Managing Inventory Costs: The Hidden Costs of Supply Chain Management

Inventory Cost Category | Explanation | Strategies for Management |
---|---|---|
Inventory Purchase | The cost of products themselves, which can vary depending on the product type, the quantity purchased, and the terms of the supplier’s agreement. | Negotiate better terms with suppliers, buy in bulk for discounts, and make wise purchasing decisions based on demand forecasting. |
Inventory Storage | The cost of storage space for the inventory which could include rent for a warehouse or security costs. | Optimize warehouse space usage, consider dropshipping or lean inventory methods, install security measures to prevent theft or damage. |
Borrowing Money for Inventory | The cost of interest when money is borrowed to pay for inventory. Generally seen in startup businesses or those expanding rapidly. | Ensure adequate capital or working capital management, consider vendor financing or trade credits. |
Labor Costs | The costs associated with paying employees to move, store, handle, and manage the inventory. | Automation, efficient staff management, training programs, or use of warehouse management systems. |
Insurance Costs | Businesses must pay for insurance to protect their inventory from theft, damage or other losses. | Monitor industry trends for competitive rates or consider self-insurance if scale permits. |
Managing Shrinkage | Inventory loss due to theft, damage, or other causes, causing reduced profits and potential customer dissatisfaction. | Install security cameras or hire security guards, conduct regular audits, implement stringent inventory control systems. |
Managing Expiration | Loss due to products stored for too long, causing a loss of profits. | Strict tracking of expiration dates, usage of First-In-First-Out (FIFO) system, regular inventory turnover. |
Overstocking Costs | Money tied up in inventory that’s just sitting on the shelves and not selling, which can cause cash flow problems. | Accurate demand forecasting, adjust reordering strategies, seasonal inventory planning. |
Understocking Costs | Loss of potential sales, customer dissatisfaction, and marketplace penalties due to stockouts. | Strengthen supplier relationships, real-time inventory monitoring, safety stock inventory. |
Opportunity Costs | Costs of missed opportunities due to money being tied up in inventory. | Balanced inventory investment, diversify product offerings, consider Just-In-Time (JIT) inventory management. |
Businesses must be aware of the shelf life of their products and keep track of expiration dates. They must also be mindful of any shrinkage that may occur due to theft or damage and take appropriate steps to prevent it. In conclusion, inventory costs are essential to any business, but they can be challenging to manage.
Companies must pay for purchasing and storing inventory and any associated labor costs. They may also need to borrow money to pay for the list, which comes with a price. Finally, businesses must be aware of shrinkage and expiration and take steps to prevent it.
Introduction
Inventory Costs
Borrowing Money to Pay for Inventory
Other Costs of Inventory Management
Managing Shrinkage and Expiration
Introduction: Inventory costs are essential to any business but can be challenging to manage. Keeping products in inventory requires money and resources and, if not handled properly, can become a significant expense. This article will discuss the costs of inventory management, including borrowing money to pay for inventory, other costs associated with inventory management, and strategies for managing shrinkage and expiration.
Inventory Costs
The most obvious cost of inventory is the cost of the products themselves. If a business purchases inventory from a supplier, it must pay for the products before they can be sold. This cost can vary depending on the product type, the quantity purchased, and the terms of the supplier’s agreement. In addition, businesses must also pay for the storage of their inventory. This could include rent for a warehouse or the cost of keeping the inventory in a secure location.
Borrowing Money to Pay for Inventory
In some cases, businesses may need to borrow money to pay for their inventory. This is often the case when a business starts and needs more money to pay for the inventory upfront. Borrowing money to pay for inventory can be beneficial in the short term, allowing businesses to purchase more than they could otherwise afford. However, borrowing money to pay for inventory also comes with a cost. Businesses must pay the loan with interest, which can add up over time.
Other Costs of Inventory Management
Maximizing Inventory Costs: Tips for Supply Chain Management
Connecting Supply Chain Communities: How Culture Impacts Supply Chain Management
In addition to the cost of purchasing and storing inventory, businesses must also pay for the labor associated with managing inventory. This could include paying employees to move and store inventory or to keep track of inventory levels. Businesses must also pay for insurance to protect their inventory from theft, damage, or other losses.
Managing Shrinkage and Expiration
Managing shrinkage and expiration is one of the most important aspects of inventory management. Shrinkage is inventory loss due to theft, damage, or other causes. This can be a high cost to businesses, reducing their profits and leading to customer dissatisfaction. To reduce shrinkage, businesses must take steps to secure their inventory, such as installing security cameras or hiring security guards.
Expiration is another issue businesses must manage. Products stored for too long can expire or become outdated, resulting in a loss of profits. To avoid this, businesses must keep track of the expiration dates of their products and ensure that they are rotated regularly.
Conclusion: Inventory costs are essential to any business, but they can be difficult to manage. Keeping products in inventory requires money and resources and, if not managed properly, can become a major expense.
This article has discussed the costs of inventory management, including borrowing money to pay for inventory, other costs associated with inventory management, and strategies for managing shrinkage and expiration. By understanding the costs associated with inventory management, businesses can take steps to reduce their costs and maximize their profits.
The cost of managing inventory is often invisible, but it can be the difference between success and failure in supply chain management.

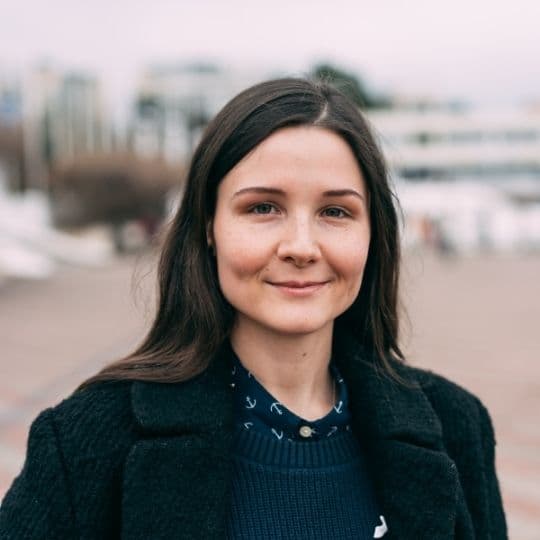
I am Amara Weiss and for many years I have worked in the field of education, specifically in the area of technology. I firmly believe that technology is a powerful tool that can help educators achieve their goals and improve student outcomes. That is why I currently work with IIENSTITU, an organization that supports more than 2 million students worldwide. In my role, I strive to contribute to its global growth and help educators make the most of available technologies.