Interview Question: Metrics for Logistics Success

I still remember the first time I walked into a bustling warehouse as a young logistics coordinator. The hum of forklifts, the beeping of scanners, and the organized chaos of pallets being shuffled around—it was both overwhelming and exhilarating. Back then, I thought logistics was all about moving goods from point A to point B. Little did I know, the true heartbeat of logistics lies in the metrics that drive it.
Category | Metric | Significance |
---|---|---|
Transportation | On-time delivery rates | This metric measures punctuality which greatly impacts customer satisfaction. |
Transportation | Freight cost per unit shipped | This metric measures cost efficiency within transportation logistics. |
Warehousing | Order picking accuracy | This metric can prevent returns and unnecessary re-stocking by minimizing errors. |
Warehousing | Inventory carrying costs | This metric helps in optimizing storage utilization. |
Inventory | Days Sales of Inventory (DSI) | This indicates how long a product sits in inventory and aids in managing inventory turnover. |
Inventory | Stockouts | Preventing stockouts ensures continuity of operations and customer satisfaction. |
Service Quality | Order accuracy | It impacts customer satisfaction and potential future business opportunities. |
Service Quality | Completeness | Ensures that orders are fully filled and delivered as per customer expectations. |
Service Quality | Condition upon arrival | Ensures that products are delivered in optimal condition, therefore resulting in higher customer satisfaction. |
General | Interdependency of metrics | Highlighting the interrelation of different metrics can provide a comprehensive understanding of operational efficiency. |
Unpacking the Question: "What Are the Metrics for Logistics Success?"
When you're sitting across from an interviewer and they ask, "What are the metrics for logistics success?" it's not just a test of your ability to list off key performance indicators (KPIs). They're delving deeper, trying to gauge your understanding of the intricate web that logistics weaves within the supply chain. They're curious about whether you can identify the pivotal factors that not only measure success but also drive strategic decisions.
How To Answer What Time Management Technique Starts Your Day İnterview Question
Personal Time Management Habit That Changed Work Life İnterview Question
How To Answer İnterview Question About Managing Logistics Stress
Why Do Interviewers Ask This Question?
From my experience in human resources, I've found that this question serves multiple purposes. Interviewers are assessing your analytical skills, your grasp of the industry's complexities, and your ability to apply theoretical knowledge to real-world scenarios. They're looking for candidates who can:
1- Recognize essential KPIs in logistics and supply chain management.
2- Understand how these metrics interrelate and impact overall performance.
3- Demonstrate strategic thinking by translating data into actionable insights.
In essence, they want to know if you can look beyond the numbers and see the story they tell.
At What Interview Level Is This Question Asked?
This question typically surfaces during interviews for mid to senior-level positions in logistics, supply chain, or operations management. At these levels, you're expected to have a deep understanding of how different components of the supply chain interact. Whether you're aiming to be a logistics manager or a supply chain director, your ability to optimize processes and drive efficiency is under scrutiny.
What Kind of Answer Is Expected?
An interviewer isn't just looking for a laundry list of metrics. They want an answer that:
Shows depth of knowledge: You should be able to discuss a variety of metrics and explain their significance.
Transportation: "Efficient transportation is crucial for logistics success. Key metrics include on-time delivery rates which impacts customer satisfaction, and freight cost per unit shipped, a measure of cost efficiency."
Warehousing: "Warehouse efficiency greatly affects logistic success. Consider metrics like order picking accuracy (to minimize returns and re-stocking), and inventory carrying costs (to optimize storage utilization)."
Inventory: "Inventory effectiveness can be gauged using metrics such as days sales of inventory (DSI) which measures how long a product sits in inventory, and stockouts to prevent running out of items."
Service Quality: "The quality of logistic services hugely impacts customer satisfaction and retention rates. Track metrics like order accuracy, completeness, and condition upon arrival."
Provides practical examples: Illustrate how you've used these metrics in past experiences.
Demonstrates strategic insight: Explain how these metrics can influence decision-making and overall strategy.
Diving into Key Metrics: From Transportation to Service Quality
Over the years, I've come to appreciate that logistics success isn't measured by a single metric. Instead, it's a tapestry of various indicators woven together. Let's explore some of the critical metrics across different areas of logistics.
1. Transportation Metrics
Transportation is the lifeblood of logistics. Without efficient transport, even the best products can't reach customers in time.
KPI | Description | Measurement |
---|---|---|
On-time delivery | Percentage of shipments delivered on time | Percentage |
Average transit time | Average time taken for a shipment to reach its destination | Days |
Cost per mile | Average cost of transporting goods per mile | Dollars |
Fuel efficiency | Miles driven per gallon of fuel consumed | Miles per gallon |
Load utilization | Percentage of total available capacity utilized | Percentage |
Accident rate | Number of accidents per million miles driven | Accidents per million miles |
On-Time Delivery Rate: This measures the percentage of deliveries made on schedule. In one of my previous roles, we managed to increase our on-time delivery rate from 85% to 95% within a year by optimizing our routing schedules. This not only boosted customer satisfaction but also enhanced our reputation in the market.
Strategy | Description | Expected Outcome |
---|---|---|
Inventory optimization | Reducing excess or obsolete inventory levels, improving forecasting accuracy | Reduced carrying costs, minimized stock-outs |
Supplier consolidation | Reducing the number of suppliers by choosing strategic partners | Leveraging economies of scale, negotiating better terms |
Route optimization | Analyzing and optimizing delivery routes to minimize distance and fuel consumption | Reduced fuel and transportation costs, improved delivery times |
Warehouse process optimization | Streamlining warehouse operations to reduce handling, improve space utilization | Decreased labor costs, increased storage capacity |
Technology adoption | Implementing advanced logistics management systems and software | Increased efficiency, improved visibility and control |
Collaborative planning with partners | Working closely with suppliers, customers, and other stakeholders for shared planning and cost optimization | Streamlined processes, reduced lead times, cost-sharing benefits |
On-Time Delivery Rate | Customer Satisfaction | Impact |
---|---|---|
High | High | Positive |
Medium | Medium | Neutral |
Low | Low | Negative |
High | Medium | Positive |
Medium | Low | Negative |
Low | High | Negative |
What are the indicators of successful logistics performance?
How can we measure the success of logistics operations?
What kind of metrics are typically used to gauge the effectiveness of logistics?
Can you list the metrics that indicate a successful logistics operation?
Which metrics can illustrate the effectiveness of logistics management?
What characteristics or metrics define a successful logistics system?
What performance metrics should be tracked in logistics for effective functioning?
What measurements can show the efficiency and success of logistics processes?
What metrics are critical in evaluating the success of our logistics strategies?
If I want to determine the achievements of my logistics operations, which metrics should I analyze?

Freight Cost per Unit Shipped: This metric evaluates the cost efficiency of shipping operations. By negotiating better rates with carriers and consolidating shipments, we reduced our freight cost per unit by 10%, leading to significant savings.
2. Warehousing Metrics
The warehouse is more than just a storage space; it's a dynamic environment where efficiency can significantly impact the bottom line.
Order Picking Accuracy: This measures how often orders are picked correctly. An error here means returns, re-stocking, and unhappy customers. I recall implementing a barcode scanning system that improved our order picking accuracy from 92% to 99%, drastically reducing errors.
Inventory Carrying Costs: This includes all expenses related to storing inventory, such as warehousing costs, insurance, and obsolescence. By adopting a just-in-time inventory approach, we cut our carrying costs by 15%, freeing up capital for other investments.
3. Inventory Metrics
An effective inventory management system ensures that you have the right products at the right time.
Days Sales of Inventory (DSI): This indicates how long inventory sits before being sold. A lower DSI means faster turnover. In one project, we analyzed our product demand patterns and adjusted our stocking levels, reducing our DSI from 60 days to 45 days.
Stockout Rate: This measures how often products are unavailable when customers want to buy them. We tackled high stockout rates by implementing better forecasting models, which led to an increase in sales and customer trust.
4. Service Quality Metrics
At the end of the day, customer satisfaction is paramount.
Order Accuracy: Ensuring that customers receive exactly what they ordered. Mistakes here can erode trust.
Return Rate: A high return rate can signal product issues or mismatches in customer expectations. By analyzing return reasons, we improved product descriptions and quality checks, reducing our return rate by 8%.
Bringing It All Together: Demonstrating Comprehensive Understanding
When addressing this question in an interview, it's essential to highlight how these metrics are interconnected. For instance, improving transportation efficiency can lead to better on-time delivery rates, which enhances customer satisfaction reflected in service quality metrics.
Real-Life Scenario
Let me share a story. During a supply chain revamp at my previous company, we noticed that although our on-time delivery rate was high, customer satisfaction scores were declining. Upon digging deeper, we found that our order accuracy was slipping. Orders were arriving on time but with incorrect items.
By retraining our warehouse staff and implementing double-checking procedures, we improved order accuracy by 6%. This, in turn, boosted our customer satisfaction ratings. This experience taught me that focusing on one metric without considering others can lead to blind spots.
Tips for Optimizing Supply Chain Management Processes
Understanding metrics is one thing, but knowing how to use them to optimize supply chain management processes is another. Here are some tips drawn from my experiences:
1- Implement Regular Audits: Regularly review your processes to identify inefficiencies.
2- Leverage Technology: Use software solutions for better visibility and data analysis.
3- Collaborate with Partners: Work closely with suppliers and carriers for seamless operations.
4- Invest in Training: Equip your team with the skills they need to excel.
5- Focus on Customer Feedback: Use feedback to drive improvements in service quality.
Conclusion
Answering the question, "What are the metrics for logistics success?" is about more than listing KPIs. It's about demonstrating a holistic understanding of how these metrics interact and impact the entire supply chain. By sharing practical examples and showing strategic insight, you not only answer the question but also showcase your value as a potential asset to the organization.
References
Christopher, M. (2016). Logistics & Supply Chain Management. Pearson Education.
Chopra, S., & Meindl, P. (2013). Supply Chain Management: Strategy, Planning, and Operation. Pearson.
Mentzer, J.T. (2001). Supply Chain Management. Sage Publications.
Similar Interview Questions to Consider
What are the indicators of successful logistics performance?
How can we measure the success of logistics operations?
What kind of metrics are typically used to gauge the effectiveness of logistics?
Can you list the metrics that indicate a successful logistics operation?
Which metrics can illustrate the effectiveness of logistics management?
What characteristics or metrics define a successful logistics system?
What performance metrics should be tracked in logistics for effective functioning?
What measurements can show the efficiency and success of logistics processes?
What metrics are critical in evaluating the success of our logistics strategies?
If I want to determine the achievements of my logistics operations, which metrics should I analyze?
By preparing for these questions and understanding the metrics deeply, you'll be well-equipped to impress your interviewer and take your career in logistics to new heights. Remember, logistics isn't just about moving goods; it's about moving the right goods, at the right time, to the right place, and doing so efficiently and effectively.
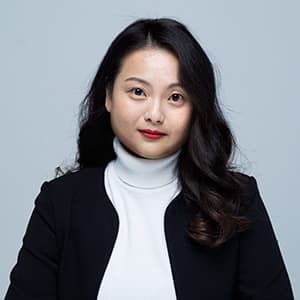
Yu Payne is an American professional who believes in personal growth. After studying The Art & Science of Transformational from Erickson College, she continuously seeks out new trainings to improve herself. She has been producing content for the IIENSTITU Blog since 2021. Her work has been featured on various platforms, including but not limited to: ThriveGlobal, TinyBuddha, and Addicted2Success. Yu aspires to help others reach their full potential and live their best lives.