Ensuring Order Fulfillment Reliability in Logistics Management

Topic | Explanation | Importance in logistics management |
---|---|---|
Order Fulfilment Reliability | It is the company's ability to fulfill orders promptly and satisfactorily within agreed terms of time, quality and quantity. | Creates order reliability, boosting customer satisfaction and competitiveness. |
Components of Order Cycle | These include order processing, material planning, allocation, picking, packing, and transportation. | Coordinated management ensures smooth order fulfillment, maintaining reliability. |
Order Processing | It involves receiving and processing orders from customers. | Timely order processing decreases fulfillment time, increasing reliability. |
Material Planning | Involves determining necessary materials for an order and allocating them for production. | Ensures material availability, preventing delays and increasing reliability. |
Allocation | Includes assigning required materials to the production process. | Prevents wastage and reduces idle time, boosting reliability and efficiency. |
Picking | Involves retrieving the required materials from the warehouse. | Speedy picking reduces wait time, enhancing order fulfillment reliability. |
Packing | Entails preparing the shipping materials and products. | Appropriate packing prevents product damage, ensuring product quality and reliability. |
Transportation | Related to delivering the materials to the customer. | Reliable transportation ensures on-time delivery, enhancing overall fulfillment reliability. |
Order Management System | A system that tracks and monitors the progress of orders, providing real-time updates. | Allows for adjustments, ensuring order fulfillment reliability. |
Importance of Order Fulfilment Reliability | Key for customer satisfaction and competitiveness. | Unreliable fulfillment can lead to production delays and customer loss. |
This article discusses Order Fulfilment Reliability, which is the ability of a company to fulfill orders within the agreed time frame and with the desired quantity and quality of the material. It explains the components of the order cycle, the importance of Order Fulfilment Reliability, and how it can be achieved.
Companies can achieve Order Fulfilment Reliability by implementing an effective order management system that tracks and monitors the progress of orders, provides real-time updates, and enables companies to make necessary adjustments.
Introduction
What is Order Fulfilment Reliability?
Components of Order Cycle
Importance of Order Fulfilment Reliability
Conclusion
Introduction: The customer experience is of utmost importance in the modern business world. Companies must be able to provide customers with reliable, timely, and satisfactory services to remain competitive. In the transaction phase, one of the most critical factors for customer satisfaction is Order Fulfilment Reliability. This is the ability of a company to fulfill orders within the agreed time frame and with the desired quantity and quality of the material.
Top Time Management Strategies To İmprove Productivity And Eliminate Stress
Smart Supply Chain Management Estimating Demand Optimization Strategies
A company must coordinate and manage the various components of the order cycle to maintain Order Fulfillment Reliability. This article will discuss what Order Fulfilment Reliability is, the components of the order cycle, the importance of Order Fulfilment Reliability, and how it can be achieved.
What is Order Fulfilment Reliability?
Order Fulfilment Reliability is the ability of a company to fulfill orders within the agreed time frame and with the desired quantity and quality of the material. It measures the company’s reliability in delivering customer orders promptly and satisfactorily. To maintain Order Fulfilment Reliability, companies need to coordinate and manage the various components of the order cycle.
Components of Order Cycle
The order cycle consists of various components that must be managed and coordinated to ensure the reliability of order fulfillment. These components include order processing, material planning, allocation, picking, packing, and transportation. Order processing involves receiving and processing orders from customers.
Material planning involves determining the necessary materials for a specific order and allocating them for production. Allocation involves assigning the necessary materials to the production process. Picking involves retrieving the required materials from the warehouse. Packing involves preparing the shipping materials, and transportation involves delivering the materials to the customer.
Importance of Order Fulfilment Reliability
Order Fulfilment Reliability is paramount for companies who want to remain competitive in the modern business environment. Customers expect their orders to be fulfilled promptly and satisfactorily, and any delays or issues with quality or quantity can lead to customer dissatisfaction.
Furthermore, customer production schedules are often dependent on the reliability of the supplier’s order fulfillment. If the supplier is unreliable, it can lead to production delays and, ultimately, customer losses.
Conclusion: In conclusion, Order Fulfilment Reliability is an essential factor in the transaction phase of the business cycle. A company can fulfill orders within the agreed time frame and with the desired quantity and quality of the material.
To maintain Order Fulfilment Reliability, companies need to coordinate and manage the various components of the order cycle, such as order processing, material planning, allocation, picking, packing, and transportation. Companies must ensure that they are reliable to remain competitive in the modern business environment and to satisfy their customers.
Reliability in logistics management is the key to successful order fulfillment.
Related Course: Logistics Certificate Programs Online

Order fulfillment is an essential component of any logistics management system. The reliability of the order fulfillment process is essential for customer satisfaction and the success of the business. To ensure order fulfillment reliability, there are certain strategies that can be employed.
The first strategy is utilizing an effective inventory management system. By tracking inventory levels and trends, businesses can ensure that they always have enough stock to fulfill customer orders. This is an important part of order fulfillment reliability as customers will be dissatisfied if their orders cannot be fulfilled due to lack of inventory.
The second strategy is utilizing an efficient transportation system. The transportation system needs to be able to transport goods quickly and efficiently to ensure that orders are fulfilled on time. Utilizing a reliable transportation system can go a long way in ensuring order fulfillment reliability.
The third strategy is utilizing effective order processing systems. These systems should be able to quickly and accurately process customer orders so that they can be fulfilled in a timely manner. Automated order processing systems can help improve order fulfillment reliability.
The fourth strategy is utilizing clear communication channels. It is important that communication between customers and the business is clear so that both parties know what to expect and when. This is especially important when it comes to ordering fulfillment as customers need to know when their orders will be fulfilled.
Finally, effective customer service strategies are essential for ensuring order fulfillment reliability. Customers should be able to contact the business quickly and easily if they have any questions or concerns about their orders. By providing excellent customer service, businesses can ensure that orders are fulfilled on time and to the customer's satisfaction.
In conclusion, there are several strategies that can be employed to ensure order fulfillment reliability in logistics management. Utilizing an effective inventory management system, an efficient transportation system, effective order processing systems, clear communication channels and effective customer service strategies can all help to ensure order fulfillment reliability. By utilizing these strategies, businesses can ensure that their customers are satisfied with the order fulfillment process.

Order fulfilment is a critical component of the supply chain and can have a major impact on customer satisfaction, customer loyalty, and business profitability. The order cycle is a series of steps that are necessary for the successful completion of an order. It includes order entry, order processing, order picking, packing, and shipping. Optimizing these components of the order cycle can help to improve order fulfilment reliability and ultimately customer satisfaction.
There are a number of strategies that can be employed to optimize the order cycle and improve order fulfillment reliability. These strategies include streamlining processes, implementing automated systems, using inventory management software, and utilizing data analysis to optimize operations.
Streamlining processes can help to reduce the amount of time it takes to complete the order cycle. This can be done by eliminating unnecessary steps and streamlining existing processes. Automated systems can help to reduce errors, speed up the order cycle, and improve accuracy. Automated systems can include barcode scanning, pick-to-light systems, and automated packing and shipping processes.
Inventory management software can help to ensure that the necessary items are in stock to fulfill orders. This helps to reduce the risk of backorders and other issues related to order fulfilment. Data analysis can be used to identify areas that can be optimized and areas that are causing problems. This can help to identify the root cause of problems in the order cycle and provide solutions that can be implemented to improve order fulfilment reliability.
In conclusion, optimizing the components of the order cycle can go a long way towards improving order fulfilment reliability and customer satisfaction. Streamlining processes, implementing automated systems, using inventory management software, and utilizing data analysis can all be used to optimize the order cycle and improve order fulfilment reliability.

Inadequate order fulfilment reliability in logistics management can have serious repercussions for businesses and their customers. Many companies rely on a reliable supply chain to meet customer needs, yet order fulfilment reliability is often overlooked in the development of the logistics management system. This lack of attention to order fulfilment reliability can lead to a number of potential risks, including increased costs, delays in delivery, and customer dissatisfaction.
The first risk associated with inadequate order fulfilment reliability is increased costs. When supply chain disruptions occur, businesses may be required to take additional steps to ensure orders are fulfilled. This may include additional inventory, a shift in production processes, or an increase in personnel to meet customer demands. These additional costs can add up quickly and can be difficult to absorb without compromising other areas of the business.
The second risk associated with inadequate order fulfilment reliability is delays in delivery. Even minor disruptions to the supply chain can lead to delays in delivery, which can have a negative impact on customer satisfaction and loyalty. Delayed shipments can cause customers to look elsewhere for their needs, resulting in lost sales and revenue.
The final risk associated with inadequate order fulfilment reliability is customer dissatisfaction. Customers expect their orders to be fulfilled in a timely fashion, and any delays can lead to frustration and a decrease in customer loyalty. This can result in customers switching to other companies, which can lead to a decrease in sales and revenue.
In conclusion, inadequate order fulfilment reliability in logistics management can lead to a number of potential risks, including increased costs, delays in delivery, and customer dissatisfaction. For businesses to remain competitive in today’s market, it is essential to ensure order fulfilment reliability is considered when developing the logistics management system.

**Understanding Order Fulfillment**
Order fulfillment in logistics refers to the comprehensive process of receiving, processing, and delivering an order to a customer. This crucial aspect of supply chain management (SCM) encompasses various stages, including inventory management, order placement, order processing, picking and packing, and transportation. Ultimately, the goal of order fulfillment is to provide a seamless and satisfying experience for the customer, while maximizing efficiency and minimizing costs for businesses.
**Key Components of Order Fulfillment**
*Inventory Management:* Effective order fulfillment begins with consistent inventory management. Businesses must track and regulate their products to ensure they can meet customer demands promptly and accurately.
*Order Placement:* Once a customer selects a product, order placement involves the seamless transfer of information from the customer to the business, facilitating timely and accurate order processing.
*Order Processing:* Businesses then go through the process of confirming and verifying orders, ensuring all relevant details (e.g., pricing, customer information) are accurate before proceeding to fulfillment.
*Picking and Packing:* Warehouse staff locate the ordered items, pick them from the inventory, and properly package the items to prepare for shipping.
*Transportation:* The final stage of order fulfillment entails shipping the packaged orders to customers through efficient and reliable transportation methods; this stage may also involve using multiple shipping providers to optimize delivery times and costs.
**The Significance of Order Fulfillment**
Properly implementing an efficient order fulfillment system is vital for businesses to thrive in today's competitive market. By streamlining these processes, businesses can effectively reduce their operational costs while providing customers with better service and faster deliveries.
Moreover, order fulfillment transcends simply ensuring customers receive their orders on time; it also reflects the business's commitment to customer satisfaction. This can significantly impact customer loyalty, long-term profitability, and overall brand reputation.

Approach 1: Direct Fulfillment
The first approach to order fulfillment is direct fulfillment, which involves the manufacturer or retailer managing the entire process. This includes storing inventory, packing and shipping items, and handling customer returns. With direct fulfillment, businesses control every aspect of the supply chain, ensuring a seamless experience for customers. However, this method requires significant resources and management, making it more suitable for larger organizations.
Approach 2: Third-Party Fulfillment Providers
The second approach is to partner with a third-party fulfillment provider. These entities specialize in handling order fulfillment tasks, often offering services such as warehousing, shipping, and returns management. Companies can choose to outsource all or part of their fulfillment operations to these providers, allowing them to focus on their core business. This approach is effective for small and medium businesses that lack the resources and infrastructure to manage their own fulfillment processes. A downside, however, is that businesses must trust the third-party provider to maintain their brand reputation and consistently meet customers' expectations.
Approach 3: Dropshipping
The last approach is dropshipping, a popular fulfillment method wherein the retailer acts as a liaison between the customer and the manufacturer or wholesaler. Upon receiving an order, the retailer forwards the details to the manufacturer or wholesaler, who then handles the inventory, packaging, and shipping aspects. Businesses using this approach do not need to maintain stock or handle physical products, which can reduce overhead costs and risks associated with inventory management. Dropshipping is an accessible option for start-ups or businesses with limited resources, but it can also result in lack of control over inventory and may lead to longer shipping times for customers.
In conclusion, the three primary approaches to order fulfillment - direct fulfillment, third-party fulfillment providers, and dropshipping - offer businesses varying degrees of control and resource allocation. The choice between these methods depends on factors such as business size, available resources, and the desired level of involvement in the fulfillment process.

Reliability in Logistics
Reliability in logistics refers to the capability of a supply chain to consistently deliver products or services to customers on time and without any damages or errors. A reliable logistics system is an important factor in achieving customer satisfaction and maintaining a competitive advantage in the marketplace.
Timely Deliveries
One of the primary contributions of a reliable logistics system is its ability to consistently deliver products on time. Timely deliveries minimize delays, which can lead to a reduction in stockouts, ultimately benefiting both the business and the customers. This helps ensure that the order fulfillment process runs smoothly and efficiently.
Accuracy and Efficiency
An effective logistics system must not only deliver goods on time but also ensure that orders are accurate and free from errors. This includes the correct items being delivered, in the right quantity, and with proper documentation. Efficiency in the order fulfillment process contributes to a reduction in operational costs, which helps improve the overall profitability of the business.
Damage Prevention
Preventing damages during transportation is another crucial aspect of a reliable logistics system. Proper packaging, handling, and shipping procedures should be in place to ensure that products are not damaged or lost during transit. This contributes to successful order fulfillment as customers receive products in optimal condition, which can lead to increased customer satisfaction and loyalty.
Customer Satisfaction
Ultimately, the goal of a reliable logistics system is to create a positive experience for the customer. By ensuring timely deliveries, accurate orders, and minimal product damages, a business can foster long-lasting relationships with its customers. This not only enhances the customer's shopping experience but also creates a strong reputation for the business, leading to repeat purchases and recommendations to others.
In conclusion, reliability in logistics plays an essential role in successful order fulfillment by directly impacting factors such as timely deliveries, order accuracy, and damage prevention. Implementing a reliable logistics system contributes to enhanced customer satisfaction and increased competitiveness in the marketplace, which are vital for any business's overall success.

Effective Inventory Management Techniques
To ensure order fulfillment reliability, effective inventory management plays a crucial role in maintaining a streamlined supply chain. By adopting strategic inventory management techniques, businesses can optimize their stock levels, reduce costs, and enhance customer satisfaction.
Demand Forecasting
Informed decision-making hinges on accurate demand forecasting, which involves assessing historical data and identifying trends to predict future demand. Incorporating seasonality, market changes, and promotional activities into the analysis enables businesses to respond proactively, ensuring stock availability and prompt fulfillment.
Just-in-Time Inventory
Adopting a just-in-time (JIT) inventory approach involves minimizing stock levels and ordering only what is necessary, based on actual customer demand. This reduces carrying costs, minimizes stock obsolescence, and enhances cash flow. Additionally, JIT inventory management necessitates strong supplier relationships and coordination to maintain stock availability and timely order fulfillment.
Safety Stock
Maintaining safety stock is essential for addressing variability in supply and demand. Determining appropriate safety stock levels involves taking into account lead times, supplier reliability, and demand fluctuations. By having an adequate safety stock in place, businesses can avoid stockouts and ensure timely order fulfillment.
Inventory Classification
Classifying inventory based on the ABC analysis aids businesses in prioritizing stock items according to their value, demand, and turnover rate. High-priority items (A items) usually require close monitoring and frequent replenishment. Focusing on inventory classification helps in allocating resources to critical items, thereby improving order fulfillment reliability.
Collaborative Planning
Collaborative planning, forecasting, and replenishment (CPFR) is a joint process involving the supplier and the retailer to align their supply chain activities. This collaboration improves inventory visibility, facilitates better demand forecasting and replenishment planning, and ultimately reduces stockouts, ensuring order fulfillment reliability.
Inventory Management Systems
Leveraging technological advancements, such as inventory management systems, enhances visibility into stock levels, demand trends, and supplier lead times. Utilizing real-time data, businesses can make better decisions on stock replenishment, manage inventory more effectively, and maintain order fulfillment reliability.
In conclusion, effective inventory management is essential for ensuring order fulfillment reliability. By employing techniques such as demand forecasting, just-in-time inventory, safety stock, inventory classification, and collaborative planning, businesses can optimize their inventory and maintain customer satisfaction. Embracing inventory management systems further supports these efforts, streamlining the entire supply chain process.

Impact on Inventory Management
Demand forecasting plays a significant role in managing inventory, which is crucial for the order fulfillment process. Accurate predictions of customer demand enable businesses to maintain optimal stock levels, reducing the likelihood of stockouts or excess inventory. Stockouts can negatively affect customer satisfaction and brand reputation, while excess inventory leads to higher costs for storage and potential obsolescence.
Improvement in Production Planning
Furthermore, demand forecasting allows businesses to improve their production planning. With a better understanding of future demand, production schedules can be adjusted to match the expected sales volumes. This alignment helps companies avoid production delays, minimize lead times, and reduce the risk of stockouts, contributing to overall order fulfillment reliability.
Enhancing Supplier Collaboration
Accurate demand forecasting helps businesses collaborate more effectively with their suppliers. Sharing demand forecasts with suppliers ensures that the required raw materials and components are available when needed. This collaboration enables suppliers to plan their production and deliveries more efficiently, leading to a more streamlined and reliable order fulfillment process.
Facilitating Efficient Resource Allocation
By accurately forecasting demand, companies can allocate their resources more efficiently. Adequate staffing levels can be maintained during periods of high demand, ensuring timely order processing and delivery. Additionally, warehousing and transportation resources can be optimized to minimize costs and maximize efficiency in the order fulfillment process.
Promoting Customer Satisfaction
Finally, demand forecasting contributes to customer satisfaction by enabling businesses to deliver their products on time and in the right quantities. When companies can consistently meet customers' expectations, they build trust and loyalty, which ultimately leads to repeat purchases and positive word-of-mouth advertising.
In conclusion, demand forecasting impacts the order fulfillment process and its overall reliability in various ways. By enhancing inventory management, improving production planning, facilitating supplier collaboration, allocating resources efficiently, and promoting customer satisfaction, businesses can ensure a more streamlined and dependable fulfillment process that meets customer expectations and contributes to long-term success.

Role of Technology in Enhancing Reliability
Technology plays a crucial role in improving the reliability of logistics operations and order fulfillment by enhancing visibility, streamlining processes, and enabling data-driven decisions. Visibility is achieved through real-time tracking of shipments and inventory levels, allowing companies to ensure the accuracy and timeliness of deliveries.
Streamlining Processes through Automation
Furthermore, technology streamlines logistical processes by automating tasks such as data entry, routing, and scheduling. Automation significantly reduces human errors, increases efficiency, and minimizes the chances of delays in the supply chain. As a result, companies can fulfill orders more quickly and accurately, meeting customer expectations and mitigating potential issues.
Data-driven Decision Making
Moreover, technology enables companies to leverage data and analytics to make informed decisions that optimize their logistics operations. By analyzing trends, identifying patterns, and predicting future demands, businesses can proactively adjust their strategies to better align with customer needs. This proactive approach ultimately enhances the reliability of order fulfillment, as companies can adapt to fluctuations in demand without compromising on service quality.
Integration of Advanced Technologies
In addition to these aspects, the integration of advanced technologies such as artificial intelligence, machine learning, and the Internet of Things (IoT) allows companies to further enhance the effectiveness and reliability of logistics operations. These technologies enable predictive analytics, intelligent routing, and automated decision-making processes, further improving the ability of companies to fulfill orders accurately and on time.
Mitigating Risks and Challenges
Lastly, technology plays an essential role in identifying and mitigating risks and challenges that may negatively impact the logistics industry. For example, companies can utilize advanced analytics and simulation tools to assess the potential impact of natural disasters, labor strikes, or political unrest on their operations. This information allows businesses to develop contingency plans and risk management strategies, ensuring a higher level of reliability in their logistics operations and order fulfillment.
In conclusion, technology is an indispensable tool in enhancing the reliability of logistics operations and order fulfillment. By improving visibility, streamlining processes, enabling data-driven decision-making, and integrating advanced technologies, companies can optimize their supply chains, meet customer expectations, and ultimately achieve a competitive edge in today's rapidly evolving business environment.

Essential Components of Logistics Reliability
Reliability in Fulfillment Process
Logistics reliability plays a crucial role in successful order fulfillment, ensuring that products reach customers efficiently and effectively. The key elements of a reliable logistics system include accurate forecasting, effective inventory management, efficient transportation, and timely delivery.
Accurate Forecasting
Accurate forecasting of demand is essential for planning and managing inventory levels. By accurately predicting customer demand, businesses can optimize their inventory levels to ensure they have sufficient stock to meet orders. This reduces the likelihood of stockouts, leading to more satisfied customers and increased sales.
Effective Inventory Management
Inventory management is a critical aspect of logistics reliability. Effective inventory management systems track available stock and can help businesses make informed decisions on reorder points and optimal order quantities. With real-time data at their fingertips, companies can avoid costly stockouts or excessive inventory, ensuring a smooth order fulfillment process.
Efficient Transportation
Efficient transportation plays a significant role in logistics reliability. Businesses should consider factors such as shipping costs, carrier reliability, and transit times when selecting transportation methods. Choosing the most efficient and reliable transportation options can lead to reduced lead times, decreased shipping costs, and improved overall customer satisfaction.
Timely Delivery
Ultimately, timely delivery is the primary goal for any business involved in order fulfillment. Logistics systems should be flexible enough to adapt to changing circumstances such as delays, cancellations, or unexpected increases in demand. An agile and reliable logistics infrastructure can ensure timely delivery of products, leading to happier customers and increased brand loyalty.
In conclusion, logistics reliability is an essential aspect of order fulfillment that ultimately contributes to a company's success. By effectively managing key elements such as accurate forecasting, inventory management, transportation, and delivery, businesses can enhance logistics reliability and improve overall customer satisfaction.

Demand forecasting and inventory management systems
Effective demand forecasting plays a crucial role in enhancing the overall reliability of the order fulfillment process. Accurate anticipation of customer needs facilitates better planning, reduced stockouts, and minimized excess inventory. By refining demand predictions, businesses can optimize stock levels and streamline operations.
Integration of real-time data
Integrating real-time data into demand forecasting enables companies to quickly adapt to market trends and changes in consumer behavior. Real-time data analysis supports the development of data-driven strategies, ensuring that companies can rapidly adjust their inventory to fluctuating demand. Consequently, organizations can minimize supply chain disruptions, enhance customer satisfaction, and maintain service levels.
Inventory management strategies
Proactive inventory management strategies contribute to effective order fulfillment by ensuring the appropriate level of stock is maintained at all times. Adopting a just-in-time inventory system helps businesses reduce excess inventory and associated costs. Moreover, implementing reorder point algorithms allows for timely arrivals of new stock, reducing the likelihood of stockouts and delayed deliveries.
Leveraging automation and technology
Utilizing advanced technologies, such as artificial intelligence and machine learning, can further improve demand forecasting and inventory management. These systems can analyze historical data, market trends, and other variables to generate more accurate demand forecasts. This assists companies in making informed decisions about sourcing, purchasing, and resource allocation. Additionally, automated inventory systems can track stock levels and trigger alerts, ensuring that replenishment occurs promptly.
Collaborative relationships with upstream partners
Developing collaborative relationships with suppliers and manufacturers is instrumental in maintaining a reliable order fulfillment process. This cooperation enables businesses to receive critical information regarding production capacity, lead times, and potential supply chain disruptions. Knowledge sharing ensures that appropriate measures can be taken to reduce the impact of any delays and maintain a consistent order delivery process.
In conclusion, effective demand forecasting and inventory management represent two essential components to enhancing the overall reliability of the order fulfillment process. By adopting innovative technologies, collaborating with upstream partners, and implementing strategic inventory management techniques, businesses can minimize supply chain disruptions, meet customer expectations, and maximize operational efficiency.

Optimizing Order Fulfillment through Technology
Technology plays a critical role in enhancing logistics reliability and optimizing the order fulfillment process. One way it achieves this is through data analytics, which enables businesses to monitor and evaluate key performance indicators in real-time, leading to better decision-making and process optimization.
Inventory Management Systems
The integration of inventory management systems allows businesses to maintain accurate stock levels and avoid issues with out-of-stock products or excess inventory. These systems also help in demand forecasting, resulting in more efficient ordering, stocking, and replenishment processes.
Automated Warehouse Solutions
Automation in warehouses improves the efficiency and accuracy of the order fulfillment process. By implementing advanced technologies such as robotics, barcode scanning, and automated storage and retrieval systems (AS/RS), businesses can reduce manual errors, minimize labor costs, and increase the speed of order processing.
Real-Time Tracking and Transparency
The ability to track shipments in real-time ensures timely deliveries and reduces the risk of loss or damage. Through the use of GPS technology and telematics, companies have visibility into their fleets' movements, leading to better communication with customers and improved customer satisfaction.
Integration of Supply Chain Systems
Technology allows for seamless integration of various supply chain systems, from order management and warehouse management to transportation management and customer relationship management. This integration facilitates efficient communication among various stakeholders, resulting in streamlined operations and a more reliable end-to-end supply chain process.
IoT and Smart Technology
IoT and smart technology devices can monitor various environmental factors affecting the order fulfillment process. Devices can track quality-control parameters such as temperature, humidity, and shipment handling, ensuring that products maintain the desired quality level.
In conclusion, technology is an indispensable tool for enhancing logistics reliability and optimizing the order fulfillment process. By leveraging capabilities such as data analytics, inventory management systems, automated warehousing, real-time tracking, and smart technologies, businesses can create value through improved efficiency, reduced costs, and a more reliable supply chain.

Key Performance Indicators for Order Fulfillment Reliability
Order Accuracy and Completeness
One prominent indicator of logistics reliability is order accuracy and completeness, which refers to the percentage of customer orders correctly shipped without any discrepancies. This performance indicator highlights the company's ability to minimize errors and keep customers satisfied.
On-Time Delivery
Another essential aspect to assess the reliability of logistics operations is on-time delivery, measured as the percentage of products delivered within the agreed-upon time frame. Maintaining a high on-time delivery rate signals a dependable and efficient operation, directly contributing to customer satisfaction and repeat business.
Inventory Accuracy
To effectively gauge the efficiency of logistics operations, it is crucial to track inventory accuracy, computed from the difference between physical inventory levels and recorded data in the inventory management system. High inventory accuracy ensures that order fulfillment can be achieved without delays or stockouts, leading to a more reliable supply chain.
Cycle Time
The cycle time, or the total time taken from order placement to delivery, is another vital performance indicator for logistics reliability. A shorter cycle time signifies an efficient order fulfillment process and can contribute to better customer satisfaction, while longer cycle times could be indicative of bottlenecks or operational inefficiencies.
Order Fill Rate
The order fill rate measures the proportion of customer orders satisfied without any backorders. A high order fill rate reflects efficient inventory management and the ability of the logistics operation to fulfill orders expediently, enhancing its reputation for reliability.
Customer Complaints and Returns
Lastly, tracking the rate of customer complaints and returns related to order fulfillment can provide valuable insights into the effectiveness of logistics operations. A low rate of complaints and returns could indicate that the company is providing a reliable service to its customers, while a high rate may suggest operational inefficiencies or recurring issues that need addressing.
In conclusion, the reliability of logistics operations in the context of order fulfillment can be measured using several key performance indicators, such as order accuracy, on-time delivery, inventory accuracy, cycle time, order fill rate, customer complaints, and returns. Constantly monitoring and improving these metrics is imperative to maintain and enhance the overall reliability and efficiency of logistics operations, ultimately leading to better customer satisfaction and business success.

Role of Integration in Supply Chain Partners
As business environments become increasingly complex, organizations must coordinate and collaborate with their supply chain partners to improve order fulfillment reliability. Integration among supply chain partners plays a pivotal role in enhancing overall performance by streamlining processes, optimally allocating resources, and promoting effective communication of real-time data.
Collaborative Approach to Forecasting and Planning
A critical component of achieving order fulfillment reliability is the sharing of key business information among partners, enabling a coordinated approach to demand forecasting and capacity planning. This collaborative approach facilitates the optimization of inventory levels and manufacturing plans, reducing stockouts and overstocks, and ultimately improving customer service.
Synchronized Flow and Lean Practices
Through integration, supply chain partners can align their operational processes and thereby create an efficient and responsive supply chain. By adopting synchronized flow and lean manufacturing practices, organizations can minimize lead times, eliminate waste, and reduce variability in the supply chain, thereby consistently meeting customer requirements and improving order fulfillment reliability.
Information Sharing and Advanced Technologies
Leveraging advanced technologies, such as cloud computing, artificial intelligence, and blockchain, can significantly enhance information sharing and integration among supply chain partners. Access to real-time data across the entire supply chain network allows organizations to proactively manage and mitigate potential disruptions and delays, thus ensuring timely order fulfillment.
Building Trust and Strong Relationships
Cultivating trust and strong relationships among supply chain partners is essential for successful integration. Trust encourages the sharing of vital business information and fosters collaborative problem-solving strategies. Consequently, supply chain partners become more agile and responsive, effectively addressing customer needs while maintaining high order fulfillment reliability.
In conclusion, integrating supply chain partners is instrumental in enhancing order fulfillment reliability by fostering collaboration, enabling synchronized flow, promoting efficient data sharing, and building strong relationships. By streamlining operations and leveraging advanced technologies, organizations can create a responsive and agile supply network, ultimately ensuring customer satisfaction and competitive advantage.

Efficient Transportation Management
Efficient transportation management plays a crucial role in ensuring the reliability of the order fulfillment process. It involves the optimization of various aspects such as route planning, delivery scheduling, and cost management, which can substantially improve the overall efficiency of supply chain operations.
Route Planning and Optimization
An essential aspect of efficient transportation management is route planning and optimization. By utilizing advanced software tools and algorithms, companies can choose the ideal routes for delivering products to their customers. This minimizes the overall delivery time and enhances customer satisfaction levels, contributing to the reliability of the order fulfillment process.
Delivery Scheduling and Timeliness
Another vital factor contributing to the reliability of the order fulfillment process is effective delivery scheduling. Companies must have timely and accurate information about their product inventories and customer orders. With this information, efficient transportation management ensures an effective balance between product availability and delivery timeliness, directly influencing the order fulfillment reliability.
Cost Management and Resource Allocation
The management of logistical costs and efficient resource allocation are also integral components of successful transportation management. By optimizing the usage of available transport resources, companies can minimize transportation costs and reduce waste. This, in turn, leads to improved financial stability and enables businesses to fulfill their customer orders more consistently and reliably.
Visibility and Transparency
Visibility and transparency are crucial aspects of efficient transportation management, as they promote better decision-making and reduce instances of miscommunication. Through the implementation of real-time tracking technologies and maintaining clear communication channels, companies can ensure that all involved parties remain updated on the status of shipments. This increased visibility helps minimize errors and delays, enhancing the overall reliability of the order fulfillment process.
Collaboration and Partnerships
Finally, establishing strategic collaborations and partnerships with carriers and logistics providers can significantly improve transportation management efficiency. By leveraging the expertise and resources of industry partners, companies can access specialized services, advanced technologies, and an extended network of delivery routes. This collaborative approach positively impacts the reliability of the order fulfillment process by streamlining operations and reducing potential bottlenecks.
In conclusion, efficient transportation management is vital for a reliable order fulfillment process. Through optimizing route planning, delivery scheduling, and cost management, coupled with enhancing visibility, fostering collaborations, and leveraging technologies, companies can ensure the timely and accurate delivery of products, leading to satisfied customers and long-term business success.

Factors Affecting Order Fulfillment
In the context of global supply chain complexities, several factors influence the reliability of order fulfillment. These factors can be categorized into internal and external aspects that affect the overall performance of the supply chain.
Internal Factors
1. Company resources: The availability and management of a company's resources, such as financial, human, and technology, play a critical role in the efficiency of order fulfillment. A well-resourced business is more likely to deliver orders on time and with higher accuracy.
2. Organizational structure: A company's organizational structure heavily affects the decision-making process, communication, and coordination among departments. A streamlined structure facilitates better order fulfillment across the supply chain.
3. Inventory management: Effective inventory management ensures that products are available when needed, preventing stockouts and delays in order fulfillment. This includes accurate demand forecasting, timely replenishment, and efficient storage.
External Factors
1. Global trade regulations: Policies and regulations impacting global trade create complexities in the supply chain, increasing the likelihood of disruption and delays in order fulfillment. Companies must navigate through varied licensure, taxation, and documentation requirements.
2. Transportation infrastructure: The quality of transportation infrastructure, such as roads, ports, and airports, influences the speed and efficiency of product deliveries. Poor infrastructure increases the risk of late or damaged orders.
3. Geopolitical risks: Businesses with global supply chains are exposed to geopolitical risks that can disrupt order fulfillment. These risks include trade wars, political instability, currency fluctuations, and natural disasters.
4. Supplier performance: The reliability of supplier performance is crucial in maintaining order fulfillment efficiency, as delays or inconsistencies in raw material supply can lead to complications and order shipment failures.
5. Technological advancements: Innovations in supply chain technology, such as improved tracking systems and automation, enable companies to monitor and manage their order fulfillment processes more effectively, reducing the likelihood of errors and delays.
In conclusion, a myriad of internal and external factors influence the reliability of order fulfillment in the context of global supply chain complexities. Companies must strategize and adapt to these factors to optimize their order fulfillment processes and maintain a competitive edge in a rapidly changing business landscape.

Contribution of Logistics Network to Order Fulfillment Reliability
Effective Management of Supply Chain
A robust and responsive logistics network significantly contributes to enhancing the reliability of order fulfillment by effectively managing the supply chain. This efficient management reduces delays and ensures timely delivery of products to customers. Effective coordination among various stakeholders, such as suppliers, manufacturers, and retailers, is crucial in streamlining the flow of goods and services.
Inventory Control and Forecasting
Logistics networks play an essential role in maintaining appropriate inventory levels and minimizing stockouts. By employing advanced technologies for inventory management, companies can keep track of their stocks and make informed decisions regarding replenishment. Additionally, accurate demand forecasting allows businesses to better anticipate customer needs and adjust their supply chain operations accordingly. This proactive approach helps avoid stockouts, backorders, and other disruptions, ultimately enhancing order fulfillment reliability.
Implementation of Advanced Technologies
Integrating advanced technologies, such as automation and digitalization, into the logistics network improves its responsiveness and resilience. These technologies enable real-time data sharing, enhancing visibility and transparency across the entire supply chain. This vital information supports better decision-making and promotes proactive responses to changes in the market. Furthermore, advancements in transportation technologies, such as autonomous vehicles and drones, offer more efficient and reliable delivery options.
Risk Mitigation and Contingency Planning
A robust logistics network can enhance reliability by identifying potential risks and developing contingency plans to minimize their impact on order fulfillment. By continuously monitoring the operations and external factors affecting the supply chain, businesses can proactively address any disruptions. An effective risk mitigation strategy includes diversifying suppliers, adopting multi-modal transportation options, and maintaining backup inventory to ensure seamless order fulfillment even in the face of unforeseen challenges.
Improved Customer Satisfaction and Trust
A responsive and reliable logistics network plays a crucial role in enhancing the overall customer experience. By meeting customers' expectations and delivering products on time, businesses can improve customer satisfaction and build long-term trust. Moreover, satisfied customers are more likely to recommend the company to others, thereby contributing to the growth and success of the business.
In conclusion, a robust and responsive logistics network is vital in enhancing the reliability of order fulfillment. By optimizing supply chain management, implementing advanced technologies, and developing risk mitigation strategies, businesses can improve the efficiency of their operations, resulting in more reliable order fulfillment and increased customer satisfaction.

Methods for Monitoring Order Fulfillment Reliability
The first method for monitoring order fulfillment reliability in logistics management is to develop Key Performance Indicators (KPIs). These should be aligned with the organization's objectives and measure aspects such as on-time deliveries, order accuracy, and order-cycle time.
Real-Time Data Tracking
Another effective method is the use of real-time data tracking, such as using GPS technology to monitor shipments throughout the supply chain. This allows companies to react promptly to potential disruptions and continuously improve delivery performance.
Continuous Improvement Initiatives
Continuous improvement initiatives, such as lean and Six Sigma, help identify areas for improvement within the logistics process. Regularly reviewing and adjusting these processes ensures that order fulfillment remains productive and reliable.
Customer Feedback
Incorporating customer feedback into the evaluation process is crucial for maintaining reliability. This may involve surveys or other methods to gather data on customer satisfaction, typically related to order accuracy, delivery time, and overall service quality.
Technology Implementation
Leveraging technology solutions, such as Warehouse Management Systems (WMS) and Transportation Management System (TMS), is vital for optimizing order fulfillment processes. These software solutions enable detailed tracking, analytics, and automation of logistics tasks, thereby improving the reliability of the supply chain.
Collaboration with Suppliers
Establishing strong partnerships and communication channels with suppliers helps to ensure reliable delivery of materials, which contributes to the success of the entire production process. Regular communication with suppliers allows for proactive management and quick resolution of any potential issues.
Benchmarking
Comparing your organization's performance with industry benchmarks and competitors provides valuable insights into your order fulfillment reliability. This may involve examining industry-wide standards or participating in benchmarking groups to identify areas of strength or opportunities for improvement.
In conclusion, a multi-faceted approach is necessary for monitoring and evaluating order fulfillment reliability in logistics management. Key components include the development of KPIs, real-time data tracking, continuous improvement initiatives, customer feedback, technology implementation, collaboration with suppliers, and benchmarking. By utilizing these methods and best practices, companies can ensure their supply chain remains efficient, productive, and reliable.

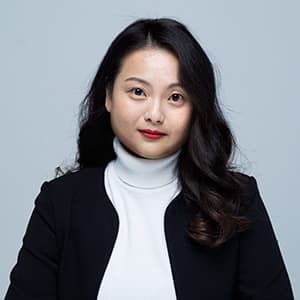
Yu Payne is an American professional who believes in personal growth. After studying The Art & Science of Transformational from Erickson College, she continuously seeks out new trainings to improve herself. She has been producing content for the IIENSTITU Blog since 2021. Her work has been featured on various platforms, including but not limited to: ThriveGlobal, TinyBuddha, and Addicted2Success. Yu aspires to help others reach their full potential and live their best lives.