Unlocking Your Supply Chain: Solving Capacity Issues with TOC

I still remember the day when I was first introduced to the Theory of Constraints (TOC) in a supply chain management seminar. The concept was both enlightening and transformative. It dawned on me that much like the weakest link in a chain determines its overall strength, a single bottleneck can limit the entire capacity of a supply chain. This realization sparked a newfound passion for optimizing supply chain processes, and I became eager to delve deeper into how TOC could unlock unprecedented efficiencies.
Key Concepts | Brief Description | Additional Information |
---|---|---|
Theory of Constraints (TOC) | A framework for identifying the bottleneck in a system and determining the best solutions for improving the capacity | In supply chain management, TOC can help improve efficiency and meet customer demands by enhancing system capacity |
Identifying the Constraint | The first step of TOC which usually involves identifying the slowest step that limits the whole process | Focussing on this step can help improve entire system's capacity |
Slowing Down the Process | One solution of TOC where all other steps are slowed to match the slowest step | This can prevent inventory buildup. However, it may not always meet customers' needs |
Improving the Constraint | Another solution of TOC where the slowest step(condition) is improved to fasten the whole supply chain | May involve streamlining processes, increasing efficiency, or investing in new technology |
Customer Demands | The need to ensure supply chain capacity meets customer requirements | Often a key driving factor in improving supply chain efficiency and capacity |
Inventory Buildup | An issue that can arise when process steps have different speeds | Can be prevented by slowing the whole process to match the speed of the slowest step |
Process Efficiency | The ability to complete a process with minimum waste and maximum output | An important factor to consider when improving the constraint in the supply chain |
New Technology | Potential method for improving the constraint | Can lead to improved efficiency and can be a significant investment |
Market Needs | Determined by customer demand | Understanding market needs are vital to adjust the process and capacity of the supply chain system |
System's Capacity | Maximum output a system can produce | TOC helps in increasing system's capacity by identifying and improving the constraint |
In the fast-paced world of supply chain management, meeting customer demands swiftly and efficiently is paramount. However, various constraints often impede this goal, leading to delays and dissatisfied customers. Supply chain management management isn't just about moving goods from point A to point B; it's about ensuring every part of the process is optimized and functioning harmoniously.
Introduction
Identifying the Constraint
Option 1: Slowing Down the Process
Option 2: Improving the Constraint
Conclusion
In this article, we'll explore the Theory of Constraints in detail, guiding you through the process of identifying bottlenecks in your supply chain activities and discussing two primary strategies to enhance capacity. Whether you're a seasoned professional or new to SCM management, these insights can help you revolutionize your approach to supply chain mgmt.
Understanding the Theory of Constraints in Supply Chain Management
At its core, the Theory of Constraints is a methodology for identifying the most significant limiting factor (i.e., the constraint) in a process and systematically improving it. As Dr. Eliyahu M. Goldratt, the father of TOC, once said, "Tell me how you measure me, and I'll tell you how I will behave." This quote underscores the importance of recognizing and measuring constraints to drive behavioral change and process improvement.
The Essence of Constraints
In the realm of supply and chain management, a constraint could be any element that prevents the system from achieving higher performance. These constraints can be internal, such as a machine's production capacity, or external, like market demand fluctuations. Identifying and addressing these constraints is crucial for optimizing the entire supply chain m.
Personal Encounter with Constraints
In my early days as a supply chain analyst, I encountered a significant constraint while working for a manufacturing company. Despite high demand, we couldn't increase our output. After some investigation, we discovered that a specific component supplied by a vendor had a long lead time, creating a bottleneck. This experience highlighted the importance of chain of supply management and the need to identify and address constraints promptly.
Identifying the Constraint: The First Step Toward Optimization
The journey to optimize your supply chain begins with pinpointing the constraint. Here's how you can effectively identify it:
1- Data Collection and Analysis: Gather data on all processes within your supply chain. Look for areas where delays occur or where throughput is consistently lower than other areas.
2- Process Mapping: Create a visual representation of your supply chain activities. This map helps in identifying stages that slow down the overall process.
By unlocking your supply chain with TOC, you can open the potential of your capacity.

3- Employee Feedback: Those working on the front lines often have valuable insights. Engage with your team to understand where they perceive bottlenecks.
4- Performance Metrics: Establish key performance indicators (KPIs) for each stage of the supply chain mgmt to identify underperforming segments.
5- Benchmarking: Compare your processes against industry standards to spot areas needing improvement.
Underlined: Identifying the constraint is not a one-time task but a continuous process crucial for sustained efficiency.
Option 1: Slowing Down the Process
Once the constraint is identified, one potential solution is to adjust the pace of other processes to match the constraint's capacity.
The Logic Behind Slowing Down
At first glance, slowing down might seem counterproductive. However, aligning all processes prevents excess inventory buildup and reduces wasted resources. This method ensures that the constraint is not overburdened, which could lead to breakdowns or quality issues.
Pros and Cons of Slowing Down
Pros:
Inventory Control: Reduces surplus stock and associated holding costs.
Resource Allocation: Optimizes the use of resources across the supply chain.
Process Stability: Creates a steady workflow, making it easier to manage.
Cons:
Reduced Output: Overall production might decrease, affecting revenue.
Customer Satisfaction: Delays in order fulfillment could impact customer relationships.
Competitive Disadvantage: Slower processes might allow competitors to capture market share.
Italicized: In my experience, slowing down is a short-term fix. While it stabilizes processes, it doesn't address the root cause of the constraint.
Case Study: A Real-world Application
At a previous company, we faced a constraint in the packaging department. To prevent overproduction and wasted materials, we slowed down the assembly line. This adjustment led to reduced overtime costs but also delayed shipments, resulting in customer complaints. The lesson learned was that while slowing down can offer temporary relief, it's not a sustainable long-term strategy.
Option 2: Improving the Constraint
The second, and often more effective, option is to enhance the performance of the constraint itself.
Strategies for Improvement
1- Process Improvement Techniques: Implement methodologies like Lean or Six Sigma to streamline operations.
2- Technological Upgrades: Invest in modern equipment or software that increases efficiency.
3- Training and Development: Equip employees with the skills needed to improve productivity.
4- Additional Resources: Allocate more staff or shifts to the constrained area.
5- Supplier Collaboration: Work closely with suppliers to reduce lead times and improve quality.
Bold: Focusing on the constraint transforms it from a bottleneck into a catalyst for growth.
Benefits of Improving the Constraint
Increased Throughput: Enhances overall production capacity.
Customer Satisfaction: Faster fulfillment times improve customer experiences.
Competitive Edge: Ability to meet market demands swiftly can set you apart from competitors.
Revenue Growth: Higher output often leads to increased sales and profitability.
My Success Story with Constraint Improvement
In one of my most rewarding projects, we faced a constraint in our machining process. By investing in a new CNC machine and providing specialized training to operators, we increased that station's capacity by 50%. This improvement not only eliminated delays but also opened opportunities for new contracts, significantly boosting the company's bottom line.
Combining Both Options for Optimal Results
Sometimes, the best approach is a hybrid one. While working on improving the constraint, it's practical to adjust other processes to maintain balance.
The Balanced Approach
Short-term Adjustments: Temporarily slow down non-critical processes to prevent overwhelming the constraint.
Long-term Investments: Simultaneously work on strategies to enhance the constraint's capacity.
Continuous Monitoring: Regularly assess the supply chain to identify new constraints as they emerge.
Bold and Underlined: This balanced strategy ensures immediate stability and paves the way for sustained improvements.
Factors Influencing the Choice of Option
Several variables determine whether you should slow down processes or focus on improving the constraint:
Resource Availability: Do you have the capital and human resources to invest in improvements?
Time Constraints: Is there an urgent need to meet market demand?
Market Conditions: Are competitors likely to capitalize on any slowdown in your operations?
Strategic Goals: Does improving the constraint align with your long-term business objectives?
Italicized: It's essential to consider these factors holistically to make an informed decision.
The Ongoing Cycle of Improvement
Remember that once a constraint is resolved, another will take its place. This concept is known as the "continuous improvement loop" in supply chain management.
Steps in the Continuous Improvement Loop
1- Identify: Locate the current constraint.
2- Exploit: Make quick improvements to optimize the constraint.
3- Subordinate: Align other processes to support the constraint's maximum capacity.
4- Elevate: Invest in significant changes to eliminate the constraint.
5- Repeat: Once the constraint is broken, return to step one.
Bold: This cycle ensures that your supply chain m evolves and improves continuously.
Embracing Technology and Innovation
The future of SCM supply lies in leveraging technology. Tools like AI and IoT can provide real-time data, helping identify and address constraints more efficiently.
Technological Solutions
Predictive Analytics: Anticipate potential constraints before they become critical.
Automation: Use robotics and automated systems to increase capacity.
Cloud Computing: Enhance collaboration and data accessibility across the supply chain.
Final Thoughts
Optimizing your supply chain management process tips isn't just about immediate fixes; it's about fostering a culture of continuous improvement. By understanding and applying the Theory of Constraints, you position your organization to respond adeptly to challenges and seize new opportunities.
Bold: In the dynamic world of supply chain mgmt, adaptability and proactive improvement are your greatest assets.
Encouraging Empowerment and Collaboration
Empower your team to identify constraints and propose solutions. Collaboration across departments can uncover insights that might otherwise be overlooked.
Italicized and Underlined: After all, a unified team can overcome any obstacle.
References
1- Goldratt, E. M. (1984). The Goal: A Process of Ongoing Improvement. North River Press.
2- Schragenheim, E., Dettmer, H. W., & Patterson, J. (2009). Supply Chain Management at Warp Speed: Integrating the System from End to End. CRC Press.
3- Mentzer, J. T. (2004). Fundamentals of Supply Chain Management: Twelve Drivers of Competitive Advantage. Sage Publications.
4- Krajewski, L. J., Ritzman, L. P., & Malhotra, M. K. (2013). Operations Management: Processes and Supply Chains. Pearson Education.
5- Chopra, S., & Meindl, P. (2010). Supply Chain Management: Strategy, Planning, and Operation. Prentice Hall.
By embracing the Theory of Constraints and continually seeking to improve, you'll not only enhance your supply chain activities but also drive your organization toward greater success. Remember, in the ever-evolving landscape of supply chain management, staying stagnant is not an option. So take the first step, identify that constraint, and unlock your supply chain's full potential.
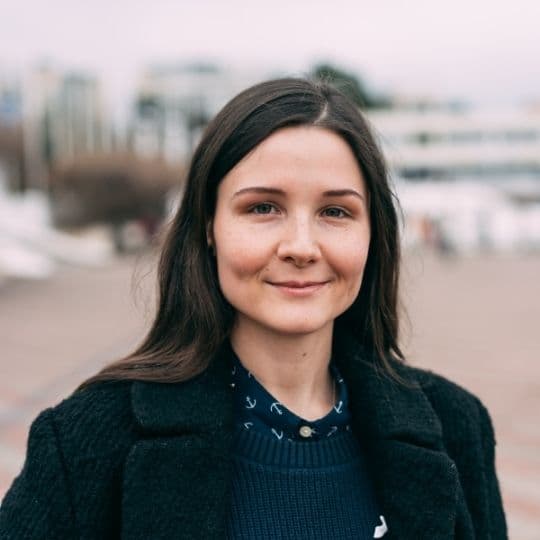
I am Amara Weiss and for many years I have worked in the field of education, specifically in the area of technology. I firmly believe that technology is a powerful tool that can help educators achieve their goals and improve student outcomes. That is why I currently work with IIENSTITU, an organization that supports more than 2 million students worldwide. In my role, I strive to contribute to its global growth and help educators make the most of available technologies.