In today's fast-paced and highly competitive business environment, lean logistics has emerged as a game-changing approach to streamlining supply chain operations. By embracing the principles of lean thinking, organizations can unlock unprecedented levels of efficiency, agility, and customer satisfaction. As someone who has witnessed the transformative power of lean logistics firsthand, I am excited to share my insights and experiences on this fascinating topic.
At its core, lean logistics is all about eliminating waste and maximizing value. It is a philosophy that challenges us to rethink every aspect of our supply chain, from sourcing raw materials to delivering finished products to customers. By identifying and eliminating non-value-adding activities, we can create a more streamlined and efficient logistics process that delivers superior results.
One of the key benefits of lean logistics is its ability to reduce lead times and improve responsiveness to customer demands. In today's world, customers expect faster and more reliable delivery than ever before. By implementing lean principles such as just-in-time delivery and continuous flow, we can significantly reduce the time it takes to get products to market. This not only enhances customer satisfaction but also helps to reduce inventory costs and improve cash flow.
Another important aspect of lean logistics is its focus on continuous improvement. Rather than settling for the status quo, lean organizations are always looking for ways to optimize their processes and eliminate waste. This requires a culture of experimentation, collaboration, and learning. By empowering employees to identify and solve problems, we can create a more agile and adaptive logistics operation that can quickly respond to changing market conditions.
Of course, implementing lean logistics is not without its challenges. It requires a significant shift in mindset and a willingness to embrace change. Many organizations struggle with the idea of letting go of traditional logistics practices and embracing a more flexible and responsive approach. However, as the examples of successful lean logistics implementations demonstrate, the benefits far outweigh the challenges.
One such example is the case of Toyota, the company that pioneered the lean manufacturing approach. Toyota's logistics operation is a marvel of efficiency and precision, with a just-in-time delivery system that ensures that parts and materials arrive exactly when they are needed. This has allowed Toyota to reduce inventory levels, improve quality, and respond quickly to changes in customer demand. As Liker (2004) notes in his book "The Toyota Way," Toyota's success is built on a foundation of continuous improvement and respect for people, two key principles of lean thinking.
Technologies For Enhancing Supply Chain Visibility İnterview Strategies
Long Tail Keyword: Decision Support Systems For Efficient Production And Distribution Planning
Another example of lean logistics in action is the case of Amazon, the world's largest online retailer. Amazon has built a logistics operation that is the envy of the industry, with a vast network of fulfillment centers, delivery vehicles, and technology systems that enable it to deliver products to customers faster and more efficiently than ever before. By embracing lean principles such as standardization, visual management, and continuous flow, Amazon has been able to create a logistics operation that is both highly efficient and highly responsive to customer needs.
However, it is important to note that lean logistics is not a one-size-fits-all solution. Every organization has its own unique challenges and opportunities, and what works for one company may not work for another. As Myerson (2012) points out in his book "Lean Supply Chain and Logistics Management," lean logistics requires a customized approach that takes into account the specific needs and constraints of each organization.
One of the key differences between lean logistics and traditional logistics is the focus on value creation. Traditional logistics tends to prioritize cost reduction above all else, often at the expense of customer service and responsiveness. Lean logistics, on the other hand, recognizes that value is defined by the customer, and that the ultimate goal of any logistics operation should be to deliver that value as efficiently and effectively as possible.
To achieve this goal, lean logistics relies on a range of strategies and tools, including value stream mapping, kaizen events, and 5S workplace organization. These tools help organizations to visualize their logistics processes, identify areas for improvement, and implement changes that eliminate waste and enhance value creation.
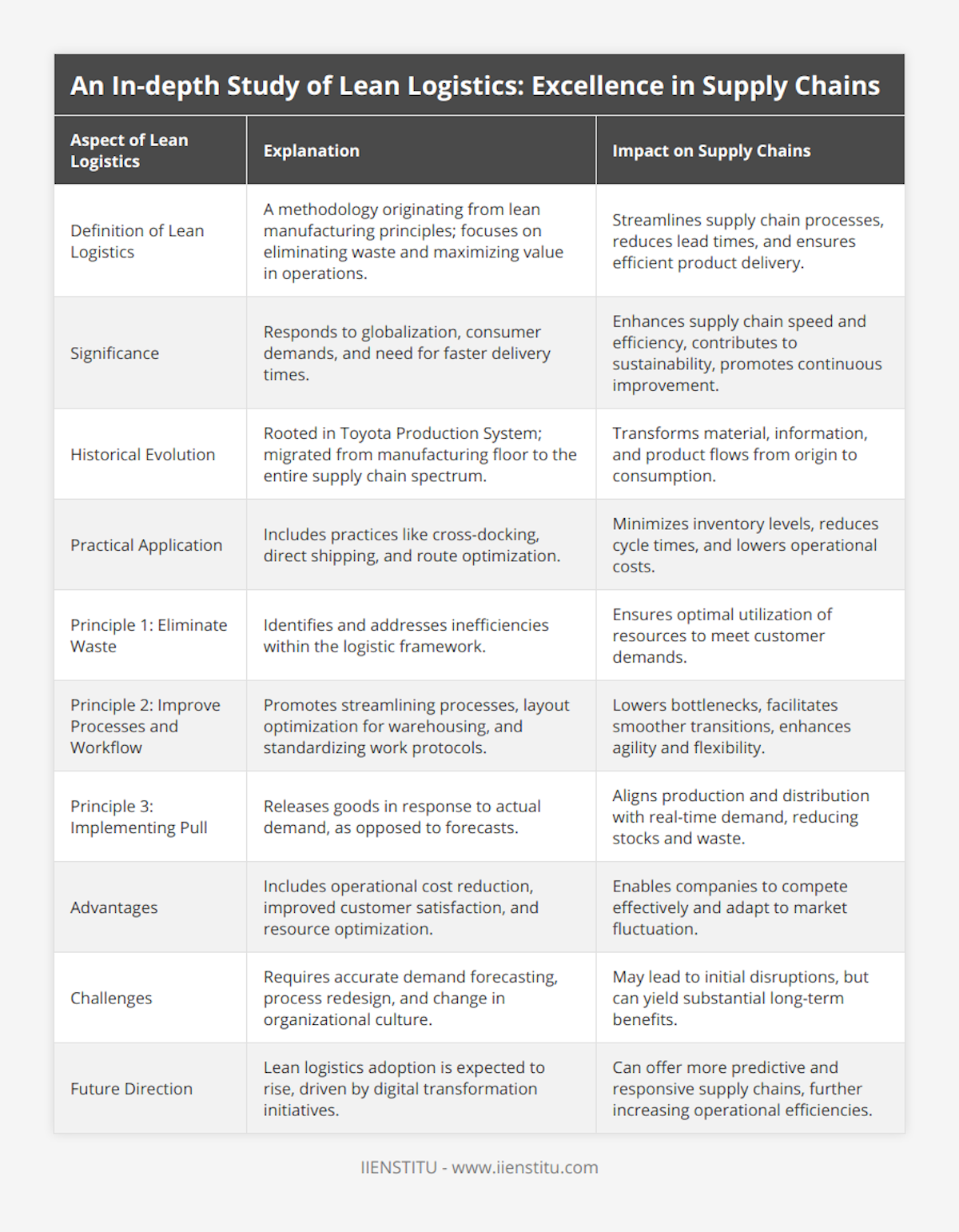
One of the most powerful lean logistics strategies is the use of pull systems, which ensure that products are only produced and delivered when there is actual demand from customers. This helps to reduce overproduction and inventory waste, while also improving responsiveness to changing customer needs. As Womack and Jones (2003) explain in their book "Lean Thinking," pull systems are a key enabler of lean logistics, allowing organizations to "sell one, make one" and "deliver one" in perfect synchronization with customer demand.
Another important aspect of lean logistics is the focus on supply chain collaboration and integration. In a lean logistics environment, all members of the supply chain work together as a single, cohesive unit, sharing information and resources to optimize performance and minimize waste. This requires a high degree of trust, transparency, and communication between supply chain partners, as well as a willingness to put the needs of the end customer first.
Of course, implementing lean logistics is not without its challenges. One of the biggest challenges is overcoming resistance to change within the organization. Many people are comfortable with the status quo and may be reluctant to embrace new ways of working. To overcome this resistance, leaders must communicate the benefits of lean logistics clearly and consistently, and involve employees in the change process from the very beginning.
Another challenge is the need for significant investments in technology and infrastructure. Lean logistics relies heavily on real-time data and advanced analytics to drive continuous improvement and optimize performance. This requires organizations to invest in modern logistics management systems, as well as in the training and development of their employees.
Despite these challenges, the benefits of lean logistics are clear. By eliminating waste, improving efficiency, and enhancing customer value, lean logistics can help organizations to reduce costs, improve service levels, and gain a competitive advantage in the marketplace. As the global economy continues to evolve and customer expectations continue to rise, the importance of lean logistics will only continue to grow.
In conclusion, lean logistics is a powerful approach to supply chain management that can help organizations to achieve unprecedented levels of efficiency, agility, and customer satisfaction. By focusing on value creation, continuous improvement, and supply chain collaboration, lean logistics enables organizations to eliminate waste, reduce costs, and deliver superior value to their customers. While implementing lean logistics can be challenging, the benefits are well worth the effort. As more and more organizations embrace lean thinking and apply it to their logistics operations, we can expect to see a new era of supply chain excellence emerge, one that is defined by innovation, flexibility, and an unwavering commitment to customer value.
References:
Liker, J. K. (2004). The Toyota Way: 14 Management Principles from the World's Greatest Manufacturer. McGraw-Hill.
Myerson, P. (2012). Lean Supply Chain and Logistics Management. McGraw-Hill.
Womack, J. P., & Jones, D. T. (2003). Lean Thinking: Banish Waste and Create Wealth in Your Corporation. Free Press.
Goldsby, T. J., & Martichenko, R. (2005). Lean Six Sigma Logistics: Strategic Development to Operational Success. J. Ross Publishing.
Baudin, M. (2004). Lean Logistics: The Nuts and Bolts of Delivering Materials and Goods. Productivity Press.
Zylstra, K. D. (2006). Lean Distribution: Applying Lean Manufacturing to Distribution, Logistics, and Supply Chain. John Wiley & Sons.