Optimizing Efficiency: A Comprehensive Examination of Batch Picking

In the modern era of supply chain management, efficiency and precision have become paramount for businesses seeking to maintain a competitive edge. Central to the realization of these objectives is batch picking, a method employed within warehouse and distribution center operations to promote better utilization of resources and enhance order fulfillment processes. In setting the stage for a comprehensive examination of batch picking, it is vital to acknowledge its importance in fostering streamlined workflows that can make significant contributions to organizational success.
As industries continue to evolve and customer demands become more complex, batch picking emerges as a pivotal component in navigating the intricacies of supply chain logistics, meriting an in-depth analysis of its concept, importance, and best practices.
Understanding the Concept of Batch Picking
Batch picking refers to an order picking method where multiple orders are processed simultaneously, allowing the picking of items in an aggregated manner. This technique often proves to be profoundly beneficial when multiple orders contain the same item or a set of common items. The quintessence of batch picking is the ability to minimize the number of trips to and from various pick locations, thereby significantly expanding picking efficiency.
The mechanics of batch picking revolve around compiling a list of the items needed across a batch of orders. The process begins with the formulation of this consolidated pick list, which directs the picker to collect the cumulative quantity of each item required, rather than the quantity needed for individual orders. In this way, items are picked in bulk and subsequently sorted into separate orders at a designated consolidation area.
How this system functions in practice involves the synchronization of orders that exhibit overlaps in their item requirements. Through a carefully orchestrated ballet of resource allocation, pickers traverse the warehouse following a strategic pathway that minimizes redundant movements. Grounded in the principles of economy of motion, batch picking eradicates inefficiencies, demonstrating the core philosophy of doing more with less. This blueprint is supported by meticulously calibrated procedures that ensure the smooth execution of the picking routine.
Importance of Batch Picking in Order Fulfillment
The pulse of batch picking resides in its unparalleled potential to heighten work efficiency. By embracing this methodology, operations can leverage the simultaneous handling of several orders, effectively reducing labor costs and expediting the picking process. It's not merely a theoretical proposition, as real-world deployments of batch picking regularly demonstrate a marked amplification in workflow productivity. For instance, a fulfillment center that integrates batch picking could see a substantial reduction in the time required to process a set of orders, versus addressing each separately.
Within the sphere of time and cost effectiveness, batch picking rises to prominence as a strategic enabler of operational thriftiness. It's a straightforward equation: fewer trips across the picking area translate into less time spent, which in turn leads to cost savings. This methodology doesn't just conserve fiscal resources; it also capitalizes on time as a valuable asset. By collapsing the time frame needed for order fulfillment, organizations can meet tighter shipping windows and bolster customer satisfaction.
Minimization of errors is another hallmark of this picking strategy. Each order picking method has its potential pitfalls, but batch picking streamlines the complex dance of supply chain activities, serving to reduce the frequency of inaccuracies. This is largely due to the reduction in complexity that batch picking affords—by condensing the logistical variables into manageable clusters of activity, there is a smaller margin for error, ultimately leading to a more reliable fulfillment process.
Decoding the Process and Benefits of Return Merchandise Authorization (RMA)
Crucial Aspects and Importance of Freight Rate Audit in Supply Chain
Different Approaches to Batch Picking
Discrete Picking
Discrete picking, the practice of picking items for a single order before moving to the next, is the antithesis to batch picking. It's characterized by a linear approach—complete one order, then start another. The merits of discrete picking lie in its simplicity and its direct alignment with straightforward, small-scale operations. However, its demerits are illuminated in settings with high order volumes, where the repetition of visiting the same locations for different orders can amount to a considerable waste of time and energy.
Zone Picking
Zone picking partitions the warehouse into specific areas, with pickers assigned to each zone. They are responsible for picking all items within their zone for every order that passes through. This method can be used in conjunction with batch picking for further optimization. It's especially beneficial for large warehouses with a vast assortment of items, as it aids in reducing picker travel time and increasing specialization. Conversely, the need for sorting items into individual orders post-picking is its primary shortcoming, potentially introducing a bottleneck if not properly managed.
Wave Picking
Wave picking is often perceived as a hybrid between batch and zone picking. It involves organizing the picking schedule into distinct waves, often aligning with shipping schedules or the prioritization of certain orders. This can help manage labor allocation and ensures orders are picked in time for their respective dispatch waves. Ideal for operations that have variable peaks in demand, wave picking ensures efficiency without overburdening the system. It does, however, require careful planning and a well-coordinated warehouse management system to execute effectively.
Implementing Batch Picking: Best Practices
When contemplating the adoption of batch picking within the architecture of a warehouse operation, it's crucial to lay the foundations with meticulous planning and organizing. Establishing optimized pick paths, accurate inventory management, and the deployment of skilled personnel are ingredients in crafting a successful batch picking strategy. Training and cross-training workers to be proficient in the nuances of batch picking are also essential in extracting maximum advantage from the initiative.
Technological tools represent a powerful lever in the mechanics of batch picking. The utilization of warehouse management systems (WMS), barcode scanners, and pick-to-light systems can act as force multipliers, streamlining the batch picking process. By incorporating technological aids, businesses can expedite the picking process, enhance accuracy, and present workers with real-time data to make informed decisions on the fly.
Challenges & Limitations of Batch Picking
Despite its numerous advantages, batch picking is not immune to challenges. The primary potential hurdle is the complexity that comes with scaling operations. As the order volume grows, so does the risk of complications in managing larger batches and maintaining accuracy. There may also be a point where the benefits of time-saving begin to diminish if the sorting process is not well-configured.
The discussion on the limitations of batch picking would be incomplete without addressing the need for a space conducive to sorting post-pick activities. If the throughput exceeds the available area for order consolidation, it can lead to congestion and reduced productivity.
In synthesis, batch picking is a critical aspect of supply chain efficiency, offering several benefits capable of significantly bolstering business operations. However, this method requires careful implementation and a clear understanding of its nuances. The future of batch picking is inextricably tied to advancements in technology, such as robotics and AI, which promise to evolve and refine order picking strategies even further—ushering in new levels of accuracy, speed, and cost-effectiveness.
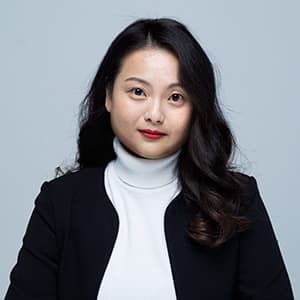
Yu Payne is an American professional who believes in personal growth. After studying The Art & Science of Transformational from Erickson College, she continuously seeks out new trainings to improve herself. She has been producing content for the IIENSTITU Blog since 2021. Her work has been featured on various platforms, including but not limited to: ThriveGlobal, TinyBuddha, and Addicted2Success. Yu aspires to help others reach their full potential and live their best lives.