Optimizing Supply Chain Management: Procurement & Logistics

I still remember the early days of my career in supply chain management. Fresh out of university, I joined a manufacturing company that was struggling to keep up with customer demand. One of my first tasks was to explore ways to optimize our operations. Little did I know that the concept of increasing batch size would become a pivotal strategy in our journey toward efficiency.
Aspect | Benefits | Drawbacks |
---|---|---|
Procurement & Logistics | Find best sources of materials, negotiate best prices, efficient movement of materials from suppliers to customers | Potential increased logistics costs with increasing batch size |
Increasing Batch Size | Economies of scale, Reduced cost per item, Improvement in inventory management, Reduced order processing costs, Improved customer service, Improved forecasting accuracy | Potential increased costs in storage and additional transportation |
Inventory Management | Reduced need to restock, Better inventory level management | Requires larger storage spaces for large batches |
Order Processing | Reduced order processing costs due to fewer orders secondarily improving customer service | May be overwhelming to process large orders at once |
Customer Service | Orders can be filled more quickly due to larger available stock | Potentially longer wait times due to large order processing |
Forecasting Accuracy | Ability to predict customer demand more accurately due to larger data set | Could lead to inaccurate predictions if not adjusted well for large batch size |
Economies of Scale | Reduces cost per item, More significant savings when sourcing from low-cost regions | Cost advantages may be offset by increased logistics costs |
Procurement in Low-Cost Regions | Further reduces material costs | May raise ethical considerations, potential for lower quality materials |
Sourcing Large Batches | Ability to meet higher customer demand, Potential for pricing discounts | Greater risk of inventory going obsolete or spoiling |
Logistics Cost | Potential cost savings with efficient logistics management | Increased costs due to larger batch sizes, needs larger storage areas, additional transportation needs |
In this article, we'll delve into the potential benefits and drawbacks of increasing batch size to optimize supply chain management. We'll explore how procurement and logistics play crucial roles and share insights from real-world experiences and academic studies. Whether you're a seasoned professional or new to the field, understanding the impact of batch size on your supply chain can make a significant difference.
Introduction
Procurement & Logistics
Optimizing Supply Chain Management
Benefits of Increasing Batch Size
Conclusion
Procurement and Logistics: The Backbone of Supply Chain Management
Before we dive deeper, let's take a moment to appreciate the vital roles that procurement and logistics play in the realm of supply chain management. These two departments are the lifeblood of any organization that relies on moving goods from point A to point B.
The Role of Procurement
The procurement team is on the frontline of sourcing the best materials at the most competitive prices. They're the ones negotiating with suppliers, assessing risks, and ensuring that the company gets the best bang for its buck. In today's globalized world, this often means dealing with suppliers from low-cost regions to minimize expenses.
I remember when our procurement team scored a massive win by negotiating a long-term contract with a key supplier. Not only did we secure a significant discount, but we also established a strong partnership that would benefit us for years to come. It was a testament to the importance of supplier relationship management in the grand scheme of supply chain optimization.
The Importance of Logistics
On the other hand, the logistics department ensures that these materials reach their destinations efficiently. This involves coordinating transportation, managing supply chain activities, and ensuring timely delivery. Logistics is not just about moving goods; it's about optimizing the entire process to reduce costs and improve customer satisfaction.
I recall a particularly challenging project where we had to deliver a large shipment to a remote location within a tight deadline. Our logistics team worked tirelessly to coordinate multiple modes of transportation, navigating through customs, and ensuring that the goods arrived intact and on time. It was a prime example of how logistics efficiency can make or break a company's reputation.
Optimizing Supply Chain Management Through Batch Size Adjustment
One strategy that often comes into play when trying to optimize supply chain management techniques is adjusting the batch size of orders. But what does increasing batch size actually entail, and how does it impact both procurement and logistics?
Economies of Scale
When we increase the batch size, we often benefit from economies of scale. Buying in larger quantities usually means getting a lower cost per unit. I recall a time when we decided to bulk purchase raw materials. Not only did we secure a significant discount from our supplier, but we also locked in favorable terms for future orders. This move was celebrated in the procurement department as a big win.
Efficient supply chain management is the key to successful procurement and logistics.

Enhanced Supplier Relationships
Larger orders can strengthen relationships with suppliers. They see you as a valuable customer and, in turn, may offer better service levels, priority production scheduling, or even share insights about market trends that could benefit your company.
The Potential Drawbacks of Increasing Batch Size
However, it's not all sunshine and roses. While increasing batch size has its perks, it also brings along some challenges, especially for the logistics team.
Increased Logistics Costs
One of the immediate consequences of larger batch sizes is the increase in logistics costs. Here's why:
Storage Requirements: More inventory means more space is needed. This could lead to higher warehousing costs or the need to invest in additional storage facilities.
Transportation Challenges: Larger batches may require more complex transportation solutions, potentially increasing shipping costs.
Risk of Obsolescence: Holding more inventory increases the risk that some items may become obsolete, especially in fast-moving industries.
I vividly remember when our company decided to increase the batch size of a component used in one of our electronics products. Due to delays in product launch, we ended up with a surplus of components that became outdated quickly, leading to significant losses.
Balancing the Scales: Weighing Benefits and Drawbacks
So, how do companies decide whether increasing batch size is the right move? It boils down to a careful analysis of the potential benefits versus the possible drawbacks.
Benefits of Increasing Batch Size
1- Improved Inventory Management: By having larger quantities on hand, companies can better meet customer demand without the constant need to reorder. This is particularly beneficial during peak seasons.
2- Reduced Order Processing Costs: Processing fewer, larger orders can reduce administrative costs associated with order placement, invoicing, and payment processing.
3- Improved Customer Service: With more stock available, companies can fulfill orders faster, leading to higher customer satisfaction.
4- Enhanced Forecasting Accuracy: Larger batch sizes can smooth out demand variability, making it easier to predict and plan for future needs.
Drawbacks of Increasing Batch Size
1- Higher Holding Costs: Increased inventory leads to higher costs for storage, insurance, and capital tied up in stock.
2- Logistics Complexity: Managing larger batches can complicate transportation and handling processes.
3- Risk of Waste: Perishable goods or items with a short life cycle may spoil or become obsolete.
Real-World Applications and Examples
Case Study: Automotive Industry
In the automotive industry, companies often grapple with the decision of batch sizes. An increase in batch size can lead to lower costs per unit, but the demand for customization and just-in-time delivery has shifted the preference toward smaller batches.
Electronic Supply Chain Management
In electronics, electronic supply chain management requires balancing batch sizes carefully. Technology evolves rapidly, and holding large inventories can result in obsolete stock. Companies like Apple are known for their efficient supply chain department that minimizes inventory while meeting global demand.
Strategies to Mitigate Drawbacks
To reap the benefits of increased batch sizes while minimizing risks, companies can adopt several strategies:
1- Implementing Advanced Inventory Systems: Utilizing the best Gantt chart for project management can help in planning and visualizing inventory levels, production schedules, and shipping timelines.
2- Leveraging Supply Chain Management Software: SCM management tools can provide real-time data, predictive analytics, and automation to optimize both procurement and logistics processes.
3- Collaboration with Suppliers: Developing strong relationships can lead to better terms, shared risk, and improved communication.
4- Flexible Supply Chain Design: Designing a chain of supply management that can adapt to changes in demand or supply conditions can reduce risks associated with larger batch sizes.
The Role of Technology in Supply Chain Optimization
Technology plays a pivotal role in modern supply chain management management. From blockchain for transparency to AI for predictive analytics, embracing technological solutions can enhance efficiency.
Electronic Supply Chain Management
Electronic supply chain management involves integrating technology into all aspects of the supply chain. This can include:
Automation of Processes
Real-Time Tracking
Data Analytics for Forecasting
Conclusion
Reflecting on my journey through the world of supply chain management, I can attest that there's no one-size-fits-all answer to whether increasing batch size is the right strategy. It's a decision that requires careful consideration of both the benefits and drawbacks.
Companies must analyze their specific situation, considering factors like industry dynamics, demand variability, storage capacity, and financial implications. By leveraging tools like the best Gantt chart for project management, utilizing advanced SCM supply, and fostering strong supplier relationships, organizations can make informed decisions.
In the end, optimizing supply and chain management is about finding the right balance. Whether through increasing batch sizes or other strategies, the goal remains the same: delivering value to customers efficiently and effectively.
References
1- Christopher, M. (2016). Logistics & Supply Chain Management (5th ed.). Pearson Education Limited.
2- Chopra, S., & Meindl, P. (2019). Supply Chain Management: Strategy, Planning, and Operation (7th ed.). Pearson.
3- Simchi-Levi, D., Kaminsky, P., & Simchi-Levi, E. (2008). Designing and Managing the Supply Chain: Concepts, Strategies, and Case Studies (3rd ed.). McGraw-Hill/Irwin.
4- Johnson, P. F., Leenders, M. R., & Flynn, A. E. (2017). Purchasing and Supply Management (15th ed.). McGraw-Hill Education.
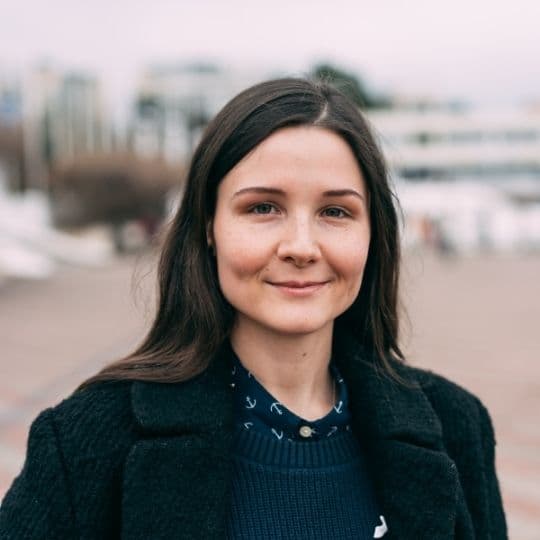
I am Amara Weiss and for many years I have worked in the field of education, specifically in the area of technology. I firmly believe that technology is a powerful tool that can help educators achieve their goals and improve student outcomes. That is why I currently work with IIENSTITU, an organization that supports more than 2 million students worldwide. In my role, I strive to contribute to its global growth and help educators make the most of available technologies.