivity.
Cloud Computing and Big Data Analytics
Cloud computing can provide scalable and flexible infrastructure for logistics and supply chain operations. It can enable real-time data sharing and collaboration among stakeholders, improving decision-making and responsiveness. Big data analytics can help identify patterns, trends, and insights from the vast amounts of data generated by the supply chain.
Challenges and Considerations
While technology can bring significant benefits to logistics and supply chain processes, there are also challenges to consider. These include the high initial costs of implementation, the need for skilled personnel, and the potential for data privacy and security risks. Companies must also ensure that their technology investments align with their overall business strategy and goals.
In conclusion, technology can play a crucial role in optimizing logistics and supply chain processes. By leveraging AI, IoT, blockchain, automation, cloud computing, and big data analytics, companies can improve efficiency, reduce costs, and enhance customer satisfaction. However, it is important to carefully consider the challenges and ensure that technology investments are aligned with business objectives.

Mitigating risks in global supply chains requires a proactive approach that involves various strategies. Firstly, companies should diversify their supplier base to reduce dependence on a single source. This helps to spread risk and ensures continuity of supply in case of disruptions. Secondly, implementing robust risk management processes, such as regular risk assessments and contingency planning, is crucial. These processes help identify potential threats and develop appropriate response strategies.
Enhancing Visibility and Collaboration
Enhancing visibility throughout the supply chain is another key strategy. By leveraging technology such as IoT devices and blockchain, companies can gain real-time insights into their supply chain operations. This increased transparency helps to identify bottlenecks, monitor performance, and make informed decisions. Additionally, fostering strong collaborations with suppliers and partners is essential. Regular communication, information sharing, and joint problem-solving efforts can help mitigate risks and improve overall supply chain resilience.
Building Resilience through Flexibility
Building flexibility into the supply chain is crucial for mitigating risks. This involves designing agile processes that can adapt quickly to changing circumstances. For example, having multiple sourcing options, flexible manufacturing capabilities, and adaptable logistics networks can help companies respond effectively to disruptions. Moreover, investing in inventory management strategies, such as safety stock and just-in-time delivery, can help strike a balance between risk mitigation and cost efficiency.
Embracing Technology and Innovation
Embracing technology and innovation is another important strategy. Adopting advanced analytics, artificial intelligence, and machine learning can help companies predict and mitigate risks. These technologies can analyze vast amounts of data, identify patterns, and provide early warning signals for potential disruptions. Additionally, exploring new technologies such as 3D printing and robotics can help to localize production and reduce reliance on global supply chains.
Developing a Risk-Aware Culture
Finally, developing a risk-aware culture within the organization is essential. This involves educating employees about potential risks, encouraging open communication, and fostering a proactive mindset. Regular training and awareness programs can help employees understand their roles in mitigating risks and contribute to overall supply chain resilience. By embedding risk management into the company's culture, it becomes an integral part of decision-making processes and operations.
In conclusion, mitigating risks in global supply chains requires a multi-faceted approach. By diversifying suppliers, enhancing visibility, building flexibility, embracing technology, and developing a risk-aware culture, companies can effectively navigate the complexities and uncertainties of global supply chains. Implementing these strategies helps to ensure business continuity, protect brand reputation, and maintain a competitive edge in today's dynamic business environment.

When interviewing for a Logistics Assistant position, candidates should expect a range of questions that assess their relevant skills and experience. Employers often ask about the applicant's familiarity with logistics software and their ability to manage inventory effectively. They may also inquire about the candidate's experience in coordinating shipments and deliveries, as well as their problem-solving skills in handling delays or discrepancies. Additionally, interviewers might ask behavioral questions to gauge the applicant's ability to work under pressure, communicate effectively with team members, and adapt to changing priorities.
Organizational Skills
Interviewers will likely ask questions that evaluate the candidate's organizational abilities, which are crucial for success in a Logistics Assistant role. They may ask about the applicant's experience in maintaining accurate records, managing multiple tasks simultaneously, and prioritizing workload. Candidates should provide specific examples of how they have demonstrated strong organizational skills in their previous roles, such as implementing a new filing system or successfully managing a complex project.
Attention to Detail
Logistics Assistants must have a keen eye for detail to ensure accuracy in inventory management and order fulfillment. Interviewers may ask questions that assess the candidate's ability to spot errors, verify information, and maintain high standards of quality control. They might also inquire about the applicant's experience in conducting inventory audits or reconciling discrepancies in shipping documents.
Example Questions:
How do you ensure accuracy when managing inventory?
Describe a time when you caught an error in a shipment. How did you handle it?
Communication and Collaboration
Logistics Assistants often work closely with other departments, such as sales, customer service, and production. Interviewers may ask questions that evaluate the candidate's communication and collaboration skills, such as their ability to build positive relationships with colleagues, communicate clearly and concisely, and work effectively in a team environment. They may also inquire about the applicant's experience in coordinating with external partners, such as suppliers or carriers.
Example Questions:
How do you foster positive relationships with colleagues from other departments?
Describe a time when you had to collaborate with an external partner to resolve a logistics issue.
Problem-Solving Skills
In the fast-paced world of logistics, problems can arise at any time. Interviewers will likely ask questions that assess the candidate's ability to think critically, analyze situations, and develop effective solutions. They may ask about the applicant's experience in handling delays, resolving customer complaints, or finding alternative routes or carriers when necessary. Candidates should provide specific examples of how they have successfully navigated challenges in their previous roles.
Example Questions:
Describe a time when you had to solve a complex logistics problem. What steps did you take?
How do you prioritize tasks when faced with multiple competing deadlines?

Preparing for a Logistics Assistant interview requires a combination of researching the company, understanding the job requirements, and practicing interview skills. Begin by thoroughly reviewing the job description and the company's website to gain insights into their operations and culture. Identify the key qualifications and skills they seek in a candidate and assess how your experience aligns with these requirements. Consider specific examples from your past work that demonstrate your ability to handle logistics tasks efficiently and effectively.
Research the Company and Industry
Conduct additional research on the company and the logistics industry to expand your knowledge and understanding. Look for recent news articles, press releases, or industry reports that provide relevant information. Familiarize yourself with common logistics terminology, processes, and technologies. This research will help you engage in informed discussions during the interview and show your genuine interest in the position and the company.
Prepare for Common Interview Questions
Anticipate common interview questions and prepare thoughtful and concise responses. Questions may cover topics such as your experience with inventory management, shipping and receiving procedures, and problem-solving skills. Use the STAR method (Situation, Task, Action, Result) to structure your answers, providing specific examples that highlight your abilities. Practice your responses out loud to improve your delivery and confidence.
Highlight Your Relevant Skills
Identify the key skills required for a Logistics Assistant role and emphasize how you possess and have applied these skills. Important skills may include attention to detail, organizational abilities, communication skills, and proficiency with logistics software. Use concrete examples to illustrate how you have utilized these skills in previous roles or during your education.
Prepare Questions for the Interviewer
Demonstrate your interest and engagement by preparing thoughtful questions for the interviewer. Inquire about the company's logistics processes, team dynamics, and opportunities for growth and development. Ask about the challenges the logistics department faces and how you can contribute to solving them. Asking well-informed questions shows that you have done your research and are genuinely interested in the position.
Practice Interview Etiquette
Pay attention to your interview etiquette to create a positive impression. Dress professionally and arrive at the interview location early. Bring copies of your resume, a notepad, and a pen. Greet the interviewer with a firm handshake and maintain eye contact throughout the conversation. Listen actively and respond thoughtfully to their questions. Show enthusiasm for the opportunity and express your interest in contributing to the company's success.
Final Preparations
In the days leading up to the interview, review your research and practice your responses. Get a good night's sleep and ensure you have all the necessary documents and directions to the interview location. Stay calm and confident, remembering that you have prepared thoroughly for this opportunity. By following these steps and showcasing your skills and experience, you can increase your chances of success in a Logistics Assistant interview.

Finding sample answers to Logistics Assistant interview questions in PDF format can be accomplished through various online resources. Websites such as JobTestPrep, Glassdoor, and Indeed offer comprehensive guides and sample questions specific to logistics roles. These resources provide valuable insights into the types of questions commonly asked during interviews for Logistics Assistant positions. Additionally, industry-specific websites and forums, such as Supply Chain Management Review and Logistics Management, may have downloadable PDF resources with sample interview questions and answers.
Utilize Job Search Websites
Job search websites like Monster, CareerBuilder, and ZipRecruiter often feature interview preparation materials for various industries, including logistics. These websites may have downloadable PDF guides containing sample interview questions and suggested answers for Logistics Assistant roles. Take advantage of these resources to familiarize yourself with the types of questions you may encounter during your interview.
Explore Industry-Specific Forums and Websites
Engage with logistics and supply chain management forums and websites to access interview preparation materials. These platforms often have dedicated sections where professionals share their experiences and offer guidance to job seekers. Look for threads or discussions related to Logistics Assistant interviews and see if any members have shared sample questions and answers in PDF format.
Consult with Recruitment Agencies
Recruitment agencies specializing in logistics and supply chain management can be valuable sources of interview preparation materials. These agencies often work closely with employers in the industry and have insights into the interview processes. Reach out to recruitment agencies and inquire if they have any PDF resources containing sample Logistics Assistant interview questions and answers.
Leverage Professional Networks
Tap into your professional network, including colleagues, mentors, and industry connections, to gather interview preparation resources. Ask if they have any PDF documents with sample Logistics Assistant interview questions and answers that they can share with you. Your network may have firsthand experience interviewing for similar roles and can provide valuable guidance.
Check Educational Institutions and Training Providers
Educational institutions and training providers offering courses in logistics and supply chain management may have interview preparation resources available. Check their websites or reach out to their career services departments to inquire about any PDF materials containing sample Logistics Assistant interview questions and answers. These institutions often have industry connections and may have compiled relevant resources for their students and alumni.
Remember, while sample answers can provide guidance, it's essential to tailor your responses to your own experiences and qualifications. Use the sample answers as a starting point to craft compelling and personalized responses that showcase your skills and suitability for the Logistics Assistant role.

When preparing for a logistics management job interview, candidates should anticipate questions that assess their knowledge, skills, and experience. Interviewers often ask about the candidate's ability to optimize supply chain processes, reduce costs, and improve efficiency. They may inquire about the candidate's familiarity with inventory management systems, transportation networks, and warehousing strategies. Additionally, interviewers may pose situational questions to evaluate the candidate's problem-solving skills and ability to handle challenges in a logistics environment.
Understanding the Supply Chain
Candidates should be ready to demonstrate their understanding of the entire supply chain process, from procurement to delivery. Interviewers may ask about the candidate's experience in managing relationships with suppliers, negotiating contracts, and ensuring timely deliveries. They may also inquire about the candidate's knowledge of international trade regulations, customs procedures, and import/export documentation. Candidates should be prepared to discuss their ability to analyze data, forecast demand, and make informed decisions to optimize the supply chain.
Inventory Management
Interviewers often ask questions related to inventory management, as it is a crucial aspect of logistics. Candidates should be ready to discuss their experience in implementing and maintaining inventory control systems, conducting physical inventory counts, and managing stock levels. They may also be asked about their strategies for reducing inventory costs, minimizing stockouts, and improving inventory turnover. Candidates should demonstrate their ability to use data analysis tools and techniques to optimize inventory levels and improve overall efficiency.
Transportation and Distribution
Logistics management involves coordinating the movement of goods from suppliers to customers, so interviewers may ask about the candidate's experience in managing transportation and distribution networks. Candidates should be prepared to discuss their knowledge of various transportation modes, such as air, sea, rail, and road, and their ability to select the most cost-effective and efficient options. They may also be asked about their experience in route planning, carrier selection, and freight consolidation to optimize transportation costs and improve delivery times.
Warehousing and Material Handling
Candidates should expect questions related to warehousing and material handling, as these are essential components of logistics management. Interviewers may ask about the candidate's experience in designing and managing warehouse layouts, implementing picking and packing processes, and ensuring proper storage and handling of goods. They may also inquire about the candidate's knowledge of warehouse management systems, automation technologies, and safety procedures. Candidates should be prepared to discuss their strategies for improving warehouse efficiency, reducing labor costs, and enhancing customer service.
Problem-Solving and Contingency Planning
Logistics management often involves dealing with unexpected challenges and disruptions, so interviewers may pose situational questions to assess the candidate's problem-solving skills. Candidates should be ready to provide examples of how they have handled supply chain disruptions, such as transportation delays, supplier issues, or natural disasters. They should demonstrate their ability to think quickly, adapt to changing circumstances, and develop contingency plans to minimize the impact on operations and customer service.
Continuous Improvement and Technology
Interviewers may also ask about the candidate's commitment to continuous improvement and their familiarity with emerging technologies in logistics. Candidates should be prepared to discuss their experience in implementing process improvements, such as lean manufacturing principles or Six Sigma methodologies, to streamline operations and reduce waste. They should also demonstrate their knowledge of supply chain technology trends, such as blockchain, Internet of Things (IoT), and artificial intelligence (AI), and how they can be applied to enhance logistics management.

During a job interview, effectively showcasing your logistics management skills and experience is crucial to landing the position. To make a strong impression, prepare specific examples of your achievements and challenges you've overcome. Highlight your ability to optimize supply chain processes, reduce costs, and improve efficiency. Demonstrate your proficiency in logistics software and your experience collaborating with cross-functional teams. Emphasize your problem-solving skills and your ability to adapt to changing circumstances. Provide quantifiable results whenever possible to illustrate the impact of your work. Throughout the interview, maintain a confident and professional demeanor, and be prepared to ask thoughtful questions about the company and the role.
Prepare Specific Examples
Before the interview, reflect on your logistics management experience and identify specific examples that showcase your skills. Choose stories that highlight your ability to optimize processes, reduce costs, and improve efficiency. Practice narrating these examples concisely, focusing on the challenges you faced, the actions you took, and the results you achieved. Having concrete examples ready will help you respond to questions confidently and demonstrate your expertise.
Highlight Your Technical Proficiency
Logistics management often involves working with specialized software and technologies. During the interview, emphasize your proficiency in relevant tools, such as transportation management systems (TMS), warehouse management systems (WMS), and enterprise resource planning (ERP) software. Discuss how you've used these tools to streamline operations, improve visibility, and make data-driven decisions. Showcasing your technical skills will demonstrate your ability to thrive in a modern logistics environment.
Collaborative Experience
Logistics management rarely happens in isolation; it often requires collaboration with cross-functional teams. Highlight your experience working with colleagues from various departments, such as sales, manufacturing, and customer service. Share examples of how you've fostered effective communication, resolved conflicts, and worked together to achieve common goals. Demonstrating your ability to collaborate will show that you can be a valuable team player.
Problem-Solving Skills
Logistics managers often face complex challenges that require creative problem-solving. During the interview, discuss instances where you've encountered obstacles and how you've overcome them. Explain your thought process, the steps you took, and the outcomes you achieved. Emphasize your ability to think critically, adapt to changing circumstances, and find innovative solutions. Showcasing your problem-solving skills will demonstrate your resilience and ability to handle the responsibilities of the role.
Quantifiable Results
Whenever possible, provide quantifiable results to illustrate the impact of your work. Share metrics such as cost savings, efficiency improvements, or customer satisfaction rates. Using numbers and percentages will make your achievements more tangible and memorable to the interviewer. Be prepared to explain how you achieved these results and what strategies you employed. Quantifiable results will help you stand out from other candidates and demonstrate your value to the organization.
Ask Thoughtful Questions
At the end of the interview, be prepared to ask thoughtful questions about the company and the role. Inquire about their current logistics challenges, plans for growth, and opportunities for professional development. Asking informed questions will show your genuine interest in the position and your desire to contribute to the company's success. It will also give you valuable insights into whether the role aligns with your career goals and expectations.
By following these strategies, you can effectively showcase your logistics management skills and experience during a job interview. Remember to be confident, articulate, and enthusiastic throughout the conversation. With thorough preparation and a strong focus on your achievements, you'll be well-positioned to make a lasting impression and secure the logistics management position you desire.

Interviewers typically focus on several key areas of logistics management when assessing candidates during the hiring process. They seek to evaluate the applicant's knowledge, skills, and experience in these critical domains to determine their suitability for the role. Let's explore the primary areas that interviewers emphasize.
Supply Chain Management
Interviewers assess the candidate's understanding of supply chain management principles and their ability to optimize processes. They look for individuals who can effectively manage the flow of goods from suppliers to customers. Key aspects include:
Sourcing and procurement strategies
Inventory management techniques
Distribution network optimization
Vendor relationship management
Transportation and Logistics
Efficient transportation and logistics are crucial for timely delivery and cost control. Interviewers evaluate the candidate's knowledge of:
Various modes of transportation (e.g., air, sea, road, rail)
Carrier selection and contract negotiation
Route optimization and shipment consolidation
Customs regulations and international trade compliance
Warehouse Management
Effective warehouse management ensures smooth operations and inventory accuracy. Interviewers assess the candidate's expertise in:
Warehouse layout and space utilization
Inventory control and stock rotation
Order processing and fulfillment
Material handling equipment and automation
Technology and Systems
Logistics management heavily relies on technology and systems to streamline processes and enhance efficiency. Interviewers focus on the candidate's proficiency in:
Warehouse Management Systems (WMS)
Transportation Management Systems (TMS)
Enterprise Resource Planning (ERP) software
Data analysis and reporting tools
Continuous Improvement and Problem-Solving
Interviewers seek candidates who can identify areas for improvement and implement solutions. They assess the applicant's ability to:
Analyze processes and identify inefficiencies
Develop and implement cost-saving initiatives
Resolve supply chain disruptions and mitigate risks
Foster a culture of continuous improvement
Leadership and Communication
Effective leadership and communication skills are essential in logistics management. Interviewers evaluate the candidate's capability to:
Lead and motivate teams
Collaborate with cross-functional departments
Communicate clearly and persuasively
Build strong relationships with internal and external stakeholders
By focusing on these key areas, interviewers gain a comprehensive understanding of the candidate's qualifications and potential to excel in a logistics management role. Demonstrating expertise and experience in these domains increases the likelihood of a successful interview outcome and securing the desired position in logistics management.

Logistics interviews often focus on assessing a candidate's knowledge, experience, and problem-solving skills in supply chain management. Interviewers seek to understand how well the applicant can handle challenges and optimize logistics processes. Some common logistics interview questions revolve around inventory management, transportation, warehousing, and distribution. Candidates should prepare to discuss their familiarity with industry-specific software, their ability to manage relationships with suppliers and carriers, and their strategies for reducing costs and improving efficiency.
Inventory Management Questions
Interviewers may ask about your experience with inventory control systems and how you manage stock levels. They want to know if you can forecast demand accurately, minimize inventory costs, and prevent stockouts. A strong answer would demonstrate your ability to analyze data, set appropriate reorder points, and collaborate with other departments to ensure optimal inventory levels.
Example Question:
"How do you determine the right stock levels for a product, considering factors like lead time and demand variability?"
Appropriate Answer:
"I analyze historical sales data and consider factors such as seasonality, promotions, and market trends. I collaborate with sales and marketing teams to understand upcoming initiatives that may impact demand. Based on this information, I calculate safety stock levels and reorder points to maintain adequate inventory while minimizing holding costs."
Transportation and Logistics Questions
Interviewers may inquire about your knowledge of transportation modes, routing, and carrier selection. They want to assess your ability to design efficient transportation networks, negotiate rates, and ensure on-time deliveries. A good answer would highlight your experience in managing transportation costs, optimizing routes, and handling logistics challenges.
Example Question:
"How do you select carriers and evaluate their performance?"
Appropriate Answer:
"I consider factors such as cost, transit times, reliability, and service levels when selecting carriers. I regularly review their performance metrics, including on-time delivery rates, claims ratios, and customer feedback. I establish clear KPIs and conduct periodic reviews to ensure carriers meet our standards and provide value to our supply chain."
Warehousing and Distribution Questions
Interviewers may ask about your experience in managing warehouses, optimizing layouts, and improving pick-and-pack processes. They want to know how you can streamline operations, reduce handling costs, and ensure accurate order fulfillment. A strong answer would showcase your knowledge of warehouse management systems, your ability to design efficient layouts, and your strategies for enhancing productivity.
Example Question:
"How do you optimize warehouse layout and picking routes to improve efficiency?"
Appropriate Answer:
"I analyze product velocity and storage requirements to determine the optimal layout. I use techniques like ABC analysis and slotting to place high-volume items in easily accessible locations. I design picking routes that minimize travel time and optimize picker productivity. By continuously monitoring performance metrics and seeking employee feedback, I identify opportunities for improvement."
Preparing for logistics interviews requires a solid understanding of industry best practices and the ability to articulate your experience effectively. Be ready to discuss specific examples of how you have tackled logistics challenges, implemented process improvements, and contributed to cost savings. Demonstrate your problem-solving skills, attention to detail, and commitment to continuous improvement to stand out as a strong candidate.

Finding a comprehensive PDF guide on excelling in a logistics job interview requires thorough research and discretion. Many websites offer resources for job seekers, but not all provide reliable or relevant information. To locate a suitable guide, start by searching reputable career websites and logistics industry forums.
Identifying Reliable Sources
When searching for a logistics job interview guide, prioritize sources with a proven track record of providing accurate information. Well-established career websites, such as Indeed, Monster, and Glassdoor, often feature articles and guides written by industry experts. These platforms also host user-generated content, including interview tips and experiences from professionals in the logistics field.
Industry-Specific Resources
In addition to general career websites, explore logistics industry associations and publications for targeted advice. Organizations like the Council of Supply Chain Management Professionals (CSCMP) and the International Warehouse Logistics Association (IWLA) may offer member resources, including interview preparation materials. Trade publications, such as Logistics Management and Supply Chain Dive, may also feature articles on interview best practices.
Assessing PDF Quality and Relevance
When you find a potential PDF guide, assess its quality and relevance before relying on its content. Check the publication date to ensure the information is current and applicable to modern logistics roles. Review the author's credentials to gauge their expertise and credibility within the industry. Skim the document to confirm it covers key topics, such as common interview questions, industry terminology, and role-specific knowledge.
Supplementing Your Preparation
While a comprehensive PDF guide can be an excellent foundation, supplement your preparation with additional resources. Conduct informational interviews with logistics professionals to gain insights into the interview process and desired qualifications. Practice your responses to common interview questions, and refine your knowledge of the company and role you are pursuing.
Tailoring Your Approach
Remember that each logistics job interview is unique, and the best preparation approach may vary. Consider the specific requirements and focus of the role, and adapt your preparation accordingly. Research the company's values, culture, and recent developments to demonstrate your understanding and enthusiasm during the interview.
Conclusion
Locating a comprehensive PDF guide on excelling in a logistics job interview requires careful research and evaluation. By targeting reputable career websites, industry associations, and trade publications, you can find high-quality resources to support your preparation. Supplement the guide with additional research and practice to tailor your approach and maximize your chances of success in your logistics job interview.

Finding a reliable source for downloading a sample logistics interview questions and answers PDF can be challenging. Many websites claim to offer such resources, but not all of them are trustworthy or provide accurate information. When searching for a dependable source, it is essential to consider factors such as the website's reputation, user reviews, and the quality of the content provided.
Reputable Websites
One way to ensure that you are downloading a reliable PDF is to stick to well-known and reputable websites. These websites often have a team of experts who create and review the content to ensure its accuracy and relevance. Some examples of reputable websites that may offer logistics interview questions and answers include:
Indeed.com
Glassdoor.com
Monster.com
CareerBuilder.com
Industry-Specific Websites
Another option is to search for industry-specific websites that cater to logistics professionals. These websites often have a wealth of resources, including interview questions and answers specific to the logistics field. Some examples of industry-specific websites include:
SupplyChain247.com
LogisticsMgmt.com
InboundLogistics.com
DCVelocity.com
Educational Institutions and Professional Organizations
Educational institutions and professional organizations related to logistics may also provide reliable resources for interview preparation. These organizations often have a vested interest in ensuring that their members or students have access to accurate and up-to-date information. Some examples include:
The Council of Supply Chain Management Professionals (CSCMP)
The International Society of Logistics (SOLE)
The Chartered Institute of Logistics and Transport (CILT)
Universities with logistics programs, such as MIT, Penn State, and Ohio State University
User Reviews and Recommendations
When considering a website for downloading a logistics interview questions and answers PDF, it can be helpful to read user reviews and recommendations. Other professionals who have used the resource can provide valuable insights into the quality and usefulness of the content. You can find user reviews on the website itself, or by searching for reviews on forums or social media platforms related to logistics.
Verifying the Content
Before relying on any downloaded PDF for your interview preparation, it is crucial to verify the content's accuracy and relevance. One way to do this is to cross-reference the information with other reputable sources. If the questions and answers align with what you find on other trusted websites or in industry publications, you can be more confident in the resource's reliability.
Customizing Your Preparation
While a downloaded PDF can be a helpful starting point, it is essential to customize your interview preparation to your specific situation. Consider the company you are interviewing with, the specific role you are applying for, and your own background and experiences. Use the downloaded resource as a foundation, but be sure to adapt and expand upon the content to create a personalized approach to your interview preparation.
Conclusion
In conclusion, finding a reliable source for downloading a logistics interview questions and answers PDF requires careful consideration. By focusing on reputable websites, industry-specific resources, educational institutions, and professional organizations, and by verifying the content and customizing your preparation, you can increase your chances of finding a valuable and trustworthy resource to aid in your interview success.

A successful logistics management system comprises several essential components that work together to ensure efficient and effective operations. These components include transportation management, warehouse management, inventory management, and order processing. Each of these elements plays a crucial role in optimizing the flow of goods and information throughout the supply chain.
Transportation Management
Transportation management involves the planning, execution, and control of the physical movement of goods from origin to destination. This component focuses on selecting the most appropriate modes of transportation, such as trucking, rail, air, or sea, based on factors like cost, speed, and reliability. Effective transportation management also includes route optimization, carrier selection, and freight consolidation to minimize costs and improve delivery times.
Warehouse Management
Warehouse management encompasses the efficient storage, handling, and movement of goods within a warehouse facility. This component includes activities such as receiving, put-away, picking, packing, and shipping. A well-designed warehouse layout, along with the use of advanced technologies like barcode scanning and radio-frequency identification (RFID), can significantly enhance the accuracy and productivity of warehouse operations.
Inventory Management
Inventory management focuses on maintaining optimal stock levels to meet customer demand while minimizing holding costs. This component involves accurate forecasting, inventory tracking, and replenishment strategies. By implementing just-in-time (JIT) inventory practices and establishing safety stock levels, companies can reduce the risk of stockouts and overstocking, ultimately improving inventory turnover and cash flow.
Order Processing
Order processing is the backbone of a successful logistics management system. It involves the timely and accurate processing of customer orders, from initial entry to final delivery. This component includes order validation, picking, packing, and shipping, as well as managing returns and exchanges. Streamlining order processing through automation and integration with other systems, such as customer relationship management (CRM) and enterprise resource planning (ERP), can significantly improve order accuracy and reduce lead times.
Integration and Visibility
To achieve optimal performance, a successful logistics management system must integrate all components seamlessly. This integration enables real-time information sharing, allowing for better decision-making and improved collaboration among supply chain partners. Additionally, end-to-end visibility is crucial for monitoring the movement of goods, identifying potential disruptions, and taking proactive measures to mitigate risks.
Continuous Improvement
A successful logistics management system embraces a culture of continuous improvement. By regularly monitoring key performance indicators (KPIs), such as on-time delivery, order accuracy, and inventory turnover, companies can identify areas for improvement and implement necessary changes. Continuous improvement initiatives, such as lean practices and Six Sigma, can help eliminate waste, reduce costs, and enhance overall supply chain efficiency.
In conclusion, a successful logistics management system requires the integration of transportation management, warehouse management, inventory management, and order processing. By focusing on these key components, along with fostering visibility, collaboration, and continuous improvement, companies can optimize their supply chain operations and gain a competitive edge in today's dynamic business environment.

Technology can be leveraged to optimize logistics processes and improve supply chain efficiency in several ways. By implementing advanced technologies such as artificial intelligence (AI), machine learning (ML), and the Internet of Things (IoT), companies can streamline their logistics operations and achieve significant improvements in supply chain performance.
Real-time Tracking and Monitoring
IoT devices and sensors can be used to track and monitor goods in real-time throughout the supply chain. This enables companies to have complete visibility over their inventory, shipments, and deliveries, allowing them to identify and address potential issues promptly. Real-time tracking also helps in optimizing routes and reducing transportation costs.
Predictive Analytics
AI and ML algorithms can analyze vast amounts of data to predict demand, optimize inventory levels, and forecast potential disruptions. By leveraging predictive analytics, companies can make informed decisions, reduce waste, and improve overall supply chain efficiency. This technology helps in identifying patterns and trends that may not be apparent to human analysts.
Automation and Robotics
Automation and robotics can streamline various logistics processes, such as warehousing, packaging, and material handling. Automated systems can work 24/7, reducing human error and increasing productivity. Robotics can also be used for tasks that are dangerous or difficult for humans, improving safety and efficiency in the workplace.
Blockchain Technology
Blockchain technology can be used to create a secure, transparent, and tamper-proof record of transactions in the supply chain. This technology can help in reducing fraud, improving traceability, and enhancing trust among supply chain partners. By using blockchain, companies can also automate various processes, such as payments and contracts, reducing administrative costs and improving efficiency.
Cloud Computing and Big Data
Cloud computing and big data analytics can help companies manage and analyze vast amounts of supply chain data. By storing data in the cloud, companies can access it from anywhere, enabling better collaboration and decision-making. Big data analytics can also help in identifying inefficiencies, reducing costs, and improving overall supply chain performance.
Collaborative Platforms
Collaborative platforms can be used to improve communication and coordination among supply chain partners. These platforms enable real-time information sharing, reducing the need for manual data entry and improving accuracy. By using collaborative platforms, companies can also improve their responsiveness to changes in demand or supply, ensuring a more agile and efficient supply chain.
Conclusion
In conclusion, technology can be a powerful tool for optimizing logistics processes and improving supply chain efficiency. By leveraging advanced technologies such as AI, ML, IoT, automation, robotics, blockchain, cloud computing, and big data analytics, companies can streamline their operations, reduce costs, and improve overall performance. As technology continues to evolve, it is essential for companies to stay up-to-date and adopt new solutions to remain competitive in today's fast-paced business environment.

Implementing effective strategies to mitigate risks and disruptions in logistics operations is crucial for maintaining a smooth supply chain. One key approach is to invest in advanced technology solutions such as real-time monitoring systems and predictive analytics tools. These technologies enable logistics managers to proactively identify potential issues and take corrective actions before disruptions occur.
Diversifying Supplier Network
Another important strategy is to diversify the supplier network and establish multiple sourcing options for critical components and materials. This helps reduce the impact of disruptions caused by supplier failures or geopolitical events. Additionally, developing strong relationships with key suppliers and fostering open communication channels can facilitate quick problem-solving and minimize the effects of disruptions.
Enhancing Visibility and Collaboration
Enhancing visibility and collaboration throughout the supply chain is also essential for mitigating risks and disruptions. Implementing a centralized supply chain management system that provides real-time data sharing and enables seamless collaboration among stakeholders can significantly improve responsiveness to disruptions. By fostering a culture of transparency and information sharing, logistics operations can quickly adapt to changing circumstances and minimize the impact of disruptions.
Building Resilience through Flexibility
Building resilience through flexibility is another crucial strategy for mitigating risks and disruptions in logistics operations. This involves designing logistics processes and networks that can easily adapt to changing demand patterns, supply disruptions, and other unforeseen events. Implementing flexible transportation options, such as intermodal shipping and multi-carrier strategies, can help ensure the continuity of operations during disruptions.
Developing Robust Contingency Plans
Developing robust contingency plans is also critical for mitigating risks and disruptions in logistics operations. These plans should outline clear protocols and procedures for responding to various disruption scenarios, such as natural disasters, cyber-attacks, or labor strikes. Regular training and drills can help ensure that logistics teams are well-prepared to execute contingency plans effectively when disruptions occur.
Leveraging Data Analytics
Leveraging data analytics is another powerful strategy for mitigating risks and disruptions in logistics operations. By analyzing historical data and identifying patterns and trends, logistics managers can gain valuable insights into potential risks and develop proactive mitigation strategies. Additionally, using predictive analytics tools can help forecast demand fluctuations, optimize inventory levels, and improve overall supply chain efficiency.
In conclusion, mitigating risks and disruptions in logistics operations requires a multi-faceted approach that combines advanced technology, diversification, collaboration, flexibility, contingency planning, and data analytics. By implementing these strategies, logistics operations can build resilience, minimize the impact of disruptions, and ensure the smooth flow of goods and services across the supply chain.

Logistics companies often ask freshers a variety of questions during interviews to assess their suitability for the role. Some common questions revolve around the candidate's understanding of logistics and supply chain management concepts. Interviewers may ask about the candidate's knowledge of transportation modes, warehouse management systems, and inventory control techniques. They may also inquire about the candidate's problem-solving skills and ability to work under pressure.
Behavioral Questions
Behavioral questions are another common type of interview question for logistics freshers. These questions aim to evaluate the candidate's past behavior in specific situations to predict their future performance. Examples of behavioral questions include:
Tell me about a time when you had to deal with a difficult customer or client.
Describe a situation where you had to work under tight deadlines.
Give an example of a time when you had to use your problem-solving skills to overcome a challenge.
Situational Questions
Situational questions present hypothetical scenarios to the candidate and ask how they would respond. These questions test the candidate's ability to think on their feet and make sound decisions. Examples of situational questions include:
If a shipment is delayed, how would you communicate with the customer?
What would you do if you noticed a discrepancy in the inventory count?
How would you handle a situation where a team member is not pulling their weight?
Technical Questions
Technical questions assess the candidate's knowledge of logistics-specific tools and technologies. These questions may cover topics such as warehouse management systems, transportation management systems, and enterprise resource planning (ERP) software. Examples of technical questions include:
What experience do you have with warehouse management systems?
How familiar are you with ERP software such as SAP or Oracle?
What are some common transportation management system features?
Tips for Answering Logistics Interview Questions
To successfully answer logistics interview questions, candidates should:
Research the company and the specific role beforehand.
Provide specific examples from past experiences to illustrate their skills and abilities.
Demonstrate a strong understanding of logistics and supply chain management concepts.
Show enthusiasm for the opportunity and a willingness to learn and grow within the company.
Conclusion
Logistics interviews for freshers can be challenging, but with proper preparation, candidates can showcase their skills and potential. By understanding common interview questions and preparing thoughtful responses, freshers can increase their chances of landing a rewarding career in logistics.

Preparing for a logistics interview as a fresher requires a combination of research, practice, and self-reflection. Start by thoroughly researching the company you are interviewing with, including its mission, values, and recent news. This will help you understand the company's culture and demonstrate your interest during the interview. Additionally, familiarize yourself with common logistics terms and concepts, such as supply chain management, inventory control, and transportation modes.
Practice Answering Common Interview Questions
Anticipate potential questions the interviewer may ask and practice your responses. Common questions include discussing your strengths, weaknesses, and how you handle challenges. Provide specific examples from your education or internships that showcase your problem-solving skills, teamwork abilities, and attention to detail. Practice your answers out loud to improve your confidence and delivery.
Highlight Your Relevant Skills and Experiences
Although you may not have direct logistics experience, emphasize transferable skills from your education or extracurricular activities. Discuss projects or coursework that required analytical thinking, organization, and communication skills. If you have any internships or volunteer experiences related to logistics or supply chain management, be sure to highlight those as well.
Prepare Questions for the Interviewer
Demonstrate your interest in the company and the role by preparing thoughtful questions for the interviewer. Ask about the company's logistics processes, challenges they face, and opportunities for growth within the organization. This shows that you have done your research and are genuinely interested in contributing to the company's success.
Showcase Your Enthusiasm and Willingness to Learn
As a fresher, employers understand that you may not have extensive logistics experience. Emphasize your enthusiasm for the field and your eagerness to learn and grow within the company. Discuss your ability to adapt quickly, work well in a team, and take on new challenges. Highlight any relevant coursework or certifications you have completed to show your commitment to professional development.
Review Logistics Case Studies and Industry News
Familiarize yourself with real-world logistics challenges and solutions by reviewing case studies and industry news. This will help you understand the practical applications of logistics concepts and demonstrate your knowledge during the interview. Be prepared to discuss how you would approach similar challenges and offer potential solutions.
Practice Your Communication Skills
Effective communication is crucial in logistics roles. Practice active listening, speaking clearly, and articulating your thoughts concisely. Be prepared to discuss how you would communicate with team members, suppliers, and customers to ensure smooth logistics operations.
Dress Professionally and Arrive Early
Make a positive first impression by dressing professionally for the interview. Arrive at least 10-15 minutes early to allow time for parking and finding the interview location. Bring copies of your resume, a notebook, and a pen to take notes during the interview.
By following these tips and dedicating time to preparation, you can increase your chances of success in a logistics interview as a fresher. Remember to stay confident, showcase your potential, and demonstrate your enthusiasm for the role and the company.

Employers in the logistics industry seek a diverse set of skills and qualities when interviewing freshers for positions. They look for candidates who possess a strong foundation in logistics principles and demonstrate potential for growth. Key skills that employers prioritize include analytical thinking, problem-solving abilities, and proficiency in relevant software applications. Freshers should showcase their ability to analyze data, optimize supply chain processes, and make data-driven decisions.
Communication and Teamwork
Effective communication is crucial in logistics roles, as freshers will often collaborate with cross-functional teams. Employers assess candidates' ability to articulate ideas clearly, listen actively, and maintain open lines of communication. They seek individuals who can work well in a team environment, contributing their skills and expertise to achieve common goals. Freshers should highlight instances where they have successfully worked in teams and communicated effectively.
Adaptability and Resilience
The logistics industry is dynamic and fast-paced, requiring professionals to adapt to changing circumstances. Employers look for freshers who demonstrate flexibility and resilience in the face of challenges. They value individuals who can think on their feet, find creative solutions to problems, and maintain a positive attitude under pressure. Freshers should provide examples of situations where they have successfully navigated change and overcome obstacles.
Attention to Detail and Organization
Logistics operations require meticulous attention to detail to ensure accuracy and efficiency. Employers seek freshers who are detail-oriented and have strong organizational skills. They look for candidates who can manage multiple tasks simultaneously, prioritize effectively, and maintain accurate records. Freshers should emphasize their ability to stay organized, meet deadlines, and deliver high-quality work consistently.
Continuous Learning and Technology Proficiency
The logistics industry is constantly evolving, with new technologies and best practices emerging regularly. Employers value freshers who demonstrate a passion for continuous learning and a willingness to stay updated with industry trends. They seek candidates who are proficient in relevant software applications and can quickly adapt to new technologies. Freshers should showcase their eagerness to learn, highlighting any relevant certifications or training they have undertaken.
Customer Focus and Problem-Solving
Logistics professionals often interact with customers and stakeholders, requiring strong customer service skills. Employers look for freshers who can effectively communicate with customers, understand their needs, and provide solutions to their problems. They value individuals who can think critically, analyze complex situations, and propose innovative solutions. Freshers should provide examples of how they have successfully resolved customer issues or implemented problem-solving strategies.
Leadership Potential and Initiative
While freshers may not have extensive leadership experience, employers look for candidates who demonstrate leadership potential. They seek individuals who take initiative, are proactive in identifying areas for improvement, and can inspire and motivate others. Freshers should highlight instances where they have taken on leadership roles, whether in academic projects, extracurricular activities, or previous internships.
By possessing a combination of technical skills, soft skills, and a growth mindset, freshers can position themselves as attractive candidates in logistics interviews. Employers seek well-rounded individuals who can contribute to the organization's success and adapt to the evolving demands of the industry.

The logistics department faces numerous challenges in today's fast-paced and ever-evolving business environment. One of the most significant challenges is the increasing complexity of supply chain networks. As companies expand their operations globally, managing the flow of goods and information becomes more intricate. This complexity is further compounded by the need to coordinate with multiple stakeholders, including suppliers, manufacturers, distributors, and customers, across different geographical locations and time zones.
Technological Advancements and Integration
Another major challenge is keeping pace with technological advancements and integrating new technologies into existing logistics processes. The rapid development of automation, artificial intelligence, and the Internet of Things (IoT) has the potential to revolutionize logistics operations. However, implementing these technologies requires significant investment, training, and change management. Logistics departments must carefully evaluate the costs and benefits of adopting new technologies while ensuring seamless integration with their current systems and processes.
Balancing Cost and Service Quality
Balancing cost efficiency and service quality is another critical challenge for logistics departments. Customers expect faster, more reliable, and cost-effective delivery options. At the same time, logistics departments must manage rising transportation costs, fuel prices, and labor expenses. Finding the right balance between cost optimization and maintaining high service standards requires careful planning, negotiation with carriers, and continuous process improvement initiatives.
Inventory Management and Visibility
Effective inventory management and real-time visibility are also significant challenges for logistics departments. Ensuring the right products are available in the right quantities and at the right time is crucial for meeting customer demands and avoiding stockouts or overstocking. However, achieving real-time visibility across the entire supply chain can be difficult, especially when dealing with multiple systems, data formats, and communication protocols. Logistics departments must invest in robust inventory management systems and collaborate closely with supply chain partners to improve visibility and responsiveness.
Talent Acquisition and Retention
Finally, attracting and retaining skilled logistics professionals is a growing challenge for many organizations. The logistics industry requires a diverse range of skills, including supply chain management, transportation planning, warehouse operations, and data analytics. However, the talent pool for these skills is often limited, and competition for top talent is fierce. Logistics departments must develop effective recruitment and retention strategies, invest in employee training and development, and create a positive work environment to attract and retain the best logistics professionals.
In conclusion, logistics departments face a multitude of challenges in today's dynamic business landscape. From managing complex supply chain networks and adopting new technologies to balancing cost and service quality, effective inventory management, and talent acquisition, logistics professionals must navigate a range of obstacles to ensure the smooth flow of goods and information. By proactively addressing these challenges and continuously improving their processes and capabilities, logistics departments can enhance their performance, competitiveness, and customer satisfaction.

Our company employs a multi-faceted approach to guarantee prompt and precise delivery of products to our valued customers. We understand that timely and accurate delivery is crucial for maintaining customer satisfaction and loyalty. To achieve this, we have implemented a robust logistics management system that streamlines our supply chain operations.
Advanced Inventory Management
We utilize cutting-edge inventory management software that provides real-time visibility into our stock levels and locations. This allows us to maintain optimal inventory levels and quickly identify any potential shortages or oversupply. By closely monitoring our inventory, we can ensure that products are always available when customers place their orders.
Efficient Order Processing
Our order processing system is designed to be fast, accurate, and reliable. We have automated many aspects of the process, reducing the chances of human error and speeding up order fulfillment. As soon as an order is placed, it is automatically routed to our warehouse for picking, packing, and shipping.
Strategic Warehouse Locations
We have strategically located our warehouses to be close to major transportation hubs and population centers. This proximity allows us to reduce shipping times and costs while ensuring that products reach customers quickly. Our warehouses are equipped with advanced technology and staffed by experienced professionals who efficiently manage the storage and handling of goods.
Reliable Shipping Partners
We partner with reputable and reliable shipping carriers who have a proven track record of delivering products on time. Our shipping partners use advanced tracking systems that provide real-time updates on the status of each shipment. This allows us to monitor the progress of deliveries and quickly address any issues that may arise.
Continuous Performance Monitoring
We continuously monitor our delivery performance using key metrics such as on-time delivery rates, order accuracy, and customer feedback. This data-driven approach allows us to identify areas for improvement and make necessary adjustments to our processes. We strive to exceed customer expectations by consistently delivering products on time and in perfect condition.
Dedicated Customer Support
In the rare event that a delivery issue arises, our dedicated customer support team is ready to assist. We have multiple channels for customers to reach us, including phone, email, and live chat. Our team works diligently to resolve any concerns and ensure that customers are satisfied with their experience.
At our company, we are committed to providing exceptional service and ensuring timely and accurate delivery of goods. Through our advanced logistics management system, strategic warehouse locations, reliable shipping partners, and continuous performance monitoring, we strive to exceed customer expectations and build long-lasting relationships based on trust and reliability.

Effective inventory management and supply chain optimization are crucial for businesses to minimize costs and maximize profits. The company employs a comprehensive approach to streamline its inventory management process and enhance supply chain efficiency. This approach involves several key strategies and technologies that work together to create a lean and agile supply chain.
Inventory Management Techniques
The company uses a combination of inventory management techniques to maintain optimal stock levels and reduce holding costs. These techniques include:
Just-in-Time (JIT) Inventory
The company employs a JIT inventory system, which means that materials and products arrive as needed. This approach reduces the need for large inventory holdings, lowering storage costs and minimizing the risk of obsolescence.
ABC Analysis
The company categorizes its inventory using the ABC analysis method, prioritizing items based on their value and importance. This allows the company to focus its resources on managing high-value items more closely, while simplifying the management of lower-value items.
Supply Chain Optimization Strategies
To optimize its supply chain efficiency, the company implements several strategies that streamline processes and improve collaboration with suppliers and partners. These strategies include:
Supplier Collaboration
The company works closely with its suppliers to ensure timely deliveries, high-quality products, and cost-effective solutions. By fostering strong relationships with suppliers, the company can quickly adapt to changes in demand and minimize supply chain disruptions.
Demand Forecasting
The company uses advanced analytics and machine learning algorithms to forecast demand accurately. This enables the company to plan its inventory and production levels more effectively, reducing the risk of stockouts or overstocking.
Technology Integration
The company integrates various technologies to support its inventory management and supply chain optimization efforts. These include:
Enterprise Resource Planning (ERP) Systems
The company uses an ERP system to centralize data and automate processes across its supply chain. This enables real-time visibility into inventory levels, order status, and financial information, facilitating better decision-making and coordination among departments.
Radio-Frequency Identification (RFID) Technology
The company employs RFID technology to track and monitor inventory movements throughout its supply chain. This provides accurate, real-time data on inventory levels and locations, enabling the company to optimize stock management and quickly identify potential issues.
By implementing these inventory management techniques, supply chain optimization strategies, and technologies, the company can effectively manage its inventory and enhance supply chain efficiency. This leads to reduced costs, improved customer satisfaction, and a competitive edge in the market.

Logistics managers face various challenges in their daily operations, requiring them to develop effective problem-solving strategies. One common challenge is managing inventory levels effectively. Overstock leads to increased storage costs and tied-up capital, while understock results in stockouts and lost sales. To address this issue, logistics managers can implement just-in-time (JIT) inventory management systems, which involve closely coordinating with suppliers to ensure timely deliveries and maintaining optimal stock levels based on demand forecasts.
Enhancing Supply Chain Visibility
Another challenge logistics managers face is the lack of visibility in the supply chain. Without real-time information on the status of shipments, inventory levels, and potential disruptions, making informed decisions becomes difficult. To overcome this, logistics managers can invest in advanced technology solutions such as radio-frequency identification (RFID) tags, GPS tracking, and cloud-based software platforms. These tools provide end-to-end visibility, enabling managers to monitor the entire supply chain, identify bottlenecks, and take proactive measures to mitigate risks.
Optimizing Transportation and Routing
Efficient transportation and routing are crucial for timely deliveries and cost control. Logistics managers must navigate challenges such as fluctuating fuel prices, traffic congestion, and limited carrier capacity. To optimize transportation, managers can leverage transportation management systems (TMS) that utilize algorithms to determine the most cost-effective and efficient routes. Additionally, building strong relationships with reliable carriers and negotiating favorable contracts can help secure competitive rates and ensure consistent service levels.
Managing Supply Chain Disruptions
Supply chain disruptions, such as natural disasters, geopolitical events, or supplier failures, can severely impact logistics operations. To mitigate the effects of disruptions, logistics managers need to develop robust risk management strategies. This involves conducting regular risk assessments, identifying potential vulnerabilities, and creating contingency plans. Building a diversified supplier base, maintaining adequate safety stock, and establishing clear communication channels with all stakeholders are essential steps in managing disruptions effectively.
Ensuring Compliance and Sustainability
Logistics managers must navigate a complex landscape of regulations, trade policies, and sustainability requirements. Non-compliance can result in hefty fines, reputational damage, and operational disruptions. To ensure compliance, managers need to stay up-to-date with the latest regulations, conduct regular audits, and implement strict adherence to industry standards. Additionally, incorporating sustainable practices, such as optimizing fuel consumption, reducing waste, and using eco-friendly packaging, can help meet sustainability goals and enhance the company's brand image.
Continuous Improvement and Innovation
To stay competitive in a dynamic market, logistics managers must foster a culture of continuous improvement and innovation. This involves regularly reviewing processes, identifying inefficiencies, and implementing data-driven solutions. Encouraging cross-functional collaboration, investing in employee training and development, and leveraging emerging technologies can drive operational excellence and create a competitive edge.
In conclusion, logistics managers face a range of challenges that require a proactive and strategic approach to problem-solving. By leveraging technology, optimizing processes, managing risks, ensuring compliance, and driving innovation, logistics managers can overcome these challenges and deliver exceptional value to their organizations.

Optimizing supply chain processes is crucial for businesses to remain competitive and efficient. In my experience, I successfully optimized a supply chain process by employing several strategies. First, I conducted a thorough analysis of the existing process to identify bottlenecks and inefficiencies. This involved gathering data from various sources, including supplier performance metrics, inventory levels, and transportation costs.
Identifying Areas for Improvement
After analyzing the data, I identified several areas for improvement. One major issue was the lack of communication between different departments, leading to delays and errors. Another problem was the inefficient use of warehouse space, resulting in higher storage costs and longer picking times.
Implementing Lean Principles
To address these issues, I implemented lean principles throughout the supply chain process. This included streamlining communication channels between departments, establishing clear performance metrics, and eliminating waste in the form of unnecessary steps and excess inventory.
Collaborating with Suppliers
I also worked closely with suppliers to improve their performance and align their processes with our company's goals. This involved regular meetings to discuss performance, share best practices, and identify opportunities for improvement. By collaborating with suppliers, we were able to reduce lead times, improve quality, and lower costs.
Utilizing Technology
Another key strategy was the implementation of technology to automate and optimize various aspects of the supply chain process. This included the use of warehouse management systems to improve inventory accuracy and reduce picking times, as well as transportation management systems to optimize routes and reduce costs.
Measuring and Monitoring Performance
Throughout the optimization process, I regularly measured and monitored performance using key performance indicators (KPIs). This allowed me to track progress, identify areas for further improvement, and make data-driven decisions. Some of the KPIs I used included on-time delivery, inventory turnover, and cost per unit.
Continuous Improvement
Optimizing a supply chain process is not a one-time event but rather a continuous effort. I encouraged a culture of continuous improvement, where everyone in the organization was encouraged to identify and suggest ways to further optimize the process.
By employing these strategies, I was able to successfully optimize the supply chain process, resulting in significant improvements in efficiency, cost savings, and customer satisfaction. The key to success was a combination of thorough analysis, lean principles, collaboration, technology, and continuous improvement.

Effective communication and collaboration among stakeholders in the logistics process are crucial for achieving optimal results. To ensure this, several strategies can be employed. First, establish clear channels of communication, such as regular meetings, emails, and project management tools. These channels should facilitate the exchange of information, ideas, and concerns among all parties involved.
Defining Roles and Responsibilities
Clearly define the roles and responsibilities of each stakeholder in the logistics process. This helps everyone understand their part in the overall operation and promotes accountability. When roles are well-defined, individuals can focus on their specific tasks and contribute effectively to the team.
Encouraging Open Dialogue
Foster an environment that encourages open dialogue and active listening among stakeholders. Create opportunities for individuals to share their thoughts, ideas, and concerns freely. This promotes a sense of trust and collaboration, as everyone feels heard and valued. Regular feedback sessions can help identify areas for improvement and celebrate successes.
Implementing Collaborative Tools
Utilize collaborative tools and technologies to streamline communication and collaboration. Project management software, shared documents, and instant messaging platforms can help stakeholders stay connected and informed. These tools enable real-time updates, file sharing, and task assignments, ensuring everyone is on the same page.
Conducting Regular Meetings
Schedule regular meetings to discuss progress, challenges, and upcoming tasks. These meetings provide a platform for stakeholders to align their efforts, share insights, and make informed decisions. Prepare agendas in advance to ensure meetings are focused and productive. Encourage participation from all attendees to gather diverse perspectives.
Establishing Communication Protocols
Develop clear communication protocols that outline how information should be shared and when. This includes guidelines for email etiquette, response times, and escalation procedures. Having standardized protocols helps avoid misunderstandings and ensures important information is communicated effectively and efficiently.
Promoting Cross-Functional Collaboration
Encourage collaboration across different functions and departments involved in the logistics process. Break down silos and promote a culture of teamwork. Organize cross-functional meetings, workshops, and brainstorming sessions to foster innovation and problem-solving. When stakeholders from various areas work together, they can identify opportunities for improvement and optimize the overall logistics operation.
Providing Training and Support
Invest in training and support programs to enhance the communication and collaboration skills of stakeholders. Offer workshops on effective communication, active listening, and conflict resolution. Provide resources and guidance on using collaborative tools and technologies. By equipping stakeholders with the necessary skills and knowledge, you enable them to communicate and collaborate more effectively.
In conclusion, ensuring effective communication and collaboration among stakeholders in the logistics process requires a multi-faceted approach. By establishing clear channels, defining roles, encouraging open dialogue, implementing collaborative tools, conducting regular meetings, establishing protocols, promoting cross-functional collaboration, and providing training and support, organizations can create a cohesive and efficient logistics operation that delivers exceptional results.

When interviewing for a Logistics Assistant position, candidates can expect to encounter various questions that assess their relevant skills and experience. Employers often inquire about the applicant's familiarity with supply chain management, inventory control, and transportation planning. They may also ask about the candidate's ability to work in a fast-paced environment and handle multiple tasks simultaneously. Additionally, interviewers might pose situational questions to gauge the applicant's problem-solving skills and adaptability in handling potential challenges that may arise in the role.
Understanding of Logistics Processes
Interviewers will likely ask candidates to demonstrate their knowledge of key logistics processes. They may inquire about the applicant's experience with inventory management systems, such as warehouse management software (WMS) or enterprise resource planning (ERP) tools. Candidates should be prepared to discuss their proficiency in tracking inventory levels, processing orders, and managing stock replenishment. Furthermore, employers may ask about the applicant's understanding of transportation logistics, including route planning, carrier selection, and shipment tracking.
Attention to Detail and Organizational Skills
Logistics Assistants must possess strong attention to detail and organizational skills to ensure the smooth flow of goods. Interviewers may ask candidates to provide examples of how they have demonstrated these skills in previous roles. This could include discussing their experience in maintaining accurate records, preparing shipping documents, or coordinating with various stakeholders to ensure timely deliveries. Candidates should emphasize their ability to prioritize tasks, meet deadlines, and maintain a high level of accuracy in their work.
Communication and Collaboration
Effective communication and collaboration are essential for success in a Logistics Assistant role. Interviewers may ask candidates about their experience working with cross-functional teams, such as purchasing, production, and customer service departments. They may also inquire about the applicant's ability to communicate with external partners, such as suppliers and carriers. Candidates should highlight their strong verbal and written communication skills, as well as their ability to build and maintain positive relationships with colleagues and stakeholders.
Problem-Solving and Adaptability
Logistics Assistants often face challenges that require quick thinking and problem-solving skills. Interviewers may present hypothetical scenarios and ask candidates how they would address specific issues, such as delayed shipments or inventory discrepancies. Candidates should demonstrate their ability to analyze problems, identify root causes, and propose effective solutions. Additionally, employers may inquire about the applicant's adaptability and willingness to learn new processes or technologies to improve logistics operations.
Customer Service Orientation
Logistics Assistants play a crucial role in ensuring customer satisfaction by facilitating the timely and accurate delivery of goods. Interviewers may ask candidates about their experience in handling customer inquiries and resolving issues related to orders or shipments. They may also inquire about the applicant's approach to managing customer expectations and maintaining positive relationships. Candidates should emphasize their commitment to providing excellent customer service and their ability to communicate effectively with both internal and external stakeholders.
By preparing for these common interview questions, candidates can effectively showcase their skills and experience relevant to a Logistics Assistant position. Demonstrating a strong understanding of logistics processes, attention to detail, communication skills, problem-solving abilities, and customer service orientation will help applicants stand out during the interview process and increase their chances of securing the role.

To prepare for a Logistics Assistant interview, you should focus on several key areas. First, research the company thoroughly. Understand its mission, values, and the specific role you are applying for. This knowledge will help you align your answers with the company's goals and demonstrate your enthusiasm for the position.
Review Common Interview Questions
Next, review common interview questions and practice your responses. Some questions you may encounter include:
What experience do you have in logistics?
How do you handle stress and pressure in a fast-paced work environment?
Describe a time when you had to solve a complex problem at work.
Practice answering these questions concisely and with specific examples from your experience.
Highlight Your Relevant Skills
Highlight your relevant skills and experiences during the interview. Logistics Assistants often need strong organizational, communication, and problem-solving skills. Think of examples from your past that demonstrate these abilities and be ready to discuss them.
Organizational Skills
Discuss how you have successfully managed inventory, tracked shipments, or optimized warehouse space in previous roles.
Communication Skills
Describe instances where you communicated effectively with colleagues, suppliers, or customers to resolve issues or improve processes.
Problem-Solving Skills
Share examples of how you identified and solved problems in a logistics setting, such as reducing shipping costs or improving delivery times.
Familiarize Yourself with Industry Terms and Technologies
Familiarize yourself with industry-specific terms and technologies. Logistics Assistants often work with various software systems, such as warehouse management systems (WMS) or transportation management systems (TMS). Knowing these terms and technologies will show the interviewer that you are well-prepared and knowledgeable about the field.
Prepare Questions for the Interviewer
Prepare questions for the interviewer to demonstrate your interest in the role and the company. Ask about the company's logistics processes, the challenges they face, and opportunities for growth within the organization.
Dress Professionally and Arrive Early
Finally, dress professionally and arrive at the interview location early. This shows respect for the interviewer's time and allows you to gather your thoughts before the interview begins.
By following these steps, you will be well-prepared for your Logistics Assistant interview and increase your chances of success.

Finding sample answers to Logistics Assistant interview questions in PDF format is possible through various online resources. Websites such as JobTestPrep, InterviewPenguin, and Glassdoor offer comprehensive guides and sample answers to assist job seekers. These resources provide a wide range of questions and answers that cover different aspects of the role. Additionally, industry-specific websites and forums can also be valuable sources of information for aspiring Logistics Assistants.
Online Job Resources
Online job resources are excellent places to start your search for sample answers to Logistics Assistant interview questions. These websites often have dedicated sections for interview preparation, including sample questions and answers. They cover a broad spectrum of industries and job roles, making them suitable for various job seekers. The information provided is usually well-structured and easy to navigate, allowing users to find relevant content quickly.
JobTestPrep
JobTestPrep is a popular online resource that offers comprehensive interview preparation materials for numerous job roles. Their Logistics Assistant interview guide includes sample questions and answers in PDF format. The questions cover topics such as inventory management, supply chain optimization, and problem-solving skills. JobTestPrep's materials are designed to help candidates familiarize themselves with the types of questions they may encounter during the interview process.
InterviewPenguin
InterviewPenguin is another valuable online resource for job seekers preparing for Logistics Assistant interviews. Their website provides a PDF guide that contains sample questions and answers specific to the role. The guide covers a range of topics, including the candidate's experience, technical skills, and ability to work in a team. InterviewPenguin's materials are well-organized and provide clear explanations, making them easy to understand and apply.
Glassdoor
Glassdoor is a well-known website that offers company reviews, salary information, and interview preparation resources. Their interview section includes sample questions and answers for various job roles, including Logistics Assistants. The questions are often sourced from real interviews, providing candidates with valuable insights into the hiring process. Glassdoor's community-driven approach ensures that the information provided is up-to-date and relevant to current job market trends.
Industry-Specific Websites and Forums
In addition to general job resources, industry-specific websites and forums can be excellent sources of information for Logistics Assistant interview preparation. These platforms often have dedicated sections where professionals share their experiences, tips, and sample questions and answers. By engaging with these communities, aspiring Logistics Assistants can gain valuable insights into the role and learn from the experiences of others in the field.
Supply Chain Management Review
Supply Chain Management Review is an industry-specific website that provides news, articles, and resources related to supply chain management. Their website includes a section dedicated to career development, which may contain sample interview questions and answers for Logistics Assistants. The information provided is often written by industry experts, ensuring its reliability and relevance to the field.
Logistics and Supply Chain Management Forum
The Logistics and Supply Chain Management Forum is an online community where professionals in the field can share their experiences, ask questions, and engage in discussions. The forum may have threads dedicated to interview preparation, where members share sample questions and answers specific to Logistics Assistant roles. By participating in these discussions, aspiring Logistics Assistants can learn from the experiences of seasoned professionals and gain valuable insights into the interview process.

Logistics specialists play a crucial role in ensuring the smooth flow of goods and services within an organization. To excel in this field, individuals must possess a diverse set of skills that enable them to effectively manage supply chains, coordinate transportation, and optimize inventory levels. Among the most critical skills for a logistics specialist are strong analytical abilities, excellent communication skills, and a keen attention to detail.
Analytical Skills
Logistics specialists must be able to analyze vast amounts of data to make informed decisions. They should be proficient in using various software tools to track inventory levels, monitor shipments, and identify potential bottlenecks in the supply chain. Strong analytical skills enable logistics specialists to optimize routes, reduce costs, and improve overall efficiency.
Data Analysis
Logistics specialists should be comfortable working with numbers and interpreting complex data sets. They must be able to use statistical analysis to identify trends, forecast demand, and make data-driven decisions.
Problem-Solving
The ability to think critically and solve problems is essential for logistics specialists. They must be able to quickly identify issues and develop effective solutions to minimize disruptions and ensure the smooth flow of goods.
Communication Skills
Effective communication is vital for logistics specialists, as they often collaborate with various stakeholders, including suppliers, carriers, and customers. They must be able to clearly convey information, negotiate contracts, and build strong relationships with partners.
Written Communication
Logistics specialists should have excellent written communication skills to create detailed reports, write clear emails, and document processes and procedures.
Verbal Communication
Strong verbal communication skills are essential for logistics specialists, as they often need to communicate with team members, vendors, and clients over the phone or in person.
Attention to Detail
Logistics specialists must have a keen eye for detail to ensure accuracy in all aspects of their work. They should be meticulous in tracking inventory, monitoring shipments, and maintaining accurate records.
Accuracy
Attention to detail is crucial for logistics specialists to avoid costly errors, such as incorrect shipments or inaccurate inventory counts.
Organization
Logistics specialists must be highly organized to manage multiple tasks and priorities simultaneously. They should be able to create and maintain efficient systems for tracking inventory, managing schedules, and documenting processes.
Other Important Skills
In addition to analytical, communication, and detail-oriented skills, logistics specialists should also possess:
Time Management
Logistics specialists must be able to manage their time effectively to meet deadlines and ensure timely delivery of goods.
Adaptability
The logistics industry is constantly evolving, and specialists must be able to adapt to new technologies, processes, and regulations.
Leadership
Logistics specialists often lead teams and projects, so strong leadership skills are valuable for motivating and guiding others towards common goals.
In conclusion, the most important skills for a logistics specialist to possess are strong analytical abilities, excellent communication skills, and a keen attention to detail. By mastering these skills and continuously developing their knowledge of the industry, logistics specialists can excel in their roles and contribute to the success of their organizations.

Handling unexpected delays or disruptions in the supply chain requires a proactive and adaptable approach. Companies must develop contingency plans to mitigate the impact of unforeseen events. This involves identifying potential risks, such as natural disasters, labor strikes, or supplier failures, and creating strategies to address them.
Diversifying Supplier Base
One effective strategy is to diversify the supplier base. By sourcing materials and components from multiple suppliers in different locations, companies can reduce their dependency on a single supplier. If one supplier experiences a disruption, the company can quickly shift production to another supplier, minimizing the impact on the supply chain.
Building Strong Relationships with Suppliers
Building strong relationships with suppliers is crucial for managing unexpected delays. Regular communication and collaboration with suppliers can help identify potential issues early on. This allows companies to work together to find solutions and implement corrective actions before the disruption escalates.
Implementing Technology Solutions
Technology plays a vital role in managing supply chain disruptions. Implementing real-time visibility tools, such as GPS tracking and IoT sensors, enables companies to monitor the movement of goods and identify delays promptly. This real-time data allows for quick decision-making and the ability to reroute shipments or adjust production schedules as needed.
Leveraging Data Analytics
Data analytics can help predict and prevent supply chain disruptions. By analyzing historical data, companies can identify patterns and trends that may indicate potential issues. This predictive analysis allows companies to take proactive measures, such as increasing inventory levels or securing alternative suppliers, to mitigate the impact of disruptions.
Developing Flexible Logistics Networks
Creating a flexible logistics network is essential for handling unexpected delays. This involves having multiple transportation options, such as air, sea, and land, to quickly adapt to disruptions. Companies should also consider establishing strategic warehousing locations to store inventory closer to customers, reducing the impact of transportation delays.
Collaborating with Supply Chain Partners
Collaboration with supply chain partners, including suppliers, logistics providers, and customers, is key to managing disruptions effectively. Sharing information, such as demand forecasts and inventory levels, can help all parties make informed decisions and adjust their operations accordingly. Regular meetings and open lines of communication foster trust and enable quick problem-solving.
Continuously Improving Supply Chain Resilience
Handling unexpected delays requires a continuous improvement mindset. Companies should regularly review and update their contingency plans based on new risks and lessons learned from previous disruptions. Investing in employee training and development helps create a knowledgeable and adaptable workforce that can respond effectively to supply chain challenges.
In conclusion, handling unexpected delays or disruptions in the supply chain requires a multifaceted approach. By diversifying suppliers, building strong relationships, leveraging technology, developing flexible logistics networks, collaborating with partners, and continuously improving resilience, companies can minimize the impact of disruptions and ensure the smooth flow of goods to customers.

Optimizing logistics processes is crucial for efficient supply chain management. One notable example of successful optimization involved streamlining warehouse operations for an e-commerce company. The goal was to reduce order processing time and minimize errors.
Analyzing the Current Process
The first step was to analyze the existing process and identify bottlenecks. This involved mapping out the entire workflow, from receiving orders to shipping packages. Data was collected on processing times, error rates, and resource utilization. This analysis revealed several inefficiencies, such as redundant steps and uneven workload distribution.
Implementing Lean Principles
To address these issues, lean principles were applied. This included eliminating unnecessary steps and reducing waste. The warehouse layout was reorganized to minimize travel time and improve flow. Work stations were standardized to ensure consistency and reduce errors. Visual management tools, such as color-coded labels and signs, were implemented to improve communication and clarity.
Automation and Technology
Automation and technology played a key role in the optimization process. A warehouse management system (WMS) was implemented to track inventory and orders in real-time. This reduced manual data entry and improved accuracy. Barcode scanning and RFID technology were used to speed up order picking and reduce errors. Conveyor systems and sorting machines were installed to streamline the packing and shipping process.
Training and Continuous Improvement
Employee training was also a critical component of the optimization effort. Workers were trained on the new processes and technologies. They were encouraged to provide feedback and suggestions for further improvement. A continuous improvement culture was fostered, with regular meetings to discuss performance metrics and identify areas for enhancement.
Results and Benefits
The optimization project yielded significant results. Order processing time was reduced by 30%, and error rates dropped by 50%. Employee productivity increased, and customer satisfaction improved due to faster and more accurate order fulfillment. The company was able to handle higher order volumes without increasing staff or space. This led to cost savings and increased profitability.
Key Takeaways
Analyze current processes to identify inefficiencies and bottlenecks
Apply lean principles to eliminate waste and streamline workflows
Leverage automation and technology to improve accuracy and speed
Invest in employee training and foster a continuous improvement culture
Monitor performance metrics and adapt as needed to ensure ongoing success
Conclusion
Optimizing logistics processes requires a holistic approach that addresses people, processes, and technology. By analyzing current workflows, implementing lean principles, leveraging automation, and investing in training, companies can significantly improve their supply chain efficiency. The success of this optimization project demonstrates the potential for substantial improvements in order processing time, accuracy, and overall profitability.

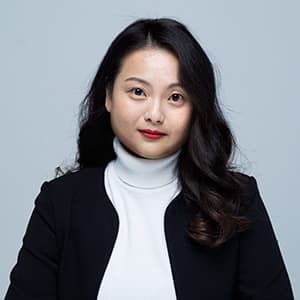
Yu Payne is an American professional who believes in personal growth. After studying The Art & Science of Transformational from Erickson College, she continuously seeks out new trainings to improve herself. She has been producing content for the IIENSTITU Blog since 2021. Her work has been featured on various platforms, including but not limited to: ThriveGlobal, TinyBuddha, and Addicted2Success. Yu aspires to help others reach their full potential and live their best lives.