3D Printing in Logistics: Revolutionizing Supply Chains

As I sit here in my home office, surrounded by various 3D-printed objects - from a custom phone stand to a miniature replica of the Eiffel Tower - I can't help but marvel at how far this technology has come. It's not just about creating cool trinkets anymore; 3D printing is revolutionizing entire industries, and nowhere is this more evident than in the world of logistics.
In the ever-evolving landscape of modern manufacturing and supply chain management, 3D printing has emerged as a game-changing technology that's redefining conventional processes. Gone are the days when 3D printing was solely confined to prototyping; it has now infiltrated various industries, propelling them towards a future where bespoke production and on-demand manufacturing are becoming the norm.
As someone who's been following this technology for years, I've witnessed its growth from a niche hobby to a powerful industrial tool. And let me tell you, the potential it holds for logistics is nothing short of mind-blowing.
In this blog post, we'll dive deep into the intricate relationship between 3D printing and logistics. We'll explore its extensive applications, untapped potentials, and the challenges that lie ahead on this converging path. So, buckle up and get ready for a journey into the future of supply chains!
The Concept of 3D Printing
Before we delve into the logistics side of things, let's take a moment to understand what 3D printing really is.
Detailed Understanding of 3D Printing
3D printing, also known as additive manufacturing, is a process that constructs three-dimensional objects from a digital file. It's like magic, really - layer by layer, the printer stacks material until the desired shape is achieved.
I remember the first time I saw a 3D printer in action. It was at a tech conference back in 2010, and I was mesmerized. The printer was creating a small, intricate gear, and I couldn't take my eyes off it. It felt like I was witnessing the future unfold before my very eyes.
The history of 3D printing dates back to the early 1980s, where it was primarily used for rapid prototyping. Since then, technological advancements have tremendously broadened its capabilities.
The exact working mechanism of 3D printers varies across different technologies:
Stereolithography (SLA): Uses a laser to cure and solidify liquid resin
Fused Deposition Modeling (FDM): Extrudes heated plastic filament
Selective Laser Sintering (SLS): Uses a laser to sinter powdered material
But they all revolve around the same theme: converting digital blueprints into tangible objects.
Various Applications of 3D Printing
The applications of 3D printing are vast and varied. It's like a Swiss Army knife for manufacturing - versatile and incredibly useful in a wide range of scenarios. Here are just a few examples:
Medical Field: Custom prosthetics and dental implants
Manufacturing: Complex parts that would be impractical or impossible to produce through traditional methods
Fashion Industry: Intricate designs and patterns for runway shows
Construction: Building components and even entire structures
Aerospace: Lightweight parts for aircraft and spacecraft
Education: Creating visual aids and models for better learning experiences
I once visited a medical lab where they were using 3D printing to create custom prosthetic limbs. The level of detail and personalization was astounding. It really drove home how this technology is not just changing industries, but changing lives.
3D Printing Relevance to Logistics
Now, let's get to the meat of our discussion - how does 3D printing relate to logistics?
Exploring the Link Between 3D Printing and Logistics
The connection between 3D printing and logistics is where things get really exciting. It's like discovering a secret passage that completely changes how you navigate a building.
Here's how 3D printing is shaking things up in logistics:
Reduced Inventory: Companies can print on demand, reducing the need for stockpiling and warehousing.
Personalized Customer Experience: The customizable nature of 3D printing allows for more tailored products.
Localized Production: Goods can be printed closer to the end-consumer, dramatically reducing lead times and transportation requirements.
I remember talking to a logistics manager who implemented 3D printing in their operations. He told me, "It's like we've unlocked a new level in the game of supply chain management. We're faster, more efficient, and more responsive to customer needs than ever before."
Explanation of How 3D Printing Overcomes Logistics Challenges
3D printing is like a superhero swooping in to save the day for logistics managers everywhere. Here's how it's tackling some major challenges:
Transportation Costs: By decentralizing production and allowing for local manufacturing, 3D printing significantly reduces transportation costs.
Lead Times: With on-demand production, lead times can be slashed dramatically.
Customization: 3D printing makes it easier and more cost-effective to produce customized products.
Supply Chain Resilience: A shorter supply chain means fewer opportunities for interruptions or delays.
Benefits of 3D Printing in Logistics
Let's break down the benefits of 3D printing in logistics in more detail.
Detailed Description of the Advantages
Cost Savings: 3D printing can lead to significant financial savings by:
Reducing waste through precise material use
Eliminating the need for tooling
Decreasing transportation and warehousing costs
Time Efficiency: Rapid prototyping and manufacturing enable quicker time-to-market for new products.
Sustainability: On-demand production can diminish overproduction and waste, aligning with the rising global emphasis on eco-conscious business practices.
Flexibility: 3D printing allows for quick design changes and production of small batches, making it easier to respond to market demands.
Simplified Supply Chain: With localized production, the supply chain becomes shorter and easier to manage.
Case Studies Showing Implementation of 3D Printing in Logistics
Let's look at some real-world examples of how companies are leveraging 3D printing in their logistics operations:
Automobile Industry: BMW has been using 3D printing to produce parts on demand, minimizing inventory and reducing warehouse space. They've reported significant cost savings and improved efficiency.
Aerospace Industry: Airbus integrates 3D printing to manufacture components. This not only lightens aircraft weight, contributing to fuel efficiency, but also simplifies the supply chain and reduces lead times.
Fashion Industry: Adidas has been experimenting with 3D-printed midsoles for shoes. This allows for customized footwear and on-demand production, potentially revolutionizing their supply chain.
Healthcare: Companies like Invisalign use 3D printing to create custom dental aligners. This has dramatically simplified their production and distribution process.
Current Limitations and Future of 3D Printing in Logistics
While the benefits are numerous and exciting, it's important to acknowledge that 3D printing in logistics isn't without its challenges.
Discussion on the Current Constraints Faced in Incorporating 3D Printing in Logistics
High Initial Investment: The cost of industrial-grade 3D printers can be prohibitive for small to medium-sized enterprises.
Limited Materials: The range of materials suitable for 3D printing is still relatively restricted compared to conventional manufacturing methods.
Skill Gap: Designing for 3D printing requires specialized skills and software, creating a barrier for widespread use.
Quality Control: Ensuring consistent quality across different 3D printing locations can be challenging.
Legal and Intellectual Property Issues: The ease of replicating designs raises concerns about copyright infringement.
Forecast on the Future Advancement and Growth of 3D Printing in Logistics
Despite these challenges, the future of 3D printing in logistics looks incredibly promising. Here's what we can expect:
Technological Advancements: Continuous improvements in 3D printing technology, such as enhanced speed, precision, and material variability, will expand its applicability.
Increased Adoption: As awareness of the long-term economic benefits grows, more companies will integrate 3D printing into their logistics operations.
New Business Models: We may see the rise of 3D printing hubs that serve multiple businesses, similar to cloud computing services.
Sustainability Focus: As environmental concerns become more pressing, the sustainable aspects of 3D printing will drive further adoption.
Integration with Other Technologies: The combination of 3D printing with AI, IoT, and blockchain could lead to even more efficient and transparent supply chains.
As we stand at the intersection of 3D printing and logistics, we're witnessing a pivotal period of transition and opportunity within the industry. The benefits - from cost savings and improved efficiency to enhanced sustainability and customization - are too significant to ignore.
Yet, as with any transformative technology, challenges remain. The high initial costs, material limitations, and skill gaps are hurdles that need to be overcome. But if there's one thing I've learned from following the 3D printing industry for years, it's that innovation never stops.
The future of logistics, shaped by 3D printing, presents a compelling vision. It's a future of responsive, efficient, and customizable supply chains. It's not a question of if this vision will become reality, but when.
As I look at the 3D-printed objects around my office, I'm reminded of how far we've come. And I can't help but feel excited about where we're going. The revolution in logistics is here, and it's being printed, layer by layer, right before our eyes.
References:
Attaran, M. (2017). The rise of 3-D printing: The advantages of additive manufacturing over traditional manufacturing. Business Horizons, 60(5), 677-688.
Holmström, J., Partanen, J., Tuomi, J., & Walter, M. (2010). Rapid manufacturing in the spare parts supply chain: Alternative approaches to capacity deployment. Journal of Manufacturing Technology Management, 21(6), 687-697.
Khajavi, S. H., Partanen, J., & Holmström, J. (2014). Additive manufacturing in the spare parts supply chain. Computers in Industry, 65(1), 50-63.
Weller, C., Kleer, R., & Piller, F. T. (2015). Economic implications of 3D printing: Market structure models in light of additive manufacturing revisited. International Journal of Production Economics, 164, 43-56.
Gao, W., Zhang, Y., Ramanujan, D., Ramani, K., Chen, Y., Williams, C. B., ... & Zavattieri, P. D. (2015). The status, challenges, and future of additive manufacturing in engineering. Computer-Aided Design, 69, 65-89.
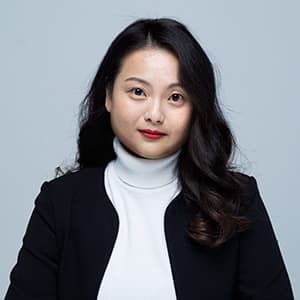
Yu Payne is an American professional who believes in personal growth. After studying The Art & Science of Transformational from Erickson College, she continuously seeks out new trainings to improve herself. She has been producing content for the IIENSTITU Blog since 2021. Her work has been featured on various platforms, including but not limited to: ThriveGlobal, TinyBuddha, and Addicted2Success. Yu aspires to help others reach their full potential and live their best lives.