Optimizing Logistics for Order Postponement

Introduction
Topic | Description | Benefits |
---|---|---|
Order Postponement | Delaying or splitting an order into multiple parts for future delivery | Allows customer flexibility in their order; can help businesses manage inventory |
Reasons for Postponement | Rescheduling requirements, product unavailability | Adjusts for changes in schedule or product supply; ensures customer needs are met |
Supply Chain Communication | Informing all parties of order change | Prevents errors in order fulfillment; keeps everyone in the loop |
New Delivery Date | Establishing a later date for order delivery | Provides a clear timeline for all involved; helps plan for order fulfillment |
Customer Notification | Updating the customer on changes to the order | Maintains good customer service; keeps customer informed |
Inventory Management | Managing stock to accommodate postponed orders | Prevents overstocking or shortages; maintains a smooth supply chain |
Logistics Optimization | Improving the logistics process with order postponement in mind | Prevents errors; maintains efficiency and effectiveness |
Third-party Logistics Providers | Involving intermediaries in the logistics process | Relieves workload; brings in expert assistance |
Order Changes | Adjusting the order details based on postponement | Accommodates customer's needs; ensures correct product is delivered |
Postponement Planning | Identifying potential need for order postponement ahead of time | Predicts future stock requirements; allows smoother operational flow |
I still remember the day when I was waiting eagerly for my new laptop to arrive. The excitement was palpable, and I had cleared my entire weekend to set it up. But then, an unexpected email arrived: "Your order has been postponed due to supply chain delays." At first, I was frustrated, but soon I realized the complexities behind such postponements.
In today's fast-paced world, order postponement isn't just a logistical hiccup; it's a strategic tool in supply chain management. It's fascinating how this concept plays a pivotal role in ensuring customers eventually receive what they need, even if it means waiting a little longer.
Introduction
Definition of Order Postponement
Reasons for Order Postponement
Optimizing Logistics for Order Postponement
Conclusion
In this article, we'll delve deep into the nuances of order postponement, exploring its definition, reasons, and how businesses can optimize their logistics processes to handle it effectively. Whether you're a supply chain enthusiast or someone curious about how your online orders reach you, there's something here for everyone.
Understanding Order Postponement
What is Order Postponement?
At its core, order postponement refers to the intentional delay or splitting of an order into multiple deliveries at later dates. This strategy allows businesses to manage inventory more efficiently and respond flexibly to customer needs. Instead of rushing to fulfill an order that might not be optimal in terms of stock availability or delivery logistics, companies postpone certain aspects to ensure better service quality.
Real-Life Scenarios
Imagine you're hosting a big family reunion, and you've ordered several items online: decorations, catering supplies, and gifts. Some items are available immediately, while others are out of stock or will arrive later due to shipping constraints. Rather than delaying the entire order, the company might send the available items first and postpone the rest.
This approach offers several benefits:
Customer Satisfaction: You get essential items on time, ensuring your event isn't jeopardized.
Inventory Management: The company can manage stock levels without overextending resources.
Logistical Efficiency: Splitting deliveries can optimize routes and reduce shipping costs.
Reasons Behind Order Postponement
Understanding why order postponement occurs helps in appreciating its strategic value.
1. Supply Chain Disruptions
In an interconnected global economy, disruptions are inevitable. Factors like natural disasters, political unrest, or pandemics (remember COVID-19?) can halt production or delay shipping. Companies might postpone orders to navigate these uncertainties.
2. Inventory Management
Sometimes, certain products are out of stock or in limited supply. By postponing orders, businesses can replenish stock without disappointing customers with cancellations.
3. Customized Products
For products that require customization, additional time might be needed. Postponing the order ensures that the product meets the customer's specifications without rushing the process.
4. Consolidated Shipping
To reduce shipping costs and environmental impact, companies might delay orders to consolidate shipments. This strategy can lead to significant savings and more sustainable operations.
5. Regulatory Compliance
Certain goods require compliance with regulations, like safety certifications or import/export laws. Postponing orders allows time to navigate these requirements.
The Impact on Customers and Businesses
Customers' Perspective
From a customer's viewpoint, order postponement can be both a boon and a bane.
Advantages:
- Receiving Partial Orders: Getting some items earlier can be beneficial.
- Enhanced Product Quality: Delays might ensure better quality or customization.
Disadvantages:
- Inconvenience: Waiting longer can be frustrating.
- Uncertainty: Lack of clear communication can lead to dissatisfaction.
Businesses' Perspective
For businesses, the stakes are high.
Planning for order postponement is the key to optimizing logistics.

Advantages:
- Optimized Supply Chain Management Process Tips: By postponing orders, companies can implement strategies to optimize their supply chains.
- Cost Savings: Efficient inventory and logistics management can reduce operational costs.
- Flexibility: Companies can adapt to changing market conditions.
Disadvantages:
- Customer Dissatisfaction: Poor handling can damage reputation.
- Complexity: Managing postponed orders adds to operational complexity.
Optimizing Logistics for Order Postponement
Now, let's get to the crux: How can businesses optimize their logistics when dealing with order postponement?
1. Effective Communication is Key
One of the most critical aspects is keeping all parties informed.
Notify Customers Promptly: As soon as a delay is anticipated, inform the customer.
Provide Clear Timelines: Offer realistic delivery dates to manage expectations.
Utilize Multiple Channels: Email, SMS, and in-app notifications ensure the message is received.
2. Collaborate with Supply Chain Partners
Coordination among suppliers, manufacturers, and logistics providers is essential.
Shared Information Systems: Implement platforms where all parties can access real-time data.
Joint Planning Sessions: Regular meetings can preempt potential delays.
Align Objectives: Ensure everyone understands the importance of timely deliveries.
3. Invest in Technology
Modern technology can make a world of difference.
Inventory Management Systems: Track stock levels accurately.
AI and Predictive Analytics: Anticipate demand and potential disruptions.
Automation: Streamline warehousing and distribution processes.
4. Flexible Logistics Solutions
Adopt logistics strategies that accommodate changes.
Multiple Warehousing Locations: Reduce shipping times by storing products closer to customers.
Alternative Shipping Methods: If one route is blocked, have backups like air freight instead of sea.
Dynamic Routing: Adjust delivery routes in real-time based on traffic or weather conditions.
5. Customer-Centric Policies
Putting the customer first can mitigate negative impacts.
1- Offer Incentives: Discounts on future purchases or free shipping can soothe frustrations.
2- Easy Cancellations and Returns: Provide hassle-free processes if customers choose to cancel.
3- Personalized Updates: Tailor communications to individual customer preferences.
6. Training and Development
Equip your team to handle postponements effectively.
Regular Training Sessions: Keep staff updated on best practices.
Empower Decision-Making: Allow frontline employees to make calls that enhance customer satisfaction.
Feedback Mechanisms: Encourage staff to share insights from customer interactions.
7. Implementing Lean Principles
Adopting lean management can streamline operations.
Eliminate Waste: Remove non-value-adding activities.
Continuous Improvement: Regularly assess and improve processes.
Value Stream Mapping: Visualize processes to identify bottlenecks.
8. Risk Management Strategies
Prepare for the unexpected.
Risk Assessments: Identify potential supply chain risks regularly.
Diversify Suppliers: Don't rely on a single source for critical components.
Buffer Stocks: Maintain safety stock levels for high-demand items.
Personal Anecdote: Lessons from the Field
Working in the retail sector a few years back, I faced a significant challenge when a popular product was suddenly out of stock due to unforeseen supplier issues. Customers were eager, and cancellations started pouring in. We decided to postpone orders rather than cancel them, offering a small gift as a token of appreciation for their patience.
Surprisingly, many customers responded positively. Not only did they wait for the product, but we also received appreciative messages for our transparency. This experience taught me the power of effective communication and customer-centric approaches in turning potential crises into opportunities.
The Future of Order Postponement
As technology and consumer behaviors evolve, so will strategies around order postponement.
Embracing AI and Machine Learning
Predictive Demand Forecasting: Anticipate spikes in demand to prevent stockouts.
Automated Communication Bots: Keep customers informed in real-time.
Sustainable Practices
Eco-Friendly Shipping: Postponing orders to consolidate shipments reduces carbon footprints.
Sustainable Packaging: Extra time allows for sourcing environmentally friendly materials.
Personalization
Customized Delivery Options: Allow customers to choose when and how they receive orders.
Adaptive Supply Chains: Tailor operations based on individual customer data.
Conclusion
Order postponement, while sometimes seen as a setback, can be a strategic tool in optimizing supply chain management. By understanding its causes and implementing effective strategies, businesses can turn potential challenges into advantages. The key lies in communication, collaboration, and putting the customer first.
The next time you experience a delayed order, consider the intricate dance happening behind the scenes. And if you're a business navigating these waters, remember that with the right approach, you can not only optimize your supply chain but also build stronger relationships with your customers.
References
1- Christopher, M. (2016). Logistics & Supply Chain Management. Pearson Education Limited.
2- Simchi-Levi, D., Kaminsky, P., & Simchi-Levi, E. (2008). Designing and Managing the Supply Chain: Concepts, Strategies, and Case Studies. McGraw-Hill.
3- Ivanov, D., Tsipoulanidis, A., & Schönberger, J. (2019). Global Supply Chain and Operations Management. Springer International Publishing.
4- Slack, N., Brandon-Jones, A., & Johnston, R. (2013). Operations Management. Pearson Education Limited.
5- Coyle, J. J., Langley, C. J., Novack, R. A., & Gibson, B. J. (2017). Supply Chain Management: A Logistics Perspective. Cengage Learning.
Incorporating effective order postponement strategies can significantly enhance your business operations. So, why not give these optimize supply chain management process tips a try?
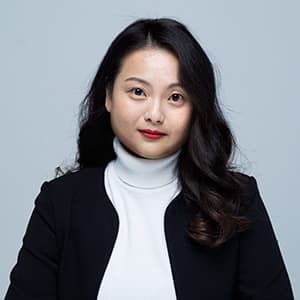
Yu Payne is an American professional who believes in personal growth. After studying The Art & Science of Transformational from Erickson College, she continuously seeks out new trainings to improve herself. She has been producing content for the IIENSTITU Blog since 2021. Her work has been featured on various platforms, including but not limited to: ThriveGlobal, TinyBuddha, and Addicted2Success. Yu aspires to help others reach their full potential and live their best lives.