Role of HR in Total Quality Mgmt: A People-Focused Approach

It was a crisp autumn morning when I first stepped onto the factory floor of our family-owned business. The familiar hum of machines and the scent of freshly cut materials always brought back memories of my childhood, running around the place, oblivious to the intricacies of manufacturing. But this time was different; I was here not just as the owner's child but as a part of the team, eager to contribute to our company's success. Little did I know, the journey ahead would be deeply intertwined with the principles of Total Quality Management (TQM).
TQM Subsystem | Responsible Entity | Key Responsibilities |
---|---|---|
Management Subsystem | Management Teams | Setting objectives, developing strategies, providing leadership, allocating resources |
Social Subsystem | HR and Employees | Establishing good relationships, building trust among employees-customers-suppliers, incentivizing and rewarding quality work |
Technical Subsystem | Technical / Operation Teams | Developing processes, implementing procedures, ensuring tool-(machinery-)availability, monitoring process efficiency |
Education Subsystem | HR / Training and Development Teams | Providing training, enabling employees to perform effectively |
Quality Focus | Organizational-Level | Building quality from the beginning, maintaining tools/machinery, quantifying quality |
Quality Focus | Individual-Level | Adhering to norms/standards, maintaining healthy work relations |
Individual Contributions | All Employees | Adherence to norms, respect for status-power relationships |
Creativity and Motivation | All Employees | Participation in work committees, involvement in activities promoting motivation and creativity |
People-Focused Approach | Long-Term Success | Ensuring a healthy work environment, fostering trust and respect, encouraging employee participation and creativity |
TQM Overview | Continuous Improvement | Quality built-in from start, focus on management/social/technical/education subsystems, employee's role, HR's people-focused approach |
Embracing Quality from the Ground Up
Growing up, my father often said, "Quality isn't just an act; it's a habit." Back then, I didn't fully grasp what he meant. However, as I delved deeper into the workings of the business, I realized that quality isn't something you inspect into a product—it's something you build from the very start. This philosophy is at the heart of Total Quality Management.
Introduction
Role of Corporate HR in Total Quality Management
Responsibilities of Individuals
Focus on Quality
Conclusion
Understanding Total Quality Management
Total Quality Management (TQM) is more than just a buzzword; it's a comprehensive system of management that fosters continuous improvement in an organization's products and services. It's based on the idea that quality should be built in from the beginning rather than inspected and corrected after the fact. This proactive approach ensures that we not only meet but often exceed our customers' expectations.
The Four Organizational Subsystems of TQM
TQM focuses on four organizational subsystems:
1- The Management Subsystem
2- The Social Subsystem
3- The Technical Subsystem
4- The Education Subsystem
These subsystems work in harmony to create a culture where quality is everyone's responsibility.
The Management Subsystem: Leading by Example
In any organization, leadership sets the tone. The management subsystem is responsible for setting objectives, developing strategies, and allocating resources. I recall a time when we were facing stiff competition from overseas manufacturers. Our management team didn't just sit back; they took proactive steps to innovate and improve our processes.
Key roles of management include:
Providing clear direction and vision
Allocating resources effectively
Encouraging a culture of continuous improvement
By leading by example, our managers showed that quality wasn't just a department—it was a mindset.
The Social Subsystem: People Make the Difference
An organization is only as good as its people. The social subsystem focuses on the relationships and culture within the company. This means establishing trust and respect among employees, customers, and suppliers.
I fondly remember Maria, one of our longest-serving employees, who always took newcomers under her wing. Her willingness to share knowledge and foster teamwork made a significant difference in the overall morale and productivity of the team.
Important aspects of the social subsystem are:
Building strong interpersonal relationships
Encouraging collaboration and teamwork
Recognizing and rewarding quality work
The Technical Subsystem: Streamlining Processes
The technical subsystem is all about developing and implementing effective processes and procedures. This ensures that we have the right tools and machinery in place to produce quality products.
After facing repeated delays in our supply chain, we decided to optimize our supply chain management process. We sought tips from industry experts, invested in new technology, and redefined our logistics strategy. The result? We not only reduced delays but also improved overall efficiency.
Total Quality Management's success lies in the HR team's hands, who must ensure a people-focused approach to drive long-term success.

Key components of the technical subsystem include:
Implementing efficient processes
Embracing new technologies
Continuous monitoring and quantifying quality metrics
The Education Subsystem: Learning Never Stops
Education and continuous learning are crucial for maintaining high-quality standards. The education subsystem ensures that employees at all levels receive the training and development they need.
We initiated a program where employees could attend workshops and seminars related to their field. This not only improved their skills but also boosted their confidence.
Essential elements of the education subsystem are:
Providing ongoing training and development
Encouraging knowledge sharing among employees
Fostering a culture of continuous learning
After all, when employees grow, the organization grows with them.
The Individual's Role in TQM
At the heart of TQM is the belief that every individual is responsible for quality. Employees must:
Adhere to the organization's norms and standards
Respect the status and power relationships within the organization
Participate actively in initiatives that promote motivation and creativity
I recall when John, a junior technician, suggested a minor tweak in the assembly line that reduced errors by 15%. His initiative not only improved our output but also highlighted how individual contributions are vital to the TQM process.
Focusing on Quality: Meeting and Exceeding Customer Expectations
Quality is not just about meeting standards; it's about exceeding expectations. Our customers trust us to deliver products that not only fulfill their needs but also stand the test of time.
Building Quality from the Beginning
We believe that quality should be integrated into every step of the process. This means:
Using high-quality materials
Employing skilled professionals
Implementing rigorous testing procedures
By doing so, we reduce the need for after-the-fact inspections and corrections.
Quantifying Quality
To ensure we maintain our standards, we:
Set measurable quality objectives
Monitor performance through key performance indicators (KPIs)
Regularly review and adjust our processes as needed
This quantifiable approach allows us to identify areas for improvement and track our progress over time.
The Role of Corporate HR in Total Quality Management
Our HR team plays a pivotal role in embedding TQM into our organizational culture. They ensure that the principles of TQM are reflected in our hiring practices, training programs, and performance evaluations.
HR's responsibilities include:
Recruiting individuals who value quality
Designing training programs focused on TQM principles
Developing reward systems that recognize quality contributions
By aligning our people strategies with our TQM goals, we create a cohesive approach that drives long-term success.
Employee Involvement in Continuous Improvement Processes
Employee involvement is critical for continuous improvement. When employees are engaged, they are more likely to:
Identify inefficiencies
Suggest innovative solutions
Take ownership of their work
We established cross-functional teams to tackle specific challenges. These teams bring together diverse perspectives, leading to more comprehensive solutions.
Implementing TQM Strategies in Small Businesses
While TQM is often associated with large corporations, small businesses can also reap significant benefits.
Steps for small businesses include:
1- Commitment from Leadership: Owners must champion TQM principles.
2- Employee Training: Provide training on quality management concepts.
3- Customer Focus: Engage with customers to understand their needs.
4- Process Management: Streamline processes for efficiency.
5- Continuous Improvement: Encourage feedback and make iterative improvements.
By implementing TQM strategies, small businesses can improve their competitiveness and customer satisfaction.
Challenges and How to Overcome Them
Implementing TQM isn't without its challenges. Common obstacles include:
Resistance to change
Lack of understanding of TQM principles
Insufficient resources
Overcoming these challenges requires:
Effective communication about the benefits of TQM
Investing in training and education
Demonstrating management's commitment to quality
Remember, change doesn't happen overnight. Patience and persistence are key.
Real-Life Application: A Success Story
Let me share a story about our supplier, a small parts manufacturer. They were struggling with high defect rates and customer complaints. We collaborated with them to implement TQM principles.
Actions taken:
Provided training sessions for their employees
Helped them streamline their production processes
Established regular quality audits
Within a year, their defect rates dropped by 40%, and customer satisfaction increased dramatically. This not only strengthened our partnership but also highlighted the transformative power of TQM.
The Importance of Quality Assurance in Customer Satisfaction
Quality assurance (QA) plays a vital role in meeting customer expectations. QA involves systematic activities implemented in a quality system so that quality requirements for a product or service will be fulfilled.
Key aspects of QA include:
Defining clear quality standards
Regular testing and inspections
Feedback mechanisms to identify areas for improvement
By prioritizing QA, we ensure that our products consistently meet the highest standards, leading to greater customer trust and loyalty.
Training and Development for TQM Success
Investing in our employees' growth is non-negotiable. Training and development programs equip our team with the skills and knowledge needed to uphold quality standards.
Our approach includes:
On-the-job training
Workshops and seminars
Mentorship programs
By fostering a learning environment, we empower our employees to contribute effectively to our TQM objectives.
The Future of TQM in Our Organization
Looking ahead, we're excited about the possibilities. Emerging technologies like AI and machine learning offer new ways to enhance quality. We're exploring these options to stay ahead of the curve.
Our focus areas include:
Implementing advanced data analytics to predict potential issues
Automating repetitive tasks to reduce errors
Enhancing customer engagement through personalized experiences
Conclusion
Reflecting on our journey, it's clear that Total Quality Management has been instrumental in our success. By embedding quality into every aspect of our organization, we've not only improved our products and services but also built a stronger, more cohesive team.
To anyone considering adopting TQM principles, I say go for it! The road may have its challenges, but the rewards—higher customer satisfaction, improved efficiency, and a motivated workforce—are undeniably worth it.
As my father wisely said, "In the pursuit of quality, there are no finish lines—only new beginnings." And with that mindset, we continue to strive for excellence every day.
References
1- Deming, W. E. (1986). Out of the Crisis. MIT Press.
2- Juran, J. M. (1988). Juran's Quality Control Handbook. McGraw-Hill.
3- Crosby, P. B. (1979). Quality Is Free: The Art of Making Quality Certain. McGraw-Hill.
4- Besterfield, D. H. et al. (2003). Total Quality Management. Prentice Hall.
5- Ishikawa, K. (1985). What Is Total Quality Control? The Japanese Way. Prentice Hall.
Remember, quality isn't a destination but a journey—a journey we're all on together.
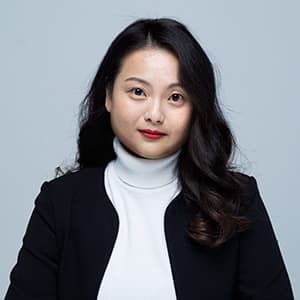
Yu Payne is an American professional who believes in personal growth. After studying The Art & Science of Transformational from Erickson College, she continuously seeks out new trainings to improve herself. She has been producing content for the IIENSTITU Blog since 2021. Her work has been featured on various platforms, including but not limited to: ThriveGlobal, TinyBuddha, and Addicted2Success. Yu aspires to help others reach their full potential and live their best lives.