Optimizing Inventory Control: An Examination of Safety Stock

Safety Stock Concept | Importance & Impact | Strategies & Considerations |
---|---|---|
Definition | Critical reservoir in inventory management, preventing stockouts. | Distinct from cycle stock and buffer stock. |
Reasons for Holding | Protects against unpredictability in supply and demand patterns. | Calibrations should align with broader strategic objectives. |
Influencing Factors | Determines ideal quantity, affecting response to demand variability and lead times. | Considerations include historic purchase patterns, service level metrics, and delivery performance scores. |
Benefits | Enhances customer service; insulates against market demand changes and associated perils. | Helps mitigate impact of supplier-side delays. |
Drawbacks | Potential financial constraints, product obsolescence, and inflated holding costs. | Balance required between preparedness and cost-efficiency. |
Balancing Strategies | Caters to fulfillment needs while considering financial implications. | Requires complex modelling taking into account various variables. |
Safety Stock Calculation | Determines optimal safety stock levels. | Factors considered - standard deviation of demand, desired service levels, and z-score. |
Technology & Safety Stock | Facilitates strategic optimization and future applications. | Continuous advancements shape the future application of safety stock. |
Resilience in Supply Chain | Ensures operational continuity, adaptable to unforeseen exigencies. | Key in curriculum for logistics management courses. |
Customer Satisfaction Metric | Safety stock increases customer loyalty through uninterrupted service. | Takes into consideration an instantaneous response to customer needs. |
In an intricate tapestry of supply chain management, safety stock holds a pivotal position in the architecture of inventory control. As businesses strive to meet the demands of a dynamic marketplace, the calibration of safety stock levels becomes a cornerstone of operational efficiency. The essentiality of safety stock in inventory management sistemas as a buffer against the unpredictability of supply and demand.
This academic exploration will delve into the multifaceted aspects of safety stock, elucidating its definition, mechanics, and strategic optimization, with an emphasis on benefits, challenges, and technological advancements shaping its future application.
Understanding Safety Stock
Definition of safety stock
Safety stock serves as a critical reservoir in the inventory management equation, positioned to avert the ramifications of stockouts. This safeguard is a quantifiable allotment that insulates an enterprise's operations from the vicissitudes of supply chain disruptions.
While intertwined with overarching inventory management strategies, safety stock is distinctly differentiated from cycle stock, which caters to normal demand patterns, and buffer stock, which specifically addresses short-term variances. The alignment of safety stock with the strategic objectives of logistics management courses often becomes a focal point of curriculum, equipping scholars with the tools to navigate the intricacies of inventory control.
Reasons for holding safety stock
Entities procure safety stock primarily as a fortification against the twin uncertainties of demand and supply. The fluctuations in customer procurement patterns, matched with potential unpredictability among suppliers, mandate a ready reserve.
This reserve acts as a fortification, ensuring continuity of service and fostering resilience in the face of unforeseen exigencies. The acuity of supply chain managers, often honed by certificate courses online, is pivotal in discerning the appropriate magnitude of safety stock warranted for any given operation.
Uncovering Strength in Decision Making Using Sensitivity Analysis
Analyzing the Critical Role of Cold Chain Logistics in the Industry
Factors influencing safety stock levels
Deciphering the appropriate quantity of safety stock involves a multitude of considerations. Lead Time—the elapsed interval between order placement and receipt—bears significant weight in this equation. Moreover, the capricious nature of demand variability introduces another layer of complexity, compelling a careful analysis of historic purchase patterns. Service Level metrics and Delivery Performance scores also inform this calibration, prescribing the degree of buffer necessary to achieve desired customer satisfaction standards.
An anecdotal illustration of safety stock might involve a retailer who, having analyzed sales during holiday peaks and supplier delays, maintains a calculated reserve of a popular toy to ensure fulfillment of any unanticipated demand surges.
Benefits and Drawbacks of Safety Stock
Benefits of safety stock
The institution of safety stock harbors substantial advantages. It empowers enterprises to contend with unexpected market demand and to prevent the perils associated with stockouts and consequent backorders.
Customer service sees tangible improvements when companies leverage safety stock to address instantaneous needs without delay, enabling the constructor of customer loyalty. Furthermore, the incorporation of safety stock buffers the impact of lead time variations, precluding the potential operational disruptions attributable to supplier-side delays.
Drawbacks of safety stock
Notwithstanding the merits, safety stock sustains intrinsic limitations. Capital tied up in unnecessary excess can inflate holding costs, with resources languishing dormant in warehouses. This capital, otherwise employed in revenue-generating activities, can impinge on financial liquidity.
In parallel, overstocking carries the peril of product obsolescence—items may depreciate or become outdated, leading to unsellable inventory. Therefore, identifying the equilibrium point in safety stock levels where benefits overshadow drawbacks is a managerial tightrope walk of strategic importance.
System Approach To Logistics Management For İnformation Flow Coordination
Advantages Of İnformation Technology İn Logistics İndustry
Balancing safety stock levels for optimal benefits
The quest for balance in safety stock levels is a relentless pursuit—a dynamic interplay between cost-efficiency and preparedness. Systematic approaches for equilibrium-seeking involve complex modeling that takes into account the aforementioned variables. Striking this balance channels into ensuring material readiness for fulfillment needs while also considering the financial constraints that excess stocking imposes.
Calculating Safety Stock
Formulae for safety stock
Safety stock calculation manifests through various formulae, each dissecting different aspects of inventory dynamics. At the core of these formulae lie elements such as standard deviation of lead time and demand, desired service levels, and the z-score or the statistical measure of service level confidence. Each factor's quantification amalgamates into a holistic portrayal of the requisite safety stock—a representation of statistics harnessed for operational fortitude.
Factors to consider when calculating safety stock
When embarking upon the safety stock calculation, meticulous consideration is paramount. Factors including the standard deviation of historical demand data, lead time variability, and the company's risk tolerance levels in terms of service level objectives come into play. Each of these factors feeds into the computational matrix, dictating the final safety stock figure.
Example calculation of safety stock
Envision a scenario in which a company desires a service level of 95%, with a lead time standard deviation of one day and daily demand standard deviation of 10 units. By applying a suitable formula, the safety stock can be calculated to meet these specified parameters, thereby rendering a numerical representation of the inventory buffer required to maintain the 95% service level.
Strategies for Optimizing Safety Stock
Just in Time (JIT) strategy
The Just in Time inventory approach epitomizes the lean philosophy, necessitating precise coordination and finely-tuned processes to minimize safety stock. JIT's core tenet lies in the synchronization of supply with demand, thus negating the need for large safety stock holdings. However, its successful implementation pivots on the near-perfect predictability of supply and demand—an ideal that is often elusive in the tumultuous terrain of global trade.
Vendor Managed Inventory (VMI)
Under VMI paradigms, suppliers assume stewardship of inventory levels, optimizing safety stock according to a mutually agreed framework. This collaboration yields a streamlined supply chain ecosystem, with vendors leveraging their insights and operational competencies to safeguard their clients' inventory health.
Use of technology and inventory management systems
Advances in technology, particularly inventory management systems, have revolutionized the science of safety stock optimization. These platforms harness real-time data, affording unprecedented visibility and agility in inventory dynamics. Drawing on perpetual analytics, these systems facilitate a proactive rather than reactive approach to safety stock maintenance, enabling continuous alignment with evolving market forces.
The Future of Safety Stock
The role of technology in predicting safety stock
The advent of AI and machine learning heralds a paradigm shift in predicting and managing safety stock. By harvesting the power of big data, predictive analytics extends the horizons of accuracy in anticipating demand cycles, thus optimizing inventory efficiency. Driven by algorithms that learn and adapt, the future of safety stock is one characterized by precision and responsiveness, underpinned by intelligent technology.
Safety stock in the era of e-commerce and omnichannel retail
E-commerce and omnichannel retailing intensify the complexities of inventory management—challenging traditional safety stock doctrines with instantaneous, multipoint demands. In response, the calibration of safety stock must incorporate an intricate web of distribution channels, embodying flexibility to cater to diverse consumer touchpoints and fulfillment options.
Case studies highlighting successful safety stock management
Excavating the annals of supply chain success stories yields a treasure trove of insights into prudently managed safety stock. Case studies from leading industry players, whose capacity to deftly navigate the balance of stock availability against financial prudence, serve as educational exemplars. These chronicles embody the principles imparted through rigorous logistics management courses, demonstrating the tangible benefits of adept safety stock management.
The reinforcement of safety stock as an integral element of inventory management is incontrovertible—serving not merely as an operational tool but as a competitive differentiator. In closing, it is incumbent upon businesses to champion the effective management of their safety stock levels—an endeavor that assures not only enhanced productivity but palpable profitability. Embracing this imperative, coupled with the judicious application of technology and continuous recalibration, positions enterprises to thrive amidst the fluidity of global commerce.

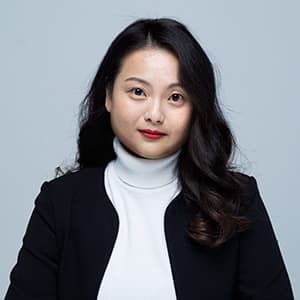
Yu Payne is an American professional who believes in personal growth. After studying The Art & Science of Transformational from Erickson College, she continuously seeks out new trainings to improve herself. She has been producing content for the IIENSTITU Blog since 2021. Her work has been featured on various platforms, including but not limited to: ThriveGlobal, TinyBuddha, and Addicted2Success. Yu aspires to help others reach their full potential and live their best lives.