Ensuring Delivery Consistency in Logistics Management

Aspect | Role in Logistics Management | Strategies for Improvement |
---|---|---|
Customer Service | Associated with routine tasks in the supply chain such as order processing, product tracking, and customer communication. | Efficient completion of routine tasks and coordination between different departments and suppliers. |
Delivery Consistency | Crucial in maintaining customer satisfaction in repeat orders. | Ensures timely, consistent and correct delivery of orders. |
Inventory Management | Determines availability and allocation of products for delivery. | Improvement of inventory accuracy and real-time updates. |
Timely Delivery | Influence customer satisfaction and repeat orders. | Continuous monitoring and tracking progress of orders. |
Communication | Transparency and clarity between stakeholders in the supply chain. | Efficient communication platforms and protocols. |
Inter-departmental Coordination | Ensure smooth flow of operations from order processing to delivery. | Establishment of clear roles and effective communication methods. |
Supplier Management | Affect timely acquisition and quality of products for delivery. | Maintaining good relationship with suppliers and regular performance reviews. |
Warehousing | Storage and dispatch hub for products. | Modern and efficient warehousing practices. |
Product Tracking | Eases traceability and confirmation of delivered orders. | Provision of real-time and accurate product tracking. |
Order Fulfillment | Covers the entire process from receipt of order to delivery to the customer. | Streamlined and efficient order fulfillment strategy. |
Logistics management oversees the efficient and effective flow of goods and services from the point of origin to the point of consumption. The customer service aspect of logistics management is essential for delivering goods and services to the customer in a timely and consistent manner.
Related Course: Logistics Management Courses Online
This article discusses the importance of customer service, coordination for efficiency, and delivery consistency to ensure customer satisfaction. It is essential to improve the accuracy of inventory management, guarantee the timely delivery of goods, and improve communication between stakeholders in the supply chain to ensure delivery consistency. Companies can ensure customer satisfaction and maintain a competitive advantage by ensuring customer service and delivery consistency.
Introduction
Definition of Logistics Management
Overview of Transaction Phase
Customer Service
Routine Tasks
Ensuring Delivery Consistency in Logistics Management
Logistics management oversees the efficient and effective flow of goods and services from the point of origin to the point of consumption. This includes various activities such as inventory management, transportation, warehousing, and customer service. The customer service aspect of logistics management is essential when delivering goods and services to the customer promptly and consistently.
This article will discuss the importance of customer service during the transaction phase, efficient coordination, and delivery consistency to ensure customer satisfaction.
Customer Service
The customer service aspect of logistics management is associated with routine tasks performed in the supply chain. These tasks include order processing, product tracking, and customer communication. These tasks must be done promptly and efficiently to ensure customer satisfaction. In addition, coordination between different departments and suppliers is necessary to ensure that goods and services are delivered on time and in the desired condition.
Carload Freight Supply Chain Management Benefits Challenges Strategies
Effective Warehousing And Logistics Management Tips And Strategies
Analyzing the Implications and Benefits of Asset Tracking in Business Operations
Unlocking Benefits from CPFR: A Collaborative Planning Journey
Delivery Consistency
The other important factor in the transaction phase is the consistency of delivery in repeat orders. If a customer places an order and receives it on time, they will likely be satisfied and place more orders in the future. However, if the customer receives their order late or unsatisfactory, they will likely be dissatisfied and may not place further orders. Therefore, it is essential to ensure that delivery consistently maintains customer satisfaction.
System Improvement
To ensure delivery consistency, it is essential to improve the various elements of order fulfillment. This includes improving the accuracy of inventory management, ensuring the timely delivery of goods, and improving communication between the various stakeholders in the supply chain. In addition, it is essential to have a system in place to monitor and track the progress of orders to ensure timely delivery.
Conclusion: In conclusion, customer service and delivery consistency are important factors in the transaction phase of logistics management. It is essential to ensure that routine tasks are done in a timely and efficient manner and that coordination between different departments and suppliers is necessary to ensure that goods and services are delivered on time and in the desired condition. In addition, it is essential to improve the various elements of order fulfillment to ensure delivery consistency.
Companies can ensure customer satisfaction and maintain a competitive advantage in the market by ensuring customer service and delivery consistency.
The key to success in logistics management is consistency in delivery.

Order fulfillment is an essential aspect of logistics management, as it is responsible for ensuring that customers receive their products in a timely and consistent manner. By understanding the key elements of order fulfillment, businesses can improve their delivery consistency and ensure customer satisfaction.
The first element of order fulfillment is order processing. This involves capturing orders, validating that the correct products and quantities have been ordered, and then entering the charge into the company’s database. This ensures that all orders are accurately recorded and that accurate information is available for further processing.
The second element of order fulfillment is inventory management. This involves ensuring the correct quantity and quality of products are available to meet customer demands. This is important as it helps to ensure that customers receive the products they have ordered promptly. It also helps to reduce the amount of time that customers have to wait for their orders.
The third element of order fulfillment is order tracking. This involves keeping track of orders from order placement to delivery. This helps to ensure that customers receive their orders promptly and that the company can keep up with customer demand.
The fourth element of order fulfillment is customer service. This involves providing customers with timely and accurate information about their orders and addressing any issues or concerns they may have. This helps ensure that customers have a positive experience and are satisfied with their demands.
Finally, the fifth element of order fulfillment is delivery. This involves ensuring that the product is delivered to the customer promptly and consistently. Again, this helps to ensure that customers receive their orders as quickly and reliably as possible.
By understanding and utilizing these five elements of order fulfillment, businesses can improve their delivery consistency and ensure customer satisfaction. This can help to improve customer loyalty and increase customer retention. Furthermore, it can help to improve the overall efficiency of the logistics management process.

Logistics management is a critical component of any successful business. Coordinating the delivery of goods in a timely and efficient manner is essential for the success of any business. To ensure consistency in the delivery of goods, routine tasks must be coordinated to ensure efficient delivery.
First, it is important to create a plan for efficient coordination. This should include a timeline for delivery, a schedule of tasks, and a list of resources needed to complete the task. This plan should be reviewed regularly to ensure that it is up-to-date and that any changes or improvements are implemented. Additionally, the plan should be communicated to all involved parties to ensure everyone knows the objectives and expectations.
Second, it is important to ensure that the necessary resources are available. This includes staff, transportation, and storage. By having the necessary resources available, delays can be minimized, and goods can be delivered in a timely manner. Additionally, it is important to ensure that all staff members are familiar with the plan, including any necessary changes or updates.
Third, it is important to develop a system for tracking the progress of the delivery. This system should include milestones, deadlines, and any changes or issues that may arise during the delivery. By having a tracking system in place, the progress of the delivery can be monitored and issues can be addressed in a timely manner.
Finally, it is important to develop strategies to ensure efficient delivery. This may include utilizing the most efficient routes, utilizing the most cost-effective methods, and utilizing the most reliable vendors. It may also be beneficial to develop a system for monitoring customer feedback and satisfaction to ensure that customers receive the highest quality service.
In conclusion, coordinating routine tasks to ensure efficient delivery consistency in logistics management is essential for the success of any business. By developing a plan, ensuring resources are available, tracking progress, and utilizing strategies for efficient delivery, businesses can ensure that their customers receive the highest quality service.

Logistics management is a vital process ensuring the timely and accurate delivery of goods to customers. Delivery consistency is a critical component of successful logistics management, and any inconsistencies in delivery consistency can hurt customer satisfaction and business profitability. This article will discuss the potential sources of inconsistencies in delivery consistency in logistics management.
The first potential source of inconsistencies in delivery consistency is inadequate planning and coordination between the transportation provider and the customer. When the customer and transportation provider lack a clear understanding of the delivery requirements, the delivery process can become disorganized and inconsistent. To ensure delivery consistency, customers and transportation providers should have clear communication and agreement on delivery details, such as pickup and delivery times and locations.
Another potential source of inconsistencies in delivery consistency is the lack of real-time tracking and communication. When customers are not informed of their shipments’ whereabouts in real-time, they may become frustrated with the lack of information and the potential for delays. Logistics managers should employ real-time tracking and communication systems to keep customers informed of shipment progress to ensure delivery consistency.
Thirdly, inadequate resources or personnel can contribute to inconsistencies in delivery consistency. If the transportation provider does not have enough resources or personnel to complete all tasks promptly, delivery delays will likely occur. To ensure delivery consistency, logistics managers should ensure that transportation providers have sufficient resources and personnel to complete tasks on time.
Finally, unpredictable weather conditions can also lead to inconsistencies in delivery consistency. Bad weather can cause delays or even cancelations of shipments, resulting in customer dissatisfaction. Logistics managers should stay informed of weather conditions to ensure delivery consistency and make contingency plans to minimize disruptions in lousy weather.
In conclusion, there are several potential sources of inconsistencies in delivery consistency in logistics management. For example, inadequate planning and coordination between the customer and transportation provider, lack of real-time tracking and communication, scarce resources or personnel, and unpredictable weather conditions can lead to delivery inconsistency. Therefore, logistics managers should address these potential sources of inconsistencies to ensure delivery consistency and customer satisfaction.

Role of Technology in Supply Chain Consistency
Supply Chain Visibility
Technology plays a crucial role in achieving consistency in supply chain management by enhancing supply chain visibility. Maximum visibility is vital for businesses to track and monitor the movement of goods and resources throughout the supply chain, ensuring smooth and efficient operations. Through the adoption of advanced technologies like the Internet of Things (IoT) and blockchain, companies can monitor each facet of their supply chain, increasing transparency and reducing discrepancies.
Real-time Data Analysis
Another key to consistent supply chain management is real-time data analysis. Technologies such as artificial intelligence (AI) and machine learning enable companies to analyze vast amounts of data, derive valuable insights, and make informed decisions. Leveraging this information allows firms to identify potential risks, predict future trends, and create contingency plans to handle fluctuations and maintain a consistent supply chain.
Automation and Optimization
Technology can also vastly improve the efficiency and cost-effectiveness of supply chain management through automation and optimization. Advanced software solutions can automate routine tasks, leading to significant improvements in consistency and reducing the probability of human error. Moreover, with available data and analytics, companies can optimize their supply chain, minimizing inefficiencies, and recognizing the best suppliers and transportation partners, leading to a more consistent and reliable supply chain.
Collaboration and Communication
Effective collaboration and communication among all supply chain stakeholders is necessary to ensure consistency. Modern technology, such as cloud-based solutions and communication tools, helps businesses streamline their interactions with suppliers, manufacturers, logistics partners, and customers to facilitate a more integrated and coordinated supply chain management approach. This improved collaboration plays a vital role in creating agile and consistent supply chains that can adapt to changing market conditions.
Risk Management
Finally, technology enhances supply chain risk management, ensuring consistent performance even in uncertain situations. By harnessing predictive modeling and statistical analysis tools, companies can identify potential threats and vulnerabilities in their supply chain, allowing them to proactively mitigate risks and maintain consistency.
In conclusion, technology is indispensable for achieving consistency in supply chain management. It fosters maximum visibility, real-time data analysis, automation, optimization, improved collaboration, communication, and efficient risk management, thus contributing to a more resilient and reliable supply chain that can withstand changing market conditions and deliver consistent results.

Benefits of Strategic Alliances in Logistics Management
Enhanced Sharing of Resources
Strategic alliances enable partner firms to share assets, such as infrastructure, technology, and human resources, to enhance their logistics management. This sharing leads to better capacity utilization and reduced operational costs, thereby enabling the companies to maintain delivery consistency.
Risk and Responsibility Sharing
By entering into strategic alliances, companies can distribute risks and responsibilities associated with logistics management. This reduces the overall vulnerability of each party and ensures expert handling of pertinent tasks, ultimately fostering a more stable and consistent delivery process.
Collaborative Planning and Execution
Strategic collaborations facilitate knowledge sharing, joint decision-making, and the development of mutually beneficial business models. Through joint planning and execution of logistics operations, companies can benefit from the best practices implemented by their alliance partners, driving better and more consistent delivery outcomes.
Expanding Customer Reach
Through strategic alliances, logistics firms can extend their reach to new markets and expand their customer bases. This access to a wider network allows them to achieve economies of scale and scope, subsequently improving their delivery consistency by optimizing routes and timelines.
Increasing Flexibility and Adaptability
In a dynamic business environment, partnering with other companies can give logistics providers the much-needed flexibility and adaptability to respond to varying customer requirements. Strategic alliances enhance the members' ability to adjust their resources and adopt innovative solutions, ensuring consistent delivery performance even during unforeseen circumstances.
Access to Advanced Technologies
Strategic alliances can foster technological collaborations, granting members access to state-of-the-art tools and platforms that streamline logistics processes. Harnessing these advanced technologies can help companies achieve more precise tracking, greater transparency, and better automation, ultimately paving the way for improved delivery consistency.
In conclusion, strategic alliances in logistics management can significantly improve delivery consistency by enhancing resource sharing, risk distribution, collaborative planning, market reach expansion, flexibility, and technological adoption. By partnering with other firms, logistics providers can leverage each other's strengths and surmount the challenges of an increasingly complex and competitive market landscape.

Concepts of Flexibility and Responsiveness
The concepts of flexibility and responsiveness serve as key components in effective logistics management. Flexibility involves the ability to adapt quickly to changes in customer demands, supply chain disruptions, or other factors that may impact the production and delivery of goods. On the other hand, responsiveness revolves around timely reactions to customer needs and market changes, ensuring that products are delivered on schedule (Christopher & Holweg, 2011).
Application of the 7 R's and 7 C's
Effective logistics management, through flexibility and responsiveness, is closely related to the 7 R's and 7 C's principles to ensure customer satisfaction and cost-efficiency. The 7 R's comprise the right product, in the right quantity, at the right time, in the right location, to the right customer, at the right cost, and in the right condition (Christopher & Holweg, 2011). Achieving these objectives is influenced by the flexibility of supply chains, as disruptions or changes can impact the ability to meet customer needs.
Correspondingly, the 7 C's are essential factors in successful logistics management: customer, cost, communication, control, customization, collaboration, and competition (Bottani & Rizzi, 2008). Flexible and responsive supply chains enable organizations to better address customer requirements, control costs, establish clear communication channels, manage and monitor operations more effectively, tailor solutions to individual customers, collaborate with suppliers and partners, and maintain a competitive edge in the market.
Relationship between Flexibility, Responsiveness, and the 7 R's and 7 C's
Flexibility and responsiveness act as facilitators in achieving the 7 R's and 7 C's of logistics, contributing significantly to effective logistics management. For example, adapting to fluctuating customer demands (flexibility) can help businesses maintain the right balance of product supply, ensuring that products arrive timely and in good condition (7 R's). Moreover, by rapidly responding to market changes (responsiveness), companies can maintain a competitive advantage through customer-centric approaches and collaboration with supply chain partners (7 C's).
In conclusion, flexibility and responsiveness are critical elements of effective logistics management. They support the successful implementation of the 7 R's and 7 C's principles, driving customer satisfaction and fostering operational efficiency. Supply chains that prioritize these concepts can enhance their overall effectiveness, leading to better collaborations, cost-control, communication, and ultimately, customer service.

Impact of Demand Forecasting Accuracy
Accurate demand forecasting significantly influences supply chain consistency through effective inventory management and efficient allocation of resources. When a company accurately predicts customer demand, it can maintain optimal inventory levels, thus avoiding stockouts and excess inventory, which can negatively impact the supply chain. This balance enables organizations to quickly adapt to changes in demand and effectively meet customer expectations, thereby improving customer satisfaction and strengthening the company's competitive position.
Optimizing Demand Forecasting Techniques
To optimize demand forecasting accuracy, companies should consider employing a combination of qualitative and quantitative forecasting methods. Quantitative methods, such as moving averages and exponential smoothing, effectively analyze historical data to predict future demand patterns. These data-driven techniques provide a reliable basis for inventory planning and resource allocation.
Complementing these quantitative methods, incorporating qualitative techniques, such as market research, expert opinions, and customer feedback, ensures a more comprehensive understanding of market conditions and potential fluctuations in demand. This collaboration enables organizations to develop a more accurate and robust demand forecast, addressing the limitations of relying solely on quantitative or qualitative methods.
Implementation of Technology and Analytics
Adopting forecasting technology and analytics tools can further enhance demand forecasting accuracy. Advanced tools, such as machine learning and artificial intelligence, can identify patterns and trends in vast amounts of data, allowing organizations to create demand forecasts with improved precision. Moreover, these technologies enable real-time monitoring and adjustment of forecasts, accounting for unexpected fluctuations in demand and reducing discrepancies in supply chain management.
Collaborative Forecasting Approach
A collaborative approach to demand forecasting can also contribute to optimized accuracy. Integrating input from various stakeholders, including suppliers, manufacturers, and customers, creates a more comprehensive and accurate understanding of the market. This collaborative approach enables organizations to anticipate potential supply chain disruptions, allowing for proactive adjustments to maintain consistency.
Continuous Monitoring and Evaluation
Lastly, continuous monitoring and evaluation of demand forecasting accuracy is crucial to maintaining supply chain consistency. Regular assessment of forecasting performance may reveal areas for improvement or highlight inconsistences, informing the company on necessary adjustments. This proactive approach to refining forecasting techniques and methods ensures a continually optimized supply chain, enhancing operational efficiency, customer satisfaction, and overall business performance.

Importance of Data Analytics and AI in Logistics Management
Data analytics and artificial intelligence (AI) have revolutionized the field of logistics management in multiple ways. They contribute significantly to enhancing supply chain operations by providing better visibility, accurate forecasts, and real-time insights.
Visibility Enhancement in Supply Chain
Through data analytics, companies can monitor their end-to-end supply chain operations. They gain access to real-time information on inventory levels, transit times, and potential bottlenecks. This improved visibility enables logistics managers to make informed decisions and streamline their operations.
Accurate Demand Forecasting
AI algorithms, combined with historical data and external factors, provide accurate demand forecasts. This enables businesses to optimize their inventory levels, prevent stockouts or excess inventory, and reduce overall supply chain costs.
Efficient Route Optimization
Data analysis tools can identify the most efficient transport routes based on factors such as fuel consumption, costs, and delivery timeframes. This enables logistics managers to minimize transportation costs and transit times, boosting overall supply chain efficiency.
Supply Chain Risk Management
Data analytics and AI play a critical role in anticipating and mitigating supply chain risks. By analyzing various data sets, companies can identify potential disruptions and implement contingency plans to minimize their impact on supply chain operations.
AI in Warehouse Management
Automation technologies driven by AI improve warehouse management processes, including picking, packing, and shipping. They streamline these processes by reducing manual labor, minimizing errors, and enhancing overall productivity.
AI-Driven Pricing Strategies
AI algorithms can analyze vast amounts of data to set accurate and competitive prices for products across the supply chain. These algorithms consider factors such as customer trends, competitor pricing, supply chain costs, and inventory levels, leading to increased profitability.
Dynamic Supply Chain Strategy
Data analytics and AI enable companies to develop and implement dynamic supply chain strategies based on real-time information. This agility allows businesses to adapt quickly to changes in customer demands, market conditions, and other external factors, ensuring their long-term competitiveness.
In conclusion, data analytics and artificial intelligence are integral components for enhancing logistics management and achieving consistency in supply chain operations. Companies that embrace these technologies can improve their visibility, forecasting accuracy, risk management, warehouse management, and pricing strategies, leading to streamlined operations and sustained competitive advantage.

Risk Identification and Assessment
One of the best practices in risk management in logistics is identifying potential risks and assessing their impact. This involves considering both internal and external factors that may disrupt the supply chain, such as supplier performance, transportation disruptions, and demand fluctuations. Clear communication with stakeholders, systematic monitoring of trends or events, and continuous improvement of risk identification methods contribute to successful risk management.
Risk Mitigation Strategies
Developing and implementing appropriate risk mitigation strategies is a critical practice for logistics risk management. This may involve diversifying suppliers, implementing safety stock policies, or using alternative transportation modalities. Moreover, collaborating with stakeholders and deploying agile and adaptive supply chain mechanisms can provide long-term risk mitigation solutions.
Application of the 7 R's
The 7 R's of logistics (Right product, Right quantity, Right condition, Right place, Right time, Right customer, and Right cost) play a significant role in risk management for establishing consistency in supply chain operations. Emphasizing and adhering to these principles ensures a customer-centric approach in logistics management, reducing the potential for disruptions and improving overall efficiency.
Integration of the 7 C's
In conjunction with the 7 R's, incorporating the 7 C's principles (Controllable, Compatible, Compensable, Comparable, Conceivable, Contemplatable, and Comprehensible) in risk management provides an additional layer of assurance. By evaluating supply chain risks based on these criteria, decision-makers can adopt suitable approaches to prevent and address potential disruptions. Consequently, the integration of the 7 C's facilitates a comprehensive assessment of risks and allows for strategic responses.
Technology and Data Analytics
Employing technology and data analytics in logistics risk management creates opportunities to not only proactively identify risks but also predict and prevent disruptions. Leveraging tools such as artificial intelligence, machine learning, and Internet of Things (IoT) devices for data collection and analysis improves the effectiveness and efficiency of supply chain risk management. Such data-driven insights contribute to decision-making, risk mitigation, and overall operational excellence.
In conclusion, the best practices for risk management in logistics involve identifying and assessing potential risks, developing mitigation strategies, implementing the 7 R's and 7 C's principles, and leveraging technology and data analytics. These practices ultimately facilitate supply chain consistency, improve customer satisfaction, and enable organizations to navigate an increasingly complex and competitive business landscape.

Developing a Systematic Strategy
To ensure the effectiveness of logistics management, a systematic, comprehensive strategy involving three key approaches is essential. These approaches include performance measurement, technology adoption, and continuous improvement initiatives.
Performance Measurement
The first step in ensuring effective logistics management is to establish and monitor a set of key performance indicators (KPIs). By regularly tracking data, such as the time taken for order processing or the percentage of late deliveries, organizations can identify areas within their logistics process that require improvement. In addition to this, establishing industry benchmark comparisons can lead to further enhancements in efficiency and overall performance.
Technology Adoption
Integrating advanced technology solutions, such as warehouse management systems (WMS), transportation management systems (TMS), and real-time tracking software, is a critical aspect to streamline logistics operations. Investing in technology systems provides data-driven insights that facilitate quicker decision-making, reduce human errors, and optimize the overall supply chain efficiency. Another critical technological tool is the integration of enterprise resource planning (ERP) systems, which enable organizations to centralize their data sources and ensure better collaboration among various departments.
Disaster Recovery Planning
To maintain an effective logistics management system, it is crucial to develop a robust disaster recovery plan. It involves identification of potential risk factors, implementation of necessary mitigation measures, and development of contingency plans to ensure the continuous functioning of supply chain operations. Having a properly-executed disaster recovery plan in place will safeguard organizations against unforeseen external factors, such as natural disasters or political instabilities, that could disrupt the flow of goods and services.
Continuous Improvement Initiatives
An organization should prioritize continuous improvement initiatives to achieve peak effectiveness in its logistics management. Emphasizing employee training and development fosters a culture of growth and skill enhancement, leading to higher operational efficiency. Regular feedback from stakeholders, including suppliers and customers, is a crucial aspect of continuous improvement, allowing organizations to identify and address inefficiencies, ultimately driving process improvements and cost reductions. Furthermore, organizations can benefit from applying methodologies like Lean or Six Sigma to eliminate waste and streamline their logistics operations.
In conclusion, ensuring the effectiveness of logistics management is a multifaceted process that demands an organized, strategic approach. By focusing on performance measurement, technology adoption, disaster recovery planning, and continuous improvement initiatives, organizations can achieve optimized and efficient logistics operations, ultimately contributing to their overall success.

Seven R's for Effective Logistics Management
Right Product
The first R emphasizes selecting the appropriate product. Logistics management must ascertain that the correct product is chosen, stored, and transported at the appropriate time to satisfy the clients' needs.
Right Quantity
Secondly, determining the suitable quantity of goods is essential to avoid waste or insufficiency. The logistics management team must enact measures to ensure accurate inventory and tracking, thus maintaining a proper supply-demand correlation.
Right Condition
It is paramount for the logistics team to maintain products in their optimal condition. This encompasses proper packaging, storage, temperature control, and transportation to ensure that products arrive damage-free and in good working order to the customers.
Right Place
The fourth factor focuses on strategically identifying the ideal locations for warehouses, distribution centers, and transportation hubs. The aim is to minimize transportation distances and costs, resulting in increased efficiency and customer satisfaction.
Right Time
Effective logistics management entails the timely processing and delivery of goods. This includes coordinating activities such as ordering, processing, and transportation, ensuring deadlines are met, avoiding delays, and providing a consistently dependable service for customers.
Right Customer
Logistics management must concentrate on identifying and targeting the correct customer base to optimize product distribution. This involves recognizing target markets, meeting customer requirements, and ensuring products reach their intended users.
Right Cost
Finally, cost efficiency is vital in logistics management. The goal is to balance the expenses related to storage, transportation, and inventory management while maintaining high-quality products and services. This entails pursuing cost-effective tactics in various stages of the logistics process to maximize profit margins and satisfy customer expectations.
In conclusion, adhering to the seven R's of logistics management ensures efficiency, cost-effectiveness, and customer satisfaction. Proper product selection, quantity, condition, location, timing, targeting, and cost control are vital components in creating a successful logistics strategy in today's competitive business landscape.

Key Principles of Consistency
Consistency in supply chain management refers to maintaining stable, reliable, and predictable systems throughout the entire process. This entails coordinating logistics, procurement, and production operations to provide efficient, uninterrupted flows of goods and services. By focusing on clear communication and continuous improvement, a company can achieve better levels of efficiency, increased responsiveness to customer demands, and improved overall performance.
Reducing Variability and Uncertainty
One crucial aspect of consistency is reducing variability and uncertainty in the supply chain. This can be achieved by optimizing inventory levels, standardizing processes, and implementing accurate forecasting methods. By minimizing lead times, addressing fluctuations in supply and demand, and enhancing visibility at each stage of the supply chain, a company can achieve a more consistent and predictable flow of goods and improved customer satisfaction.
Benefits of Consistency
A consistent supply chain offers numerous benefits to stakeholders involved, including lower operational costs, better resource utilization, increased flexibility, and improved risk management. These advantages contribute to higher profit margins and a more sustainable competitive edge. Consistency also fosters trust and transparency between customers, suppliers, and other key stakeholders, facilitating a collaborative environment conducive to meeting operational excellence.
Implementing Consistency Strategies
To promote consistency in the supply chain, companies should develop strategies that address the key areas identified above. Implementing robust tools, such as enterprise resource planning (ERP) systems, visibility solutions, and demand management tools, can help businesses monitor, analyze, and predict trends to better inform decision-making processes. Additionally, a commitment to ongoing learning, training, and process improvement helps ensure that organizations consistently adapt and grow to meet changing industry demands.
In conclusion, consistency in the supply chain is paramount for businesses seeking to maximize efficiency, reduce risks, and foster strong stakeholder relationships. By focusing on reducing variability, improving communication, and implementing appropriate strategies for consistency, businesses can thrive in competitive markets and ensure long-term success.

Logistics as a Key Factor in Supply Chain Management
The three main logistics objectives in achieving a balanced and effective supply chain are cost control, customer satisfaction, and efficiency optimization. These objectives contribute to the overall goal of managing supply chain operations, ensuring product availability to meet customer demand while minimizing costs and delays.
Cost Control: Reducing Total Expenses
One of the most critical objectives in logistics management is cost control. This involves reducing the overall cost of transporting, storing, and handling goods throughout the supply chain. Efficient transportation and warehousing systems can help businesses minimize expenses and boost their profitability. Some tactics to achieve this objective may include consolidating shipments, selecting cost-effective carriers, route optimization, and adopting technologies that streamline daily operations.
Customer Satisfaction: Enhancing Customer Experience
Another crucial objective in logistics management is maintaining high levels of customer satisfaction. Ensuring timely delivery of products in good condition is key to achieving this goal. When products arrive without any defects or delays, customers are more likely to be satisfied, leading to increased loyalty and repeat business. To achieve this objective, businesses should focus on effective communication with their logistics partners, continuous performance monitoring, and swift problem resolution.
Efficiency Optimization: Streamlining Operations
Lastly, efficiency optimization in logistical operations is essential for an effective supply chain. Companies must continually adapt to market changes and implement new practices that promote lean operations. This can lead to an increase in the speed and reliability of supply chain processes, while facilitating better decision-making. Examples of practices that improve efficiency include inventory management techniques to reduce excess stock, implementing advanced planning systems to estimate demand more accurately, and conducting regular assessments of logistics partners to ensure they meet performance standards.
In conclusion, the three main logistics objectives of cost control, customer satisfaction, and efficiency optimization are vital for achieving a balanced and effective supply chain. By constantly monitoring and improving these objectives, businesses can maintain an optimal level of inventory, reduce overall costs, and enhance customer satisfaction, ultimately leading to a more profitable and competitive organization.

Performance Measurement in Supply Chain Management
Performance measurement plays a vital role in ensuring consistency in supply chain management. Assessing key performance indicators (KPIs) assists managers in analyzing the efficiency of their supply chains. These metrics include inventory turnover, order accuracy, and on-time delivery. Monitoring these indicators enables organizations to identify areas of improvement, subsequently enhancing supply chain consistency. Additionally, a robust performance measurement system facilitates effective decision-making and resource allocation, supporting an organization's strategic goals and objectives.
Continuous Improvement Strategies in Supply Chain Management
Continuous improvement strategies further contribute to supply chain management consistency. By adopting methods such as Lean, Six Sigma, and Total Quality Management (TQM), organizations can consistently enhance their supply chain performance. These strategies focus on eliminating waste, reducing variation, and improving overall efficiency, resulting in a more streamlined and dependable supply chain.
Collaboration and Information Sharing
Effective collaboration and information sharing between supply chain partners also support consistency. Establishing strong communication channels and integrating information systems aid in reducing errors, enhancing visibility, and fostering trust among stakeholders. This collaborative environment allows for proactive decision-making and swift resolution of potential issues before they escalate, ensuring a consistent and reliable supply chain.
Adapting to Changing Market Conditions
In a dynamic and ever-evolving business landscape, the ability to adapt to changing market conditions is essential for maintaining supply chain consistency. By embracing flexibility and agility, organizations can swiftly respond to fluctuations in demand and supply, mitigating potential disruptions in the supply chain. Moreover, continuous monitoring of external factors, such as industry trends, emerging technologies, and global economic shifts, enables organizations to proactively anticipate and respond to potential challenges and opportunities.
In conclusion, performance measurement and continuous improvement strategies are critical in maintaining consistency in supply chain management. When effectively implemented, these elements enable organizations to streamline operations, reduce potential disruptions, and continuously seek opportunities for enhancement. By fostering a culture of collaboration, agility, and adaptability, organizations can maintain and consistently improve supply chain reliability and performance.

Role of End-to-End Visibility in Logistics Management
End-to-end visibility serves as a cornerstone for effective logistics management, empowering organizations to closely monitor and optimize each stage of their supply chain. Real-time access to accurate information enables informed decision-making, maximizes asset utilization, and minimizes delays or disruptions. Moreover, this unparalleled visibility allows companies to mitigate risks and address challenges proactively by adjusting their strategies accordingly, leading to improved overall performance.
Collaboration as a Key to Supply Chain Consistency
In the context of supply chains, collaboration refers to the seamless coordination of all stakeholders involved, including manufacturers, suppliers, logistics providers, and customers. This concerted effort fosters transparency, open communication, and shared objectives, fostering a more streamlined and efficient logistics process. Furthermore, collaboration cultivates a sense of joint responsibility among partners, which significantly impacts performance metrics like on-time delivery, order accuracy, and inventory levels, ultimately contributing to supply chain consistency.
Technology: Enabler of Visibility and Collaboration
Advanced technologies play a critical role in enhancing end-to-end visibility and collaboration in logistics management. For instance, cloud-based platforms help integrate data from disparate sources, providing real-time insights and performance metrics to stakeholders. Additionally, tools like the Internet of Things (IoT) and Radio Frequency Identification (RFID) enable robust tracking and monitoring throughout the entire supply chain. By harnessing these innovative solutions, companies can foster more effective logistical operations and achieve greater consistency across their networks.
In conclusion, end-to-end visibility and collaboration significantly impact logistics management effectiveness and supply chain consistency. By embracing these practices and leveraging advanced technologies, organizations can prosper in a competitive market while delivering exceptional customer service and sustaining growth.

Understanding Demand Variability and Supply Chain Consistency
Demand variability refers to the fluctuations in customer demand, while supply chain consistency pertains to the predictable flow of materials and products throughout the supply chain system. The relationship between these two elements is critical to achieving better logistics performance, as excessive variability in demand can lead to inefficiencies and higher costs.
Balancing Inventory Levels
Balancing inventory levels is essential to mitigate the effects of demand variability on supply chain consistency. By adequately forecasting demand, businesses can prevent both stockouts and overstocking, improving overall logistics performance. Accurate demand forecasting allows companies to maintain appropriate safety stock levels, which help in enhancing product availability and reducing risk to the supply chain.
Synchronized Information Sharing
Supply chain partners can achieve better logistics performance by sharing information on demand and inventory levels. Synchronized information sharing allows companies to coordinate production and replenishment schedules, resulting in a more consistent, responsive, and resilient supply chain. This collaborative approach can help businesses tackle demand variability effectively while synchronizing their supply chain processes, leading to improved logistics performance.
Agile Supply Chain Strategies
An agile supply chain strategy can be highly beneficial in managing the impact of demand variability on supply chain consistency. Agility in the supply chain enables companies to rapidly respond to changes in demand by employing flexible and adaptable production, transportation, and distribution processes. Incorporating elements such as real-time data analytics, demand-driven replenishment, and modular production can contribute to an agile supply chain, enabling greater consistency in the face of demand fluctuations.
In conclusion, the relationship between demand variability and supply chain consistency is crucial for better logistics performance. By implementing strategies that focus on balancing inventory levels, synchronized information sharing, and agility in the supply chain, businesses can effectively manage the impacts of demand variability and maintain supply chain consistency, ultimately leading to improved logistics performance.

**Integration of Functions and Processes**
The integration of diverse functions and processes within the supply chain plays a vital role in attaining the 7 R's in logistics management, which are the right product, right quantity, right condition, right place, right time, right customer, and right cost. Effective coordination and communication among supply chain partners are the keys to achieving the 7 R's and enhancing customer value.
**Streamlined Information Flow**
One critical aspect of integration is streamlining information flow among supply chain partners. The integration of information systems provides timely and accurate data, enabling logistics managers to make informed decisions so that goods arrive at the right time and at the right place. This reduces lead times and prevents stockouts or overstocking.
**Quality Assurance and Control**
Another significant aspect is quality assurance and control. By collaborating closely with suppliers and manufacturers, logistics managers ensure that goods meet the right quality and condition standards. The integration of manufacturing and transportation processes allows for better product traceability, enabling companies to establish responsibility for defects and swiftly address any quality concerns.
**Optimizing Inventory Levels**
Moreover, the integration of various processes promotes optimal inventory management, aligning inventory levels with customer demand to conserve resources, minimize waste and ensure the right quantity of goods for consumers. This includes employing techniques such as just-in-time delivery, cross-docking, and vendor-managed inventory systems, which align the supply chain from production to distribution.
**Cost Efficiency and Customization**
Integrated processes contribute to achieving the right cost by optimizing logistics activities, such as selecting the most efficient transportation mode, consolidating shipments, and utilizing appropriate warehousing solutions. Additionally, integration allows companies to provide customized services to specific customers, increasing customer satisfaction and loyalty.
**Coordination and Collaboration**
Lastly, integration enables coordination and collaboration, fostering strong relationships among supply chain partners. This leads to a higher trust level, increased information sharing, and better understanding of the needs of each link in the supply chain. In turn, this supports the achievement of the right customer target and enhanced service offerings.
In conclusion, the integration of different functions and processes within the supply chain is essential for achieving the 7 R's in logistics management. Integration facilitates a streamlined information flow, quality assurance and control, optimized inventory levels, cost efficiency, customization, and greater coordination among supply chain partners. Ultimately, this results in increased customer satisfaction and a more competitive business.

Incorporating Effective KPIs in Supply Chain Management
Key performance indicators (KPIs) are essential metrics that organizations use to evaluate the success of their supply chain management efforts. Incorporating effective KPIs helps in monitoring and improving consistency throughout various stages of the supply chain.
Selecting Relevant and Specific KPIs
It is crucial for organizations to select KPIs that directly relate to their business objectives. By doing so, the selected KPIs will accurately reflect the organization's progress towards achieving its goals. Ensuring that the KPIs are specific allows for precise tracking of each aspect of the supply chain management process.
Monitoring KPIs for Real-Time Insights
Continuous monitoring of KPIs provides real-time insights into the performance of the entire supply chain. By analyzing the data gathered, organizations can identify bottlenecks and potential issues, enabling proactive and timely interventions. This approach not only ensures that supply chain operations are optimized, but also helps maintain consistency throughout the process.
Benchmarking to Improve Performance
Comparing KPIs against industry standards and competitors provides valuable insights that can help organizations improve their supply chain management practices. By understanding where they stand in comparison to others, businesses can identify areas of improvement and implement strategies to enhance their performance and maintain consistency throughout the supply chain.
Training and Communication
Efficient utilization of KPIs requires proper training and communication among all stakeholders involved in the supply chain operations. By ensuring that everyone understands the significance of the selected KPIs, organizations can enhance teamwork, foster employee engagement, and ensure that the entire supply chain operates in a consistent and coordinated manner.
Implementing Continuous Improvement Frameworks
To effectively utilize KPIs in improving supply chain consistency, organizations should adopt continuous improvement frameworks, such as Lean Six Sigma or the Plan-Do-Check-Act (PDCA) cycle. These methodologies enable consistent monitoring and improvement of processes, thus ensuring the supply chain remains agile and adaptable to the dynamic business environment.
In conclusion, the effective utilization of KPIs is instrumental in monitoring and improving consistency in supply chain management. Organizations must select relevant KPIs, monitor them in real-time, benchmark their performance, enhance communication among stakeholders, and implement continuous improvement frameworks for successful supply chain management.

Implications of Consistent Delivery
Consistent delivery signifies the provision of products or services in a timely and regular manner. It holds immense significance in reducing the inventory levels of business customers. When suppliers consistently deliver on time, it enhances the dependability of the supply chain. This increased reliability allows companies to maintain lower levels of inventory.
Cutting Inventory Costs
Reduced inventory levels signify lesser funds tied up in stock. They translate into lower warehousing costs and decreased chances of product obsolescence. Thus, consistent delivery directly impacts the financial health of businesses, as costs reduce while liquidity enhances. Reduced inventory also minimizes risk exposure to price fluctuations.
Enhancing Operational Efficiency
Business customers also benefit operationally from consistent delivery. It facilitates better production planning and supply chain management. When business customers can count on their suppliers to deliver on time, they can plan and execute their operations smoothly. It minimizes the likelihood of production halts due to stockouts.
Improving Customer Satisfaction
Finally, consistent delivery is instrumental in enhancing customer satisfaction. If a company can rely on its suppliers for regular deliveries, it can, in turn, reassure its customers about the availability and timely delivery of its products or services. Thus, with reduced inventory levels, businesses not only lower their costs and streamline operations but also ensure higher levels of customer satisfaction.
Hence, consistent delivery carries substantial significance in reducing the inventory levels of business customers. It contributes to financial, operational, and service improvements of companies, strengthening their positions in the competitive marketplace.

Understanding Demand
Making strategic decisions in logistics demands the complete comprehension of the company's demand cycle. It involves tracking historical demand patterns, forecasting future needs, and understanding factors that influence demand.
Supply Chain Design
A company should consider supply chain design while making strategic decisions. A well-structured supply chain system improves efficiency and speed. It covers selection of suppliers, distribution centers, transportation routes, and inventory levels.
Risk Management
Risk management often comes into highlight in strategic decision making. It involves identifying potential risks, assessing their impact, and developing plans to mitigate them. Unexpected disruptions, whether due to supplier defaults, market changes, or natural calamities can potentially affect the supply chain.
Cost and Value Analysis
Cost and value analysis plays a pivotal role in strategic decision-making. Companies should account for all their costs and revenues to fully understand their profit margins. Cost-benefit analysis, pricing strategies, and life-cycle costing are critical components of this aspect.
In conclusion, understanding demand, supply chain design, risk management, and cost and value analysis are significant aspects while making strategic decisions on logistics. These elements ensure the company's preparedness for change, the vulnerability of the Supply chain, and profitability, eventually leading the company towards growth and sustainability.

Understanding Flexibility and Responsiveness
Flexibility and responsiveness serve as key aspects in effective logistics management. Flexibility enables businesses to adapt to a fluctuating market and swiftly adjust to unexpected situations. It involves the ability to scale operations to meet varying customer demands. Meanwhile, responsiveness is about businesses promptly reacting to customer requirements and efficiently managing unforeseen disruptions in supply chains.
Relationship to the 7 R's of Logistics
The concepts of flexibility and responsiveness are intertwined with the seven R's of logistics, which include the right product, right quantity, right condition, right place, right time, right cost, and right customer. Flexibility gives the entity the capacity to fulfill these criteria despite market instability. Moreover, responsiveness ensures delivery of the seven R's in a timely manner, establishing customer satisfaction and trust.
Correlation to the 7 C's of Logistics
Further, responsiveness and flexibility also connect with the seven C's of logistics: customer, cost, communication, control, current, continuity, and channel. A customer-focused approach requires businesses to respond promptly to customer requests while being flexible to their changing needs. On the other hand, communication, control, and continuity necessitate quick responses and adaptable procedures. By being flexible and responsive, businesses can effectively manage costs, stay current with market trends, and choose the optimal distribution channels.
In sum, flexibility and responsiveness heighten a business's ability to adhere to the 7 R's and 7 C's of logistics. These concepts ensure customers receive the desired products at the right time, in the right place, and at the right cost, ultimately improving the overall effectiveness of logistics management.

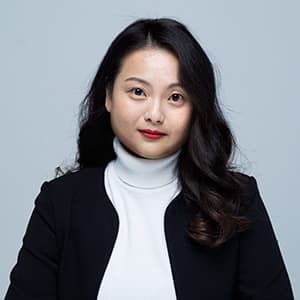
Yu Payne is an American professional who believes in personal growth. After studying The Art & Science of Transformational from Erickson College, she continuously seeks out new trainings to improve herself. She has been producing content for the IIENSTITU Blog since 2021. Her work has been featured on various platforms, including but not limited to: ThriveGlobal, TinyBuddha, and Addicted2Success. Yu aspires to help others reach their full potential and live their best lives.