Interview Question: JIT vs. Safety Stock in Supply Chain Approach

I still remember my early days working in the bustling world of supply chain management. It was my first big project, and I was eager to make a meaningful impact. One afternoon, as I sipped my coffee, my mentor leaned over and asked, "Have you ever heard of Just-In-Time and Safety Stock?" I blinked, realizing that while I had come across these terms in textbooks, I hadn't fully grasped their real-world applications. That conversation ignited a journey of discovery into the intricacies of inventory management, a journey I'd like to share with you.
Inventory Management Approach | Definition | Key Considerations |
---|---|---|
Just-In-Time (JIT) | An inventory strategy that aims to improve a business's return on investment by reducing in-process inventory and its associated carrying costs. | Requires a stable and predictable production process. Any disruption can cause significant issues due to the absence of back-up stock. |
Safety Stock | An inventory strategy that acts as a buffer to guard against uncertainties in supply and demand, allowing a business to avoid shortages and keep the production process running smoothly. | This approach demands high maintenance and offers cushioning against uncertainties, hence, a higher risk tolerance is required. |
Comparison of Risk Factors | The degree of risk involved in JIT and Safety Stock inventory strategies | While JIT is less tolerant to risk due to lack of back-up stock, Safety Stock involves higher risk tolerance due to the demands of high maintenance. |
Cost Implication | Financial considerations of each strategy | JIT strategy aims to reduce costs by minimizing waste, while Safety Stock involves greater financial investment as it acts as a buffer stock. |
Efficiency and Effectiveness | A measure of how well each inventory strategy performs | JIT is seen as an efficient strategy due to reduced overheads, while Safety Stock can be an effective strategy when dealing with demand uncertainty. |
Customer Service Objectives | How each strategy meets customer expectations | While JIT can risk late deliveries due to production issues, Safety Stock ensures availability of goods to meet customer needs. |
Supply Chain Characteristics | The unique features of a company's supply chain which can influence choice of strategy | Companies with a stable supply chain can benefit from JIT while those facing fluctuations in demands or supply might opt for Safety Stock. |
Company Tolerance for Risk | The company’s approach towards prospective risk | Companies with lower risk tolerance tend to opt for Safety Stock while those that can bear potential risks usually prefer JIT approach. |
Strategic Planning | The long-term goals of the company regarding inventory management | Whether the business plans for a lean manufacturing approach (JIT) or a more flexible one (Safety Stock), depends on the business’s strategic goals. |
Practical Implications | The real-life uses and applications of each strategy | Companies need to gauge their supply-demand patterns, risk tolerance, financial constraints before implementing either JIT or Safety Stock approach. |
Understanding the Essentials of Inventory Management
Before diving into the depths of Just-In-Time (JIT) and Safety Stock, it's essential to appreciate the pivotal role inventory management plays in the supply chain. Effective inventory management ensures that products are available when customers need them, without incurring unnecessary costs from overstocking. It's a delicate balancing act, one that can make or break a company's operational efficiency.
The Dance of Demand and Supply
In the dynamic dance between demand and supply, businesses strive to:
Smart Supply Chain Management Estimating Demand Optimization Strategies
How To Answer What's Your Top Problem-solving Method İnterview Question
Meet customer expectations promptly.
Minimize holding costs associated with excess inventory.
Avoid stockouts that can lead to lost sales and dissatisfied customers.
Optimize processes to enhance overall efficiency.
Achieving these goals requires a strategic approach to managing inventory, which brings us to the two prominent methodologies: Just-In-Time and Safety Stock.
Just-In-Time (JIT): A Symphony of Timeliness
Just-In-Time is more than just a strategy; it's a philosophy that revolutionized manufacturing and supply chain processes. Originating from Japan's Toyota Production System in the 1970s, JIT emphasizes producing and delivering goods exactly when they are needed, no sooner, no later.
The Core Principles of JIT
1- Elimination of Waste: JIT seeks to remove any non-value-adding activities, streamlining processes to enhance efficiency.
2- Continuous Improvement: It encourages ongoing evaluation and refinement of processes.
3- Integrated Systems: Collaboration across departments and suppliers ensures seamless operations.
4- Quality Management: Emphasizing high-quality production reduces defects and associated costs.
Advantages of JIT
Reduced Inventory Costs: By minimizing inventory levels, companies can significantly cut down on storage and handling expenses.
Improved Cash Flow: Less capital is tied up in stock, freeing resources for other investments.
Enhanced Supplier Relationships: JIT requires close coordination with suppliers, fostering stronger partnerships.
Greater Responsiveness: Companies can quickly adapt to changes in demand without the burden of excess stock.
I recall a project where we implemented JIT for a client producing electronic components. The results were astounding: inventory holding costs dropped by 35%, and the efficiency of the production line improved markedly. The synchronization of supply with production demand was like watching a well-rehearsed orchestra perform—every part played in harmony.
Challenges of Implementing JIT
However, JIT isn't without its challenges:
Supplier Reliability: Delays from suppliers can halt production.
Lack of Buffer: With minimal inventory, there's little room for error.
Demand Fluctuations: Sudden spikes in demand can be difficult to meet promptly.
Safety Stock: The Guardian Buffer
In contrast to JIT's lean approach, Safety Stock acts as a cushion against uncertainty. It's the extra inventory kept on hand to mitigate risks associated with supply chain disruptions and unpredictable demand.
The Rationale Behind Safety Stock
Unpredictable Demand: Even with forecasts, demand can vary due to market trends, seasonal factors, or unforeseen events.
Supply Chain Disruptions: Delays from suppliers, transportation issues, or production hiccups can lead to stockouts.
Lead Time Variability: Differences between expected and actual lead times necessitate a buffer.
Benefits of Safety Stock
Risk Factors | JIT Approach | Safety Stock Approach |
---|---|---|
Inventory holding costs | Low | High |
Stockout risk | High | Low |
Lead time variability | High | Low |
Supplier reliability | High | Low |
Customer demand variability | High | Low |
Production capacity | Low | High |
Protection Against Stockouts: Ensures products are available, maintaining customer satisfaction.
Method | Cost Implications | Advantages/Disadvantages |
---|---|---|
JIT | Lower inventory carrying costs as there is no need for safety stock | Reduced storage space requirements, reduced risk of stock obsolescence, lower holding costs. However, there is a higher risk of stockouts leading to potential lost sales. |
Safety Stock | Higher inventory carrying costs due to the need for extra stock to mitigate uncertainty | Reduced risk of stockouts and potential lost sales. However, higher holding costs, increased storage space requirements, and increased risk of stock obsolescence. |
JIT | Lower inventory carrying costs as there is no need for safety stock | Reduced storage space requirements, reduced risk of stock obsolescence, lower holding costs. However, there is a higher risk of stockouts leading to potential lost sales. |
Safety Stock | Higher inventory carrying costs due to the need for extra stock to mitigate uncertainty | Reduced risk of stockouts and potential lost sales. However, higher holding costs, increased storage space requirements, and increased risk of stock obsolescence. |
JIT | Lower inventory carrying costs as there is no need for safety stock | Reduced storage space requirements, reduced risk of stock obsolescence, lower holding costs. However, there is a higher risk of stockouts leading to potential lost sales. |
Safety Stock | Higher inventory carrying costs due to the need for extra stock to mitigate uncertainty | Reduced risk of stockouts and potential lost sales. However, higher holding costs, increased storage space requirements, and increased risk of stock obsolescence. |
Stabilizes Production: Aids in smoothing out the production schedule despite fluctuations.
Approach | Efficiency | Effectiveness |
---|---|---|
JIT | Reduces inventory holding costs | Minimizes waste and lead time |
JIT | Improves cash flow | Promotes continuous improvement |
Safety Stock | Ensures product availability | Reduces the risk of stockouts |
Safety Stock | Provides a buffer against demand variability | Enhances customer service level |
Both Approaches | Require accurate demand forecasting | Can enhance supply chain responsiveness |
Both Approaches | Can result in higher coordination and communication requirements | Demand fluctuations can lead to imbalances |
Risk Mitigation: Acts as a safeguard against external uncertainties.
Can you compare and contrast the JIT and Safety Stock strategies in a supply chain approach?
How does JIT differ from Safety Stock in managing a supply chain?
Could you explain the difference between the JIT and safety stock in a supply chain approach?
What distinguishes JIT from Safety Stock in their approach to supply chain management?
Could you provide insights into the pros and cons of JIT and Safety Stock in the handling of supply chains?
In the context of supply chain strategy, can you outline the key differences between JIT and Safety Stock?
Is there an advantage of JIT over Safety Stock in supply chain management or vice versa?
How do the approaches of JIT and Safety Stock compare when faced with supply chain demands?
When it comes to a supply chain approach, how do you differentiate between JIT and Safety Stock?
Can you provide a comparative study on JIT and Safety Stock strategies in managing a supply chain?

On one occasion, a sudden snowstorm disrupted our supply routes. Thanks to the Safety Stock we had diligently maintained, operations continued without a hitch, and our customers were none the wiser. It was a lesson in the value of preparedness, one that underscored the importance of balancing efficiency with resilience.
Drawbacks of Safety Stock
Yet, maintaining Safety Stock comes with its own set of challenges:
Increased Holding Costs: Additional inventory means more capital tied up and higher storage expenses.
Potential Obsolescence: Risk of stock becoming outdated, especially in industries with rapid product cycles.
Reduced Cash Flow: Funds invested in excess inventory cannot be used elsewhere.
Comparing JIT and Safety Stock: Striking the Right Balance
Understanding the differences between JIT and Safety Stock is crucial for any supply chain professional. Both approaches offer unique advantages and come with inherent risks. The key lies in assessing which strategy aligns best with a company's operational goals and market conditions.
Key Differences
| Aspect | Just-In-Time (JIT) | Safety Stock |
|-------------------------|---------------------------------------------------------|--------------------------------------------------------|
| Inventory Levels | Minimal inventory, aligned with immediate needs | Additional inventory as a buffer |
| Cost Implications | Lower holding costs but relies heavily on supplier efficiency | Higher holding costs due to extra stock |
| Risk Management | Vulnerable to supply chain disruptions | Provides protection against uncertainties |
| Supplier Dependence | Requires reliable and responsive suppliers | Less immediate pressure on suppliers |
| Flexibility | Less flexible in responding to sudden demand spikes | More adaptable to demand fluctuations |
When to Use Each Approach
Opting for JIT When:
Supplier Reliability is High: Strong, dependable supplier relationships are in place.
Demand is Predictable: Stable market conditions with accurate demand forecasting.
Focus on Lean Operations: The company aims to streamline processes and reduce waste.
Choosing Safety Stock When:
Demand is Volatile: Industries with seasonal or unpredictable demand patterns.
Supply Chain Risks are Present: Potential for supplier delays or logistical challenges.
Customer Service is Paramount: Prioritizing product availability to maintain satisfaction.
Integrating JIT and Safety Stock: A Hybrid Approach
In practice, many companies find that a hybrid strategy serves them best. By combining elements of both JIT and Safety Stock, businesses can optimize their supply chain management process to suit their specific needs.
Tips for Balancing Both Strategies
1- Analyze Demand Patterns: Use data analytics to understand demand fluctuations.
2- Segment Inventory: Apply JIT to stable products and Safety Stock to volatile items.
3- Strengthen Supplier Relationships: Collaborate closely to improve reliability.
4- Invest in Technology: Implement systems for real-time tracking and forecasting.
5- Continuous Improvement: Regularly review and adjust strategies as conditions change.
In one of our supply chain optimization projects, we helped a manufacturer adopt this hybrid approach. By segmenting their product lines based on demand volatility, they could apply JIT principles to consistent sellers while maintaining Safety Stock for unpredictable items. This not only reduced overall costs but also improved their ability to meet customer demands swiftly.
Navigating the Risks: Mitigation Strategies
Understanding the risk factors associated with JIT and Safety Stock is essential. Here are some strategies to mitigate these risks:
For Just-In-Time
Diversify Suppliers: Avoid over-reliance on a single source.
Enhance Communication: Establish clear and constant communication channels.
Implement Contingency Plans: Prepare alternative solutions for potential disruptions.
For Safety Stock
Optimize Stock Levels: Use statistical models to determine optimal quantities.
Regularly Review Inventory: Monitor for obsolescence or slow-moving items.
Balance Costs and Benefits: Weigh the holding costs against the risk of stockouts.
Conclusion: Crafting the Right Strategy for Your Business
Reflecting on my journey through supply chain management, I've come to appreciate that there's no one-size-fits-all solution. Every business is unique, with its own set of challenges and objectives.
By understanding the fundamental differences between Just-In-Time and Safety Stock, and recognizing the circumstances under which each is most effective, companies can make informed decisions. Whether striving for lean operations or safeguarding against uncertainties, the ultimate goal remains the same: to deliver value to customers efficiently and effectively.
So, the next time you're evaluating your inventory management strategies, consider these insights. Perhaps, like me, you'll find that the key lies not just in choosing one approach over the other but in finding the perfect balance that aligns with your business goals.
References
1- Chopra, S., & Meindl, P. (2016). Supply Chain Management: Strategy, Planning, and Operation. Pearson.
2- Heizer, J., & Render, B. (2014). Operations Management: Sustainability and Supply Chain Management. Prentice Hall.
3- Christopher, M. (2016). Logistics & Supply Chain Management. Pearson UK.
Similar Interview Questions to Consider
How do you integrate both JIT and Safety Stock in a supply chain strategy?
Can you discuss the impact of demand forecasting on inventory management approaches?
How would you handle supply chain disruptions in a JIT environment?
What methods do you recommend to optimize supply chain management processes?
Could you explain the role of technology in managing Safety Stock levels?
Key Takeaways:
Just-In-Time (JIT) focuses on reducing inventory levels and requires high supplier reliability.
Safety Stock provides a buffer against uncertainties but increases holding costs.
A hybrid approach can offer the benefits of both strategies.
Understanding your company's specific needs is essential to optimize supply chain management processes.
Remember, the world of supply chain is ever-evolving. Staying informed and adaptable is key to success. Happy managing!
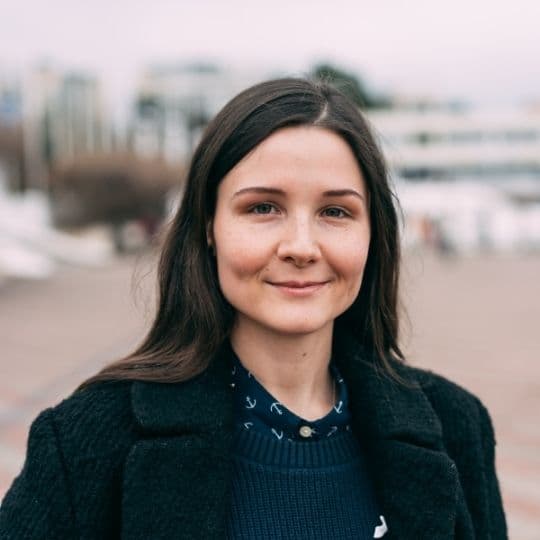
I am Amara Weiss and for many years I have worked in the field of education, specifically in the area of technology. I firmly believe that technology is a powerful tool that can help educators achieve their goals and improve student outcomes. That is why I currently work with IIENSTITU, an organization that supports more than 2 million students worldwide. In my role, I strive to contribute to its global growth and help educators make the most of available technologies.