Quick Response Logistics: Leveraging Technology for Speed

Feature | Description | Impact |
---|---|---|
Quick Response Logistics (QRL) | The capability of a business to promptly deliver services to customers. | Improves customer satisfaction and loyalty; increases revenue; provides cost savings. |
Information Processing Technology | It includes automation, artificial intelligence (AI), and machine learning (ML). | Facilitates accurate decision-making and reduces time to deliver services. |
Automation | Technology used to streamline information processing in QRL. | Enhances speed and accuracy of decision-making; reduces operational costs. |
Artificial Intelligence & Machine Learning | AI and ML are used to analyze data and identify patterns, aiding decision-making in QRL. | Improves predictive capability and accuracy; enables real-time decision-making. |
Flexibility | Businesses can quickly respond to varying customer orders, even at the point of consumption. | Enhanced customer satisfaction; allows businesses to meet dynamic customer requirements. |
Revenue growth | Prompt response to customer needs leads to increased customer satisfaction and loyalty, resulting in higher revenue. | Provides financial advantages for businesses. |
Improved Customer Experience | Customers receive their orders quickly, improving their overall experience with the business. | Boosts customer loyalty and potential for repeat business. |
Cost savings | QRL reduces the time taken to fulfill orders, thereby saving on labor costs. | Direct cost savings for businesses, leading to overall increased efficiency. |
Business Benefits | Increased customer satisfaction, loyalty, revenue, and cost savings. | Improved brand image and competitive advantage in the marketplace. |
Customer Benefits | Prompt delivery of services and quick response to needs. | Increased satisfaction and loyalty, improving the overall customer experience. |
This article discussed the advantages of Quick Response Logistics (QRL) and how businesses can use it. It explored how information processing technology can help reduce the time taken to make decisions, as well as how QRL allows businesses to be flexible to meet customer requirements. It also highlighted the various advantages of QRL, such as increased customer satisfaction, loyalty, revenue, and cost savings.
Introduction
Technology in Information Processing
Flexibility to Fulfill Customer Requirements
Advantages of Quick Response Logistics
Conclusion
Introduction: Quick Response Logistics (QRL) is a term used to describe the capability of a business to extend services to customers promptly. Leveraging the latest information processing and communication technology can help facilitate accurate decision-making and reduce the time taken to deliver services. This article will explore the advantages of QRL and how businesses can use it to their advantage.
Technology in Information Processing
Technology has revolutionized how businesses process information, enabling them to make decisions faster and more accurately. Automation, artificial intelligence (AI), and machine learning (ML) are some of the most commonly used technologies in information processing. Automation helps to streamline processes, while AI and ML can be used to analyze data and identify patterns that can be used to make decisions. By leveraging technology, businesses can reduce the time taken to process information and make decisions, thus improving their ability to provide quick response services to customers.
Flexibility to Fulfill Customer Requirements
QRL allows businesses to be flexible to meet customer requirements. For example, businesses can quickly respond to customer orders for small shipments and deliver them rapidly, even at the point of consumption. This flexibility allows businesses to meet customer needs better and increase customer satisfaction.
Advantages of Quick Response Logistics
QRL offers several advantages to both businesses and customers. For businesses, it allows them to respond quickly to customer needs, leading to increased customer satisfaction, loyalty, and revenue. For customers, it will enable them to receive their orders quickly, thus improving their overall experience with the business. QRL also allows businesses to save time and money, as they can reduce the time taken to fulfill orders and reduce the cost of labor.
Conclusion: In conclusion, Quick Response Logistics (QRL) is a term used to describe the capability of a business to extend services to customers promptly. Leveraging the latest information processing and communication technology can help facilitate accurate decision-making and reduce the time taken to deliver services. QRL offers several advantages to both businesses and customers, such as improved customer satisfaction, loyalty, revenue, and cost savings. Thus, QRL is essential for businesses to ensure they can quickly and effectively meet customer needs.
Speed is essential in Quick Response Logistics; technology is the key to unlocking it.

It is no secret that technology has revolutionized the logistics industry. With the introduction of automation, the logistics industry has seen its operations become quicker, more efficient, and less expensive. In the realm of quick response logistics, technology is even more critical. Quick response logistics is utilizing high-speed transportation and delivery systems to transport goods from one location to another quickly. Leveraging technology for speed can provide numerous benefits to companies in the logistics industry.
First and foremost, technology can increase efficiency and accuracy in quick response logistics. Automation can be used to quickly identify the most efficient route and vehicle to transport goods, reducing the amount of time and resources required to deliver goods to their destination. Additionally, automation can be used to monitor the progress of a shipment, providing real-time updates to the customer and helping to ensure that goods are not delayed due to unforeseen circumstances.
Moreover, leveraging technology for speed can help to improve customer service. With automation, customers can quickly and efficiently track their shipments, allowing them to plan accordingly and receive their goods on time. Furthermore, the use of automation can help reduce the time and resources needed to handle customer inquiries, allowing companies to devote more time and resources to providing quality customer service.
Finally, leveraging technology for speed can help to reduce costs for companies in the logistics industry. Automation can be used to identify the most cost-effective route to transport goods, reducing the amount of time, money, and resources needed to complete a delivery. Additionally, automation can streamline the process of booking, scheduling, and tracking shipments, reducing the time and resources needed for administrative tasks.
In conclusion, leveraging technology for speed in quick response logistics can be an invaluable asset to companies in the logistics industry. By increasing efficiency and accuracy, improving customer service, and reducing costs, technology can help logistics companies enhance their operations and better serve their customers.

Quick Response Logistics (QRL) is an emerging concept in supply chain management that emphasizes rapid order fulfillment, shorter lead times, and quick inventory turnover. It is a customer-centric approach that leverages technology to provide timely and accurate delivery of goods and services. Technology plays a critical role in enabling QRL to reach its goal of maximizing customer satisfaction and convenience. This article will explore how technology can enhance decision-making accuracy and time in QRL.
Real-time data analytics is essential to QRL, as it allows for informed decision-making and timely response to customer needs. Data analytics can identify trends and patterns in customer orders, such as the most popular products, times of peak demand, and geographic preferences. This information can be used to make informed decisions about inventory replenishment, staffing levels, and delivery routes. In addition, data analytics can provide insights into customer behavior that can be used to develop customized marketing campaigns and promotions.
Technology can also automate and streamline the ordering and fulfillment process. Automation of order processing and fulfillment can significantly reduce order errors and delays. Automation also allows for more accurate and timely inventory updates, enabling QRL practitioners to respond quickly to customer needs. Automating the ordering and fulfillment process also reduces the need for manual intervention, which can help reduce costs and improve customer satisfaction.
Robotic process automation (RPA) is also becoming an increasingly important part of QRL. RPA can automate repetitive tasks such as order processing and fulfillment, allowing QRL practitioners to focus their time and energy on more complex tasks. RPA can also automate customer service functions such as order tracking, product returns, and customer inquiries, allowing faster response times and improved customer satisfaction.
Finally, technology can enhance the accuracy and timeliness of delivery. Real-time tracking and location technologies can be used to monitor the progress of shipments, allowing QRL practitioners to make adjustments as needed to ensure timely delivery. In addition, advanced routing algorithms can be used to optimize delivery routes and reduce delays. In contrast, automated dispatching can be used to manage the allocation of resources and ensure optimal delivery performance.
In conclusion, technology can be critical in enabling QRL to maximize customer satisfaction and convenience. By leveraging data analytics, automation, robotics, and advanced routing algorithms, QRL practitioners can enhance decision-making accuracy and time, reduce costs and improve customer service.

Quick Response Logistics (QRL) is a form of supply chain management that enables companies to acquire and deliver goods rapidly and cost-effectively. The goal of QRL is to reduce lead times and improve customer service. Through QRL, companies can provide their customers with an efficient and reliable delivery service, even for small shipments.
QRL is becoming increasingly popular amongst companies due to its ability to reduce lead times and improve customer service. Small shipments can be delivered quickly and without disruption due to the streamlined processes and reduced paperwork associated with QRL. For example, a company may use QRL to transport small shipments from a warehouse to a retail store or from a supplier to a customer. With QRL, these shipments can be delivered within a few hours or even faster, depending on the desired delivery time.
Another example of a small shipment that can be delivered quickly through QRL is a single item or small parcel. This type of shipment is typically used for online orders or for sending items to a customer. Through QRL, companies can ensure that these small shipments arrive at their destination with minimal disruption and on time.
Additionally, QRL can deliver large orders of products quickly and efficiently. For example, a company may use QRL to transport a large order of products from a warehouse to a customer. Through QRL, the products can be delivered within a few hours or even faster, depending on the desired delivery time. This allows companies to provide their customers with a quick and reliable delivery service.
In conclusion, QRL is a form of supply chain management that enables companies to acquire and deliver goods quickly and efficiently. Through QRL, companies can provide their customers with a quick and reliable delivery service, even for small shipments. Examples of small shipments that can be delivered quickly through QRL include single items or small parcels and large orders of products. QRL is becoming increasingly popular amongst companies for its ability to reduce lead times and improve customer service.

Role of Demand Forecasting
Quick response logistics is an efficient supply chain management strategy that aims to meet the evolving demands of consumers through rapid product delivery and inventory turnover. Demand forecasting plays a critical role in this process, as it helps businesses to prepare for fluctuations in customer needs, thereby maximizing customer satisfaction and minimizing inventory costs.
Data-Driven Insights
Demand forecasting relies on historical sales data and market trends to predict future consumer demand, allowing businesses to optimize production levels and more effectively allocate resources. Accurate demand forecasts provide greater insights for the entire supply chain, helping businesses make informed decisions on sourcing, manufacturing, and distribution of products.
Inventory Management
Properly forecasted demand facilitates better management of inventory levels, preventing stock-outs and overstock scenarios. This helps meet urgent customer demands, increasing the chances of repeat business and improving overall profitability. Adopting just-in-time inventory systems, organizations can further reduce warehouse costs and increase efficiency in product distribution.
Production Planning
Accurate demand forecasting also aids in production planning, allowing manufacturers to schedule resources optimally and avoid potential disruptions or bottlenecks. Consequently, reducing lead times and ensuring products reach customers in the shortest possible time. Collaborative efforts, such as sales and operations planning, can help bridge the gap between production and demand forecasts, ensuring a smooth flow of goods throughout the supply chain.
Resource Allocation
By effectively anticipating customer demand, businesses can allocate their valuable resources - such as capital, labor, and capacity planning - to other strategic areas, driving growth and innovation. Additionally, understanding shifting market trends can help organizations identify new product or market opportunities, enabling them to adapt and stay competitive in an ever-changing business environment.
In conclusion, demand forecasting plays a vital role in quick response logistics, driving efficiencies across the entire supply chain. Accurate forecasts offer valuable insights into customer behaviour, resulting in improved inventory management, production planning, and resource allocation. Ultimately, demand forecasting enables businesses to compete effectively and deliver products to customers more efficiently and rapidly.

Importance of Collaborative Partnerships
Collaborative partnerships play a vital role in enhancing the efficiency of a quick response strategy in logistics. By joining forces with various stakeholders, including suppliers, manufacturers, and retailers, a logistics company can optimize its performance and resources to achieve a more agile and swift supply chain management.
Combined Knowledge and Expertise
Integrating the know-how and experience of all participants allows the identification of potential bottlenecks and deficiencies in the logistics process. As a result, a logistics company can redesign its operations and routes more effectively, ensuring timely delivery and improved service quality.
Risk Management and Contingency Planning
Collaborative partnerships contribute to managing potential risks and disruptions in the logistics sector. By coordinating efforts and exchanging information, partners enhance their capacity to foresee potential threats, develop robust contingency plans, and mitigate the impact of unexpected events such as natural disasters, accidents, or sudden market changes.
Enhanced Communication and Data Sharing
Effective collaboration requires seamless communication and data sharing among partners. By investing in advanced information technology systems and ensuring data transparency, participants facilitate faster decision-making processes and support the adaptability of the entire supply chain to sudden variations in demand and supply.
Coordination of Inventory and Distribution
Working closely with other partners helps a logistics company to harmonize its inventory and distribution operations, thus reducing lead times and minimizing stock-outs, overstocking, or inefficient transportation.

Efficient Order Processing
The primary feature of successful inventory management techniques for quick response in logistics is efficient order processing, which includes the timely receipt, picking, packing, and shipping of goods. This reduces lead times and ensures swift delivery of products to satisfy customer demands.
Accurate Demand Forecasting
Another crucial characteristic is accurate demand forecasting, which means using historical data and advanced analytics tools to predict future product requirements. Aligning inventory stocks with anticipated customer needs reduces the risk of stockouts, surplus inventory, and wasted resources.
Real-time Inventory Visibility
Real-time inventory visibility is also essential for quick response in logistics. This entails tracking products throughout the supply chain using technologies such as RFID, IoT devices, and barcode scanners. The real-time information enables businesses to monitor inventory levels, minimize errors, and make informed decisions.
Flexible Adaptation
The ability to adapt to rapidly changing market conditions characterizes successful inventory management techniques. This flexibility involves responding to fluctuations in demand, adjusting lead times, and enhancing coordination with suppliers, manufacturers, and carriers. A well-prepared inventory strategy allows businesses to maintain service levels during unforeseen circumstances.
Warehouse Optimization
Warehouse optimization is another key feature that improves logistics speed. By implementing efficient layout designs, utilizing appropriate storage equipment, and optimizing picking routes, businesses can minimize handling and storage time. An organized warehouse structure ensures faster product retrieval and order fulfillment.
Proactive Stock Replenishment
Proactive stock replenishment is an integral component of successful inventory management. Businesses should establish minimum stock levels and set reorder points to maintain adequate inventory coverage. Automated inventory management systems offer significant benefits in this regard by triggering replenishment orders when stocks fall below preset levels.
Continuous Improvement
Lastly, the pursuit of continuous improvement is a hallmark of successful inventory management techniques. By regularly analyzing performance data and identifying areas for enhancement, businesses can refine their inventory processes and devise innovative strategies to achieve faster logistics response times. This commitment to improvement fosters agility and long-term competitiveness.

Role of Data Analytics in Quick Response Strategy
Data-Driven Decision Making
Data analytics plays a pivotal role in developing and executing a quick response (QR) strategy in logistics by facilitating data-driven decision making. Logistics companies leverage data analytics tools to collect, analyze and interpret vast volumes of structured and unstructured data from various sources, such as GPS tracking devices, sensors, and operational records.
Enhanced Supply Chain Visibility
Through data analytics, firms gain enhanced supply chain visibility, enabling them to identify inefficiencies, bottlenecks, and potential risks. This comprehensive understanding of their supply chain facilitates the design of more effective QR strategies, as well as more accurate forecasting and demand planning. This leads to better decision making and increased operational efficiency.
Real-Time Monitoring
Real-time monitoring of key performance indicators (KPIs) is another critical aspect of data analytics in logistics. By continuously tracking variables such as on-time delivery rates, transit times, and stock levels, logistics professionals can quickly identify deviations from their QR goals and take necessary action. For instance, if a shipment is delayed, companies can utilize data analytics insights to find alternate routes or modes of transportation, minimizing disruptions and ensuring timely deliveries.
Predictive Analytics
Predictive analytics is another essential area where data analytics supports QR strategies in logistics. By leveraging advanced algorithms and machine-learning models, companies can forecast future trends, anticipate potential challenges and devise proactive solutions. This forward-looking approach allows logistics organizations to better allocate their resources, optimize their operations, and maintain higher service levels, significantly contributing to their QR capabilities.
Agile Operations
Finally, data analytics fosters agility in logistics operations by empowering companies to rapidly respond to changes in customer demands and market conditions. With real-time data insights, logistics firms can swiftly adjust their strategies, aligning their processes and resources to the evolving landscape. Consequently, data analytics serves as a vital enabler of adaptability, a crucial aspect of any successful quick response strategy.
In conclusion, data analytics plays an indispensable role in the development and execution of a quick response strategy in logistics. Through enhanced supply chain visibility, real-time monitoring, predictive analytics, and agile operations, data-driven decision making empowers logistics companies to better anticipate and react to changes, ensuring increased efficiency and superior customer service.

Real-Time Information Usage in Logistics Planning
Incorporating real-time information into logistics planning plays a crucial role in enhancing quick response effectiveness. This incorporation results in several key benefits, which collectively contribute to overall efficiency and productivity.
Improved Decision Making
Firstly, real-time data allows decision makers to gain a comprehensive understanding of the current situation. This enables them to make more accurate and timely decisions, which ultimately reduces the risks associated with logistical operations. For instance, tracking shipments using GPS technology helps identify potential problems and delays, allowing organizations to deploy contingency plans immediately.
Optimization of Transport Routes
Secondly, real-time information facilitates route optimization, leading to reduced travel times and transportation costs. Utilizing data on traffic conditions, weather patterns, and alternative routes enables the identification of the most efficient transportation routes. Consequently, this minimizes fuel consumption, lowers emissions, and streamlines the overall logistics process.
Proactive Problem-Solving
Thirdly, access to real-time information empowers organizations to identify problems and anticipate future obstacles. This proactive approach to problem-solving enables quick responses to disruptions, significantly reducing the downtime associated with unforeseen events. For example, advanced monitoring systems can predict mechanical failures, allowing maintenance teams to address issues before they escalate into costly setbacks.
Enhanced Customer Satisfaction
Lastly, the implementation of real-time data fosters improved customer satisfaction. By monitoring delivery progress and offering accurate, up-to-date information to customers, companies can maintain open communication and ensure delivery expectations are met. In turn, this leads to increased trust and loyalty from customers, positively impacting the organization's reputation and bottom line.
In conclusion, incorporating real-time information into logistics planning is vital for enhancing quick response effectiveness. This proactive approach allows organizations to make informed decisions, optimize routes, anticipate problems, and maintain satisfied customers, leading to increased efficiency, lower costs, and an overall competitive advantage in the logistics industry.

Real-time Adaptation with AI and Machine Learning
The advent of artificial intelligence (AI) and machine learning (ML) has revolutionized many industries, and quick response logistics is no exception. Utilizing these technologies, logistics companies can optimize their operations and streamline processes, leading to increased efficiency and reduced costs.
Enhancing Route Optimization
AI and ML algorithms can analyze historical data to predict traffic patterns, weather conditions, and other factors that affect delivery routes, making real-time adjustments to maximize efficiency. By constantly updating and refining routes, AI-driven models help avoid delays and ensure timely deliveries.
Inventory Management and Demand Forecasting
AI can significantly improve inventory management by analyzing trends in customer orders, seasonal fluctuations, and other influencing factors. This allows companies to maintain the right amount of inventory, preventing stock-outs or excess inventory. Machine learning algorithms, when applied to demand forecasting, generate more accurate predictions, helping companies plan their resources, workforce, and production schedules more effectively.
Automating Warehouse Operations
Machine learning can automate various warehouse operations such as sorting, picking, and packing. By training algorithms to recognize specific products, robotics can quickly locate and transport items, reducing manual labor and improving warehouse efficiency. AI-powered cameras and sensors can monitor stock levels and alert managers in case of discrepancies, ensuring timely replenishments.
Enhancing Customer Service
AI-powered chatbots and virtual assistants can provide immediate, personalized support to customers, handling inquiries related to order status, delivery updates, and returns or refunds. These tools not only save employee time and resources but also lead to higher customer satisfaction.
Predictive Maintenance of Vehicles and Equipment
Predictive maintenance employs AI to analyze real-time data from connected devices installed in vehicles and equipment. By preemptively identifying potential breakdowns and maintenance requirements, companies can avoid costly downtime and ensure optimal performance of their logistics fleet.
In conclusion, artificial intelligence and machine learning have the potential to greatly optimize quick response logistics by enhancing route optimization, inventory management, warehouse operations, customer service, and predictive maintenance. By adopting these technologies, companies can streamline their processes and gain a competitive edge in the highly competitive logistics industry.

Quick Response in Logistics
Quick response (QR) in logistics refers to the strategic approach of improving the efficiency and effectiveness of supply chain operations, primarily through reducing lead times, enhancing information sharing, and embracing new technologies. These measures enhance supply chains' ability to respond swiftly to fluctuations in market demand and mitigate the impact of disruptions, thereby offering a competitive advantage for organizations.
Impact on Supply Chain Management
1. Reduced lead times
Implementing QR in logistics enables a reduction in lead times, allowing for faster delivery of products from manufacturers to end consumers. This is achieved through effective collaboration with suppliers, streamlining processes, and adopting just-in-time (JIT) inventory models, which help businesses to minimize stockpile and carrying costs.
2. Enhanced information sharing
QR promotes better communication and transparency throughout the supply chain by leveraging technology to facilitate real-time information sharing among stakeholders. This approach allows businesses to effectively track inventory levels, identify potential bottlenecks, and optimize their operations. Consequently, supply chain partners can make better-informed decisions, thus improving customer satisfaction and gaining a competitive edge.
3. Technology adoption
Innovations such as artificial intelligence (AI), machine learning (ML), the Internet of Things (IoT), and blockchain are increasingly being used to enable QR in logistics. These technologies help businesses automate crucial tasks, track and monitor assets, and secure transactions, which in turn accelerates decision-making and reduces the likelihood of human error.
4. Agile supply chain
Adopting QR practices fosters a more agile and resilient supply chain, capable of adapting to fluctuations in customer demand, industry trends, and unforeseen disruptions. As a result, businesses embracing QR can manage risks more effectively by identifying potential issues and implementing contingency plans ahead of time.
5. Environmental considerations
QR leads to the optimization of transportation networks and the adoption of efficient packaging solutions, consequently contributing to reduced carbon emissions and environmental impact. This can enhance an organization's corporate social responsibility, leading to increased customer goodwill and long-term growth.
In conclusion, QR is an essential strategy for the modern logistics landscape, characterized by increasing customer expectations and rapid industry changes. By implementing QR techniques, businesses can optimize their supply chain management, reducing costs and increasing efficiency while improving customer satisfaction and contributing to sustainability.

Understanding the Key Principles
A successful quick response strategy in logistics requires an understanding of the key principles that govern its effectiveness. We begin with agility, which refers to the capability of a logistics system to rapidly adjust and respond to unexpected changes in demand or supply, ensuring the timely delivery of products and services. Flexibility, on the other hand, pertains to the ability to customize operations to meet specific customer requirements and manage fluctuations in demand.
Collaboration and Integration
Effective collaboration and integration among supply chain partners are crucial components of a quick response strategy. A high level of information sharing and coordination between stakeholders (e.g., manufacturers, distributors, retailers) enables seamless operations and timely response to market changes. Integrating disparate systems and processes across the supply chain ensures that each party has access to real-time information, enabling them to make informed decisions and respond promptly to emerging challenges.
Investing in Technology
Technological advancements play a significant role in facilitating quick response logistics strategies. Investing in modern technologies such as big data analytics, artificial intelligence, and the Internet of Things (IoT) can significantly improve the overall efficiency and responsiveness of the supply chain. For instance, real-time visibility into inventory levels, order status, and shipment tracking can be achieved through IoT-enabled devices, allowing companies to make timely adjustments to meet the fluctuating market demands.
Focusing on Customer-Centric Approach
At the core of a successful quick response strategy lies a customer-centric approach. This principle dictates that companies must tune their logistics strategies to satisfy the ever-changing needs and preferences of the end-user. By employing advanced demand forecasting techniques, businesses can accurately anticipate customer requirements and make timely adjustments in production, inventory management, and distribution, ultimately leading to higher levels of customer satisfaction.
Optimizing Inventory Management
Lastly, optimal inventory management is critical in ensuring an effective quick response strategy. This component involves striking the right balance between holding adequate stock levels to meet customer demands while minimizing the associated costs of storage, handling, and obsolescence. By employing sophisticated inventory management systems and adopting proven methodologies like just-in-time and lean inventory practices, businesses can significantly improve their logistics responsiveness.
In conclusion, a successful quick response strategy in logistics is built upon a solid foundation of agility, flexibility, collaboration, and integration, underpinned by technological advancements and customer-centricity. By optimizing inventory management and effectively leveraging these key principles, businesses can forge a robust supply chain capable of responding to market fluctuations on short notice, ensuring a competitive advantage in today's dynamic business landscape.

Assessing Key Performance Indicators
To measure the effectiveness and efficiency of quick response logistics initiatives, organizations can focus on assessing key performance indicators (KPIs). These KPIs provide tangible, data-driven insights into the performance of various logistics processes, which are vital for informed decision-making.
Evaluating On-Time Delivery Rates
One fundamental KPI involves evaluating on-time delivery rates. Organizations must track the percentage of orders that reach their destination within the agreed-upon time window. Higher on-time delivery rates signify an effective and efficient supply chain, ultimately leading to greater customer satisfaction.
Monitoring Order Accuracy
Accurate order fulfillment is another essential KPI for evaluating logistics efficiency. By analyzing the percentage of orders delivered correctly, organizations can detect potential issues in their order processing system. This verification, in turn, allows them to address the root cause of the problem, preventing recurring errors and improving overall efficiency.
Reviewing Order Cycle Time
Another useful KPI for organizations is the order cycle time, which is the period between receiving an order and delivering the products to customers. A short order cycle time indicates a fast and efficient logistics process, while a longer cycle time may signify bottlenecks, delays, or inefficiencies that need to be addressed.
Analyzing Transportation Costs
Evaluating transportation expenses plays a crucial role in measuring logistics efficiency. By gathering data related to transportation costs, including fuel, maintenance, and labor charges, organizations can identify areas for improvement and seek cost-effective solutions. Lower transportation expenses combined with a high level of service indicate a successful logistics initiative.
Measuring Inventory Turnover Ratio
Finally, the inventory turnover ratio serves as a significant KPI for evaluating the effectiveness of quick response logistics initiatives. This ratio measures how fast an organization can sell and replace its inventory within a given period. A high turnover ratio signifies that the organization can promptly respond to changes in demand, thus ensuring a more efficient supply chain.
In conclusion, assessing various KPIs, such as on-time delivery rates, order accuracy, order cycle time, transportation costs, and inventory turnover ratio, enables organizations to measure the effectiveness and efficiency of their quick response logistics initiatives. By continuously monitoring these indicators, organizations can address potential weaknesses, optimize their logistics processes, and stay competitive in an increasingly fast-paced market.

Factors Contributing to Quick Response Logistics
Supplier Network Management
A critical factor in achieving quick response logistics is efficient supplier network management, which involves establishing collaborative partnerships with suppliers to ensure effective communication, enhanced visibility, and timely deliveries, and procurement processes. Well-managed supplier networks can lead to reduced lead times and improved customer satisfaction.
Inventory Management Strategies
Effective inventory management is essential for quick response logistics. Businesses should adopt strategies such as just-in-time practices, which enable reducing the inventory holding costs and minimize stockouts, and demand-driven replenishment, focusing on actual customer demand rather than forecasting. Optimizing stock levels helps businesses react more swiftly to fluctuations in market demand.
Advanced Information Systems
Quick response logistics benefit greatly from advanced information systems for real-time data collection, analysis, and communication. Technologies such as radio-frequency identification (RFID) and barcode scanning facilitate real-time tracking of inventory levels and deliveries, enabling businesses to make more informed decisions and react promptly to changes in supply and demand. Moreover, integrating emerging technologies such as artificial intelligence and machine learning can further support data-driven decision-making and enhance forecasting accuracy.
Agile Organizational Structure
Organizational agility is crucial for businesses implementing quick response logistics. Having adaptable and flexible operations enables businesses to respond promptly to emerging trends and customer demands. Lean management practices and cross-functional teams can help organizations to achieve higher efficiency levels, minimize waste, and improve collaboration among departments, ultimately leading to faster response times in the supply chain.
Strategic Location of Warehousing and Distribution Centers
The strategic location of distribution centers and warehouses plays a vital role in ensuring quick response logistics. Locating facilities closer to customers or transportation hubs can significantly reduce delivery times, transportation costs, and overall lead times. This allows businesses to quickly respond to market fluctuations and deliver products to customers in a more timely manner.
In conclusion, quick response logistics represent a critical aspect of modern supply chain management. By focusing on efficient supplier network management, inventory management strategies, advanced information systems, agile organizational structures, and strategically locating distribution centers and warehouses, businesses can enhance their responsiveness to dynamic market conditions and changing customer demands, thus improving their competitive advantage.

Role of Automation in Logistics
Technology plays a crucial role in enhancing logistics systems by reducing human error and increasing efficiency. Automation, in particular, streamlines various logistical processes, such as inventory management and order fulfillment. By utilizing barcode scanners and automated storage and retrieval systems (ASRS), companies can reduce the time needed to locate and transport products within a warehouse.
Artificial Intelligence in Decision-Making
Integration of artificial intelligence (AI) in logistics allows for more accurate forecasting and decision-making. AI-powered software can analyze large amounts of data to optimize various factors, such as delivery routes, order quantities, and warehouse layouts. Additionally, machine learning algorithms can proactively identify potential bottlenecks or disruptions in the supply chain and suggest solutions before issues arise.
Use of Robotics in Material Handling
Incorporating robotics in logistics can expedite processes and improve performance. Robotic systems, such as automated guided vehicles (AGVs) and autonomous mobile robots (AMRs), assist in the movement and handling of materials with minimal human intervention. These technologies can also reduce workplace accidents and labor costs while improving overall warehouse productivity.
IoT for Better Supply Chain Visibility
The Internet of Things (IoT) enables greater visibility throughout the supply chain by providing real-time data on the location, condition, and status of goods in transit. IoT devices, such as GPS trackers and smart sensors, can monitor factors like temperature, humidity, and vibration, ensuring high-quality product delivery. Moreover, this constant flow of information allows for better decision-making, improved planning, and ultimately, enhanced customer satisfaction.
Blockchain Technology for Enhanced Security
Blockchain technology can facilitate secure and transparent transactions within logistics networks. As an immutable and decentralized digital ledger, blockchain maintains a verifiable record of every exchange and transaction, providing enhanced security and preventing fraud. This technology also has the potential to streamline documentation processes and eliminate discrepancies, leading to reduced costs and increased trust between supply chain partners.
In conclusion, the integration of technology within logistics operations has revolutionized the industry by automating manual tasks, improving accuracy, and increasing visibility. As AI, robotics, IoT, and blockchain continue to develop and mature, it is essential for companies to adapt and incorporate these solutions into their logistics strategies to maintain a competitive edge.

Quick Response Logistics Definition
Quick response logistics in retailing refers to the information technology-based concept that focuses on enhancing the supply chain's efficiency, flexibility, and responsiveness. This approach combines elements of technology and managerial strategies to streamline processes, reduce lead times, and ultimately improve customer satisfaction.
Core Components
Quick response strategies contain several key components, including data interchange, inventory management, and order management systems. Electronic data interchange (EDI) technology, for example, allows for seamless communication and data-sharing between retailers and their suppliers, reducing delays in the supply chain. This integration helps companies monitor inventory levels in real-time, supporting a lean inventory management approach and enabling faster response to market demands.
Role of Technology
Information technology plays a crucial role in quick response logistics implementation. Technologies such as radio frequency identification (RFID) and barcodes help in tracking and tracing products throughout the supply chain, providing retailers with real-time data on their inventory status. Additionally, sophisticated analytics tools and software platforms facilitate the analysis of data to optimize inventory levels, product allocation, and demand forecasting.
Benefits for Retailers
The adoption of quick response logistics offers several benefits to retailers. Primarily, it allows them to meet fluctuating consumer demands swiftly, reducing stock outages and overstock situations, which directly impacts customer satisfaction. Furthermore, it enables efficient inventory management by reducing holding and storage costs associated with large inventory volumes. Lastly, the increased visibility and communication within the supply chain promote collaborative decision-making between retailers and suppliers, fostering a more robust and resilient supply chain network.
Challenges and Future Trends
Despite its advantages, barriers to implementing quick response logistics persist. Small-scale retailers may face high initial investment costs associated with technology and infrastructure upgrades. Additionally, developing and maintaining efficient and agile supply chain operations require constant investment in ongoing employee training and development. However, as technology evolves and becomes more cost-effective, it is expected that a growing number of retail businesses will embrace quick response logistics strategies to remain competitive and responsive in an increasingly demanding market.

Role of Information Sharing in Quick Response Logistics
Effective information sharing is critical in quick response logistics, as it allows supply chain partners to exchange data, coordinate actions, and identify potential issues. Timely and accurate information exchange helps organizations make better decisions, optimize resources, and reduce operational costs. Sharing real-time data enables supply chain actors to act proactively to prevent delays or shortages, thus ensuring that the right products reach the customers on time and with minimum errors.
Communication as a Catalyst in Quick Response Logistics
Communication in quick response logistics refers to the active engagement and collaboration among all supply chain stakeholders. This includes suppliers, manufacturers, transporters, and customers. Through strong communication channels, organizations can establish trust, align goals, and enhance cooperation, which ultimately results in improved supply chain responsiveness and efficiency. Furthermore, active communication helps in preparing for uncertainties, like sudden demand changes or natural disasters, by allowing a fast and adaptable response based on the shared information.
Conclusion
In conclusion, information sharing and communication play a vital role in enhancing the effectiveness and efficiency of quick response logistics. These elements provide supply chain players with the necessary data and coordination capabilities to make fast, informed decisions, manage resources, and ensure that customer needs are met in a timely and cost-effective manner.

Efficient Utilization of Digital Platforms
Transportation management systems (TMS) and digital platforms have revolutionized how logistics operations manage quick response requirements. TMS enables operational efficiency by automating several functions, such as route planning, carrier selection, and shipment tracking. As a result, it leads to reduced lead times and increased customer satisfaction.
Real-Time Visibility and Communication
Digital platforms facilitate real-time visibility of a freight movement, which allows shippers, carriers, and recipients to actively monitor the shipment's status. This real-time communication capability ensures that logistics managers can quickly address potential issues, enhancing the overall decision-making process.
Predictive Analytics for Improved Efficiency
Additionally, transportation management systems employ advanced data analytics, which can help predict transport-related issues, such as shipment delays and carrier unavailability. These insights derived from data analysis enable logistics operators to make informed decisions, minimize errors, and optimize resource usage.
Integration with IoT and Blockchain Technology
Incorporating Internet of Things (IoT) and blockchain technology in TMS further strengthens its benefits by offering enhanced security and transparency in supply chain operations. IoT devices, such as sensors and GPS trackers, provide real-time data to monitor various aspects of transportation, while blockchain enables secure information sharing among stakeholders.
Seamless Collaboration among Stakeholders
Digital platforms help logistics providers collaborate effectively with their partners, suppliers, and customers. Such integration allows for the seamless exchange of critical information, reducing communication lags and enhancing overall operations. Moreover, it promotes data-driven decision-making, which is vital for quick response logistics.
Cost Savings and Sustainability
Finally, TMS enables logistics operation managers to optimize transportation costs by analyzing factors, such as carrier rates, distance, and fuel consumption. This cost optimization leads to greener and more sustainable logistics practices, making a positive environmental impact.
In conclusion, transportation management systems and digital platforms significantly contribute to quick response in logistics operations by enhancing communication, enabling real-time visibility, promoting data-driven decision-making, and fostering collaboration among stakeholders. Furthermore, the integration of advanced technologies, such as IoT and blockchain, results in secure and efficient supply chains, ultimately improving overall logistics performance.

Environmental Implications
Quick response logistics strategies facilitate the efficient movement of goods throughout global supply chains with a focus on reducing lead times and optimizing inventory levels. In the context of sustainability, these strategies may yield both positive and negative environmental implications.
Pros of Quick Response
Adopting quick response strategies may lead to reduced energy consumption and a subsequent decrease in greenhouse gas emissions through improved routing, planning, and consolidation of shipments. These reductions can be realized through various technological advancements, such as real-time monitoring of shipments, route optimization, and other data-driven methods that enable companies to fine-tune their transportation strategies.
Cons of Quick Response
On the other hand, quick response strategies may potentially exacerbate the environmental impact of logistics operations through a higher frequency of smaller, less efficient shipments. The need for speed can result in transportation reliant on faster but less sustainable modes, such as air freight, which produces significant amounts of greenhouse gas emissions per unit of cargo transported. Additionally, the increased transportation intensity may contribute to a surge in fuel consumption and air pollution.
Social Implications
The social implications of implementing quick response logistics strategies can also be seen in the realms of labor practices, consumer behavior, and local communities.
Labor Practices
Efficient logistics strategies may lead to job growth within the industry, creating new employment opportunities with the expansion of supply chain operations. However, the drive for efficiency can also result in work intensification and the casualization of labor, as companies seek to reduce costs by outsourcing certain logistics functions and shifting towards temporary, low-wage employment.
Consumer Behavior
From a consumer perspective, quick response strategies offer the promise of shorter lead times and increased product availability, ultimately reshaping consumer behavior by encouraging more frequent purchasing cycles. This, in turn, may exacerbate overconsumption, the generation of waste, and the depletion of natural resources.
Local Communities
The relocation of production facilities closer to major markets, favored within quick response strategies, could benefit local communities by creating job opportunities and revitalizing regional economies. Nonetheless, this spatial shift could also contribute to the homogenization of local cultures, given that multinational businesses often introduce and perpetuate standardized products and practices.
In conclusion, quick response logistics strategies can bring about both positive and negative environmental and social implications. Balancing these impacts requires a comprehensive and responsible approach that prioritizes sustainability at each stage of the supply chain. By adopting such balanced strategies, companies can drive innovation, protect the environment, and ensure social well-being, while meeting global demands for rapid, efficient logistics.

Understanding Quick Response Strategy in Logistics
Quick response strategy in logistics refers to a system that aims to reduce lead times within the whole production flow. It hinges on integrating information systems, streamlining supply chain processes, and accelerating freight operations. All parts of the supply chain, from suppliers to consumers, work in close collaboration to ensure real-time flow of information and quick decision making.
Influence of Quick Response on Business Growth
Often, a company's competitive advantage lies in its ability to provide their services on time. Therefore, a quick response strategy in logistics demonstrates clear benefits in business growth. First, it allows a company to meet customer demands promptly, resulting in improved customer satisfaction. Second, this strategy reduces the inventory holding cost as goods are transported faster.
Quick Response and Market Competition
Furthermore, quick response logistics enhance a company's market responsiveness, allowing it to adjust swiftly to changes in the consumer market. It increases reliability and competitiveness, ultimately driving business expansion and growth. Moreover, this strategy enables companies to forecast demand accurately, manage resources more effectively and reduce wastages.
Efficiency of Quick Response Strategy
A business model utilizing a quick response strategy often experiences a substantial increase in overall productivity and efficiency. Since operations are in real time, decisions are made faster which leads to increased operational efficiency. Consequently, the process offers a higher turnover rate, adding to the company's profit margins.
In sum, the quick response strategy in logistics, through its focus on reduced lead times and integrated information systems, contributes significantly to business growth. Its ability to enhance customer satisfaction, reduce costs, boost market responsiveness and streamline operational efficiency positions the company for higher profitability and sustainable growth.

Adaptability of Supply Chains
Quick response (QR) technology plays a pivotal role in facilitating the adaptation of supply chains to sudden market changes. This cutting-edge technology offers real-time data on intra-firm operations, inventory levels, customer trends, and market shifts, enabling companies to gauge market currents and respond swiftly.
Heightened Responsiveness
In this digital age, QR technology reduces the time lapse in transmitting market feedback to the supply chain. It ensures immediate response to sudden increases in demand, quickly adjusting operational activities. Such technology maximizes supply chain agility and minimizes the risk of excess or deficient inventory.
Improved Forecasting and Planning
QR technology is not just reactive but also predictive. It leverages advanced analytics, employing historical data to forecast upcoming market trends. This predictive analysis can help companies develop flexible supply chain strategies that prepare them for sudden market changes.
Real-time Decision-Making
Having real-time data at their disposal, companies can make improved and faster decisions. Quick response technology aids decision-makers in not just identifying potential disruptions, but also in creating an immediate action plan. This expedites the response time to unexpected market changes.
In conclusion, QR technology streamlines processes, enhances decision-making capability, and promotes agility in supply chains. It ensures supply chains can adapt easily and immediately to sudden shifts in the market, thereby providing a competitive advantage. With an ever-changing market environment, this capability becomes invaluable in maintaining efficiency, reducing costs, and enhancing customer satisfaction.

Boosting Customer Satisfaction
Quick response delivery systems play a crucial role in enhancing customer satisfaction. Fast delivery services often lead to instant customer gratification, thus fostering a feeling of satisfaction. Customers appreciate businesses that respect their urgency and respond quickly. Elevating the delivery speed escalates customers' perception of a business's service quality.
Building Long-term Relationships
Long-term relationships between businesses and customers are dependent on continuous customer satisfaction. Quick response delivery systems greatly contribute to achieving this goal. Through the provision of fast and efficient delivery services, businesses are able to exceed customer expectations. Consistency in rapid delivery instils trust and reliability among customers, leading to long-term relationships.
Customer Retention
The implementation of quick response delivery systems assists in customer retention. When businesses deliver on time or earlier than expected, it anchors a positive experience for customers. This satisfaction and trust developed over time can reinforce customer loyalty. Consequently, customers are more likely to continue patronizing the company and less likely to switch to competitors.
Competitive Advantage
Quick response delivery systems also provide a competitive edge in business. With the prevalence of immediate gratification in today's consumer behavior, businesses providing faster delivery have an advantage in a saturated market. These systems can distinguish a business from its competitors, leading to increased market share.
In conclusion, quick response delivery systems are powerful tools in promoting customer satisfaction and securing long-term relationships. They not only aid customer retention but also assist businesses in attaining a competitive edge. Considering the importance of customer relationships in business longevity, these systems pose as essential mechanisms for business growth.

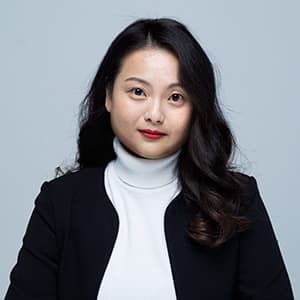
Yu Payne is an American professional who believes in personal growth. After studying The Art & Science of Transformational from Erickson College, she continuously seeks out new trainings to improve herself. She has been producing content for the IIENSTITU Blog since 2021. Her work has been featured on various platforms, including but not limited to: ThriveGlobal, TinyBuddha, and Addicted2Success. Yu aspires to help others reach their full potential and live their best lives.